Concrete needs to lose its colossal carbon footprint
Concrete will be crucial for much-needed climate-resilient construction. But the cement industry must set out its plan for decarbonization.
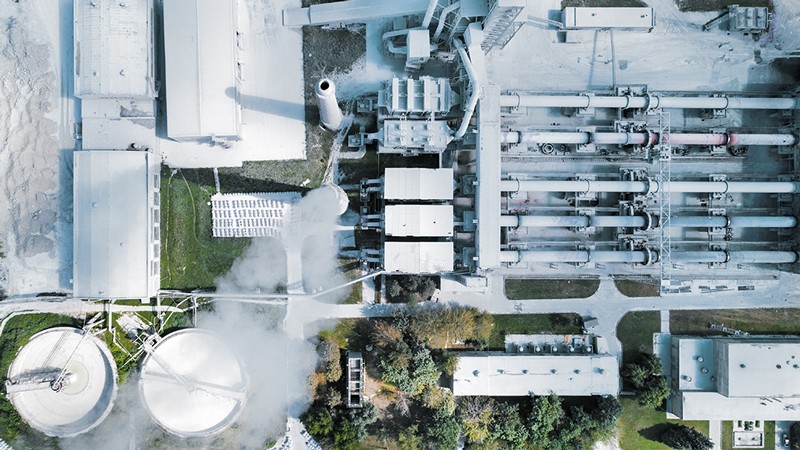
Cement manufacturing (such as that at this plant in Russia) accounts for 8% of the world’s carbon dioxide emissions.
Concrete options
Technological changes can be accelerated through regulation and legislation. A huge proportion of concrete is used in public building projects. In North America alone, public agencies buy as much as one-third of concrete manufactured annually. That means they have leverage in the low-carbon transition: they could work with researchers and manufacturers to reshape the concrete industry.
In New York and New Jersey, a bill is making its way through state legislatures that, if passed, will mandate that state agencies and departments prioritize cement that has a lower carbon footprint.
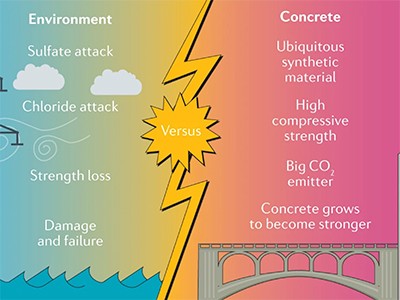
An ancient battle between environment and concrete
Other states are introducing legislation that requires construction proposals to declare the environmental impact of cement mixes. Some regions, such as Honolulu, Hawaii, have added a requirement that city construction projects must consider using concrete that stores CO2.
In Europe, the European Union’s Waste Framework Directive requires 70% of construction waste to be reused. Another idea, known as materials passports, could also help. When buildings are demolished, the waste concrete is smashed up and discarded, or sold for low-grade use such as backfilling in road construction. But a passport would ensure that concrete is recorded ‘at birth’ and then tracked throughout its life cycle — making it accessible for more kinds of reuse.
Finally, the cement industry needs to publish better emissions data so that progress can be tracked. In a study published last month, researchers from Columbia University in New York City report that some of China’s cement-making companies have an ambition for emissions to peak in 2023 (see go.nature.com/39z1sdd). But only one of the ten companies surveyed is reporting emissions data. China is the world’s largest cement producer (55% of global capacity), and cement accounts for 15% of the country’s carbon emissions. Without data, it will be impossible to know whether national targets are being met.
Next month, a cement-industry campaign called Concrete Action for Climate will announce its road map for carbon neutrality by 2050. This is overdue, but the road map must also explain interim steps, how companies intend to achieve neutrality and how progress will be measured.
Parts of the ancient world were made with concrete, and the material was used to build much of the modern world, too. Researchers and governments must work with the cement industry to slash its carbon footprint, driving the climate-resilient construction the world now sorely needs.
Nature 597, 593-594 (2021)
doi: https://doi.org/10.1038/d41586-021-02612-5
References
1.
Jackson, M. D. et al. Proc. Natl Acad. Sci. USA 111, 18484–18489 (2014).
PubMed Article Google Scholar
2.
Monteiro, P., Miller, S. & Horvath, A. Nature Mater. 16, 698–699 (2017).
PubMed Article Google Scholar
3.
Ellis, L. D., Badel, A. F., Chiang, M. L., Park, R. J.-Y. & Chiang, Y.-M. Proc. Natl Acad. Sci. USA 117, 12584–12591 (2020).
PubMed Article Google Scholar
4.
Fennell, P. S., Davis, S. J. & Mohammed, A. Joule 5, 1305–1311 (2021).
Article Google Scholar
Download references
Concrete will be crucial for much-needed climate-resilient construction. But the cement industry must set out its plan for decarbonization.
