
Is Green Concrete Truly Environmentally Friendly?
In a race to develop clean energy technologies, a question appeared: ‘Is green concrete truly environmentally friendly?’
Every year, over 4 million tons of concrete are produced, accounting for approximately 8% of global CO2 emissions. concrete production is a difficult and complex industry, which involves transformation in powerful furnaces of limestone and clay. The resulting heat releases large quantities of carbon dioxide. Transport and extraction of these raw materials are also sources of CO2 emissions into the atmosphere.
Although the National Recovery and Resilience Plan (NRRP) can play a major role in reducing the carbon footprint, quite many obstacles are in the way of deep decarbonization of concrete. The sector is dominated by a handful of important manufacturers, which are cautious in terms of creating new products that would calls into question the already existing ones. Alternative materials are not always easy to procure. In the meantime, architects, engineers, entrepreneurs, and customers are prudent regarding the new building materials. Therefore, implementation of new practices is a factor that cannot be neglected for millions of workers involved in the use of concrete in the urban landscape.
DECARBONATED CONCRETE – PROJECTS AND INITIATIVES OF SOME EUROPEAN COUNTRIES
Belgium. LEILAC project
The Belgian construction market absorbs approximately 6.5 million tons of concrete, of which approximately 75% is domestically produced concrete. National consumption amounts to over 576 kg of cement per capita (figure from 2020), which places it in the leading position compared to the neighbouring countries. The three large cement groups that carry out their activity in Belgium (Holcim, CCB Ciment, Eloy Beton) are based in Tournai, Mons, and Liège, where limestone-rich deposits ensure the necessary raw materials for the manufacturing of clinker. The current trend in the industry is to focus on the formation of increasingly large units, which is necessary to optimize productivity and efficiency of the necessary environmental protection investments.

LEILAC 1 Pilot plant at the HeidelbergCement plant in Lixhe, Belgium
To find a more environmentally friendly solution, the CBR Lixhe factory has put into practice a pilot project (LEILAC), which consists of a new carbon capture technology.
LEILAC project, financed by the EU, has developed a new technology which is expected to contribute to the significant reduction of emissions in the European cement and lime industries. In its factory in Lixhe, LEILAC uses a system that captures pure CO2, released during lime calcination (CaO), which is possible due to the separation of the furnace exhaust gases. This elegant solution does not require chemicals or additional processes to obtain a pure CO2 flow. On the project’s website it is mentioned: “When making lime or concrete CO2 is released as an intrinsic part of the production process and cannot be avoided (for example by using renewable energy). As such, carbon capture is the only realistic means by which these industrial emissions can be further reduced to support EU to be carbon neutral by 2050.”
“It is simply a new type of furnace, whose design allows an intrinsic separation of CO2, which comes out cold and very pure, which makes it a potentially valuable raw material for existing niche markets, such as greenhouses and mineralization in the concrete industry,” explains Daniel Rennie, Calix company representative who coordinates the LEILAC project. The project lasted from May 2019 until the end of 2020.
Following LEILAC success, it was decided to develop a second project, LEILAC 2. It refers to a new reactor, with a size equivalent to approximately one fifth of that of a commercial concrete factory and will focus more on the final destination of CO2 extracted during the process and, possibly, by the electrical production of the heat needed to obtain clinker. LEILAC will keep approximately half of the previous partners, especially Calix and HeidelbergCement.
“We want to be ready from a technological point of view once the carbon price makes the solution viable. If we don’t do it now and if we wait until the carbon price is set at 100 euros per ton, it will take another ten years and we have no time to lose,” says Jan Theulen, from HeidelbergCement, project partner.
Germany develops the Catch4climate project
For the first time, four European cement producers – Buzzi Unicem SpA-Dyckerhoff GmbH, HeidelbergCement AG, SCHWENK Zement KG and Vicat SA – join forces to cope with a major challenge: to contribute to the significant reduction of cement-related CO2 emissions. The Catch4climate project will allow the reuse of captured CO2 as raw material in other industrial processes. Therefore, the European concrete industry will be able to significantly reduce its CO2 emissions, bringing a major contribution to climate problems. At the end of last year, the four European cement producers that form the Cement Innovation for Climate (CI4C) joint-venture signed a Letter of Intent on the following steps of the Catch4climate pilot project. This project consists of creating a pre-industrial demonstrator of the Oxyfuel technology, on the site of the SCHWENK concrete factory in Mergelstetten, Germany. Oxyfuel Technology Oxyfuel principle (‘oxygen and fuel’) is based on the introduction of pure oxygen into a cement kiln instead of ambient air, to ensure the production of heat at high temperatures necessary for the manufacture of the clinker. In this way, the gases resulting from combustion are very pure in CO2, which greatly facilitates its capture.
Lengfurt concrete factory in Bavaria, Platinum certified
In mid-May this year, HeidelbergCement completed a campaign of certification of the Concrete Sustainability Council (CSC) at the 10 concrete plants, 12 concrete factories and five aggregates sites that were subject to the certification process. Lengfurt concrete factory in Bavaria and two concrete factories have obtained the Platinum certification. Lengfurt factory is the first concrete factory in Germany with Platinum certification.
“CSC certification allows production sites to gain a holistic understanding of their sustainability performance and our successful engagement in CSC certification highlights our commitment to sustainability,” points out Christian Artelt, senior manager sustainable construction and public affairs.
Carbon-free concrete, an ecological innovation Made in France
In France, Lafarge, Ciment Calcia, Hoffmann Green are companies in the concrete industry that propose carbon neutrality in their production chain, by 2050.
