Dec 10, 2020
by Michael Welch
The American Society of Mechanical Engineers
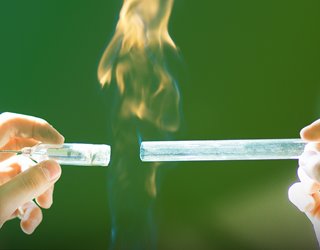
Hydrogen is the most abundant element in the universe. Engineers are working to overcome the challenges to producing hydrogen fuel at scale and adapting gas turbines to burn it.
This article is part of THECLEAN ENERGYCOLLECTION
This year is on track to be the hottest since measurements began, according to the National Oceanic and Atmospheric Administration (NOAA). The agency estimates there’s a 75 percent chance that 2020 temperatures will beat the record set in 2016, despite the temporary reduction in emissions due to the COVID-19 pandemic, continuing an upward trend in global temperatures that is altering the climate of our planet.
In 2015, nearly 200 nations agreed to respond to the threats of climate change by curbing emissions in order to keep the increase of average global temperatures below 2 °C above pre-industrial levels and try to limit increase to 1.5 °C. In order to meet those emission goals, many nations and organizations, including the European Union, are aiming to become carbon neutral by 2050. In a study published in Applied Energy last April, researchers indicate it’s possible, with the use of the right technologies, to reduce industrial greenhouse gas emissions to net zero by 2070.
Currently, between 30 and 40 percent of the electrical power in the world comes from gas turbines, most of which are powered by natural gas or other liquids that emit carbon dioxide—a major contributor to climate change. For that reason, manufacturers are looking to hydrogen, the most abundant element in the universe, as a fuel source in power generation turbines. Converting gas systems to use hydrogen fuel instead of a carbon-based fuel could, therefore, be an important link in decarbonizing the energy industry.
Despite the push to spend billions on research and development (R&D) to create this capability, hydrogen—which needs to be extracted from readily available molecules—has proven to be a difficult, and energy intensive, fuel to source. Many in the green sector are pushing for utilizing wind and solar energy to power the element’s extraction. However, the amount of resources currently required makes these ideas challenging from an economic perspective. Hydrogen is a clean-burning fuel, but its production is anything but clean or easy, at least for now.
There are, however, other ways to move us toward a hydrogen economy. Instead of running power generation turbines on 100 percent natural gas, as we do now, turbines could operate on combinations of natural gas and hydrogen, helping reduce carbon footprint while undertaking the challenges of using the new fuel in steps. To move forward, however, technological, economical and political challenges must be met with solutions that tackle each of these alone and in combination with one another, carving a path for hydrogen to become more commonplace in the energy sector.
From Grey to Blue to Green
Gas turbines convert fuels like natural gas into mechanical energy by pulling in ambient air at normal atmospheric pressure from the outside and increasing its pressure to anywhere between approximately 15 and 30 times atmospheric pressure. The engine then puts that air into a combustion can and mixes it with fuel. The fuel is ignited to create hot gases that expand over turbine stages, which turn the whole gas turbine and drive a generator, pump, or compressor.
With this very simple principle, the main objective from a combustion perspective is to mix the air and fuel in order to create very high temperature gasses that enter the turbine stages at 980 to 1370 °C. The result is exhaust gasses at temperatures of around 590 °C, which means the process is able to extract some 40 percent of the fuel energy in an open cycle configuration. Though, the fuel source for these turbines is typically natural gas, liquefied petroleum gas and alternative sources like diesel and even biogas are also common.
More on This Topic: Hydrogen Breakthrough Begins
What these fuels have in common, however, is they are all carbon-based, which means when they burn, they produce carbon dioxide, a major greenhouse gas, as a byproduct.
Hydrogen, a plentiful element in the environment, on the other hand, is considered a clean fuel source. High in energy with close to zero pollution, hydrogen does not occur as a gas on its own and can be found in organic matter, water, and hydrocarbons that make up fuels like gasoline, methanol, and natural gas. To use it, hydrogen needs to be extracted from these compounds via heat or electrolysis.
Extracting hydrogen from natural gas by adding steam produces carbon dioxide as a byproduct, which at the moment is vented into the atmosphere. For every kilogram of extracted hydrogen about 8 to 10 kilograms of carbon dioxide are generated. Hydrogen produced with such high emissions is known as grey hydrogen, with an overall carbon dioxide footprint that is worse than burning just natural gas.