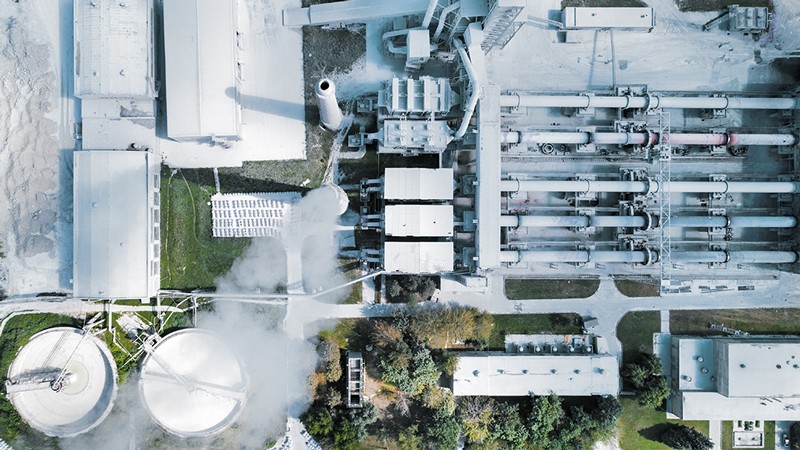
Cement manufacturing (such as that at this plant in Russia) accounts for 8% of the world’s carbon dioxide emissions.
Credit: Getty
Wet concrete has been poured into buildings, roads, bridges and more for centuries. Structures using concrete have survived wars and natural disasters, outlasting many of the civilizations that built them1. Alongside its strength and resilience, concrete is also a staple of building because it is relatively cheap and simple to make. Worldwide, 30 billion tonnes of concrete is used each year. On a per capita basis, that is 3 times as much as 40 years ago — and the demand for concrete is growing more steeply than that for steel or wood2.
Versatile and long-lasting, concrete buildings and structures are in many ways ideal for climate-resilient construction. But concrete has a colossal carbon footprint — at least 8% of global emissions caused by humans come from the cement industry alone3. We must decarbonize its production.
Concrete is made by adding sand and gravel to cement, whisking the mixture with water and pouring it into moulds before it dries. Making the cement is the most carbon-intensive part: it involves using fossil fuels to heat a mixture of limestone and clay to more than 1,400 °C in a kiln. Also, when limestone (calcium carbonate) is heated with clays, roughly 600 kilograms of carbon dioxide is released for every tonne of cement produced (see go.nature.com/3exhg82).
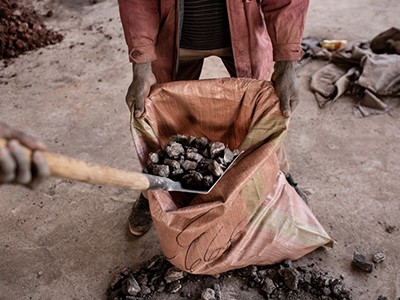
Lithium-ion batteries need to be greener and more ethical
There are alternatives to cement, but they’re in the early stages of development, and cement itself remains highly profitable — two disincentives for companies to change.
Alternatives include the leftover compounds from iron and steel production, known as slag, and heaps of unused fly ash, a residual material from coal plants. Researchers are also experimenting with reducing the temperatures needed in the cement-making process — thereby decreasing the energy used.
In carbon-accounting terms, such replacements and procedural changes will reduce cement’s environmental impact, and that of concrete, too. But they still involve carbon emissions. Coal is being phased out, so fly ash isn’t a long-term solution. And alternatives have yet to be certified for use in building; for this to happen, long-term studies on their performance are needed.
Cement will be around for the foreseeable future, so cement production itself needs to be decarbonized, which could happen in a number of ways. For example, low-carbon fuels — such as hydrogen or biomass — could be substituted for fossil fuels in heating the limestone and clay. And scientists are examining whether electricity — instead of combustion — could be used for the heating.
Carbon capture could be part of the cement industry’s transition process4. In Sweden, for example, a company announced in July that it wants to capture 1.8 million tonnes of CO2 from a cement plant and bury it in the North Sea. Another possibility is to pump the captured CO2 into concrete itself, locking it up forever — which might also improve the properties of the resulting material. The injected CO2 reacts with calcium ions in the cement, producing more calcium carbonate, and potentially making the concrete able to withstand larger loads.
Wet concrete has been poured into buildings, roads, bridges and more for centuries. Structures using concrete have survived wars and natural disasters, outlasting many of the civilizations that built them1. Alongside its strength and resilience, concrete is also a staple of building because it is relatively cheap and simple to make. Worldwide, 30 billion tonnes of concrete is used each year. On a per capita basis, that is 3 times as much as 40 years ago — and the demand for concrete is growing more steeply than that for steel or wood2.
Versatile and long-lasting, concrete buildings and structures are in many ways ideal for climate-resilient construction. But concrete has a colossal carbon footprint — at least 8% of global emissions caused by humans come from the cement industry alone3. We must decarbonize its production.
Concrete is made by adding sand and gravel to cement, whisking the mixture with water and pouring it into moulds before it dries. Making the cement is the most carbon-intensive part: it involves using fossil fuels to heat a mixture of limestone and clay to more than 1,400 °C in a kiln. Also, when limestone (calcium carbonate) is heated with clays, roughly 600 kilograms of carbon dioxide is released for every tonne of cement produced (see go.nature.com/3exhg82).
