Bloomberg News
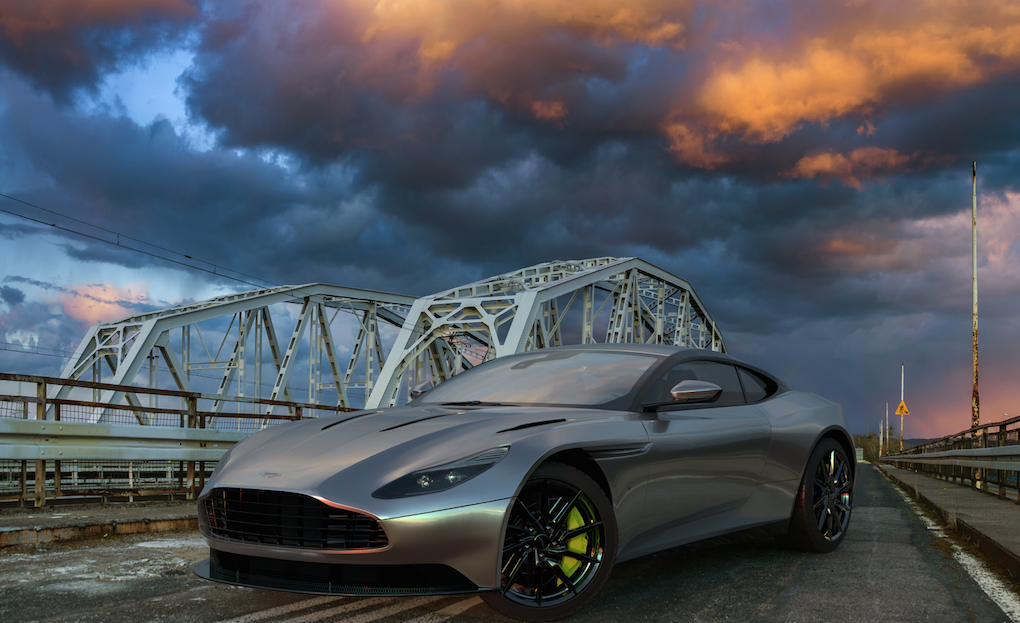
Stock image.
Picture James Bond strapped to a doomsday device while a countdown clock ticks toward zero. That’s the situation the Earth faces when it comes to climate change, according to U.K. Prime Minister Boris Johnson.