In 2020: CEM II/C-M (M for mixture) and CEM VI are the so-called ‘ternary’ blends, i.e., composed of clinker, cement compounds (slag, ash or pozzolan) and limestone. Their clinker content varies from 50 to 65% for CEM II/C-M and from 35 to 50% for CEM VI.
In 2021: LC3 (calcined clay limestone cement), composed of clinker, limestone and metakaolin (calcined clay), LC3
To find a more environmentally friendly solution, the CBR Lixhe factory has put into practice a pilot project (LEILAC), which consists of a new carbon capture technology.
LEILAC project, financed by the EU, has developed a new technology which is expected to contribute to the significant reduction of emissions in the European cement and lime industries. In its factory in Lixhe, LEILAC uses a system that captures pure CO2, released during lime calcination (CaO), which is possible due to the separation of the furnace exhaust gases. This elegant solution does not require chemicals or additional processes to obtain a pure CO2 flow. On the project’s website it is mentioned: “When making lime or concrete CO2 is released as an intrinsic part of the production process and cannot be avoided (for example by using renewable energy). As such, carbon capture is the only realistic means by which these industrial emissions can be further reduced to support EU to be carbon neutral by 2050.”
“It is simply a new type of furnace, whose design allows an intrinsic separation of CO2, which comes out cold and very pure, which makes it a potentially valuable raw material for existing niche markets, such as greenhouses and mineralization in the concrete industry,” explains Daniel Rennie, Calix company representative who coordinates the LEILAC project. The project lasted from May 2019 until the end of 2020.
Following LEILAC success, it was decided to develop a second project, LEILAC 2. It refers to a new reactor, with a size equivalent to approximately one fifth of that of a commercial concrete factory and will focus more on the final destination of CO2 extracted during the process and, possibly, by the electrical production of the heat needed to obtain clinker. LEILAC will keep approximately half of the previous partners, especially Calix and HeidelbergCement.
“We want to be ready from a technological point of view once the carbon price makes the solution viable. If we don’t do it now and if we wait until the carbon price is set at 100 euros per ton, it will take another ten years and we have no time to lose,” says Jan Theulen, from HeidelbergCement, project partner.
Germany develops the Catch4climate project
For the first time, four European cement producers – Buzzi Unicem SpA-Dyckerhoff GmbH, HeidelbergCement AG, SCHWENK Zement KG and Vicat SA – join forces to cope with a major challenge: to contribute to the significant reduction of cement-related CO2 emissions. The Catch4climate project will allow the reuse of captured CO2 as raw material in other industrial processes. Therefore, the European concrete industry will be able to significantly reduce its CO2 emissions, bringing a major contribution to climate problems. At the end of last year, the four European cement producers that form the Cement Innovation for Climate (CI4C) joint-venture signed a Letter of Intent on the following steps of the Catch4climate pilot project. This project consists of creating a pre-industrial demonstrator of the Oxyfuel technology, on the site of the SCHWENK concrete factory in Mergelstetten, Germany. Oxyfuel Technology Oxyfuel principle (‘oxygen and fuel’) is based on the introduction of pure oxygen into a cement kiln instead of ambient air, to ensure the production of heat at high temperatures necessary for the manufacture of the clinker. In this way, the gases resulting from combustion are very pure in CO2, which greatly facilitates its capture.
Lengfurt concrete factory in Bavaria, Platinum certified
In mid-May this year, HeidelbergCement completed a campaign of certification of the Concrete Sustainability Council (CSC) at the 10 concrete plants, 12 concrete factories and five aggregates sites that were subject to the certification process. Lengfurt concrete factory in Bavaria and two concrete factories have obtained the Platinum certification. Lengfurt factory is the first concrete factory in Germany with Platinum certification.
“CSC certification allows production sites to gain a holistic understanding of their sustainability performance and our successful engagement in CSC certification highlights our commitment to sustainability,” points out Christian Artelt, senior manager sustainable construction and public affairs.
Carbon-free concrete, an ecological innovation Made in France
In France, Lafarge, Ciment Calcia, Hoffmann Green are companies in the concrete industry that propose carbon neutrality in their production chain, by 2050.
In 2020: CEM II/C-M (M for mixture) and CEM VI are the so-called ‘ternary’ blends, i.e., composed of clinker, cement compounds (slag, ash or pozzolan) and limestone. Their clinker content varies from 50 to 65% for CEM II/C-M and from 35 to 50% for CEM VI.
In 2021: LC3 (calcined clay limestone cement), composed of clinker, limestone and metakaolin (calcined clay), LC3
concrete has a higher physical strength than current cements and an environmental footprint reduced by 35 to 40% compared to CEM I. This type of concrete will be included in the European standard EN 197 -1, which is the benchmark in Europe. This composition offers mechanical performance and durability similar to current cements, with a reduction of the environmental footprint from 35 to 65% compared to CEM I, the concrete used for the construction of structures.
Research is currently underway to develop new clinkers, characterized by a lower formation temperature and which allows a reduction of the environmental footprint by about 30%.
Such projects include the ECO-Binder European Research Project, which brings together 14 partners, concrete producers, laboratories, and technical control offices. So far, the results suggest that for a 30% reduction of the environmental footprint there will be a gain of 20% in thermal insulation properties and an increased fire resistance capacity. At normative level, a specific standard will be necessary, at which the ECO-Binder project is already working in close collaboration with the European Committee for Standardization CEN/TC51.
