MIT team produces practical guidelines for generating hydrogen using scrap aluminum.
Nancy W. Stauffer | MIT Energy Initiative
Publication Date:August 12, 2021
PRESS INQUIRIES
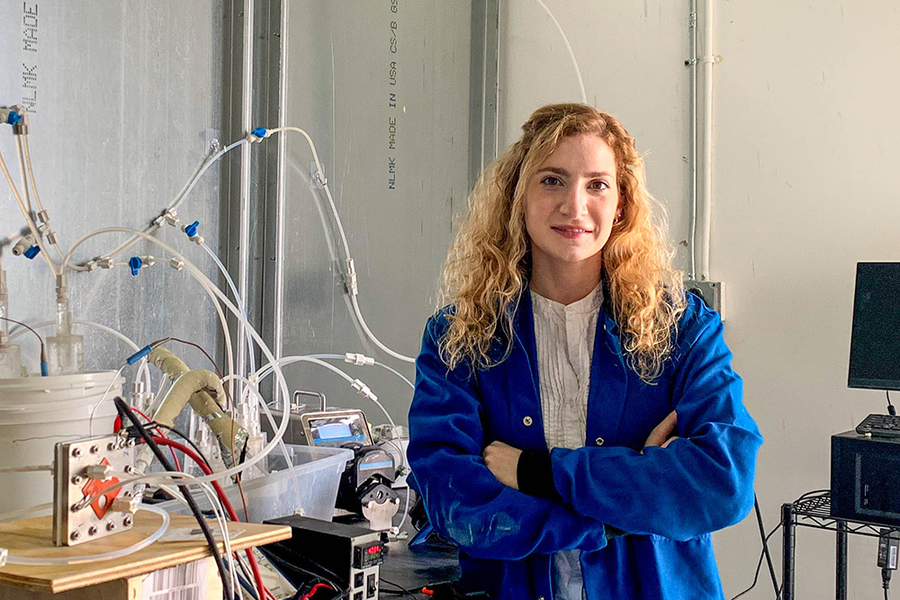
Caption:Laureen Meroueh PhD ’20 (pictured) and professors Douglas P. Hart and Thomas W. Eagar have shown how to use scrap aluminum plus water to generate the flow of hydrogen needed for a particular practical application.
Credits:Photo: Reza Mirshekari
As the world works to move away from fossil fuels, many researchers are investigating whether clean hydrogen fuel can play an expanded role in sectors from transportation and industry to buildings and power generation. It could be used in fuel cell vehicles, heat-producing boilers, electricity-generating gas turbines, systems for storing renewable energy, and more.
But while using hydrogen doesn’t generate carbon emissions, making it typically does. Today, almost all hydrogen is produced using fossil fuel-based processes that together generate more than 2 percent of all global greenhouse gas emissions. In addition, hydrogen is often produced in one location and consumed in another, which means its use also presents logistical challenges.
A promising reaction
Another option for producing hydrogen comes from a perhaps surprising source: reacting aluminum with water. Aluminum metal will readily react with water at room temperature to form aluminum hydroxide and hydrogen. That reaction doesn’t typically take place because a layer of aluminum oxide naturally coats the raw metal, preventing it from coming directly into contact with water.
Using the aluminum-water reaction to generate hydrogen doesn’t produce any greenhouse gas emissions, and it promises to solve the transportation problem for any location with available water. Simply move the aluminum and then react it with water on-site. “Fundamentally, the aluminum becomes a mechanism for storing hydrogen — and a very effective one,” says Douglas P. Hart, professor of mechanical engineering at MIT. “Using aluminum as our source, we can ‘store’ hydrogen at a density that’s 10 times greater than if we just store it as a compressed gas.”
Two problems have kept aluminum from being employed as a safe, economical source for hydrogen generation. The first problem is ensuring that the aluminum surface is clean and available to react with water. To that end, a practical system must include a means of first modifying the oxide layer and then keeping it from re-forming as the reaction proceeds.
The second problem is that pure aluminum is energy-intensive to mine and produce, so any practical approach needs to use scrap aluminum from various sources. But scrap aluminum is not an easy starting material. It typically occurs in an alloyed form, meaning that it contains other elements that are added to change the properties or characteristics of the aluminum for different uses. For example, adding magnesium increases strength and corrosion-resistance, adding silicon lowers the melting point, and adding a little of both makes an alloy that’s moderately strong and corrosion-resistant.
