Team develops eco-friendly, flame-retardant carbon plastic ideal for recycling
Provided by European Space Agency
ESA's detailed testing of this natural-fiber composite has helped it find wider terrestrial uses in turn, including inside McLaren Racing's Formula 1 cars.
Fibers from the flax plant, cultivated in Europe since the Stone Age, are weaved to make linen. An ESA project with Swiss companies Bcomp and RUAG looked into substituting them for carbon fibers, which are employed to make leading composite material 'carbon fiber reinforced plastic' (CFRP).
A strong yet light material, CFRP resembles reinforced concrete, where steel bars are added to a concrete mix in order to strengthen it. In a parallel manner, carbon fibers are mixed with epoxy resin to achieve a higher strength-to-weight ratio and rigidity. The resulting composite is used widely in satellite manufacturing, as well as the high-performance automotive and maritime sectors.
"The idea behind this Bio-Composite Structure in Space Applications project was to investigate the use of natural fibers in place of their carbon equivalents," explains ESA structural engineer Tiziana Cardone.
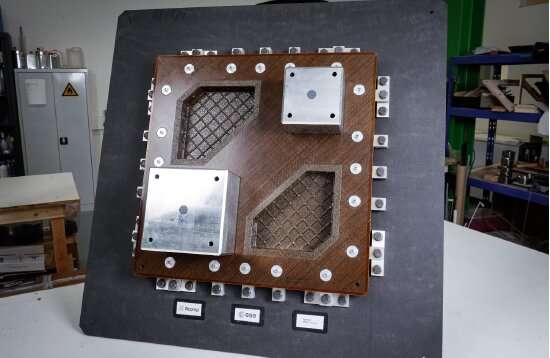
This flax-containing biocomposite satellite panel is a test version of a lateral structural panel for the Copernicus Sentinel-1 satellite – which aboard the actual mission has been made from aluminium. Credit: Bcomp
"There are two main reasons why: firstly to reduce the environmental impacts of space manufacturing, which is one of the main goals of ESA's Clean Space initiative. Our detailed Life Cycle Analysis shows this can cut carbon dioxide emissions by up to 75% compared to matching carbon fiber parts.
"In addition, in another link to Clean Space, we've been seeking out novel materials that can 'demise' more easily, meaning they can burn up more rapidly and completely during atmospheric reentry. This has been driven in turn by the requirements of Europe's space debris mitigation policy, requiring a less than 1 in 10 000 risk to people or property when satellites are disposed of at their end of life."
The project, led by ESA's Structures section and supported through the Agency's General Support Technology Programme, involved examining the flax fibers in terms of the highly demanding requirements of spaceflight.
"We found that they have exceptionally low thermal expansion—which is good in terms of the temperature extremes of orbital space—as well as high specific stiffness, and strength which can be retained right down to cryogenic temperatures," says ESA materials and processes specialist Ugo Lafont. "They are also able damp down vibration well, can endure ultraviolet radiation exposure and impede radio signals much less than carbon fibers."
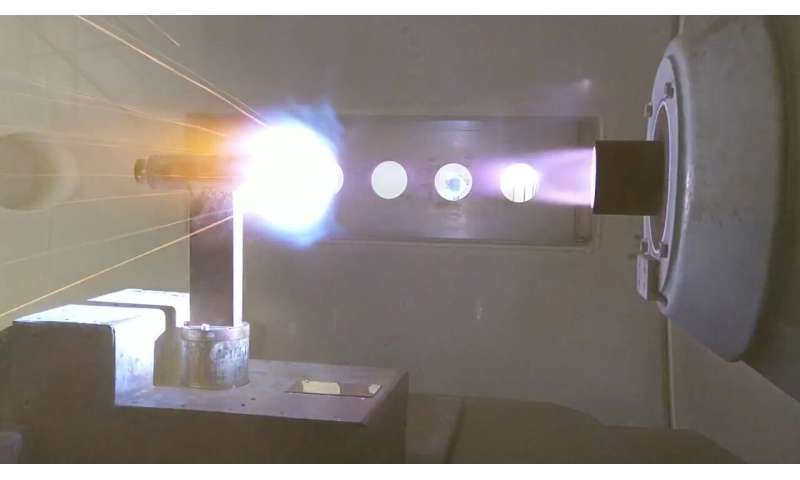
"There are two main reasons why: firstly to reduce the environmental impacts of space manufacturing, which is one of the main goals of ESA's Clean Space initiative. Our detailed Life Cycle Analysis shows this can cut carbon dioxide emissions by up to 75% compared to matching carbon fiber parts.
"In addition, in another link to Clean Space, we've been seeking out novel materials that can 'demise' more easily, meaning they can burn up more rapidly and completely during atmospheric reentry. This has been driven in turn by the requirements of Europe's space debris mitigation policy, requiring a less than 1 in 10 000 risk to people or property when satellites are disposed of at their end of life."
The project, led by ESA's Structures section and supported through the Agency's General Support Technology Programme, involved examining the flax fibers in terms of the highly demanding requirements of spaceflight.
"We found that they have exceptionally low thermal expansion—which is good in terms of the temperature extremes of orbital space—as well as high specific stiffness, and strength which can be retained right down to cryogenic temperatures," says ESA materials and processes specialist Ugo Lafont. "They are also able damp down vibration well, can endure ultraviolet radiation exposure and impede radio signals much less than carbon fibers."
