Sweden will soon be home to a major steel factory powered by the 'world's largest green hydrogen plant'
Anmar Frangoul CNBC
Established in 2020, H2 Green Steel will focus on steel made using a "fossil-free manufacturing process."
The firm says steel production will begin in 2024 and be based in the north of Sweden
Anmar Frangoul CNBC
2/25/2021
Established in 2020, H2 Green Steel will focus on steel made using a "fossil-free manufacturing process."
The firm says steel production will begin in 2024 and be based in the north of Sweden
.
© Provided by CNBC
A Swedish firm backed by investors including Spotify founder Daniel Ek plans to build a steel production facility in the north of the country that will be powered by what it describes as "the world's largest green hydrogen plant."
H2 Green Steel, which was established in 2020, will focus on steel made using a "fossil-free manufacturing process" and look to supply European manufacturers with its end product.
In an announcement earlier this week the company — which will be headed up by Henrik Henriksson, the current CEO of Scania — said steel production would start in 2024 and be based in Sweden's Norrbotten region. By 2030, the aim is for the business to have the capacity to produce 5 million tons of steel per year.
"The climate crisis is the biggest challenge of our time," Henriksson said in a statement issued Tuesday.
"And given … steel's impact on other industries' sustainable development, a rapid change of the steel industry is extremely important," he added.





According to the International Energy Agency, the iron and steel sector is responsible for 2.6 gigatonnes of direct carbon dioxide emissions each year, a figure that, in 2019, was greater than direct emissions from sectors such as cement and chemicals.
It adds that the steel sector is "the largest industrial consumer of coal, which provides around 75% of its energy demand."
The size of H2 Green Steel's hydrogen plant will be around 800 megawatts, with its end product replacing coal and coke in the steel manufacturing process.
Hydrogen can be produced in a number of ways. One includes using electrolysis, with an electric current splitting water into oxygen and hydrogen. If the electricity used in the process comes from a renewable source such as wind or solar then it's termed "green" or "renewable" hydrogen.
The company's biggest shareholder is investment firm Vargas, a co-founder of battery maker Northvolt. H2 Green Steel is currently wrapping up series A equity financing of 50 million euros (around $61.1 million). Investors include Scania, EIT InnoEnergy, and Spotify founder Daniel Ek.
For the initial phase of the project, total financing will come to roughly 2.5 billion euros. The firm's financial advisors are Societe Generale, KfW IPEX-Bank and Morgan Stanley.
Steel production is one of many industrial processes ripe for improvement when it comes to emissions and other metrics related to sustainability.
Aluminum manufacturing is another. German automaker BMW recently said it had started to source and use aluminum that has been produced using solar energy, for example.
A Swedish firm backed by investors including Spotify founder Daniel Ek plans to build a steel production facility in the north of the country that will be powered by what it describes as "the world's largest green hydrogen plant."
H2 Green Steel, which was established in 2020, will focus on steel made using a "fossil-free manufacturing process" and look to supply European manufacturers with its end product.
In an announcement earlier this week the company — which will be headed up by Henrik Henriksson, the current CEO of Scania — said steel production would start in 2024 and be based in Sweden's Norrbotten region. By 2030, the aim is for the business to have the capacity to produce 5 million tons of steel per year.
"The climate crisis is the biggest challenge of our time," Henriksson said in a statement issued Tuesday.
"And given … steel's impact on other industries' sustainable development, a rapid change of the steel industry is extremely important," he added.





According to the International Energy Agency, the iron and steel sector is responsible for 2.6 gigatonnes of direct carbon dioxide emissions each year, a figure that, in 2019, was greater than direct emissions from sectors such as cement and chemicals.
It adds that the steel sector is "the largest industrial consumer of coal, which provides around 75% of its energy demand."
The size of H2 Green Steel's hydrogen plant will be around 800 megawatts, with its end product replacing coal and coke in the steel manufacturing process.
Hydrogen can be produced in a number of ways. One includes using electrolysis, with an electric current splitting water into oxygen and hydrogen. If the electricity used in the process comes from a renewable source such as wind or solar then it's termed "green" or "renewable" hydrogen.