To minimize this footprint, we would need a process to capture, store and sequester the carbon dioxide. Hydrogen produced as such is known as blue hydrogen. This can reduce carbon dioxide emissions to 1 to 1.5 kilograms of carbon dioxide per kilogram of hydrogen, making a massive reduction in carbon intensity of power generation.
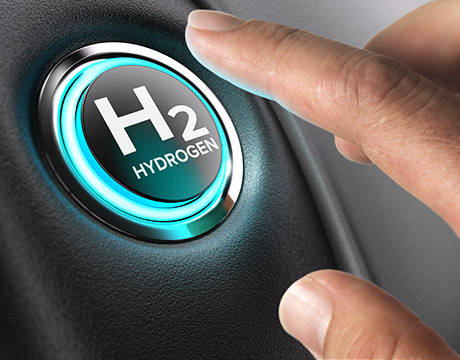
Being a very small molecule, hydrogen will leak through most materials. One would have to use the right type of steel materials, without any rubber or non-metallic seals. And current safety measures would need to be adjusted for the new fuel mix.For these reasons, environmental advocates have pushed to use wind and solar energy to power electrolyzers—devices that use electricity to separate water into hydrogen and oxygen—to extract hydrogen, where by inputting water, the only byproduct is oxygen. The problem with this approach for power generation is that the initial investment costs required are considerably higher than a conventional natural gas-fired power plant, because as well as the power plant, large wind and solar farms would be required along with the electrolyzers.
The idea also raises the question as to why use electricity to produce so-called green hydrogen instead of selling the electricity directly. The proposal is that in times when there's, for example, too much wind generation compared to load demand, or the electricity transmission system cannot handle the high quantities, we could divert this curtailed wind energy to produce hydrogen for medium- to long- term storage, and use the hydrogen later during periods of low wind generation. The challenge with this thinking is that the capital costs go up once again because of the expenditure to build the hydrogen storage facility. And so, whereas currently industrial hydrogen is between 1 and 2 dollars per kilogram, and blue hydrogen from steam methane reforming and carbon capture is probably in the 1.5 to 2.5 dollars per kilogram range, electrolysis costs will be 3 to 5.50 dollars per kilogram for green hydrogen in the short- and medium- term. Some analysts forecast the cost of green hydrogen could fall as low as the current levels of industrial hydrogen in regions with plentiful renewable energy resources, and certainly achieve parity with blue hydrogen. However, even this equates to a fuel price of 18 dollars per one million British Thermal Units (mmbtu), considerably higher than natural gas.
Further, wind and solar energy are not continuous. For example, for a power-to-hydrogen project based on an offshore wind farm with a capacity factor of around 45 percent, to produce a continuous flow of hydrogen at about 4 to 4.5 metric tons of hydrogen per hour, you would need a gigawatt scale wind farm, approximately 500 megawatts of electrolyzers and 1,000 metric tons of hydrogen storage. While this scale of plant may be appropriate for providing hydrogen to the industrial or transport sectors, the amount of hydrogen produced will barely run a 50-megawatt gas turbine, so one can begin to see the size of the challenge: The amount of renewable energy needed to provide the amount of green hydrogen required just for current industrial uses is immense.
If the goal is to use green sources for power as well, then we need many times the currently installed renewable energy capacities, which requires trillions of dollars of investments and years to construct, in addition to setting aside the large land or sea areas required for the solar photovoltaic (PV) devices and wind farms. Today, around 70 million metric tonnes per year (or 8,000 tonnes per hour) of ‘grey’ hydrogen is produced for industrial purposes. With a 50-megawatt gas turbine consuming about 4.5 tonnes per hour of hydrogen, 8,000 tonnes per hour of hydrogen equates to around 100 gigawatt of power generation capacity, whereas the current installed base for natural gas-fired generation is 1,644 gigawatt and this is forecast to rise to around 3,000 gigawatt by 2050. If hydrogen is to fully replace natural gas generation, global hydrogen production needs to increase thirtyfold, before we even consider displacing natural gas usage in industrial and domestic heating applications.
Why Hydrogen?
There isn't an easy way to decarbonize the energy industry or, in many countries, to decarbonize domestic heating. Those who live in climates where the winters are cold, like the U.K. or the northeast of the United States, use four times as much energy in the form of natural gas for heating and cooking as they do electricity. If we were all to switch to electric heating in our homes, we'd need five times as many power stations, or 20 to 30 times as much renewable energy, as we currently have. We’d also require five times as much transmission and distribution capacity, all of which create a major challenge.