HGCT – ‘carbon-free concrete’
Hoffmann Green Cement Technologies (HGCT) is a pioneer in its field, as it is the first in the world to offer carbon-free concrete. The objective of HGCT Hoffmann Green Cement Technologies is to reduce carbon emissions related to the concrete manufacturing process: zero waste, zero discharge, zero inconvenience, no quarry, use of renewable energy and manufacture of environmentally friendly short-circuit products. They use three innovative technologies: H-P2A, H-UKR and H-EVA. These acronyms represent the manufacture, conservation of natural resources and perfect compatibility with current manufacturing procedures. Each of these technologies symbolize a green cement adequate for each specific need. H-P2A is used to create 100% mineral adhesives, H-UKR is intended for the industrial concrete market (ready mixed), and H-EVA is dedicated to mortar and plaster, construction concrete and road binders.
Italy. Green concrete, an emergency!
If the situation was already worrying in recent years, the image of the Ispra 2020 land use report in Italy is alarming. Two square meters of concrete are produced every second. And this clearly means that two square meters of green or, in any case, of soil are irretrievably erased. In the largest cities, that is metropolis, the year 2019 recorded the loss of 24 square meters per hectare of green area. Overall, about 50% of national soil losses in the last year are concentrated in urban areas, 15% in central and semi-central areas, 32% in peripheral and less dense areas. The eight ball goes to Rome with a loss of 75 hectares in total (of which 57 ha in the green areas of the city). Milan devoured 11.5 hectares of land in one year (of which 11 are green areas). Turin is the only city that stands out with the least land loss, remaining the only positive reality in this bleak image.
As far as regions are concerned, Veneto has some of the largest losses: over 923 hectares. It is followed by Lombardy (633 hectares), Puglia (425), Emilia-Romagna (381) and Sicily (302).
ECO-Binder project in Italy, Romania, Spain, and the UK
The ambitious ECO-Binder project, financed by the EU, continues in five testing locations in Italy, Romania, Spain, and the UK. Specialists aimed to develop an environmentally friendly solution to drastically reduce the carbon footprint of concrete manufacturing. However, the objectives of the team went much further. Researchers took advantage of the opportunity of integrating more safety, comfort, and stability in a single package of products at a competitive price. Concrete is formed by mixing a binder, usually cement, with water. Belite-Y and Ye’elimite-Ferrite (BYF) cement binders are a family of environmentally friendly materials. The performance of the new class of cements is comparable to that of OPC. However, lower calcium content, lower combustion temperature and lower energy demand for grinding result in approximately 30% less CO2 emissions associated with concrete production.
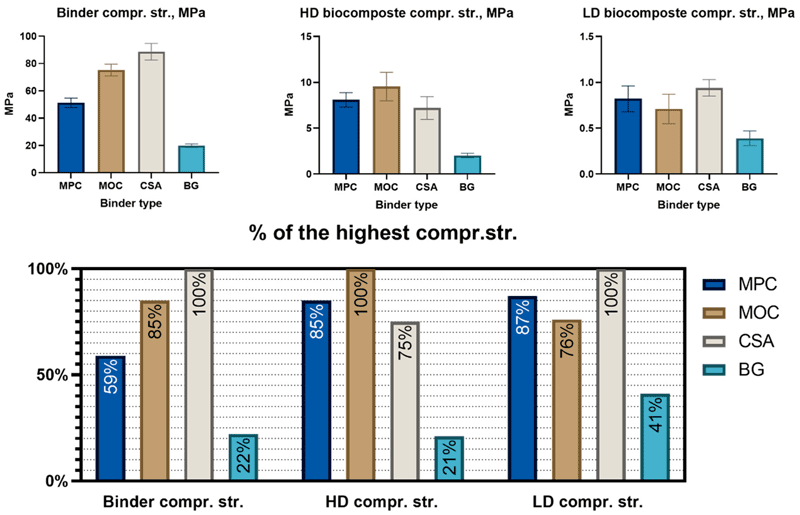
In 2018-2020 (the first two years of the four-year project), the team demonstrated the feasibility of prefabricated elements combining new BYF binders and the manufacture of advanced functional finishing materials.
Proven success
Four different concrete materials, manufactured with three BYF and OPC cements were used at small-scale models in Romania, Spain, and the UK and at a testing plant in Spain.
According to Arianna Amati, coordinator of the project, the target reached was large-scale production of BYF concrete. 11-meter-high monolithic panels were installed and tested in a real-world scenario on the demonstration site in Mantua, Italy. “165 m2 of facade of the structure were built with prefabricated BYF concrete components in order to demonstrate the complete replacement of the OPC-based product on a full scale,” explains Arianna Amati. The tests of these small- and large-scale models have confirmed the success of project objectives. Prefabricated panels with the new BYF products showed a 24% lower ‘gray energy’, as well as a 24% reduction in carbon footprint. Moreover, insulation properties were improved by 10%. Lower hygrometric shrinkage of BYF concrete (higher dimensional stability) without the use of additives has led to a reduction in air losses. All of these were delivered at a cost 15% lower than conventional OPC products.
Poland: Concrete, gypsum, plaster, and mortar obtained from ash
In turn, Poland is facing high costs for fulfilling the European agreement to reduce CO2 emissions by 40% by 2030 and for reaching carbon neutrality by 2050. The Polish Cement Association (SPC) has forecast a 2% year-on-year drop in cement sales to 18.5 million tons in 2021. In 2020, concrete imports made by Poland with Belarus increased by 80% (440,000 tons) and those in Ukraine climbed by 50% (around 32,000 tons). SPC has expressed its firm support for the European Carbon Border Adjustment Mechanism (CBAM) as a means of protecting industry against imports from both non-EU neighbouring countries and through polluting transport from concrete exporters abroad, such as in Turkey.
