Scientists improve technique for conversion of CO2 emissions into fuel feedstock
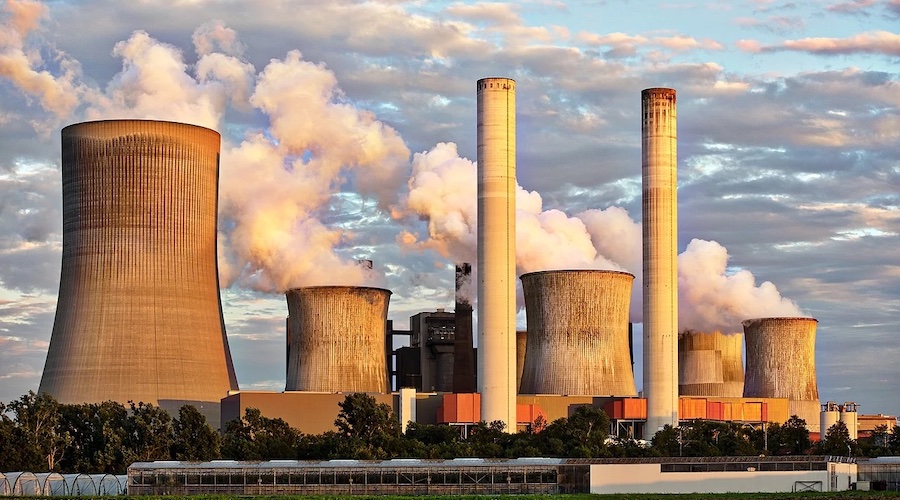
Power plant. (Reference image by Benita5, Pixabay).
In a new paper in the journal Nature Energy, researchers at Lawrence Berkeley National Laboratory report that they have improved the selectivity of a process known as electrochemical reduction, which allows the conversion of CO2 emissions into a fuel feedstock.

According to the scientists, the improvement was achieved by developing a new approach to modify the surface of the copper catalysts used to assist the reaction.
“Although we know copper is the best catalyst for this reaction, it doesn’t give high selectivity to the desired products,” Alexis Bell, one of the study’s co-authors, said in a media statement. “Our group has found that you can do various tricks with the local environment of the catalyst to provide that selectivity.”
Bell pointed out that previous studies had established the precise conditions that gave the best electrical and chemical environment for creating commercially interesting carbon-rich products. However, those conditions are contrary to those that naturally occur in a typical fuel cell, which uses a water-based conductive material.
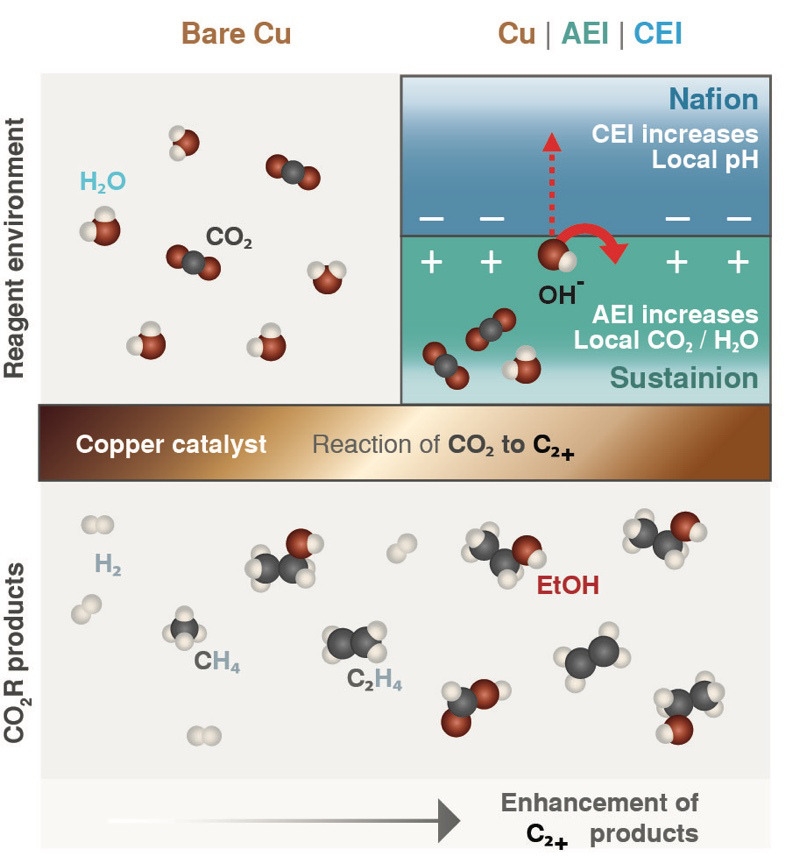
To pinpoint a design that could be used in the aqueous environment of fuel cells, Bell and his team turned to thin layers of ionomers, polymers that allow certain charged molecules (ions) to pass through while excluding others. As a result of their highly selective chemistry, they are uniquely suited to have a strong influence on the microenvironment.