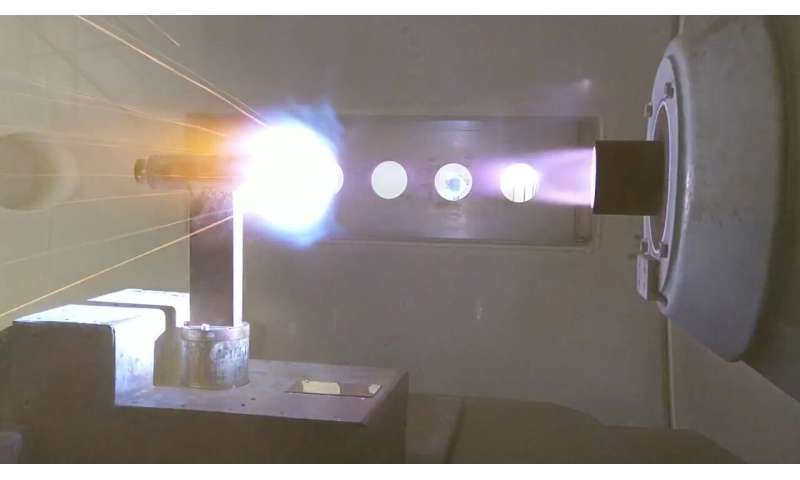
Flax-based biocomposite structural panels were tested for demisability in simulated reentry conditions using a plasma wind tunnel at the Institute of Space Systems, IRS, in Stuttgart, Germany. Credit: IRS
The project team took Bcomp's patented thin-shell 'powerRib' natural-fiber composites as their starting point, using them to make a test version of a lateral structural panel for the Copernicus Sentinel-1 satellite—which in the case of the actual mission was made from aluminum.
"These panels are designed as 'targeted demisable points' for the satellite, intended to break up early to allow heat fluxes into the satellite interior earlier than would otherwise be the case," adds Tommaso Ghidini. Heading ESA's Structures, Mechanisms and Materials Division.
"The next step was to put these remade panels to the test in as realistic manner as possible, using a plasma wind tunnel at the Institute of Space Systems, IRS in Stuttgart, Germany. The IRS worked with ESA's Materials section to develop the demisability test procedure."
he resulting baptism of fire showed a positive result compared to traditional CFRP: while carbon fiber strands tend to endure in place while their surrounding matrix is burnt away, the flax fibers ablate apart much more rapidly.
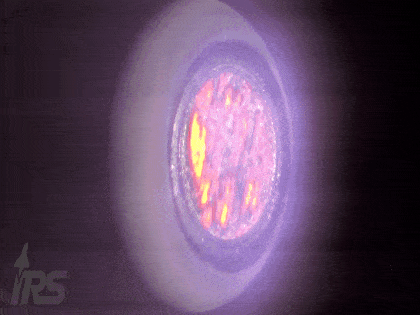
The project team took Bcomp's patented thin-shell 'powerRib' natural-fiber composites as their starting point, using them to make a test version of a lateral structural panel for the Copernicus Sentinel-1 satellite—which in the case of the actual mission was made from aluminum.
"These panels are designed as 'targeted demisable points' for the satellite, intended to break up early to allow heat fluxes into the satellite interior earlier than would otherwise be the case," adds Tommaso Ghidini. Heading ESA's Structures, Mechanisms and Materials Division.
"The next step was to put these remade panels to the test in as realistic manner as possible, using a plasma wind tunnel at the Institute of Space Systems, IRS in Stuttgart, Germany. The IRS worked with ESA's Materials section to develop the demisability test procedure."
he resulting baptism of fire showed a positive result compared to traditional CFRP: while carbon fiber strands tend to endure in place while their surrounding matrix is burnt away, the flax fibers ablate apart much more rapidly.
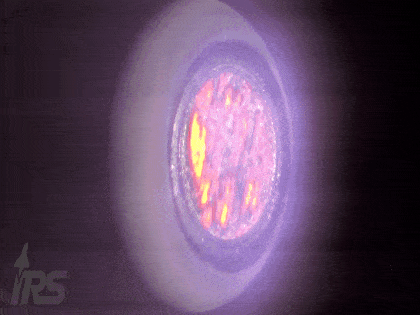
Bcomp natural flax fibres laid down in epoxy, exposed to a plasma wind tunnel to simulate atmospheric reentry conditions, testing their 'demisability'. Testing took place at the Institute of Space Systems, IRS, in Stuttgart Germany. IRS worked with ESA’s Materials section to develop the demisability test procedure. Credit: ESA
The project's detailed characterisation of Bcomp's natural fiber composite also led to it finding new terrestrial customers: Sweden's Volta Trucks firm is using the composite for weight-saving and more environmentally friendly body panels.
McLaren Racing meanwhile has collaborated with Bcomp to manufacture Formula 1's first natural fiber composite racing seat. Possessing improved vibration-damping properties to a traditional CFRP seat, the new material also offers wider safety possibilities –carbon fibers are notorious for splintering during accidents, puncturing whe
"We're a small team, and working with ESA has taught us a lot," adds Régis Voillat of Bcomp, "which we've been able to apply in turn to a lot of our other projects. So this collaboration has supported the spread of sustainable technologies to other sectors as well."
Explore further
The project's detailed characterisation of Bcomp's natural fiber composite also led to it finding new terrestrial customers: Sweden's Volta Trucks firm is using the composite for weight-saving and more environmentally friendly body panels.
McLaren Racing meanwhile has collaborated with Bcomp to manufacture Formula 1's first natural fiber composite racing seat. Possessing improved vibration-damping properties to a traditional CFRP seat, the new material also offers wider safety possibilities –carbon fibers are notorious for splintering during accidents, puncturing whe
"We're a small team, and working with ESA has taught us a lot," adds Régis Voillat of Bcomp, "which we've been able to apply in turn to a lot of our other projects. So this collaboration has supported the spread of sustainable technologies to other sectors as well."
Explore further
Provided by European Space Agency
No comments:
Post a Comment