“The tragedy is that this is not a movie and the doomsday device is real,” Johnson said Monday in Glasgow at the 26th COP climate conference, the annual meeting that’s supposed to set out plans to rein in global warming.
The transport sector is a big part of the problem. It accounts for about 10% of global greenhouse gas emissions and will face special scrutiny at COP26 because of how much it pollutes. The European Union in July proposed that member states stop selling combustion cars no later than 2035 as the region tries to cut transport emissions that have climbed by a third since 1990.
The auto industry may well be phasing out the internal combustion engine and EV sales are taking off, but that doesn’t mean the path to zero-emission driving will be easy. There are a few key roadblocks holding up progress that are likely to come up at the conference over the coming days:
Dirty production
Building an EV emits significantly more carbon dioxide than producing combustion models, researchers have found. That’s mainly because EVs are made with a resource-intensive battery and greater amounts of aluminum. Battery metals including lithium, cobalt and nickel are mined in Australia, South America and Africa and then shipped around the world for refining, resulting in massive carbon emissions. Carmakers are acutely aware of the issue’s potential to cause PR problems and have started exploring alternative sourcing methods, but the projects are still in their infancy.
Clean electricity
While EVs are dirtier than regular cars coming out of the factory, they’re supposed to make up for that big time during their driving years because they have no tailpipe emissions. Another factor in this equation, though, is the juice that powers the battery. The problem is that the world still produces electricity mostly from fossil-fired sources, with coal and natural gas accounting for almost 60% of the global power mix in 2020, according to International Energy Agency data. In China, where EV sales are surging, coal — the dirtiest fossil fuel — remains the dominant electricity source by far.
Charger anxiety
Numerous people I know are open to buying an EV but are put off by what they perceive as sub-par charging convenience. A Sky News colleague driving an electric SUV from London to the COP venue in Glasgow struggled with some patchy charging infrastructure along the way. Carmakers and politicians have identified a lack of charging spots as a key hurdle to wider EV adoption. In China, where EV adoption is outpacing infrastructure upgrades, the issues may well fuel buyer’s remorse after drivers there had to queue for hours to recharge their vehicle during last month’s Golden Week holiday. Europe has billions of euros earmarked for more charging spots, but especially in larger cities — where people tend to live in apartment buildings instead of free-standing homes — coming up with convenient charging options will remain a challenge.
Transitioning trucks
While passenger cars are fairly well on their way toward electrification, trucks are still far off from meeting the EU’s net-zero climate target for 2050, according to a new report from Transport & Environment. The Brussels-based NGO says the EU’s CO2 emission standards for trucks, introduced in 2019, should be tightened because they lack the ambition to spur real change. Almost 98% of the roughly 170,000 trucks and vans registered in Europe between July 2019 and June 2020 had a diesel engine, according to the report.
“The European Commission is addressing car emissions with plans to phase out petrol and diesel cars, yet it is still miles away from bringing trucking in line with its Green Deal ambition,” said Lucien Mathieu, acting director for freight at T&E. “With trade rebounding, now is the time to raise the ambition for truck emissions targets.”
(By Stefan Nicola)
Toyota, Yamaha, Mazda, Subaru to develop alternate fuels for combustion engines

As countries around the world tighten environmental regulations in order to cut down carbon emissions, various automakers including Toyota are working on ramping up the production of EVs. Toyota is also under pressure as the Japan government has said that it aims to be a carbon neutral nation by 2050 and is also promoting the use of hydrogen fuel.
Toyota currently has plans to develop 15 EV models by 2025 and is investing $13.5 billion over the next decade to expand battery production capacity. Meanwhile, it is also working on developing vehicles powered by hydrogen.
Toyota president Akio Toyoda spent the weekend swerving around the racetrack in western Japan in a Toyota Corolla. The version he drove was equipped with in-house hydrogen engine, which propels the vehicle by burning the fuel much like traditional engines use gasoline.
The company also showcased other vehicles running on carbon-neutral propellants in a three-hour road race, along with Mazda. "The enemy is carbon, not internal combustion engines," Toyoda said.
(with inputs from Reuters)
Reuters | November 10, 2021
Stock image.
Global automakers are planning to spend more than half a trillion dollars on electric vehicles and batteries through 2030, according to a Reuters analysis, amping up investments aimed at weaning car buyers away from fossil fuels and meeting increasingly tough decarbonization targets.

