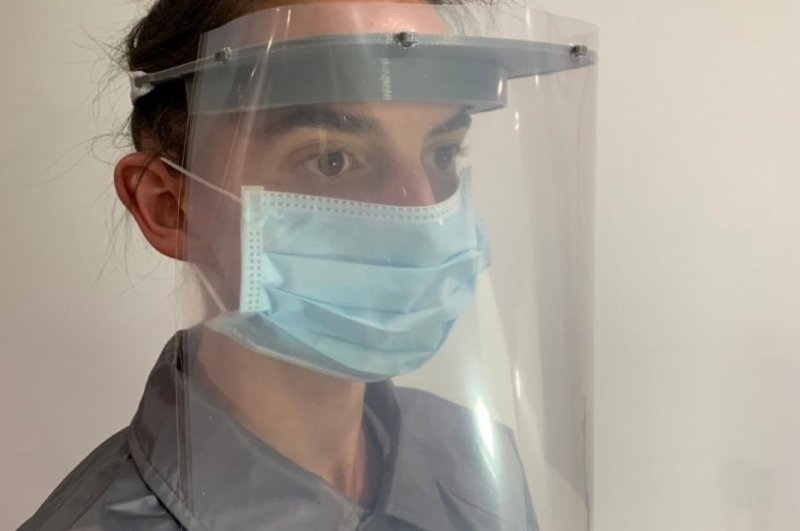
Budmen Industries, a company that makes 3D printers in Syracuse, N.Y., has converted to making face shields for medical staff. Photo courtesy of Budmen Industries
March 26 (UPI) -- Community efforts to make medical protective equipment on 3D printers have sprung up around the United States in the last week to respond to urgent shortages caused by the coronavirus.
As major manufacturers -- such as Ford Motors, 3M and General Electric -- announce projects to produce safety equipment, schools, dentists and 3D printing shops from Montana to New York have launched their own efforts using high-tech printers.
Many hospitals have asked their staffs to reuse protective equipment, such as masks, gowns, gloves and face shields, and physicians report that existing supplies could run out in many places in days, according to the American Medical Association.
"Just about every night, I'm on the phone with a couple of doctors I've been in contact with to see what we can do," said Isaac Budmen, owner of a small company that makes 3D printers, Budmen Industries, in Syracuse, N.Y.
Budmen raised $10,000 on the GoFundMe website in a week and has printed the headbands and frames for more than 600 face shields since then.
He bought plastic sheets for the shield portion and estimates each face shield is now costing about $5 apiece. The community embraced the project, with the Greater Syracuse Soundstage, a film studio, now allowing limited crews of four at a time to assemble the shields.
In many cases, entrepreneurs like Budmen have created their own designs for items they are printing, but medical supply companies have released designs for some parts.
The Department of Defense's additive manufacturing initiative, America Makes, launched a new effort Wednesday to provide designs and to connect medical institutions with 3D printers.
Printing masks has proven more difficult for the industry, according to neurosurgeon Marlin Richardson at the Billings Clinic in Montana.
He and a local dentist, Spencer Zaugg, decided to design their own mask that uses pieces of existing surgical masks as the air filter. That way, local supplies of masks can be extended.
He bought plastic sheets for the shield portion and estimates each face shield is now costing about $5 apiece. The community embraced the project, with the Greater Syracuse Soundstage, a film studio, now allowing limited crews of four at a time to assemble the shields.
In many cases, entrepreneurs like Budmen have created their own designs for items they are printing, but medical supply companies have released designs for some parts.

The Department of Defense's additive manufacturing initiative, America Makes, launched a new effort Wednesday to provide designs and to connect medical institutions with 3D printers.
Printing masks has proven more difficult for the industry, according to neurosurgeon Marlin Richardson at the Billings Clinic in Montana.
He and a local dentist, Spencer Zaugg, decided to design their own mask that uses pieces of existing surgical masks as the air filter. That way, local supplies of masks can be extended.
RELATED Face masks shake up Korean cosmetics industry
"A notice had gone up at the hospital that we had limited supplies and were going to using one mask per day. That's very unusual. We usually change masks for every patient," Richardson said.
Padding and straps for the masks are needed, and Richardson said the community has responded by sewing and making those.
He and Zaugg are working on a better design for a higher-quality respirator mask.
The Billings Clinic is now seeking out every 3D printer in the community, including all of them at Billings public schools, Rocky Mountain College and Montana State University-Billings. A Billings area company that makes industrial filters, Flowmark/HighTech, plans to provide 20,000 pieces of filter material for the project.
Other 3D printing companies that are making equipment include Voodoo Manufacturing in Brooklyn, N.Y., which says it has converted 200 3D printers to make protective equipment and replacement parts for ventilators.
"To minimize the risk of infection, we have divided our production team into sub-teams, which work separately and use good sanitation practices," Voodoo said in a statement.
Markforged, based near Boston, has printed face shields and swabs for test kits and sent them to hospitals where they are being tested, founder Greg Mark said.
"What we've found is that 20 printers can print 14,000 swabs a day," Mark said. "We have assembled a task force within Markforged to identify the biggest impact initiatives our technology can solve."
No comments:
Post a Comment