The company's biggest shareholder is investment firm Vargas, a co-founder of battery maker Northvolt. H2 Green Steel is currently wrapping up series A equity financing of 50 million euros (around $61.1 million). Investors include Scania, EIT InnoEnergy, and Spotify founder Daniel Ek.
For the initial phase of the project, total financing will come to roughly 2.5 billion euros. The firm's financial advisors are Societe Generale, KfW IPEX-Bank and Morgan Stanley.
Steel production is one of many industrial processes ripe for improvement when it comes to emissions and other metrics related to sustainability.
Aluminum manufacturing is another. German automaker BMW recently said it had started to source and use aluminum that has been produced using solar energy, for example.
BMW will now use aluminum that’s been made with solar power
PUBLISHED TUE, FEB 2 2021
Anmar Frangoul
KEY POINTS
BMW describes deal as “an important milestone” in its goal to cut carbon dioxide emissions from its supply network.
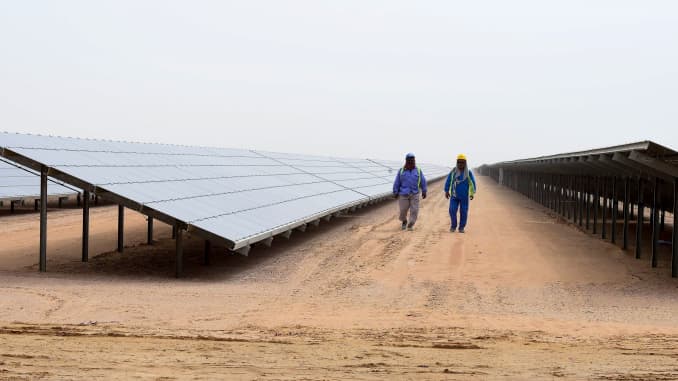
Workers photographed walking past a section of solar panels at the Mohammed bin Rashid Al-Maktoum Solar Park in Dubai on March 20, 2017.
STRINGER | AFP | Getty Images
BMW said Tuesday it had started to source and use aluminum that has been produced using solar energy, a move the German carmaker described as “an important milestone” in its goal to cut carbon dioxide emissions from its supply network.
A “triple-digit million-euro contract” will see Emirates Global Aluminium (EGA), an industrial firm based in the United Arab Emirates, provide BMW with 43,000 metric tons of aluminum this year.
BMW said EGA was the first business in the world to utilize solar electricity for commercial aluminum production.
The solar power used in the metal’s production process will come from the Mohammed Bin Rashid Al Maktoum Solar Park, a vast development located in desert south of Dubai. The aluminum will then be processed and turned into car parts at the light metal foundry of BMW’s plant in Landshut, Germany.
The “solar aluminium” sourced from the UAE will account for almost half of the yearly requirements of the Landshut foundry, according to BMW.
The deal announced Tuesday is part of a wider “long-term” strategy to source aluminum produced from renewables, which BMW says could save roughly 2.5 million metric tons of CO2 by the year 2030.
Shift to electric
BMW’s move comes as the firm — and other major car companies — attempts to ramp up its electric vehicle offering and challenge Elon Musk’s Tesla.
While electric vehicles have an advantage over diesel or gasoline when it comes to tailpipe emissions, there are clear challenges related to their manufacture.
In its announcement Tuesday, BMW acknowledged this: “The trend towards e-mobility means that a much larger percentage of a vehicle’s lifecycle CO2 emissions now comes from upstream added value in the supplier network,” it said.
“In an electrified vehicle, CO2 emissions from the use phase are much lower, but producing battery cells or aluminium is very energy-intensive,” it added.
Aluminum is seen as being particularly important going forward because, as BMW noted, its lightweight properties enable it to partially offset the heavy weight of batteries.
Using renewables to ‘green’ supply chains
The news of BMW’s plan to source aluminum produced using solar power comes a day after it was announced a turbine production plant owned by energy giant Vestas would be powered using an environmentally friendly source of gas.