Despite considerable research on aluminum as a source of hydrogen, two key questions remain: What’s the best way to prevent the adherence of an oxide layer on the aluminum surface, and how do alloying elements in a piece of scrap aluminum affect the total amount of hydrogen generated and the rate at which it is generated?
“If we’re going to use scrap aluminum for hydrogen generation in a practical application, we need to be able to better predict what hydrogen generation characteristics we’re going to observe from the aluminum-water reaction,” says Laureen Meroueh PhD ’20, who earned her doctorate in mechanical engineering.
Since the fundamental steps in the reaction aren’t well understood, it’s been hard to predict the rate and volume at which hydrogen forms from scrap aluminum, which can contain varying types and concentrations of alloying elements. So Hart, Meroueh, and Thomas W. Eagar, a professor of materials engineering and engineering management in the MIT Department of Materials Science and Engineering, decided to examine — in a systematic fashion — the impacts of those alloying elements on the aluminum-water reaction and on a promising technique for preventing the formation of the interfering oxide layer.
To prepare, they had experts at Novelis Inc. fabricate samples of pure aluminum and of specific aluminum alloys made of commercially pure aluminum combined with either 0.6 percent silicon (by weight), 1 percent magnesium, or both — compositions that are typical of scrap aluminum from a variety of sources. Using those samples, the MIT researchers performed a series of tests to explore different aspects of the aluminum-water reaction.
Pre-treating the aluminum
The first step was to demonstrate an effective means of penetrating the oxide layer that forms on aluminum in the air. Solid aluminum is made up of tiny grains that are packed together with occasional boundaries where they don’t line up perfectly. To maximize hydrogen production, researchers would need to prevent the formation of the oxide layer on all those interior grain surfaces.
Research groups have already tried various ways of keeping the aluminum grains “activated” for reaction with water. Some have crushed scrap samples into particles so tiny that the oxide layer doesn’t adhere. But aluminum powders are dangerous, as they can react with humidity and explode. Another approach calls for grinding up scrap samples and adding liquid metals to prevent oxide deposition. But grinding is a costly and energy-intensive process.
To Hart, Meroueh, and Eagar, the most promising approach — first introduced by Jonathan Slocum ScD ’18 while he was working in Hart’s research group — involved pre-treating the solid aluminum by painting liquid metals on top and allowing them to permeate through the grain boundaries.
To determine the effectiveness of that approach, the researchers needed to confirm that the liquid metals would reach the internal grain surfaces, with and without alloying elements present. And they had to establish how long it would take for the liquid metal to coat all of the grains in pure aluminum and its alloys.
They started by combining two metals — gallium and indium — in specific proportions to create a “eutectic” mixture; that is, a mixture that would remain in liquid form at room temperature. They coated their samples with the eutectic and allowed it to penetrate for time periods ranging from 48 to 96 hours. They then exposed the samples to water and monitored the hydrogen yield (the amount formed) and flow rate for 250 minutes. After 48 hours, they also took high-magnification scanning electron microscope (SEM) images so they could observe the boundaries between adjacent aluminum grains.
Based on the hydrogen yield measurements and the SEM images, the MIT team concluded that the gallium-indium eutectic does naturally permeate and reach the interior grain surfaces. However, the rate and extent of penetration vary with the alloy. The permeation rate was the same in silicon-doped aluminum samples as in pure aluminum samples but slower in magnesium-doped samples.
Perhaps most interesting were the results from samples doped with both silicon and magnesium — an aluminum alloy often found in recycling streams. Silicon and magnesium chemically bond to form magnesium silicide, which occurs as solid deposits on the internal grain surfaces. Meroueh hypothesized that when both silicon and magnesium are present in scrap aluminum, those deposits can act as barriers that impede the flow of the gallium-indium eutectic.
The experiments and images confirmed her hypothesis: The solid deposits did act as barriers, and images of samples pre-treated for 48 hours showed that permeation wasn’t complete. Clearly, a lengthy pre-treatment period would be critical for maximizing the hydrogen yield from scraps of aluminum containing both silicon and magnesium.