Less than three years ago, a similar analysis by Reuters found car companies planned to spend $300 billion on EVs and related technologies. But looming zero-carbon mandates in cities such as London and Paris and countries from Norway to China have lent additional urgency to the industry’s EV-related investment commitments.
The most recent analysis shows carmakers planning to spend an estimated $515 billion over the next five to 10 years to develop and build new battery-powered vehicles and shift away from combustion engines.
FILE PHOTO: A Toyota logo is displayed at the 89th Geneva International Motor Show in Geneva, Switzerland. (REUTERS)
Updated: 14 Nov 2021, 10:10 AM ISTHT Auto Desk
Toyota currently has plans to develop 15 EV models by 2025 and is investing $13.5 billion over the next decade to expand battery production capacity.
Meanwhile, it is also working on developing vehicles powered by hydrogen.
Toyota Motor Corp has announced that will partner with four other Japanese vehicle makers to explore the feasibility of developing alternative green motor fuels for internal combustion engine such as hydrogen fuel and synthetic fuels derived from biomass.
The companies that Toyota is partnering with include Mazda, Subaru, Yamaha Motor and Kawasaki Heavy Industries.
All the five companies made the announcement of partnership at a race track in Okayama, western Japan.
Toyota is of the belief that though transforming internal combustion engines to green fuels such as hydrogen is technologically difficult, but achieving this goal would allow the companies to support ages-old existing supply chain systems. These include hundreds of thousands of workers who may otherwise have to leave their jobs as the industry switches to producing electric vehicles (EV).
Toyota currently has plans to develop 15 EV models by 2025 and is investing $13.5 billion over the next decade to expand battery production capacity.
Meanwhile, it is also working on developing vehicles powered by hydrogen.
Toyota Motor Corp has announced that will partner with four other Japanese vehicle makers to explore the feasibility of developing alternative green motor fuels for internal combustion engine such as hydrogen fuel and synthetic fuels derived from biomass.
The companies that Toyota is partnering with include Mazda, Subaru, Yamaha Motor and Kawasaki Heavy Industries.
All the five companies made the announcement of partnership at a race track in Okayama, western Japan.
Toyota is of the belief that though transforming internal combustion engines to green fuels such as hydrogen is technologically difficult, but achieving this goal would allow the companies to support ages-old existing supply chain systems. These include hundreds of thousands of workers who may otherwise have to leave their jobs as the industry switches to producing electric vehicles (EV).
As countries around the world tighten environmental regulations in order to cut down carbon emissions, various automakers including Toyota are working on ramping up the production of EVs. Toyota is also under pressure as the Japan government has said that it aims to be a carbon neutral nation by 2050 and is also promoting the use of hydrogen fuel.
Toyota currently has plans to develop 15 EV models by 2025 and is investing $13.5 billion over the next decade to expand battery production capacity. Meanwhile, it is also working on developing vehicles powered by hydrogen.
Toyota president Akio Toyoda spent the weekend swerving around the racetrack in western Japan in a Toyota Corolla. The version he drove was equipped with in-house hydrogen engine, which propels the vehicle by burning the fuel much like traditional engines use gasoline.
The company also showcased other vehicles running on carbon-neutral propellants in a three-hour road race, along with Mazda. "The enemy is carbon, not internal combustion engines," Toyoda said.
(with inputs from Reuters)
Global carmakers now target $515 billion for EVs, batteries
Reuters | November 10, 2021

Stock image.
Global automakers are planning to spend more than half a trillion dollars on electric vehicles and batteries through 2030, according to a Reuters analysis, amping up investments aimed at weaning car buyers away from fossil fuels and meeting increasingly tough decarbonization targets.

Less than three years ago, a similar analysis by Reuters found car companies planned to spend $300 billion on EVs and related technologies. But looming zero-carbon mandates in cities such as London and Paris and countries from Norway to China have lent additional urgency to the industry’s EV-related investment commitments.
The most recent analysis shows carmakers planning to spend an estimated $515 billion over the next five to 10 years to develop and build new battery-powered vehicles and shift away from combustion engines.