Additionally, it’s not always technically or economically possible to simply retrofit electric options in industrial processes to displace combustion of natural gas or coal, so fossil fuels need to be replaced with something cleaner. The more pragmatic solution is using hydrogen as a fuel for domestic and industrial applications. At Siemens, we are involved in a project for Voestalpine in Linz, Austria, under the EU-Funded H2Future Project where they're using green energy to create hydrogen for use in steel mill steel production to displace some coke or coal. Another example of fossil fuel displacement is Cadent’s HyDeploy project at Keele University in the U.K. , which involves blending hydrogen into a natural gas network up to 20 percent by volume so they can partially decarbonize the heat network at the university.
The idea also raises the question as to why use electricity to produce so-called green hydrogen instead of selling the electricity directly. The proposal is that in times when there's, for example, too much wind generation compared to load demand, or the electricity transmission system cannot handle the high quantities, we could divert this curtailed wind energy to produce hydrogen for medium- to long- term storage, and use the hydrogen later during periods of low wind generation. The challenge with this thinking is that the capital costs go up once again because of the expenditure to build the hydrogen storage facility. And so, whereas currently industrial hydrogen is between 1 and 2 dollars per kilogram, and blue hydrogen from steam methane reforming and carbon capture is probably in the 1.5 to 2.5 dollars per kilogram range, electrolysis costs will be 3 to 5.50 dollars per kilogram for green hydrogen in the short- and medium- term. Some analysts forecast the cost of green hydrogen could fall as low as the current levels of industrial hydrogen in regions with plentiful renewable energy resources, and certainly achieve parity with blue hydrogen. However, even this equates to a fuel price of 18 dollars per one million British Thermal Units (mmbtu), considerably higher than natural gas.
Further, wind and solar energy are not continuous. For example, for a power-to-hydrogen project based on an offshore wind farm with a capacity factor of around 45 percent, to produce a continuous flow of hydrogen at about 4 to 4.5 metric tons of hydrogen per hour, you would need a gigawatt scale wind farm, approximately 500 megawatts of electrolyzers and 1,000 metric tons of hydrogen storage. While this scale of plant may be appropriate for providing hydrogen to the industrial or transport sectors, the amount of hydrogen produced will barely run a 50-megawatt gas turbine, so one can begin to see the size of the challenge: The amount of renewable energy needed to provide the amount of green hydrogen required just for current industrial uses is immense.
If the goal is to use green sources for power as well, then we need many times the currently installed renewable energy capacities, which requires trillions of dollars of investments and years to construct, in addition to setting aside the large land or sea areas required for the solar photovoltaic (PV) devices and wind farms. Today, around 70 million metric tonnes per year (or 8,000 tonnes per hour) of ‘grey’ hydrogen is produced for industrial purposes. With a 50-megawatt gas turbine consuming about 4.5 tonnes per hour of hydrogen, 8,000 tonnes per hour of hydrogen equates to around 100 gigawatt of power generation capacity, whereas the current installed base for natural gas-fired generation is 1,644 gigawatt and this is forecast to rise to around 3,000 gigawatt by 2050. If hydrogen is to fully replace natural gas generation, global hydrogen production needs to increase thirtyfold, before we even consider displacing natural gas usage in industrial and domestic heating applications.
Why Hydrogen?
There isn't an easy way to decarbonize the energy industry or, in many countries, to decarbonize domestic heating. Those who live in climates where the winters are cold, like the U.K. or the northeast of the United States, use four times as much energy in the form of natural gas for heating and cooking as they do electricity. If we were all to switch to electric heating in our homes, we'd need five times as many power stations, or 20 to 30 times as much renewable energy, as we currently have. We’d also require five times as much transmission and distribution capacity, all of which create a major challenge.
Additionally, it’s not always technically or economically possible to simply retrofit electric options in industrial processes to displace combustion of natural gas or coal, so fossil fuels need to be replaced with something cleaner. The more pragmatic solution is using hydrogen as a fuel for domestic and industrial applications. At Siemens, we are involved in a project for Voestalpine in Linz, Austria, under the EU-Funded H2Future Project where they're using green energy to create hydrogen for use in steel mill steel production to displace some coke or coal. Another example of fossil fuel displacement is Cadent’s HyDeploy project at Keele University in the U.K. , which involves blending hydrogen into a natural gas network up to 20 percent by volume so they can partially decarbonize the heat network at the university.