Meroueh cites several benefits to the process they used. “You don’t have to apply any energy for the gallium-indium eutectic to work its magic on aluminum and get rid of that oxide layer,” she says. “Once you’ve activated your aluminum, you can drop it in water, and it’ll generate hydrogen — no energy input required.” Even better, the eutectic doesn’t chemically react with the aluminum. “It just physically moves around in between the grains,” she says. “At the end of the process, I could recover all of the gallium and indium I put in and use it again” — a valuable feature as gallium and (especially) indium are costly and in relatively short supply.
Impacts of alloying elements on hydrogen generation
The researchers next investigated how the presence of alloying elements affects hydrogen generation. They tested samples that had been treated with the eutectic for 96 hours; by then, the hydrogen yield and flow rates had leveled off in all the samples.
The presence of 0.6 percent silicon increased the hydrogen yield for a given weight of aluminum by 20 percent compared to pure aluminum — even though the silicon-containing sample had less aluminum than the pure aluminum sample. In contrast, the presence of 1 percent magnesium produced far less hydrogen, while adding both silicon and magnesium pushed the yield up, but not to the level of pure aluminum.
The presence of silicon also greatly accelerated the reaction rate, producing a far higher peak in the flow rate but cutting short the duration of hydrogen output. The presence of magnesium produced a lower flow rate but allowed the hydrogen output to remain fairly steady over time. And once again, aluminum with both alloying elements produced a flow rate between that of magnesium-doped and pure aluminum.
Those results provide practical guidance on how to adjust the hydrogen output to match the operating needs of a hydrogen-consuming device. If the starting material is commercially pure aluminum, adding small amounts of carefully selected alloying elements can tailor the hydrogen yield and flow rate. If the starting material is scrap aluminum, careful choice of the source can be key. For high, brief bursts of hydrogen, pieces of silicon-containing aluminum from an auto junkyard could work well. For lower but longer flows, magnesium-containing scraps from the frame of a demolished building might be better. For results somewhere in between, aluminum containing both silicon and magnesium should work well; such material is abundantly available from scrapped cars and motorcycles, yachts, bicycle frames, and even smartphone cases.
It should also be possible to combine scraps of different aluminum alloys to tune the outcome, notes Meroueh. “If I have a sample of activated aluminum that contains just silicon and another sample that contains just magnesium, I can put them both into a container of water and let them react,” she says. “So I get the fast ramp-up in hydrogen production from the silicon and then the magnesium takes over and has that steady output.”
Another opportunity for tuning: Reducing grain size
Another practical way to affect hydrogen production could be to reduce the size of the aluminum grains — a change that should increase the total surface area available for reactions to occur.
To investigate that approach, the researchers requested specially customized samples from their supplier. Using standard industrial procedures, the Novelis experts first fed each sample through two rollers, squeezing it from the top and bottom so that the internal grains were flattened. They then heated each sample until the long, flat grains had reorganized and shrunk to a targeted size.
In a series of carefully designed experiments, the MIT team found that reducing the grain size increased the efficiency and decreased the duration of the reaction to varying degrees in the different samples. Again, the presence of particular alloying elements had a major effect on the outcome.
Needed: A revised theory that explains observations
Throughout their experiments, the researchers encountered some unexpected results. For example, standard corrosion theory predicts that pure aluminum will generate more hydrogen than silicon-doped aluminum will — the opposite of what they observed in their experiments.
To shed light on the underlying chemical reactions, Hart, Meroueh, and Eagar investigated hydrogen “flux,” that is, the volume of hydrogen generated over time on each square centimeter of aluminum surface, including the interior grains. They examined three grain sizes for each of their four compositions and collected thousands of data points measuring hydrogen flux.
Their results show that reducing grain size has significant effects. It increases the peak hydrogen flux from silicon-doped aluminum as much as 100 times and from the other three compositions by 10 times. With both pure aluminum and silicon-containing aluminum, reducing grain size also decreases the delay before the peak flux and increases the rate of decline afterward. With magnesium-containing aluminum, reducing the grain size brings about an increase in peak hydrogen flux and results in a slightly faster decline in the rate of hydrogen output. With both silicon and magnesium present, the hydrogen flux over time resembles that of magnesium-containing aluminum when the grain size is not manipulated. When the grain size is reduced, the hydrogen output characteristics begin to resemble behavior observed in silicon-containing aluminum. That outcome was unexpected because when silicon and magnesium are both present, they react to form magnesium silicide, resulting in a new type of aluminum alloy with its own properties.