EKO-ZEC, a Polish subsidiary of Veolia, collects ash from burning coal and uses it in concrete production. Since the beginning of 2017, part of the surplus was exported to other European countries. EKO-ZEC produces up to 650,000 tons of ash per year, a figure that exceeds by far the local demand, especially in winter months, when there are fewer sites and demand for concrete is lower, and the surplus is obviously exported, especially to countries with fewer coal-fired power plants. Due to these new distribution channels, EKO-ZEC and Veolia contribute to circular economy in Europe!
Romania. ECOPact – the widest range of green concrete in the industry
Local cement market had a value of EUR 630 million in 2020, according to data from the National Institute of Statistics. Compared to EUR 570 million in 2019, it results in a 10% growth of this sector last year.
2021 brought, through Holcim, for the first time in the industry of building materials in Romania, ECOPact – the widest range of green concrete in the industry, with CO2 emissions reduced by over 30%, created to accelerate transition to sustainable construction. At the same time, the company develops a new business model – ECONCEPT, which is based on three complementary directions: ECO Solutions (green products and solutions, with low CO2 footprint); ECO Services (consulting and instruments for building sustainable projects) and ECO Score (evaluation and certification of climate performances of products in the portfolio). The new range of green concrete has a wide range of uses, from residential and non-residential civil constructions, industrial and hydrotechnical constructions, special industrial constructions and to special constructions for water transport and marine structures.
With the new business model, the company has set new targets in terms of sustainability, in accordance with the ‘Net Zero’ commitment that LafargeHolcim Group signed up to last year, at global level. The latter has the goal of reaching CO2 emission neutrality by 2050.
Switzerland. LC3, one of the technologies with the greatest potential to reduce CO2 emissions
A consortium led by the Federal Polytechnic School of Lausanne (EPFL) has received support from the Swiss Agency for Development and Cooperation (SDC) worth more than 4 million francs to accelerate the development and testing of a new type of concrete with low impact on the environment. Developed in partnership with the Institutes of Technology in India and various universities in Cuba and Brazil, this product based on a mixture clay and limestone could replace up to half of the traditionally used Portland concrete, reducing by up to 40% CO2 emissions caused by this material. Researchers, who have actively collaborated with industrial and government partners, hope to make LC3 the new benchmark for the largest companies in the field. Two industrial-scale pilot projects, carried out in India and Cuba, have already proven the efficiency of the product and ease with which it can be integrated into the current production chain. “If we truly want to make concrete more attractive in terms of durability, cost, availability and environmental impact, we must act before demand explodes in developing countries,” concludes Karen Scrivener, who heads EPFL’s Building Materials Laboratory.
LC3 – short history
In 2004, prof. Karen Scrivener from EPFL Switzerland and prof. Fernando Martirena from UCLV Cuba discussed for the first time about the use of calcined clays for pozzolans, and in 2005, the two professors launched together the first research project on this topic supported by the Swiss National Scientific Foundation (SNSF) and the Swiss Development Agency and Cooperation (SDC). In 2009, a second project supported by the SNSF and SDC on materials research began to focus on ternary blended cement with clay and limestone. During this project, from 2009 until 2012, the huge potential of calcined clay was fully recognized.
In 2013, EPFL started a global project: concrete from calcined clay. In addition to the laboratory in Cuba, it was decided to open a second laboratory in India, due to the significant potential to increase the volume of construction materials.
In 2014, the first three-year phase of the LC3 project had as main objective the technical verification of LC3 technology. It involved the development of an academic network for the research of LC3 cements. Consequently, it could be proven that LC3 achieves OPC – CEM I quality and is suitable for global launch.
From 2017 until 2020, the SDC financed another three-year phase with the same team of academic partners in Switzerland, Cuba, and India. Within this phase, the LC3-Project mainly worked on verifying the economic attractiveness of the material and increasing the awareness in industrial and policy circles. Several LC3-applications were built in different parts of the world that are exposed to different environmental conditions. During the phase academic, industrial and policy circles widely acknowledged LC3 as one of the technologies with the highest potential to lower CO2-emissions in the concrete sector. Also, the first permanent large-scale production of LC3 started within the second project phase in Colombia.
Since September 2020, the LC3-Project extends its technology globally. Several new LC3-productions are on the way. The project has received high attention by Bloomberg and TED-talks.
Houses of the future without cement?
Northern countries do what they do best: they are always one step ahead in terms of environmental protection.
As part of a pilot project supported by green funds from the Danish Ministry of Environment, architects from Een til Een have built the world’s first house from waste and scrap materials from the agricultural industry. Whilst houses made from natural materials are nothing new, as numerous examples can be found in the huts of tribes living in jungles and forests around the world, in this case they are made from materials that have undergone a process of transformation and recycling. Hay and rice straw, reed, hemp, flax, algae and other cellulosic fibres, materials that are normally considered waste and are usually used as fuel for energy production, are given a new life in this project and become raw materials for construction.