Currently, less than 1 percent of the global installed gas turbine fleet is operating on a hydrogen-rich fuel, and only one refinery in Italy claims to run on 100 percent hydrogen. The composition of the fuel gases in refineries varies hour by hour. Therefore, one has to design a system so it runs on different fuels at different times of operation. For example, in a refinery project we’ve designed for use for Braskem, a Brazilian petrochemical company, the system can run on varying hydrogen concentrations from zero to 60 percent by volume with no impact on performance.
Although not the zero carbon emissions that people aspire to, hydrogen-rich fuel gas blends can cut CO2 emissions enough to make an impact on global emissions now. For example, with a blend of 20 percent hydrogen and 80 percent natural gas, carbon dioxide emissions can be cut by about 7 percent. Increasing the blend to 60 percent hydrogen will provide about a 20 percent carbon dioxide reduction. The technology is currently available to achieve these CO2 reductions and put us on course to limit global temperature rises to below 2 degrees Celsius, while helping the hydrogen economy to develop at the pace needed to achieve net zero carbon emissions by 2040 or earlier. Of course, these numbers are not necessarily the big reductions that many would like to see immediately but it's a step in the right
direction.
A Two-Step Goal
In an agreement announced by EU Turbines in January 2019, gas turbine manufacturers in Europe, which basically includes every major gas turbine supplier in the world, committed to provide gas turbines able to operate on 20 percent hydrogen by volume in combination with natural gas by 2020 and for customers to be able to acquire gas turbines for operation on 100 percent hydrogen by 2030. While the ultimate aim is be using 100 percent hydrogen, it’s clear it won’t be easy to achieve this in one big bold step. Initially, most turbines are likely to operate more on blends with much less than 100 percent hydrogen because there simply isn't enough hydrogen available, as acquiring sufficient hydrogen at an affordable cost for operating solely on hydrogen is going to be a significant challenge.
For example, for a thirty-minute whole engine test on a gas turbine at our Finspong factory in Sweden, we basically had to source every spare bit of hydrogen in that nation and extend the search to some neighboring countries. There simply isn’t enough of it readily available.
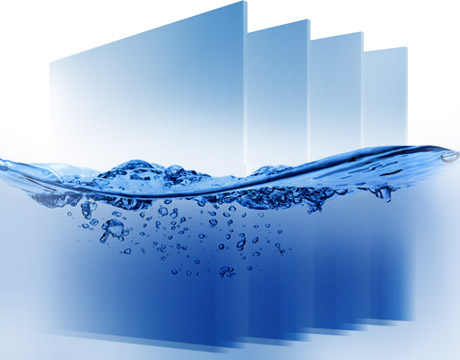
Environmental advocates have pushed to use wind and solar energy to power electrolyzers—devices that use electricity to separate water into hydrogen and oxygen—to extract hydrogen, where by inputting water, the only byproduct is oxygen.To aid this shortcoming, some of the projects in Europe, and in the U.K. in particular, are aiming to create a sufficient supply of hydrogen at a reasonable cost in order to start decarbonizing industrial sectors and replacing natural gas with hydrogen in high quantities. Six industrial clusters in the U.K. have been identified for additional funded studies to decarbonize industry and power generation, with some of these clusters proposing to use ‘blue’ hydrogen and carbon capture technologies.
Once that challenge is met, the turbines would need to be retrofitted to accommodate the new fuel mixtures. The combustion systems, a major area for change, are currently designed for natural gas with a specific flammability range and flame speed of a fuel that contains predominantly methane.
Hydrogen, on the other hand, has a much faster flame speed—approximately 10 times as fast as methane—and a wider flammability range, so it can burn when, and where, it isn’t wanted. Therefore, the fuel injectors need to be redesigned to create a flame profile and position that the combustion system can cope with. Further, as hydrogen flame burns hotter than natural gas flame, increases in thermal nitrogen oxides (NOx) also occur.
The next challenge is getting the hydrogen into the combustion system. Being a very small molecule, hydrogen will leak through most materials. One would have to use the right type of steel materials, without any rubber or non-metallic seals. And current safety measures would need to be adjusted for the new fuel mix. For example, a gas detector that's for standard natural gas will not detect a hydrogen leak.
Also, hydrogen burns with a different color flame, so a flame detector designed to sense the blue flame from natural gas wouldn’t pick up a hydrogen flame, which is virtually invisible to the naked eye.
These challenges are well understood and solutions to overcome them have already been mapped out. From a technology perspective, there is confidence that the gas turbine industry will get to 100 percent hydrogen with low emissions at some point. The biggest challenge, therefore, is an economic one—having enough hydrogen at a reasonable cost so that energy doesn’t end up costing three or four times as much as what we’re paying for today.