The researchers stress the benefits of developing a better fundamental understanding of the underlying chemical reactions involved. In addition to guiding the design of practical systems, it might help them find a replacement for the expensive indium in their pre-treatment mixture. Other work has shown that gallium will naturally permeate through the grain boundaries of aluminum. “At this point, we know that the indium in our eutectic is important, but we don’t really understand what it does, so we don’t know how to replace it,” says Hart.
But already Hart, Meroueh, and Eagar have demonstrated two practical ways of tuning the hydrogen reaction rate: by adding certain elements to the aluminum and by manipulating the size of the interior aluminum grains. In combination, those approaches can deliver significant results. “If you go from magnesium-containing aluminum with the largest grain size to silicon-containing aluminum with the smallest grain size, you get a hydrogen reaction rate that differs by two orders of magnitude,” says Meroueh. “That’s huge if you’re trying to design a real system that would use this reaction.”
This research was supported through the MIT Energy Initiative by ExxonMobil-MIT Energy Fellowships awarded to Laureen Meroueh PhD ’20 from 2018 to 2020.
This article appears in the Spring 2021 issue of Energy Futures, the magazine of the MIT Energy Initiative.
Date:August 11, 2021
Source:
Cell Press
Addressing climate change requires not only a clean electrical grid, but also a clean fuel to reduce emissions from industrial heat, long-haul heavy transportation, and long-duration energy storage. Hydrogen and its derivatives could be that fuel, argues a recent commentary , but a clean U.S. H2 economy will require a comprehensive strategy and a 10-year plan. The commentary suggests that careful consideration of future H2 infrastructure, including production, transport, storage, use, and economic viability, will be critical to the success of efforts aimed at making clean H2 viable on a societal scale.
"We applaud the U.S. Secretary of Energy, Jennifer Granholm, for launching the ambitious Hydrogen Earthshot program with a technology-agnostic stretch goal of greenhouse gas-free H2 production at $1/kg before the end of this decade," write Arun Majumdar, a Jay Precourt Professor and Co-Director of the Precourt Institute for Energy at Stanford University and lead author of the commentary, and colleagues. "Similar R&D programs with techno-economic stretch goals are needed for H2 storage, use, and transport as well. The Hydrogen Earthshot is necessary to create a hydrogen economy, but it is not sufficient."
About 70 million metric tons of H2 are produced around the world each year, with the U.S. contributing about one-seventh of the global output. Much of this H2 is used to produce fertilizer and petrochemicals, and nearly all of it is considered "gray H2," which costs only about $1 per kilogram to produce but comes with roughly 10 kilograms of CO2 baggage per kilogram H2.
"An H2 economy already exists, but it involves lots of greenhouse gas emissions," says Majumdar. "Almost all of it is based on H2 from methane. A clean H2 economy does not exist today."
Researchers have plenty of colorful visions as to what a clean H2 economy might look like. "Blue H2," for example, involves capturing CO2 and reducing emissions, resulting in H2 with less greenhouse gas output. However, it currently costs about 50% more than gray H2, not including the cost of developing the pipelines and sequestration systems needed to transport and store unwanted CO2.
"To make blue H2 a viable option, research and development is needed to reduce CO2 capture costs and further improve capture completeness," write Majumdar and colleagues.
Another form of clean H2 -- dubbed "green H2" -- has also captured scientists' attention. Green H2 involves the use of electricity and electrolyzers to split water, without any greenhouse gas byproducts. However, it costs $4 to $6 per kilogram, a price that Majumdar and colleagues suggest could be reduced to under $2 per kilogram with a reduction in carbon-free electricity and electrolyzer costs.
"Turquoise H2," which is achieved through methane pyrolysis, when methane is cracked to generate greenhouse gas-free H2, is also creating a buzz in the research world. The solid carbon co-product generated in this process could be sold to help offset costs, although Majumdar and colleagues point out that the quantity of solid carbon produced at the necessary scale would exceed current demand, resulting in a need for R&D efforts to develop new markets for its use.