The CO2 captured by these materials is not re-emitted into the atmosphere as a result of their combustion. On the other hand, the recycling of locally available materials promotes the local economy. This ‘organic’ house, as the architects themselves have dubbed it, has been designed and produced using digital technologies. Moreover, it is a fully integrated building with natural ventilation and passive solar heating, not to mention that the recycled materials are breathable. The house also sits on screw piles, instead of the traditional concrete foundation, which means better insulation and ventilation, whilst at the same time having less impact on the land on which it stands. For the cladding, wood from local sustainable forests is used, with a special treatment, also biological, which makes it resistant, durable, and dimensionally stable.
Research is currently underway to develop new clinkers, characterized by a lower formation temperature and which allows a reduction of the environmental footprint by about 30%.
Such projects include the ECO-Binder European Research Project, which brings together 14 partners, concrete producers, laboratories, and technical control offices. So far, the results suggest that for a 30% reduction of the environmental footprint there will be a gain of 20% in thermal insulation properties and an increased fire resistance capacity. At normative level, a specific standard will be necessary, at which the ECO-Binder project is already working in close collaboration with the European Committee for Standardization CEN/TC51.
HGCT – ‘carbon-free concrete’
Hoffmann Green Cement Technologies (HGCT) is a pioneer in its field, as it is the first in the world to offer carbon-free concrete. The objective of HGCT Hoffmann Green Cement Technologies is to reduce carbon emissions related to the concrete manufacturing process: zero waste, zero discharge, zero inconvenience, no quarry, use of renewable energy and manufacture of environmentally friendly short-circuit products. They use three innovative technologies: H-P2A, H-UKR and H-EVA. These acronyms represent the manufacture, conservation of natural resources and perfect compatibility with current manufacturing procedures. Each of these technologies symbolize a green cement adequate for each specific need. H-P2A is used to create 100% mineral adhesives, H-UKR is intended for the industrial concrete market (ready mixed), and H-EVA is dedicated to mortar and plaster, construction concrete and road binders.
Italy. Green concrete, an emergency!
If the situation was already worrying in recent years, the image of the Ispra 2020 land use report in Italy is alarming. Two square meters of concrete are produced every second. And this clearly means that two square meters of green or, in any case, of soil are irretrievably erased. In the largest cities, that is metropolis, the year 2019 recorded the loss of 24 square meters per hectare of green area. Overall, about 50% of national soil losses in the last year are concentrated in urban areas, 15% in central and semi-central areas, 32% in peripheral and less dense areas. The eight ball goes to Rome with a loss of 75 hectares in total (of which 57 ha in the green areas of the city). Milan devoured 11.5 hectares of land in one year (of which 11 are green areas). Turin is the only city that stands out with the least land loss, remaining the only positive reality in this bleak image.
As far as regions are concerned, Veneto has some of the largest losses: over 923 hectares. It is followed by Lombardy (633 hectares), Puglia (425), Emilia-Romagna (381) and Sicily (302).
ECO-Binder project in Italy, Romania, Spain, and the UK
The ambitious ECO-Binder project, financed by the EU, continues in five testing locations in Italy, Romania, Spain, and the UK. Specialists aimed to develop an environmentally friendly solution to drastically reduce the carbon footprint of concrete manufacturing. However, the objectives of the team went much further. Researchers took advantage of the opportunity of integrating more safety, comfort, and stability in a single package of products at a competitive price. Concrete is formed by mixing a binder, usually cement, with water. Belite-Y and Ye’elimite-Ferrite (BYF) cement binders are a family of environmentally friendly materials. The performance of the new class of cements is comparable to that of OPC. However, lower calcium content, lower combustion temperature and lower energy demand for grinding result in approximately 30% less CO2 emissions associated with concrete production.
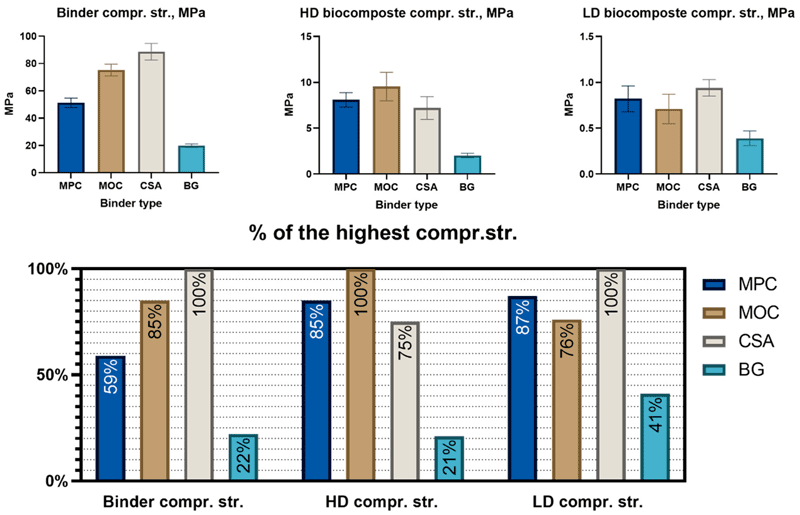
In 2018-2020 (the first two years of the four-year project), the team demonstrated the feasibility of prefabricated elements combining new BYF binders and the manufacture of advanced functional finishing materials.
Proven success
Four different concrete materials, manufactured with three BYF and OPC cements were used at small-scale models in Romania, Spain, and the UK and at a testing plant in Spain.