Source: Reuters
But industry executives and forecasters remain concerned that consumer demand for EVs could fall well short of aggressive targets without substantial additional incentives and even greater spending on charging infrastructure and grid capacity.
Brian Maxim, head of global powertrain forecasting at AutoForecast Solutions, likens the growing investment commitments in vehicle electrification to the Cold War: “Once a few manufacturers announced EV programs, everyone else had to announce their own or be viewed as being left behind.”
However, he added, “this leaves a lot of vehicle manufacturers planning significant volumes for a vehicle category that has unknown consumer acceptance, and will have minimal to no profit” for years.
Reuters compiled the investment data from company statements, investor presentations and regulatory filings.
Other surveys have come up with different spending projections. In June, consulting firm AlixPartners said auto industry investments in electric vehicles would reach $330 billion by 2025. In 2020, all global automakers combined spent nearly $225 billion on capital expenditures and research and development, according to AlixPartners.
Tesla Inc, the world’s largest EV manufacturer, appears to be the one company that is selling virtually every vehicle it can build and is readying new multibillion-dollar “gigafactories” near Berlin and Austin that will significantly boost its annual production capacity. In early November, the company was valued at $1.2 trillion, more than twice the combined value of Volkswagen AG, Toyota Motor Corp, Ford Motor Co and General Motors Co.
Meanwhile, political and regulatory pressure is building on the world’s carmakers to begin phasing out production of fossil-fueled vehicles, including gasoline-electric hybrids, over the next 10-15 years, while ramping up output of full electric models.
A number of countries, from Singapore to Sweden, have said they will ban sales of new combustion engine vehicles by 2030. U.S. President Joseph Biden has said he wants 40% to 50% of sales to be electric vehicles by 2030.
Germany’s VW Group, which is still recovering financially from the 2016 Dieselgate emissions cheating scandal, continues to lead the rest of the industry, with more than $110 billion in EV and battery investment commitments through 2030. Those commitments, which represent more than 20% of the industry total, underpin VW’s aggressive rollout plans for millions of EVs in Europe, China and North America over the next decade.
VW’s investments, like those of many of its rivals, are aimed at improving the range and performance of batteries and lowering the cost of EVs, as well as expanding battery and EV production across the globe, according to public data released by the companies.
VW and fellow German automakers Daimler AG and BMW AG are planning to spend a combined $185 billion through 2030, while U.S. automakers GM and Ford expect to spend nearly $60 billion through 2025.
Chinese automakers, led by VW and GM local partner SAIC Motor, have announced well over $100 billion in investment targets over the next decade. Japanese automakers lag far behind, with Honda Motor, Toyota Motor and Nissan Motor so far publicly committing less than $40 billion combined.
These investments do not include the tens of billions of dollars being invested in additional production capacity by the world’s largest battery companies, many in cooperation with their automaker partners.
(By Paul Lienert and Tina Bellon; Editing by Dan Grebler)
But industry executives and forecasters remain concerned that consumer demand for EVs could fall well short of aggressive targets without substantial additional incentives and even greater spending on charging infrastructure and grid capacity.
Brian Maxim, head of global powertrain forecasting at AutoForecast Solutions, likens the growing investment commitments in vehicle electrification to the Cold War: “Once a few manufacturers announced EV programs, everyone else had to announce their own or be viewed as being left behind.”
However, he added, “this leaves a lot of vehicle manufacturers planning significant volumes for a vehicle category that has unknown consumer acceptance, and will have minimal to no profit” for years.
Reuters compiled the investment data from company statements, investor presentations and regulatory filings.
Other surveys have come up with different spending projections. In June, consulting firm AlixPartners said auto industry investments in electric vehicles would reach $330 billion by 2025. In 2020, all global automakers combined spent nearly $225 billion on capital expenditures and research and development, according to AlixPartners.
Tesla Inc, the world’s largest EV manufacturer, appears to be the one company that is selling virtually every vehicle it can build and is readying new multibillion-dollar “gigafactories” near Berlin and Austin that will significantly boost its annual production capacity. In early November, the company was valued at $1.2 trillion, more than twice the combined value of Volkswagen AG, Toyota Motor Corp, Ford Motor Co and General Motors Co.
Meanwhile, political and regulatory pressure is building on the world’s carmakers to begin phasing out production of fossil-fueled vehicles, including gasoline-electric hybrids, over the next 10-15 years, while ramping up output of full electric models.
A number of countries, from Singapore to Sweden, have said they will ban sales of new combustion engine vehicles by 2030. U.S. President Joseph Biden has said he wants 40% to 50% of sales to be electric vehicles by 2030.
Germany’s VW Group, which is still recovering financially from the 2016 Dieselgate emissions cheating scandal, continues to lead the rest of the industry, with more than $110 billion in EV and battery investment commitments through 2030. Those commitments, which represent more than 20% of the industry total, underpin VW’s aggressive rollout plans for millions of EVs in Europe, China and North America over the next decade.
VW’s investments, like those of many of its rivals, are aimed at improving the range and performance of batteries and lowering the cost of EVs, as well as expanding battery and EV production across the globe, according to public data released by the companies.
VW and fellow German automakers Daimler AG and BMW AG are planning to spend a combined $185 billion through 2030, while U.S. automakers GM and Ford expect to spend nearly $60 billion through 2025.
Chinese automakers, led by VW and GM local partner SAIC Motor, have announced well over $100 billion in investment targets over the next decade. Japanese automakers lag far behind, with Honda Motor, Toyota Motor and Nissan Motor so far publicly committing less than $40 billion combined.
These investments do not include the tens of billions of dollars being invested in additional production capacity by the world’s largest battery companies, many in cooperation with their automaker partners.
(By Paul Lienert and Tina Bellon; Editing by Dan Grebler)
The race to produce higher performing batteries
Bloomberg News | November 9, 2021