Whether blue, green, or turquoise, greenhouse gas-free (and, in actuality, colorless) H2 or its derivatives could be used in transportation, the chemical reduction of captured CO2, long-duration energy storage in a highly renewable energy-dependent grid, and chemical reductants for steel and metallurgy, and as high-temperature industrial heat for glass and cement production. But for these applications to become a reality, H2 production will have to hit certain cost benchmarks -- $1 per kilogram for the production of ammonia and petrochemicals or for use as a transportation fuel or fuel cells.
The researchers also emphasize that the U.S. will need to consider how H2 pipelines will be developed and deployed in order to transport it, as well as how to store H2 cost-effectively at a large scale. "Developing and siting new pipeline infrastructure is generally expensive and involves challenges of social acceptance," write Majumdar and colleagues. "Hence, it is important to explore alternative approaches for a hydrogen economy that does not require a new H2 pipeline infrastructure. Instead, it is worth using existing infrastructure to transport the feedstock for H2 -- electric grid for transporting electricity for water splitting; natural gas pipelines to transport methane for pyrolysis."
"While there has been some systematic study of geological storage, the United States Geological Survey should be charged with undertaking a national survey to identify the many locations where underground storage of hydrogen is possible while also considering the infrastructure costs needed to use these caverns," the researchers add.
Story Source:
Materials provided by Cell Press. Note: Content may be edited for style and length.
Journal Reference:
Arun Majumdar, John M. Deutch, Ravi S. Prasher, Thomas P. Griffin. A framework for a hydrogen economy. Joule, 2021; DOI: 10.1016/j.joule.2021.07.007
Cite This Page:
MLA
APA
Chicago
Cell Press. "A clean US hydrogen economy is within reach, but needs a game plan, energy researchers say." ScienceDaily. ScienceDaily, 11 August 2021. <www.sciencedaily.com/releases/2021/08/210811113145.htm>.
Novel technique seamlessly converts ammonia to 'green' hydrogen
- August 11, 2021
- Ulsan National Institute of Science and Technology(UNIST)
- A recent study has announced a breakthrough in technology that efficiently converts liquid ammonia into hydrogen.
A research team, led by Professor Guntae Kim in the School of Energy and Chemical Engineering at UNIST has announced a breakthrough in technology that efficiently converts liquid ammonia into hydrogen. Their findings have also attracted significant attention from academic research communities owing to its new analysis protocol, capable of finding optimal process environments.
In this study, the research team succeeded in producing green hydrogen (H2) in large quantities with a purity of nearly 100 percent by decomposing liquid ammonia (NH3) into electricity. Besides, according to the research team, such method consumed three times less power than hydrogen made using electrolysis of water.
Ammonia has emerged as an attractive potential hydrogen carrier due to its extremely high energy density, and ease of storage and handling. Moreover, the electrolysis of ammonia to produce nitrogen and hydrogen only requires an external voltage of 0.06 V theoretically, which is much lower than the energy needed for water electrolysis (1.23 V), noted the research team.
In this study, the research team propose a well-established procedure using in operando gas chromatography that enables us to reliably compare and evaluate the new catalyst for ammonia oxidation. According to the research team, with the protocol, they could distinguish in detail the competitive oxidation reaction between the ammonia oxidation and oxygen evolutionreactions with real-time monitoring.
With the use of flower-like electrodeposited Pt catalyst, researchers have efficiently produced hydrogen with less power consumption of 734 LH2 kW h?1, which is significantly lower than that of the water-splitting process (242 LH2 kW h?1). "The use of this rigorous protocol should help to evaluate the practical performances for ammonia oxidation, thus enabling the field to focus on viable pathways towards the practical electrochemical oxidation of ammonia to hydrogen," noted the research team.
This study has been co-authored by Minzae Lee, Myung-gi Seo, Hyung-Ki Min, and Youngheon Choi from Lotte Chemical R&D Center, respectively. Their work has also been featured on the inside back cover of Journal of Material Chemistry A, which was made available online in March 2021 ahead of final publication in May 2021. This research has been carried out with the support of Lotte Chemical, Ministry of Science and ICT (MSIT), and the National Research Foundation of Korea (NRF).
Story Source:
Materials provided by Ulsan National Institute of Science and Technology(UNIST). Original written by JooHyeon Heo. Note: Content may be edited for style and length.