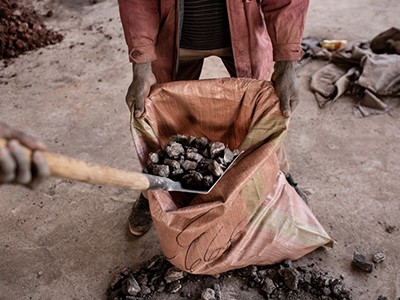
Lithium-ion batteries need to be greener and more ethical
There are alternatives to cement, but they’re in the early stages of development, and cement itself remains highly profitable — two disincentives for companies to change.
Alternatives include the leftover compounds from iron and steel production, known as slag, and heaps of unused fly ash, a residual material from coal plants. Researchers are also experimenting with reducing the temperatures needed in the cement-making process — thereby decreasing the energy used.
In carbon-accounting terms, such replacements and procedural changes will reduce cement’s environmental impact, and that of concrete, too. But they still involve carbon emissions. Coal is being phased out, so fly ash isn’t a long-term solution. And alternatives have yet to be certified for use in building; for this to happen, long-term studies on their performance are needed.
Cement will be around for the foreseeable future, so cement production itself needs to be decarbonized, which could happen in a number of ways. For example, low-carbon fuels — such as hydrogen or biomass — could be substituted for fossil fuels in heating the limestone and clay. And scientists are examining whether electricity — instead of combustion — could be used for the heating.
Carbon capture could be part of the cement industry’s transition process4. In Sweden, for example, a company announced in July that it wants to capture 1.8 million tonnes of CO2 from a cement plant and bury it in the North Sea. Another possibility is to pump the captured CO2 into concrete itself, locking it up forever — which might also improve the properties of the resulting material. The injected CO2 reacts with calcium ions in the cement, producing more calcium carbonate, and potentially making the concrete able to withstand larger loads.
Concrete options
Technological changes can be accelerated through regulation and legislation. A huge proportion of concrete is used in public building projects. In North America alone, public agencies buy as much as one-third of concrete manufactured annually. That means they have leverage in the low-carbon transition: they could work with researchers and manufacturers to reshape the concrete industry.
In New York and New Jersey, a bill is making its way through state legislatures that, if passed, will mandate that state agencies and departments prioritize cement that has a lower carbon footprint.
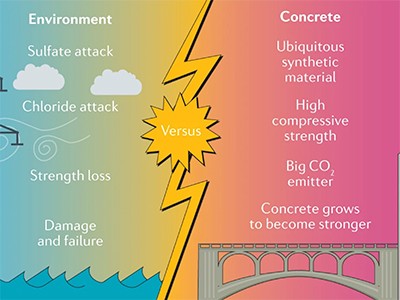
An ancient battle between environment and concrete
Other states are introducing legislation that requires construction proposals to declare the environmental impact of cement mixes. Some regions, such as Honolulu, Hawaii, have added a requirement that city construction projects must consider using concrete that stores CO2.
In Europe, the European Union’s Waste Framework Directive requires 70% of construction waste to be reused. Another idea, known as materials passports, could also help. When buildings are demolished, the waste concrete is smashed up and discarded, or sold for low-grade use such as backfilling in road construction. But a passport would ensure that concrete is recorded ‘at birth’ and then tracked throughout its life cycle — making it accessible for more kinds of reuse.
Finally, the cement industry needs to publish better emissions data so that progress can be tracked. In a study published last month, researchers from Columbia University in New York City report that some of China’s cement-making companies have an ambition for emissions to peak in 2023 (see go.nature.com/39z1sdd). But only one of the ten companies surveyed is reporting emissions data. China is the world’s largest cement producer (55% of global capacity), and cement accounts for 15% of the country’s carbon emissions. Without data, it will be impossible to know whether national targets are being met.
Next month, a cement-industry campaign called Concrete Action for Climate will announce its road map for carbon neutrality by 2050. This is overdue, but the road map must also explain interim steps, how companies intend to achieve neutrality and how progress will be measured.
Parts of the ancient world were made with concrete, and the material was used to build much of the modern world, too. Researchers and governments must work with the cement industry to slash its carbon footprint, driving the climate-resilient construction the world now sorely needs.
Nature 597, 593-594 (2021)
doi: https://doi.org/10.1038/d41586-021-02612-5
References
1.
Jackson, M. D. et al. Proc. Natl Acad. Sci. USA 111, 18484–18489 (2014).
PubMed Article Google Scholar
2.
Monteiro, P., Miller, S. & Horvath, A. Nature Mater. 16, 698–699 (2017).
PubMed Article Google Scholar
3.
Ellis, L. D., Badel, A. F., Chiang, M. L., Park, R. J.-Y. & Chiang, Y.-M. Proc. Natl Acad. Sci. USA 117, 12584–12591 (2020).
PubMed Article Google Scholar
4.
Fennell, P. S., Davis, S. J. & Mohammed, A. Joule 5, 1305–1311 (2021).
Article Google Scholar
Download references
No comments:
Post a Comment