Following a proposal by Chanyeon Kim, lead author of the paper, the researchers decided to apply a thin layer of two common ionomers, Nafion and Sustainion, as well as a bilayer of both ionomers on the surface of the copper catalyst supported by a polymer material, thus forming membranes that they could insert near one end of a hand-sized electrochemical cell.
While feeding CO2 into the cell and applying a voltage, they measured the total current flowing through the cell. Then they measured the gasses and liquids that were collected in adjoining reservoirs during the reaction. For the two-layer case, they found that carbon-rich products accounted for 80% of the energy consumed by the reaction—up from 60% in the uncoated scenario.
“This sandwich coating gives the best of both worlds: high product selectivity and high activity,” Bell said. The bilayered surface favoured not only carbon-rich products but also generated a strong electrical current, indicating increased activity.
The researchers concluded that the improved reaction was a consequence of the high CO2 concentration that built up in the coating layer immediately on top of the copper. Additionally, negatively-charged molecules that piled up in the region between the two ionomers created a low local acidity. That combination countered the concentration trade-off that tends to occur in the absence of the ionomer films.
To increase the reaction efficiency even further, the researchers turned to a technique that had been demonstrated before, without ionomer films, as another way to increase CO2 and pH: pulsing the voltage. By using a pulsed voltage with the bilayer ionomer coating, they achieved a 250% increase in carbon-rich products compared to uncoated copper and a static voltage.
These findings led them to realize that while some scientists have focused their work on developing new catalysts, catalyst discovery does not consider the operating conditions. Controlling the environment at the catalyst’s surface is a new and different approach.
“Rather than coming up with a brand new catalyst, we’ve taken what we know about the kinetics of a reaction and used that knowledge to guide our thinking about how to change the environment at the catalyst site,” said co-author Adam Weber.
New Electrocatalyst Produces Liquid Fuels From Carbon Dioxide
Electrocatalyst converts CO2 into multicarbon products.
A new electrocatalyst called a-CuTi@Cu converts carbon dioxide (CO2 ) into liquid fuels. As reported by a team of Chinese researchers in the journal Angewandte Chemie, active copper centered on an amorphous copper/titanium alloy produces ethanol, acetone, and n-butanol with high efficiency.
Most of our global energy demands are still being met by burning fossil fuels, which contributes to the greenhouse effect through the release of CO2. To reduce global warming, we must look for opportunities to use CO2 as a raw material for basic chemicals. Through electrocatalytic conversion of CO2 using renewable energy, a climate-neutral, artificial carbon cycle could be established. Excess energy produced by photovoltaics and wind energy could be stored through the electrocatalytic production of fuels from CO2. These could then be burned as needed. Conversion into liquid fuels would be advantageous because they have high energy density and are safe to store and transport. However, the electrocatalytic formation of products with two or more carbon atoms (C2+) is very challenging.
A team from Foshan University (Foshan, Guangdong), the University of Science and Technology of China (Hefei, Anhui), and Xi’an Shiyou University (Xi’an, Shaanxi), led by Fei Hu, Tingting Kong, Jun Jiang, and Yujie Xiong has now developed a novel electrocatalyst that efficiently converts CO2 to liquid fuels with multiple carbon atoms (C2–4). The primary products are ethanol, acetone, and n-butanol.
To make the electrocatalyst, thin ribbons of a copper/titanium alloy are etched with hydrofluoric acid to remove the titanium from the surface. This results in a material named a-CuTi@Cu, with a porous copper surface on an amorphous CuTi alloy. It has catalytically active copper centers with remarkably high activity, selectivity, and stability for the reduction of CO2 to C2+ products (total faradaic efficiency of about 49 % at 0.8 V vs. reversible hydrogen electrode for C2–4, and it is stable for at least three months). In contrast, pure copper foil produces C1 products but hardly any C2+ products.
The reaction involves a multistep electron-transfer process via various intermediates. In the new electrocatalyst, the inactive titanium atoms below the surface actually play an important role; they increase the electron density of the Cu atoms on the surface. This stabilizes the adsorption of *CO, the key intermediate in the formation of multicarbon products, allows for high coverage of the surface with *CO, and lowers the energy barrier for di- and trimerization of the *CO as new carbon–carbon bonds are formed.
Reference: “Ultrastable Cu Catalyst for CO2 Electroreduction to Multicarbon Liquid Fuels by Tuning C–C Coupling with CuTi Subsurface” by Prof. Fei Hu, Dr. Li Yang, Yawen Jiang, Dr. Chongxiong Duan, Dr. Xiaonong Wang, Longjiao Zeng, Xuefeng Lv, Delong Duan, Qi Liu, Prof. Tingting Kong, Prof. Jun Jiang, Ran Long and Prof. Yujie Xiong, 1 October 2021, Angewandte Chemie.
DOI: 10.1002/anie.202110303
Dr. Yujie Xiong is the Chair Professor of Chemistry at the University of Science and Technology of China. His main specialty is the artificial carbon cycle.
No comments:
Post a Comment