According to Arianna Amati, coordinator of the project, the target reached was large-scale production of BYF concrete. 11-meter-high monolithic panels were installed and tested in a real-world scenario on the demonstration site in Mantua, Italy. “165 m2 of facade of the structure were built with prefabricated BYF concrete components in order to demonstrate the complete replacement of the OPC-based product on a full scale,” explains Arianna Amati. The tests of these small- and large-scale models have confirmed the success of project objectives. Prefabricated panels with the new BYF products showed a 24% lower ‘gray energy’, as well as a 24% reduction in carbon footprint. Moreover, insulation properties were improved by 10%. Lower hygrometric shrinkage of BYF concrete (higher dimensional stability) without the use of additives has led to a reduction in air losses. All of these were delivered at a cost 15% lower than conventional OPC products.
Poland: Concrete, gypsum, plaster, and mortar obtained from ash
In turn, Poland is facing high costs for fulfilling the European agreement to reduce CO2 emissions by 40% by 2030 and for reaching carbon neutrality by 2050. The Polish Cement Association (SPC) has forecast a 2% year-on-year drop in cement sales to 18.5 million tons in 2021. In 2020, concrete imports made by Poland with Belarus increased by 80% (440,000 tons) and those in Ukraine climbed by 50% (around 32,000 tons). SPC has expressed its firm support for the European Carbon Border Adjustment Mechanism (CBAM) as a means of protecting industry against imports from both non-EU neighbouring countries and through polluting transport from concrete exporters abroad, such as in Turkey.
EKO-ZEC, a Polish subsidiary of Veolia, collects ash from burning coal and uses it in concrete production. Since the beginning of 2017, part of the surplus was exported to other European countries. EKO-ZEC produces up to 650,000 tons of ash per year, a figure that exceeds by far the local demand, especially in winter months, when there are fewer sites and demand for concrete is lower, and the surplus is obviously exported, especially to countries with fewer coal-fired power plants. Due to these new distribution channels, EKO-ZEC and Veolia contribute to circular economy in Europe!
Romania. ECOPact – the widest range of green concrete in the industry
Local cement market had a value of EUR 630 million in 2020, according to data from the National Institute of Statistics. Compared to EUR 570 million in 2019, it results in a 10% growth of this sector last year.
2021 brought, through Holcim, for the first time in the industry of building materials in Romania, ECOPact – the widest range of green concrete in the industry, with CO2 emissions reduced by over 30%, created to accelerate transition to sustainable construction. At the same time, the company develops a new business model – ECONCEPT, which is based on three complementary directions: ECO Solutions (green products and solutions, with low CO2 footprint); ECO Services (consulting and instruments for building sustainable projects) and ECO Score (evaluation and certification of climate performances of products in the portfolio). The new range of green concrete has a wide range of uses, from residential and non-residential civil constructions, industrial and hydrotechnical constructions, special industrial constructions and to special constructions for water transport and marine structures.
With the new business model, the company has set new targets in terms of sustainability, in accordance with the ‘Net Zero’ commitment that LafargeHolcim Group signed up to last year, at global level. The latter has the goal of reaching CO2 emission neutrality by 2050.
Switzerland. LC3, one of the technologies with the greatest potential to reduce CO2 emissions
A consortium led by the Federal Polytechnic School of Lausanne (EPFL) has received support from the Swiss Agency for Development and Cooperation (SDC) worth more than 4 million francs to accelerate the development and testing of a new type of concrete with low impact on the environment. Developed in partnership with the Institutes of Technology in India and various universities in Cuba and Brazil, this product based on a mixture clay and limestone could replace up to half of the traditionally used Portland concrete, reducing by up to 40% CO2 emissions caused by this material. Researchers, who have actively collaborated with industrial and government partners, hope to make LC3 the new benchmark for the largest companies in the field. Two industrial-scale pilot projects, carried out in India and Cuba, have already proven the efficiency of the product and ease with which it can be integrated into the current production chain. “If we truly want to make concrete more attractive in terms of durability, cost, availability and environmental impact, we must act before demand explodes in developing countries,” concludes Karen Scrivener, who heads EPFL’s Building Materials Laboratory.
LC3 – short history
In 2004, prof. Karen Scrivener from EPFL Switzerland and prof. Fernando Martirena from UCLV Cuba discussed for the first time about the use of calcined clays for pozzolans, and in 2005, the two professors launched together the first research project on this topic supported by the Swiss National Scientific Foundation (SNSF) and the Swiss Development Agency and Cooperation (SDC). In 2009, a second project supported by the SNSF and SDC on materials research began to focus on ternary blended cement with clay and limestone. During this project, from 2009 until 2012, the huge potential of calcined clay was fully recognized.
In 2013, EPFL started a global project: concrete from calcined clay. In addition to the laboratory in Cuba, it was decided to open a second laboratory in India, due to the significant potential to increase the volume of construction materials.
In 2014, the first three-year phase of the LC3 project had as main objective the technical verification of LC3 technology. It involved the development of an academic network for the research of LC3 cements. Consequently, it could be proven that LC3 achieves OPC – CEM I quality and is suitable for global launch.
From 2017 until 2020, the SDC financed another three-year phase with the same team of academic partners in Switzerland, Cuba, and India. Within this phase, the LC3-Project mainly worked on verifying the economic attractiveness of the material and increasing the awareness in industrial and policy circles. Several LC3-applications were built in different parts of the world that are exposed to different environmental conditions. During the phase academic, industrial and policy circles widely acknowledged LC3 as one of the technologies with the highest potential to lower CO2-emissions in the concrete sector. Also, the first permanent large-scale production of LC3 started within the second project phase in Colombia.
Since September 2020, the LC3-Project extends its technology globally. Several new LC3-productions are on the way. The project has received high attention by Bloomberg and TED-talks.
Houses of the future without cement?