In a statement Monday Earth Capital said its portfolio company, Black Dog Biogas, would send power to the Vestas factory, which manufactures blades for offshore wind turbines. Both sites are located on the Isle of Wight, off the south coast of the U.K..
The Black Dog plant is able to provide enough power to meet roughly 80% of the Vestas factory’s requirements.
PUBLISHED TUE, FEB 2 2021
Anmar Frangoul
KEY POINTS
BMW describes deal as “an important milestone” in its goal to cut carbon dioxide emissions from its supply network.
Aminum production process will come from the Mohammed Bin Rashid Al Maktoum Solar Park, south of Dubai.
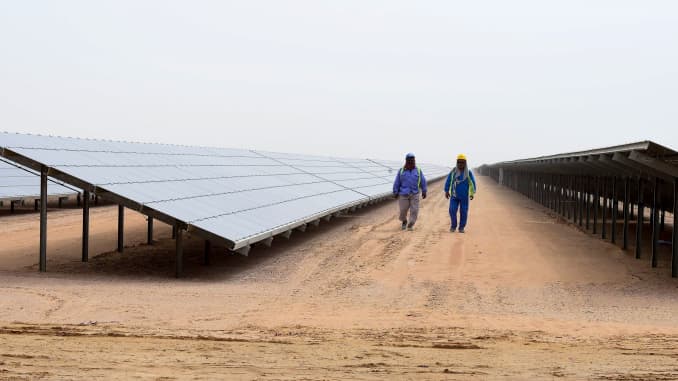
Workers photographed walking past a section of solar panels at the Mohammed bin Rashid Al-Maktoum Solar Park in Dubai on March 20, 2017.
STRINGER | AFP | Getty Images
BMW said Tuesday it had started to source and use aluminum that has been produced using solar energy, a move the German carmaker described as “an important milestone” in its goal to cut carbon dioxide emissions from its supply network.
A “triple-digit million-euro contract” will see Emirates Global Aluminium (EGA), an industrial firm based in the United Arab Emirates, provide BMW with 43,000 metric tons of aluminum this year.
BMW said EGA was the first business in the world to utilize solar electricity for commercial aluminum production.
The solar power used in the metal’s production process will come from the Mohammed Bin Rashid Al Maktoum Solar Park, a vast development located in desert south of Dubai. The aluminum will then be processed and turned into car parts at the light metal foundry of BMW’s plant in Landshut, Germany.
The “solar aluminium” sourced from the UAE will account for almost half of the yearly requirements of the Landshut foundry, according to BMW.
The deal announced Tuesday is part of a wider “long-term” strategy to source aluminum produced from renewables, which BMW says could save roughly 2.5 million metric tons of CO2 by the year 2030.
Shift to electric
BMW’s move comes as the firm — and other major car companies — attempts to ramp up its electric vehicle offering and challenge Elon Musk’s Tesla.
While electric vehicles have an advantage over diesel or gasoline when it comes to tailpipe emissions, there are clear challenges related to their manufacture.
In its announcement Tuesday, BMW acknowledged this: “The trend towards e-mobility means that a much larger percentage of a vehicle’s lifecycle CO2 emissions now comes from upstream added value in the supplier network,” it said.
“In an electrified vehicle, CO2 emissions from the use phase are much lower, but producing battery cells or aluminium is very energy-intensive,” it added.
Aluminum is seen as being particularly important going forward because, as BMW noted, its lightweight properties enable it to partially offset the heavy weight of batteries.
Using renewables to ‘green’ supply chains
The news of BMW’s plan to source aluminum produced using solar power comes a day after it was announced a turbine production plant owned by energy giant Vestas would be powered using an environmentally friendly source of gas.
In a statement Monday Earth Capital said its portfolio company, Black Dog Biogas, would send power to the Vestas factory, which manufactures blades for offshore wind turbines. Both sites are located on the Isle of Wight, off the south coast of the U.K..
The Black Dog plant is able to provide enough power to meet roughly 80% of the Vestas factory’s requirements.
No comments:
Post a Comment