Journal Reference:
- Yejin Yang, Jeongwon Kim, Hyoi Jo, Arim Seong, Minzae Lee, Hyung-Ki Min, Myung-gi Seo, Youngheon Choi, Guntae Kim. A rigorous electrochemical ammonia electrolysis protocol with in operando quantitative analysis. Journal of Materials Chemistry A, 2021; 9 (19): 11571 DOI: 10.1039/D1TA00363A
Cite This Page:
Green hydrogen: Why do certain catalysts improve in operation?
Crystalline cobalt arsenide is a catalyst that generates oxygen during electrolytic water splitting in the production of hydrogen.
- August 9, 2021
- Helmholtz-Zentrum Berlin für Materialien und Energie
- As a rule, most catalyst materials deteriorate during repeated catalytic cycles – they age. But there are also compounds that increase their performance over the course of catalysis. One example is the mineral erythrite, a mineral compound comprising cobalt and arsenic oxides. Erythrite lends itself to accelerating oxygen generation at the anode during electrolytic splitting of water into hydrogen and oxygen.
As a rule, most catalyst materials deteriorate during repeated catalytic cycles -- they age. But there are also compounds that increase their performance over the course of catalysis. One example is the mineral erythrite, a mineral compound comprising cobalt and arsenic oxides with a molecular formula of (Co3(AsO4)2?8H2O). The mineral stands out because of its purple colour. Erythrite lends itself to accelerating oxygen generation at the anode during electrolytic splitting of water into hydrogen and oxygen.
Samples from Costa Rica
The young investigator group headed by Dr. Marcel Risch at the HZB together with groups from Costa Rica has now analysed these catalysing mineral materials in detail at BESSY II and made an interesting discovery.
Using samples produced by colleagues in Costa Rica consisting of tiny erythrite crystals in powder form, Javier Villalobos, a doctoral student in Risch's group at the HZB, coated the electrodes with this powder. He then examined them before, during, and after hundreds of electrolysis cycles in four different pH-neutral electrolytes, including ordinary soda water (carbonated water).
Loss of original structure
Over time, the surface of each catalytically active layer exhibited clear changes in all the electrolytes. The original crystalline structure was lost, as shown by images from the scanning electron microscope, and more cobalt ions changed their oxidation number due to the applied voltage, which was determined electrochemically. Increased oxygen yield was also demonstrated over time in soda water (carbonated water), though only in that electrolyte. The catalyst clearly improved.
Observations at BESSY II
With analyses at BESSY II, the researchers are now able to explain why this was the case: using X-ray absorption spectroscopy, they scanned the atomic and chemical environment around the cobalt ions. The more active samples lost their original erythrite crystal structure and were transformed into a less ordered structure that can be described as platelets just two atoms thick. The larger these platelets became, the more active the sample was. The data over the course of the catalysis cycles showed that the oxidation number of the cobalt in these platelets increased the most in soda water, from 2.0 to 2.8. Since oxides with an oxidation number of 3 are known to be very good catalysts, this explains the improvement relative to the catalysts that formed in the other electrolytes.
Oxygen yield doubled
In soda water, the oxygen yield per cobalt ion decreased by a factor of 28 over 800 cycles, but at the same time 56 times as many cobalt atoms changed their oxidation number electrochemically. Macroscopically, the electrical current generation and thus the oxygen yield of the electrode doubled.
From needles to Swiss cheese
In a nutshell, Risch explains: "Over time, the material becomes like Swiss cheese with many holes and a larger surface area where many more reactions can take place. Even if the individual catalytically active centres become somewhat weaker over time, the larger surface area means that many more potential catalytically active centres come into contact with the electrolyte and increase the yield."
Risch suggests that such mechanisms can also be found in many other classes of materials consisting of non-toxic compounds, which can be developed into suitable catalysts.
Story Source:
Materials provided by Helmholtz-Zentrum Berlin für Materialien und Energie. Note: Content may be edited for style and length.
Journal Reference:
- Javier Villalobos, Diego González‐Flores, Roberto Urcuyo, Mavis L. Montero, Götz Schuck, Paul Beyer, Marcel Risch. Requirements for Beneficial Electrochemical Restructuring: A Model Study on a Cobalt Oxide in Selected Electrolytes. Advanced Energy Materials, 2021; 2101737 DOI: 10.1002/aenm.202101737
Cite This Page:
No comments:
Post a Comment