TOYOTAIZATION REDUX
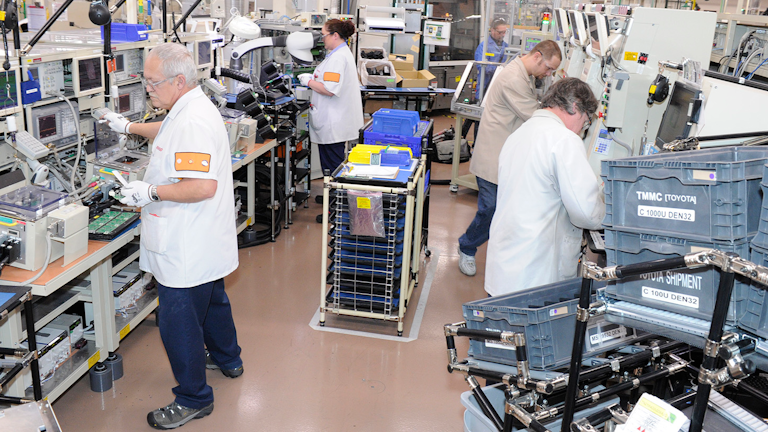
The real message here is: "adopt and adapt technology that supports your people and processes."
Jeffrey Liker
AUG 27, 2020
Society has reached the point where one can push a button and be immediately deluged with technical and managerial information. This is all very convenient, of course, but if one is not careful there is a danger of losing the ability to think. We must remember that in the end it is the individual human being who must solve the problems.
—Eiji Toyoda, Creativity, Challenge and Courage, Toyota Motor Corporation, 1983
In the 1990s Toyota’s principles of production equipment became “simple, slim, and flexible,” which some people might interpret as “go slow and be cautious in adopting new technology.” In today’s age of lightning speed technological change, particularly in the digital world, I believe that would be a mistake. The real message here is: "adopt and adapt technology that supports your people and processes." The starting point is this: where are real needs that technology can address to help achieve your goals? This is a question of pulling technology based on the opportunity, instead of pushing the technology because it is the latest fad.
This simple lesson grows more relevant every day. It seems clear to me that technology in the digital age can support lean thinking. The key issue is to avoid the temptation to buy and implement the latest gee-whiz digital tools, and instead to thoughtfully integrate technology with highly developed people and processes.
Toyota’s largest supplier, Denso, has made remarkable progress in adapting real time data collection, the Internet of Things (IOT), and data analytics to support lean systems and amplify kaizen. At the center of Denso’s approach is people, and their ability to sense reality and think creatively. Denso demonstrates that technology has the greatest potential when there is a culture of continuous improvement and the people are highly developed.
Raja Shembekar, vice president of Denso’s North American Production Innovation Center, is the chief architect of their use of the Internet of Things (IOT). As a starting point Raja benchmarked other companies thought to be leaders in the technology. He found a lot of what he came to call “IOT wallpaper” with little real application. Cool-looking displays, but no real problem solving. He concluded that Denso needed to take charge and lead their own effort, starting with treating the Battlecreek, Michigan plant as a pilot site. He built a small team, with about half IOT experts, and half shopfloor people like quality managers who were good at software. Together, they started to work on real problems identified at the gemba.
As one example they have huge brazing ovens needed to make aluminum heat exchangers. It is critical to keep the temperature constant throughout the oven and they do this with twelve expensive fans each the size of a table. If a single fan stops, it take 12 hours to cool the oven down from 700 celsius, 12 hours to replace the fan, and 12 hours to bring it back up. With tiny sensors on each fan and an IOT system they can monitor the condition and alert maintenance when there is any degradation, long before a shutdown. In one case, Denso data scientists reported to maintenance that a fan was going to fail in 58 hours and they should replace it. Raja explained: “Maintenance did not believe it. But we asked them to change it anyway. They took the fan out. Half the blades on the fan had disintegrated. They were totally shocked that they had no idea this was happening and we could provide that prediction.”
In another example they focused on direct aid to the operator of an automated assembly process with robots. We are used to the idea of operators filling out a control chart with upper and lower control limits and taking action before the process is out of control. This system continuously develops a control chart in real-time. When observing we noticed a few minutes early that the process was headed out of control and the operator made an adjustment quickly fixing the problem.
A more ambitious project that cuts to the heart of TPS is automated standardized work support. Raja found a Stanford professor working on “motion technology.” A camera videos a person and can in real time analyze the data with AI, for example chunking actions into work steps. Raja saw the potential for revolutionizing standard work and collaborated with the professor who now has a thriving company. The output will be familiar to those experienced with standardized work—steps and times versus takt, operator balance charts, and in effect real time auditing that identifies deviations from the standardized work. The analyst does not have to spend time creating all these sheets and can call up all cases where there was a line stop, or all cases where there was a certain type of deviation from standard, and go back and watch the video. What was the operator actually doing at that point? This technology is getting broad interest from around the world—including from Toyota.
Does the Technology Deskill, Replace, or Enhance?
