Step one: Slash fossil fuel refinery emissions. Step two: Kickstart new renewables.
By Caroline Delbert Feb 7, 2020
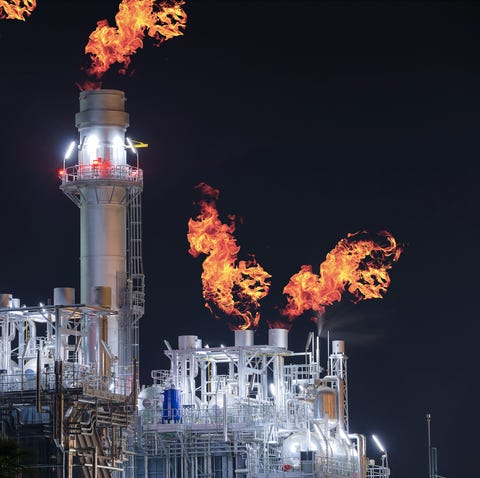
FUNFUNPHOTOGETTY IMAGES
A new way to make efficient, high-acidity catalyst material could decrease fossil fuel refinery emissions.
The process can benefit the fossil fuel industry, but may also enable new renewable fuel sources.
The key is increasing aluminum in order to boost reactive Brønsted acid sites.
Scientists in Australia say they’re working on an oil-refinement catalyst material that could create 28 percent less carbon dioxide than what the industry relies on now. The difference is all in the mix, with more acidity that increases how active the catalyst substance is.
Petrochemicals can be refined in one of a few different processes, and this catalyst is used in the process known as cracking. The process dates back over 100 years, when a Standard Oil chemist discovered thermal cracking, where heating alone is used to break big hydrocarbons into smaller ones: oils, diesel and gas, petroleum coke, and gases like propane.
Adding a catalyst, which began in the 1920s, makes for a more efficient process with higher-quality outcomes, and scientists have continued to make better catalyst materials, formats, and applications. The reason lead was originally added to gasoline was to raise octane and reduce engine knocking. The development of better catalysts over time increases octane on the front end, making it easier first to phase out lead and later to continue to make smaller, more efficient engines.
The University of Sydney team began with amorphous silica-aluminas (ASAs), which are one of the most widely used catalysts in petrochemical refining today. During the cracking process, a lot of carbon dioxide is released, and higher-temperature cracking furnaces must periodically be cleared of coke residue, which also produces carbon dioxide.
“Estimates suggest 20 to 30 percent of crude oil is transferred to waste and further burnt in the chemical process, making oil refineries the second largest source of greenhouse gases behind power plants,” the press release reads. A more efficient catalyst could reduce both emissions waste and just raw materials waste.
The catalyst these researchers developed works by increasing the presence of a specific element called a Brønsted acid sites (BAS) within a particular ASA formulation. “The lower performance of ASA in many catalytic applications is widely attributed to their moderate Brønsted acidity,” the team writes in its paper. So increasing that acidity can make catalysts better.
But how can we do that? The secret is in boosting a specific chemical component. “The formation of BAS in silica-aluminas is based on aluminum centers distributed in the silica framework or network,” the team explains. “The study revealed that compared to the widely accepted model of one Al center, two proximate Al centers can significantly boost its acid strength.”
There are many required next steps for this research to become practical. Identifying even a really promising chemical mechanism is just one important but tiny piece. Scientists first have to be able to make the materials at scale for even one petrochemical refinery plant, let alone enough to be impactful on the world’s refining emissions.
But these researchers point out that a high-efficiency, high-acidity catalyst could open up entire new avenues of refinement with biomass and other renewable energy that isn’t feasible with lower-efficiency catalysts. The researchers say that in a near future where we’ll continue to rely on fossil fuels and traditional refineries for at least a while longer, we might as well invest in making them cleaner and better.
---30---
No comments:
Post a Comment