By Ron Lyseng
WESTERN PRODUCER
Published: December 30, 2021
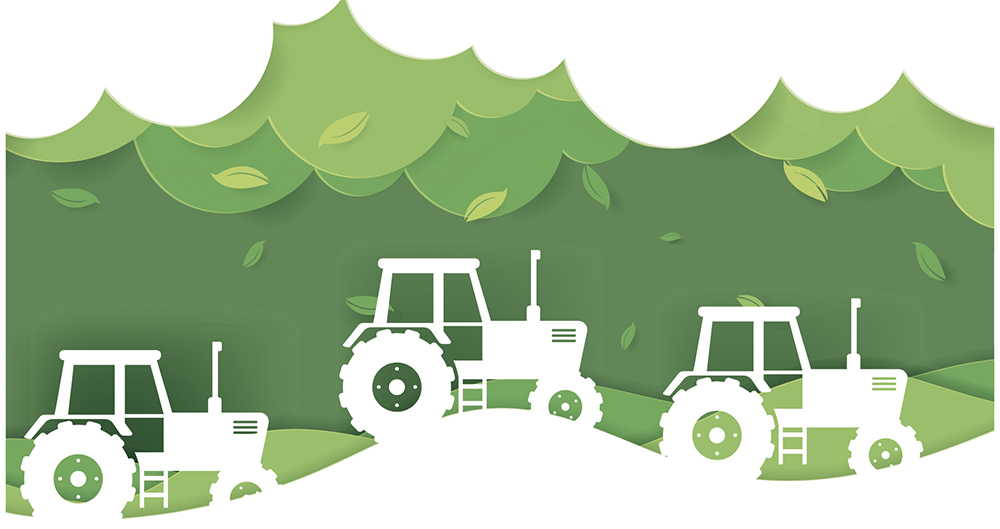
(UPDATED 12/31/2021 – This story has been updated from an earlier version that contained some out-of-date material)
“How sustainable is my five-year old German combine that’s maybe still functional for another decade, but now it’s junk because I can’t find a replacement electronic panel?”
So asks one Manitoba farmer, whose situation is far from unique.
The panel he needed was nowhere to be found. Every scrapped Claas had long ago been stripped of this particular part. So he and a buddy “fixed” the faulty part.
It worked. Sort of. Except for some safety issues.
“The manufacturers are building twice as many combines as the market can absorb,” says Larry Hertz, vice-president of the Western Equipment Dealers Association.
“North American farmers might buy 6,500 combines next year. The companies are building double that number. Where’s the sustainability in that?
“Obviously as the machines become dated and the electronics systems become dated, I’m not sure that a lot of those components will remain in production. Those parts become more expensive with time and that makes the machine obsolete.
“Some people may try to repair circuit panels or build new ones, but that becomes a safety factor. If you’re building your own panels and they’re off-spec or OEM (original equipment manufacturer) spec, you could have a hidden glitch that can create a big problem in the field or on the road.”
Hertz says the used combine market poses a real problem in terms of sustainability. Many combines are traded by the first-generation owner with 200 to 400 hours. Traditionally, those combines were purchased by medium-sized farmers.
But the proliferation of big farms has come at the expense of medium-sized farms. Those second-generation buyers are disappearing, which has disrupted the combine market.
Gene Breker is one of the founders of Amitytech, and before that worked with the development of the venerable Concord air drill. He deals with farmers on a regular basis on issues of obsolete technology and sustainability.
“Farmers don’t like scrapping a piece of equipment if there’s still life in it, or if it’s just the electronics that have gone bad,” says Breker.
“Farmers really appreciate the fact that our single disc drill has gone through four electronic cycles over 13 years. Four different electronic systems so the drill can keep on working, because the mechanical components don’t wear out. Electronics improve all the time, so we’ve put together four complete electronic packages for the drill.
“A complete electronic change is $5,000 to $8,000. That includes new sensors, new wiring harness and everything else. The entire industry now is ISO and nearly everything made now plugs into the tractor ISO monitor head, so you seldom need to buy a new monitor head.”
Breker says there’s virtually no market for used seeding and tillage machinery in the 60-foot to 80-foot and bigger range. Farmers looking for used equipment want 40-foot machines and smaller. In terms of sustainability, that leaves a lot of expensive orphaned iron.
“This is a serious issue. Over the years I’ve suggested to the company we should make a 60-foot machine designed to remove the 10-foot wing tips and turn it into a 40-foot machine,” says Breker.
“When it comes to seeding and tillage, I don’t think there’s very much scrap. Remember Concord? We sold more than 5,000 Concords in North America. Just about every one is still working. Farmers have figured out different ways to use them. You very rarely see a Concord scrapped in the trees. I think that meets the criteria for sustainability.”
No comments:
Post a Comment