To that end, nearly every turbine manufacturer is currently working on this issue by responding to industry demands. Globally, politicians, especially in Europe, are pushing for decarbonization. And no matter how much we improve the efficiency of turbines running on fossil fuels, it is not going to hit their CO2 reduction targets. So we’ve either got to have carbon capture on the power plants, or use a zero carbon fuel.
Further, gas pipeline companies are taking an interest in the technology because if, say by the mid-2030s, politicians decide that no more fossil fuels will be used, there will be thousands of miles of pipeline which will become stranded assets. So gas companies are looking at how they can repurpose those assets for either transporting carbon dioxide for sequestration or transporting natural gas and hydrogen blends down existing piping systems. Re-purposing existing infrastructure assets could be critical in keeping down the costs of the energy transition.
For turbine manufacturers the major challenge is where the hydrogen will come from. That's what markets and the politicians need to really think about. There's no point pushing researchers and companies to develop 100 percent hydrogen-capable gas turbines by 2030 if it will take another 30 years before there’s enough hydrogen to run a turbine.
If the push is for companies to spend millions on research and development to create 100 percent hydrogen capability, there needs to be enough fuel to run the gas turbines on. And while wind farms, electrolyzers and green hydrogen with zero carbon footprint is a great idea, if 1,000 megawatts of wind farm are required to run a 50-megawatt gas turbine continuously, the setup will be impractical. So we need to be looking at the various methane reforming options and carbon capture more seriously.
It’s Political
While there are technical and environmental challenges of utilizing hydrogen as a fuel, the overall political dimension of the issue is often overlooked. Add to that the varying politics of each region or nation and the energy field becomes a patchwork of approaches that resembles a multi-fabric, multi-design quilt.
Germany, for example, doesn't believe in carbon capture because the nation doesn't really have any suitable geological formations where it can store captured carbon dioxide. On the other hand, Norway, the U.K. and Australia are quite comfortable with carbon capture and sequestration as they have depleted offshore oil and gas fields where captured CO2 can be stored. In fact, Norway has for many years been sequestering CO2 in the Utsira aquifer offshore. And the U.S. has been using carbon dioxide for enhanced oil recovery in Texas in the Permian Basin and in Wyoming for years, as have the Canadians, in order to maximize oil recovery from older oilfields.
Additionally, many governments don't want to relax environmental legislation, creating a challenge to meet similar emission levels with hydrogen as required with natural gas. So, if these governments insist on lower and lower NOx emissions with hydrogen, a turbine alone isn’t enough to achieve that. This means there would have to be post-combustion exhaust cleanup systems to achieve single digit NOx levels, which increases the cost of power even more. The end result is a more expensive plant and fuel, pushing up the cost of energy that then becomes a political no-no. Because, while everybody wants clean power, nobody wants to pay a lot more for it and it’s essential for our future that energy poverty is eradicated.
At its core, having this technology succeed is about finding a technological, economical, and political balance, where we can have this abundant clean electricity that's available 24 hours a day, seven days a week, 365 days a year. It's a complex area with multiple strategies that have got to come together with compromises that need to be made in all areas to get the get the whole hydrogen economy moving in the right direction.
Perhaps it’ll serve us to learn from the past: One such example is the biomass gasification is initiative where efforts were focused so much on intellectual research, conducting studies and trying to find what the ultimate best possible solution was, it created an environment that led to nothing being built. One can certainly reduce costs far quicker by building commercial-scale demonstration plants and repeating designs and learning from them, than by more research and development to try and improve things by a fraction of a percent. You build your first plant. Prove it, test it, and then you can go back and knock 10 or 15 percent of the cost of the plant and continue cutting costs by repeating designs and learning, instead of promising the Earth and not delivering.
Fortunately, governments in Europe have become much more pragmatic and see this as the step we need to take. They realize that though it's not quite the efficiency levels, emissions reductions and low costs we are ultimately seeking, this is going to get us from where we are today to where we need to be in 2040, as opposed to trying to make that revolutionary jump in one go and failing. It's much more of an evolutionary process. Certainly in Europe, the political scene, good support, and realistic approach are there.
Europe is not aiming for an interplanetary shot with a first rocket. Instead, our goals are realistic.
Michael Welch is an industry marketing manager at Siemens Industrial Turbomachinery in Lincoln, U.K.
No comments:
Post a Comment