Northern countries do what they do best: they are always one step ahead in terms of environmental protection.
As part of a pilot project supported by green funds from the Danish Ministry of Environment, architects from Een til Een have built the world’s first house from waste and scrap materials from the agricultural industry. Whilst houses made from natural materials are nothing new, as numerous examples can be found in the huts of tribes living in jungles and forests around the world, in this case they are made from materials that have undergone a process of transformation and recycling. Hay and rice straw, reed, hemp, flax, algae and other cellulosic fibres, materials that are normally considered waste and are usually used as fuel for energy production, are given a new life in this project and become raw materials for construction.
The CO2 captured by these materials is not re-emitted into the atmosphere as a result of their combustion. On the other hand, the recycling of locally available materials promotes the local economy. This ‘organic’ house, as the architects themselves have dubbed it, has been designed and produced using digital technologies. Moreover, it is a fully integrated building with natural ventilation and passive solar heating, not to mention that the recycled materials are breathable. The house also sits on screw piles, instead of the traditional concrete foundation, which means better insulation and ventilation, whilst at the same time having less impact on the land on which it stands. For the cladding, wood from local sustainable forests is used, with a special treatment, also biological, which makes it resistant, durable, and dimensionally stable.
World’s first house from waste and scrap materials from the agricultural industry. It is exhibited at the BIOTOPE ecological park in Middelfart, Denmark
The world’s first ‘organic’ house, which aims to tackle ecological problems and global climate change, is part of the general trend towards green architecture. It is exhibited at the BIOTOPE ecological park in Middelfart, Denmark.
The new generation of concrete – ‘green’ or not?
The building sector, a significant emitter of carbon dioxide, plans to make efforts in terms of sustainable development. For this, it relies a lot on ‘green’ concrete, which would have the benefit of not containing carbon. But is green concrete truly environmentally friendly?
The disadvantage of this essential binder is that it is not truly environmentally friendly due to the manufacturing process. Its manufacture is one of the most polluting on the planet, and manufacturers would like to find a solution to protect the planet. Of course, the idea is noble, but not as easy as it seems. And not by the ‘green concrete’ indication on the bags will this product be carbon-free.
The low-carbon method, according to the manufacturers, is to replace the treatment of limestone and clay with slag – waste resulting from the manufacture of steel. This is the shocking argument for proposing the so-called green concrete. Furnaces that mainly produce steel, another element that goes into the construction of buildings, are not models in terms of sustainability.
Slag allows the use of ‘blind’ points in environmental calculation standards
In France, the Elioth design office team, a subsidiary of the Egis group, intrigued by the promises made by manufacturers to reduce CO2 emissions, took over the life-cycle analysis calculations for next-generation concrete.
The use of materials capable of not emitting carbon into the atmosphere or even storing it is gradually becoming essential. It’s about meeting the commitments assumed in France at COP 21 and the Paris Agreements signed in 2015, which translates into the National Low Carbon Strategy (SNBC). Traders support the low-carbon qualities of almost all materials, and concrete is no exception, as manufacturers now offer qualified ‘low-carbon emission’ ranges.
“These calculations are caricatural because, under certain conditions, a concrete floor had a carbon footprint comparable to that of a wooden floor,” said Guillaume Meunier, deputy director responsible for the environment division at Elioth.
Reducing the carbon footprint of so-called low-carbon concrete involves replacing part of the cement clinker with blast-furnace slag. The whole carbon footprint reduction trick looks at the LCA of this slag, which has an almost ridiculous carbon footprint through calculation tricks. Slag is a ‘waste’ of the steel processing industry. Waste, improperly said, because it is now used to justify all low-carbon concrete. 95% of the slag is sold at a rate of 82% to cement producers, at a selling price ten times higher than the real value.
The fact that slag is a by-product allows it to use blind spots in environmental calculation standards in order not to consider its impact on the environment.
On the one hand, we have steel producers who consider slag to be a material that avoids the use of clinker and, therefore, logically (from their point of view) subtract from the balance the difference between the carbon footprint of clinker and that of concrete products. This is therefore a ‘negative’ value that can be deduced from the steel LCA.
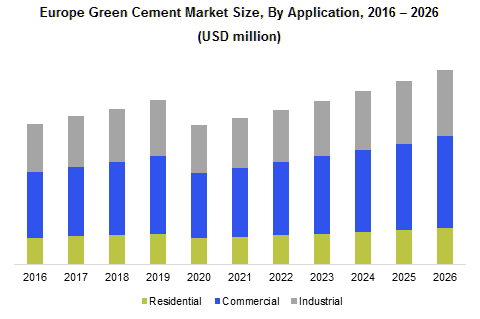
New cements blocked by the European Commission
In mid-2019, the European Commission called into question the legality of the mandate review procedure, which aims to introduce new types of cement. Any revision of the standard for current cements is blocked. From a technical point of view, the subject has become legal. But the problem is even deeper, as most of the recently revised harmonized standards are technically robust, but do not apply because they are not cited in the ‘Official Journal of the European Union’ due to lack of compliance. The technical document is expected to reach the CEN survey, and if countries vote positive, we can have a new normative document. At the same time, each concrete manufacturer develops its own strategy for greening its ranges.
