ABS Approves 3D-Printed Parts After Six Month Trial on U.S. Tanker
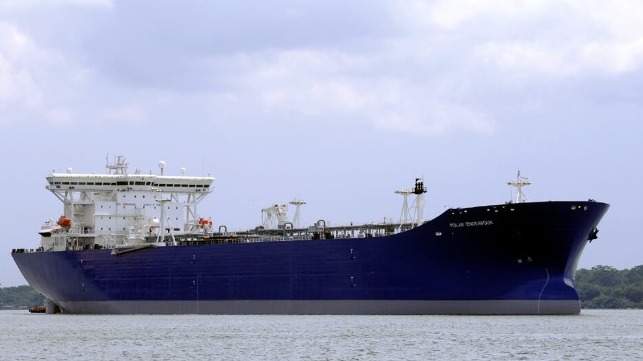
A series of 3D-printed mechanical parts used aboard an in-service oil tanker have been validated in good working condition at the end of a six-month trial. According to ABS, which participated in the project along with ConocoPhillips Polar Tankers, Sembcorp Marine Ltd, and 3D Metalforge, the project marks a milestone for the technology that could revolutionize how parts are made and supplied to ships in need of repairs.
The test project began in February 2021 with the fabrication and lab-testing of mechanical parts for use aboard the U.S.-flagged crude oil tanker Polar Endeavor. Built in 2001, the 141,740 dwt tanker was outfitted with a gear set and gear shaft for boiler fuel supply pump, flexible coupling used on a marine sanitation devices pump, and an ejector nozzle for a fresh water generator, all produced using additive manufacturing (AM) commonly known as 3D-printing.
After six months in operation, all the parts were retrieved and inspected by the vessel’s crew, followed by a remote survey by ABS that confirmed their good condition. ABS has now approved these spare parts after successful onboard testing on the tanker.
“We are delighted with the performance of the parts and the successful completion of the project,” said Patrick Ryan, Senior Vice President, Global Engineering and Technology for ABS. “It’s an important step forward for a technology that certainly has a significant role to play in the future of the marine industry. ABS is committed to ensuring these types of parts are introduced without compromising safety.”
According to ABS, the success of the trial and subsequent approval means 3D-printing can be used for products and components. The technology can permit parts to be fabricated locally or potentially on board ships and offshore assets. The result could be shrinking the supply chain and lead times for specialized and complex parts, introducing new efficiencies driven by design innovation, reduced manufacturing time, and improvements in parts availability.
“The superior performance of these parts in service is a testament to the rigorous engineering, manufacturing, and post-production testing put in place by the team involved with this venture,” said Robert Noyer, Engineering Superintendent for ConocoPhillips Polar Tankers which supplied the ship for the test. "We look forward to future opportunities to support our vessels with this technology.”
Traditional parts used in shipbuilding and repair are manufactured with casting or forging techniques. For this project, the consortium utilized AM to fabricate three types of parts that meet or may even exceed conventionally manufactured products in terms of quality. 3D-printing fabricated the parts by adding material layer by layer.
The industry has been experimenting with applications for the technology over the past few years. In February 2021, the largest metal propeller produced by 3D-printing was certified by BV while other applications have included manufacturing equipment to be tested in port operations.
No comments:
Post a Comment