Credit: Solid Power
Last week battery startup SES announced it had developed the world’s largest lithium metal cell. The cell itself is still a prototype, but the company expects to be producing them commercially for use in EVs by 2025. Off the back of this announcement, I want to talk about batteries using lithium metal anodes, and the differences between SES and its peers QuantumScape and Solid Power.

Lithium metal anodes are sought after in the battery industry, because they promise to create lightweight cells enabling EVs with longer driving ranges. Not only are companies trying to improve performance, they also are trying to make batteries safer and with a lower price tag. But they are taking different approaches to achieve this, the benefits and drawbacks of which can be understandably difficult to pick apart.
There are three key components in a lithium battery: two electrodes — the anode and the cathode — which are separated by an electrolyte. The batteries in your cell phone or EV today use a graphite for the anode and a liquid electrolyte. These are the components that most startups are working to improve, as they haven’t really changed in 30 years. Cathode development is less of a focus, as these materials have experienced steady but gradual improvements over the last decade.
Taking a step back, SES’s announcement is big news because it’s the first demonstration of a battery that could be used in an EV using a lithium metal anode with a liquid electrolyte. Using a liquid electrolyte with a lithium metal is exciting because it could almost be a ‘drop-in’ process that utilizes existing manufacturing facilities. This could lead to quick scale up and a high market penetration, while also preserving the billions of dollars of investment in current manufacturing plants.
In the past it hasn’t been possible to use lithium metal anodes with liquid electrolytes because it leads to a low-cycle life – the number of times the battery can be charged and discharged – and can cause failures leading to battery fires. SES’s secret sauce is in getting these two critical components to work together. It has achieved this by adding so much salt to its electrolyte that the properties of the liquids change, from flammable to a substance that won’t catch fire. By using a liquid SES creates good contact between all of the layers in the battery – this is essential to having a battery that can perform lots of cycles.

By sticking to a liquid-based electrolyte, SES’ approach differs from its peers Solid Power and QuantumScape. In contrast, Solid Power and QuantumScape have been targeting the use of lithium metal anodes in combination with a solid electrolytes, in place of liquids, to create solid-state batteries. Solid electrolytes have been the main focus of companies developing cells that use lithium metal anodes as it is easier to control the reactions between the two components, and removes the liquid electrolyte as a possible accelerant in the event of a fire.
Solid Power uses an electrolyte material called lithium sulfide, which promises to be relatively easy to integrate with existing manufacturing processes. As its cells only use solid components it is important to make sure all of the layers have good contact to ensure high performance over the lifetime of the system. Before it commercializes batteries with lithium metal anodes, Solid Power is also aiming to develop a cell with a silicon anode. But we’ll leave silicon anodes for a future column.
QuantumScape on the other hand will use a ceramic material for its cells. These will require the company to develop new manufacturing processes and equipment. However, its technology has the advantage of not using lithium metal, which is difficult to handle, during the manufacturing process. Instead, QuantumScape forms its lithium metal anode in-situ in the manufactured cell. It also adds a little gel electrolyte to help maintain contact between the cathode material and the solid electrolyte.
The eventual performance of each company’s cells promises to be fairly similar, all should be safer and with a higher energy density, but the routes to getting there are markedly different. Each company has its own unique set of challenges when it comes to scaling the production of the technology, but nothing that appears insurmountable. From an industry perspective, the more routes we have to achieving high performing cells the better, as it creates more resiliency and makes me confident safer high performance batteries are just around the corner.
(By James Frith)
Bloomberg News | November 9, 2021