Two ranges of ‘low carbon’ concrete: CEM II/C-M and CEM VI. The so-called ‘ternary’ are composed of clinker, limestone and cemented compounds. The compounds can be made of slag from furnaces, but also to be the ash from thermal power plants or pozzolans – volcanic rocks. Their clinker content varies from 50 to 65% for CEM II/C-M and from 35 to 50% for CEM VI. These cements are no longer in the research and development stage but have been widely validated. However, they have not yet been produced and sold due to a legal deadlock in the European Commission that prevents their approval. “In order to introduce them, we need to revise the harmonized European standard that allows them to be placed on the market. But legal issues between the European Commission and the European Committee for Standardization prevent work from being completed. Concrete companies intend to write a standard common to all member states, but to be applied at national level. We need to move forward to meet the challenges we are being asked to meet, which is to reduce our CO2 emissions. The launch on the market is expected, at best, this year,” says Xavier Guillot, head of standards coordination at LafargeHolcim.
The world’s first ‘organic’ house, which aims to tackle ecological problems and global climate change, is part of the general trend towards green architecture. It is exhibited at the BIOTOPE ecological park in Middelfart, Denmark.
The new generation of concrete – ‘green’ or not?
The building sector, a significant emitter of carbon dioxide, plans to make efforts in terms of sustainable development. For this, it relies a lot on ‘green’ concrete, which would have the benefit of not containing carbon. But is green concrete truly environmentally friendly?
The disadvantage of this essential binder is that it is not truly environmentally friendly due to the manufacturing process. Its manufacture is one of the most polluting on the planet, and manufacturers would like to find a solution to protect the planet. Of course, the idea is noble, but not as easy as it seems. And not by the ‘green concrete’ indication on the bags will this product be carbon-free.
The low-carbon method, according to the manufacturers, is to replace the treatment of limestone and clay with slag – waste resulting from the manufacture of steel. This is the shocking argument for proposing the so-called green concrete. Furnaces that mainly produce steel, another element that goes into the construction of buildings, are not models in terms of sustainability.
Slag allows the use of ‘blind’ points in environmental calculation standards
In France, the Elioth design office team, a subsidiary of the Egis group, intrigued by the promises made by manufacturers to reduce CO2 emissions, took over the life-cycle analysis calculations for next-generation concrete.
The use of materials capable of not emitting carbon into the atmosphere or even storing it is gradually becoming essential. It’s about meeting the commitments assumed in France at COP 21 and the Paris Agreements signed in 2015, which translates into the National Low Carbon Strategy (SNBC). Traders support the low-carbon qualities of almost all materials, and concrete is no exception, as manufacturers now offer qualified ‘low-carbon emission’ ranges.
“These calculations are caricatural because, under certain conditions, a concrete floor had a carbon footprint comparable to that of a wooden floor,” said Guillaume Meunier, deputy director responsible for the environment division at Elioth.
Reducing the carbon footprint of so-called low-carbon concrete involves replacing part of the cement clinker with blast-furnace slag. The whole carbon footprint reduction trick looks at the LCA of this slag, which has an almost ridiculous carbon footprint through calculation tricks. Slag is a ‘waste’ of the steel processing industry. Waste, improperly said, because it is now used to justify all low-carbon concrete. 95% of the slag is sold at a rate of 82% to cement producers, at a selling price ten times higher than the real value.
The fact that slag is a by-product allows it to use blind spots in environmental calculation standards in order not to consider its impact on the environment.
On the one hand, we have steel producers who consider slag to be a material that avoids the use of clinker and, therefore, logically (from their point of view) subtract from the balance the difference between the carbon footprint of clinker and that of concrete products. This is therefore a ‘negative’ value that can be deduced from the steel LCA.
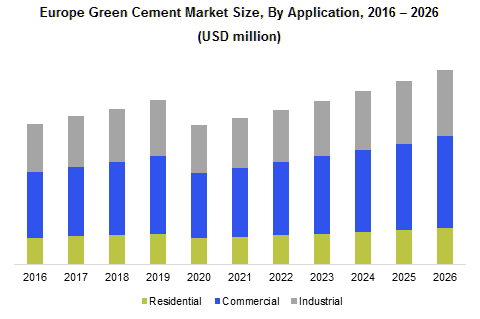
New cements blocked by the European Commission
In mid-2019, the European Commission called into question the legality of the mandate review procedure, which aims to introduce new types of cement. Any revision of the standard for current cements is blocked. From a technical point of view, the subject has become legal. But the problem is even deeper, as most of the recently revised harmonized standards are technically robust, but do not apply because they are not cited in the ‘Official Journal of the European Union’ due to lack of compliance. The technical document is expected to reach the CEN survey, and if countries vote positive, we can have a new normative document. At the same time, each concrete manufacturer develops its own strategy for greening its ranges.
Two ranges of ‘low carbon’ concrete: CEM II/C-M and CEM VI. The so-called ‘ternary’ are composed of clinker, limestone and cemented compounds. The compounds can be made of slag from furnaces, but also to be the ash from thermal power plants or pozzolans – volcanic rocks. Their clinker content varies from 50 to 65% for CEM II/C-M and from 35 to 50% for CEM VI. These cements are no longer in the research and development stage but have been widely validated. However, they have not yet been produced and sold due to a legal deadlock in the European Commission that prevents their approval. “In order to introduce them, we need to revise the harmonized European standard that allows them to be placed on the market. But legal issues between the European Commission and the European Committee for Standardization prevent work from being completed. Concrete companies intend to write a standard common to all member states, but to be applied at national level. We need to move forward to meet the challenges we are being asked to meet, which is to reduce our CO2 emissions. The launch on the market is expected, at best, this year,” says Xavier Guillot, head of standards coordination at LafargeHolcim.
No comments:
Post a Comment