A key question going back to when I first started studying the impact of computer-integrated technology in the 1980s is: does the technology deskill, replace, or enhance? And the answer then and now is that it depends on management philosophy. Consider two different approaches: mechanistic and organic. From a mechanistic perspective, the value of technology is clear—replace people, monitor those remaining, and control them with clear instructions on what to do. Implement the technology quickly and broadly to remove the unpredictable human element.
From an organic-systems perspective, the value of the technology is very different. When combined with highly developed people motivated toward goals of serving customer and helping the company, it can multiply kaizen—faster and better.
Raja made it clear what side of the fence he was on. Denso’s focus was not on using the technology to eliminate people, though he had no doubt that over time there would be a need for fewer people in the factory. While there would be cases where a closed-loop technical system diagnosed and automatically corrected problems, there would be plenty of issues that required human ingenuity and intervention. In fact, Raja is convinced that the skill requirements of the people need to grow.
“We will always need people, but their skill level needs to be completely shifted over time. The technology provides data that allows the associate and the team leaders at the gemba to provide a far higher level of decision making. In the past they would just fill out the paperwork, but by the time they did all that they had either no time or energy to really comprehend the data. If they want to see trends from say five days ago or across people, that just wasn't there. What this has provided is what we now call fast PDCA. We can’t afford to have PDCA that takes 3 weeks anymore. We want a PDCA done before the end of that shift.”
At Denso in Japan, they operate on the belief that IOT does not cut people out of the loop, but rather provides superior information to people about the process. The power of big data and artificial intelligence is to give the operator information just-in-time that they previously could only guess at. But Denso expects the operator to use that information creatively to find the root cause and solve the problem through kaizen. Denso calls this “collaborative creation and growth of human, things, and equipment.” One irony might come out of this. Historically, a major role of industrial engineers was to reduce the number of workers needed. Now, the technology might enable the workers to the point they can eliminate the industrial engineers.
Balancing Adoption of the Latest Technology with Effectiveness
Toyota is a technologically advanced company and has been for decades—shut down its computer systems and you shut down the company. But Toyota is not interested in being trendy and making adoption of new technology an end onto itself. Just as Toyota refuses to schedule parts made in one department to be pushed onto another, Toyota refuses to allow an information technology or advanced manufacturing technology department to push technology onto departments that do the value-added work of designing and building cars. Any information technology must meet the acid test of supporting people and processes and prove it adds value before it is implemented broadly. And then the ownership for introducing the new technology falls on existing management. They will run it, they will be responsible for meeting the targets, so they should lead the introduction.
The problem as I see it is that people living in the computer software world seem to believe if they can do a demonstration based on a simulated example, it should translate seamlessly into solving real problems in the outside world. That is the thinking that got companies in trouble back in the 1980s. And it was the situation that Raja of Denso encountered in the 21st century when he was exploring Industry 4.0 software. I was skeptical before talking to Raja about the bold concept of a fully-automated factory with everything run by internet connections, big data, and AI--and Raja confirmed my suspicions that it could be a lot of smoke and mirrors. On the other hand, I also was awakened to the strength of the technology. I am now convinced it is real and it includes the technologies missing from early failed attempts to computerize the factory in the 1980s. It seems they were not completely wrong about the potential, but just early.
It also became clear in seeing what Raja has been doing at Denso’s plant in Battle Creek that Industry 4.0 is not a disruptive force that makes TPS irrelevant, but rather can be an enabler that builds on TPS culture and thinking. After all, the Internet of Things necessarily includes things. And if the things are poorly designed, poorly laid out, and poorly maintained software will not solve the problem.
The difference between Denso and companies that are creating electronic wallpaper seems to be a matter of mindset. Denso starts with the problem and then builds the social and technical systems to help address the problem. It builds on its existing culture of disciplined execution and problem solving. Without this, companies are left to throwing the technology at the wall and hoping it sticks. The principles of TPS will not disappear from a company like Denso, but the way the factory operates under TPS + IOT will be very different.
I was fascinated by the IOT technologies I saw at Denso, but in the back of my mind I could not help but guess at the concerns of Toyota Production System. TPS is about forcing people to think deeply to solve problems. Will computer systems make us lazy thinkers? How can we marry the powerful information coming out of the computers with the creativity of people in developing and testing ideas for improvement?
I was encouraged by Akio Toyoda’s thoughts. It is clear he sees the possibility of combining the best of the new technology with the creativity of thinking people In a recent speech he said:
“Two concepts -- automation with people and Just-in-Time -- are the pillars of the TPS. What both have in common is that people are at the center. I believe that the more automation advances, the more the ability of the people using it will be put to the test. Machines cannot improve unless people do, too. Developing people with skills that can equal machines and senses that surpass sensors is a fundamental part of Toyota's approach.”
This article is from the upcoming revised edition of The Toyota Way, Second Edition (due out October 2020), which includes Principle 8: Adopt and Adapt Technology that Supports your People and Processes. It originally appeared in the Lean Post, the blog of the Lean Enterprise Institute, and is used with permission.
No comments:
Post a Comment