Credit: Solid Power
Last week battery startup SES announced it had developed the world’s largest lithium metal cell. The cell itself is still a prototype, but the company expects to be producing them commercially for use in EVs by 2025. Off the back of this announcement, I want to talk about batteries using lithium metal anodes, and the differences between SES and its peers QuantumScape and Solid Power.

Lithium metal anodes are sought after in the battery industry, because they promise to create lightweight cells enabling EVs with longer driving ranges. Not only are companies trying to improve performance, they also are trying to make batteries safer and with a lower price tag. But they are taking different approaches to achieve this, the benefits and drawbacks of which can be understandably difficult to pick apart.
There are three key components in a lithium battery: two electrodes — the anode and the cathode — which are separated by an electrolyte. The batteries in your cell phone or EV today use a graphite for the anode and a liquid electrolyte. These are the components that most startups are working to improve, as they haven’t really changed in 30 years. Cathode development is less of a focus, as these materials have experienced steady but gradual improvements over the last decade.
Taking a step back, SES’s announcement is big news because it’s the first demonstration of a battery that could be used in an EV using a lithium metal anode with a liquid electrolyte. Using a liquid electrolyte with a lithium metal is exciting because it could almost be a ‘drop-in’ process that utilizes existing manufacturing facilities. This could lead to quick scale up and a high market penetration, while also preserving the billions of dollars of investment in current manufacturing plants.
In the past it hasn’t been possible to use lithium metal anodes with liquid electrolytes because it leads to a low-cycle life – the number of times the battery can be charged and discharged – and can cause failures leading to battery fires. SES’s secret sauce is in getting these two critical components to work together. It has achieved this by adding so much salt to its electrolyte that the properties of the liquids change, from flammable to a substance that won’t catch fire. By using a liquid SES creates good contact between all of the layers in the battery – this is essential to having a battery that can perform lots of cycles.

By sticking to a liquid-based electrolyte, SES’ approach differs from its peers Solid Power and QuantumScape. In contrast, Solid Power and QuantumScape have been targeting the use of lithium metal anodes in combination with a solid electrolytes, in place of liquids, to create solid-state batteries. Solid electrolytes have been the main focus of companies developing cells that use lithium metal anodes as it is easier to control the reactions between the two components, and removes the liquid electrolyte as a possible accelerant in the event of a fire.
Solid Power uses an electrolyte material called lithium sulfide, which promises to be relatively easy to integrate with existing manufacturing processes. As its cells only use solid components it is important to make sure all of the layers have good contact to ensure high performance over the lifetime of the system. Before it commercializes batteries with lithium metal anodes, Solid Power is also aiming to develop a cell with a silicon anode. But we’ll leave silicon anodes for a future column.
QuantumScape on the other hand will use a ceramic material for its cells. These will require the company to develop new manufacturing processes and equipment. However, its technology has the advantage of not using lithium metal, which is difficult to handle, during the manufacturing process. Instead, QuantumScape forms its lithium metal anode in-situ in the manufactured cell. It also adds a little gel electrolyte to help maintain contact between the cathode material and the solid electrolyte.
The eventual performance of each company’s cells promises to be fairly similar, all should be safer and with a higher energy density, but the routes to getting there are markedly different. Each company has its own unique set of challenges when it comes to scaling the production of the technology, but nothing that appears insurmountable. From an industry perspective, the more routes we have to achieving high performing cells the better, as it creates more resiliency and makes me confident safer high performance batteries are just around the corner.
(By James Frith)
No comments:
Post a Comment