U.S. Army still relies on carbon-based fuels, report says
Photo by Sgt. Nathan Franco
The U.S. Army still relies on carbon-based fuels, which will likely remain the primary fuel, according to a report released by Dr. David J. Gorsich and Dr. André Boehman.
Army’s chief scientist for ground vehicle systems Dr. David J. Gorsich and professor of mechanical engineering at the University of Michigan, director of the university’s Walter E. Lay Automotive Laboratory André Boehman noted in its report that the Army’s requirement calls for the highest energy-density fuel combined with the lowest mass and volume—and gasoline and diesel still win over alternative energy.
Army scientists’ report examined why isn’t the U.S. Army using alternative forms of energy and powertrains more extensively to reduce fuel usage for its vehicles?
Tesla is building large semitrucks, and UPS and FedEx are starting to order these vehicles for delivery operations. It seems the entire automotive industry is migrating toward electrification as battery costs have dropped dramatically and recharge times and range have improved accordingly. With all of the major automobile manufacturers moving toward hybrids and electric vehicles, it’s easy to get confused and wonder why the Army is so far behind.
The reality is that the Army is not behind. It has experts in all of these fields who have been conducting research on alternative energy sources and hybrids for military vehicles for more than 20 years. In fact, the Army Rapid Capabilities and Critical Technologies Office recently awarded BAE Systems a $32 million prototype agreement to integrate a hybrid electric drive system onto a Bradley Fighting Vehicle. The development program is part of the Army’s effort to increase vehicle efficiency and boost power generation to support integration of future technologies and improve mobility for combat vehicles on the battlefield.
However, the bottom line is that there is a good reason the Army hasn’t unilaterally decided to switch to alternative fuels. The Army has a unique set of operational requirements, and no current fuel source meeting those requirements contains as much energy, by weight, as diesel or gasoline. Nor is there an alternative form of energy that can be carried or generated on board that, in terms of size or volume, is not at least four to 10 times that of gas and diesel. Electrification of the Army’s ground fleet (for example, by fielding integrated starter generators on tactical vehicles), is very important, but it still relies on diesel as the primary energy source.
This analysis focuses on energy density (the amount of energy stored in a system per unit of volume), conversion of that energy, as well as mass and volume requirements, to determine how they compare to current sources. The full technical paper was published in the Journal of Energy Resources Technology by Andrew Mansfield et al. Titled “Assessment of conventional and alternative energy carriers for use in military vehicle platforms,” the paper was published online Aug. 31, 2020.
General Dynamics Land Systems’ Advanced Ground Mobility Vehicle with in-hub electric drive. Photo by Stephen Baack
This study builds on past studies conducted primarily through the U.S. Army Hybrid-Electric Vehicle Experimentation and Assessment program. To understand why the Army still relies on diesel and gas, we need to understand the Army’s requirements, operating environment, and how energy is stored and transformed into vehicle motion.
That’s done through a process that starts with an energy carrier, which is a substance (fuel) or “material state” that stores energy that can be later converted to other forms such as mechanical work or power. We use the term “energy carrier” because it refers to energy that can exist in a variety of forms and can be converted from one form to another. Such carriers may include springs, flywheels, electrical batteries, pressurized air, hydrogen, petroleum, coal, wood and natural gas. A flywheel is a spinning mechanical device that is used to store rotational energy that provides continuous energy when the energy source, say torque from the engine, is intermittent.
Thus, energy carriers are the vehicle’s onboard store of energy, which is transformed into useful mechanical energy through a conversion device, such as combustion engines, electric motors or fuel cells. This process provides mechanical energy that can drive a vehicle transmission, which then can produce power such that:
Energy Carrier → Conversion Device → Mechanical Energy
There are several categories of transportation-applicable energy carriers, i.e., those that can reasonably be stored on board a vehicle, such as chemical and mechanical energy carriers. The various energy carriers and conversion devices considered in this analysis are illustrated in Figure 1, below. They are: hydrocarbon fuels (gas or diesel), batteries, supercapacitors, hydrogen (fuel cell) and flywheels.
Batteries and supercapacitors (electrochemical devices similar to batteries but designed to produce very high specific power, i.e. for use in regenerative brakes on hybrid vehicles) are often compared in terms of their energy and power. Batteries have a higher energy density (the amount of energy that the system can store), compared with supercapacitors, which have a higher power density (the rate of energy that the system can release).
That makes supercapacitors particularly suitable for storing and releasing large amounts of power relatively quickly, whereas batteries are capable of storing large amounts of energy over long periods of time.
Key military requirements assume that fuels will need to be transported to the battlefield, so there is a need for high-energy dense fuels with low weight, as well as a way to generate electricity. That’s because a typical Soldier carries four or five electronic devices—and in the future that burden will likely double—and such devices are useless without electrical power generation. Modern lithium ion (Li-ion) batteries cannot keep up with demand even if a Soldier could carry a large supply.
Figure 2 summarizes the performance characteristics of commercial energy carriers and promising future technologies, and illustrates the distinct superiority of diesel and gasoline fuels. They are by far the most widely used energy carriers and are used in conjunction with internal combustion engines or gas turbines with varying levels of commercialization.
Commercialization (COM) refers to the mass-market availability of a particular technology. Generally, the cheaper a technology is, the more widely available it will be for Army use. Therefore, the higher the commercialization ((↑) signifies increasing, and (↓) decreasing), the more practical the fuel is for implementation in Army vehicles. Subsequently, it becomes a factor in our best energy carrier options, and the new equation is as follows:
(Energy Carrier + Conversion Device) + (↑) COM = Mechanical Energy (Best Performance Characteristics)
Factors such as cost, reliability and commercialization strongly impact the usefulness of some of the options in Figure 2. Typical fuels (with their ease of commercialization given in parentheses), can be liquid, such as kerosene (high), diesel (high), gasoline (high) and ethanol (medium); or gaseous, such as methane and natural gas (medium to high). Lithium air (Li–air) batteries and hydrogen are middle to low performers, with similar energy density to fuels but an order-of-magnitude lower specific energy. Li-ion (medium to high) and nickel-metal hydride (Ni-MH; high) batteries, as well as flywheels (high) are at the lower end of performance with an order-of-magnitude lower energy density and specific energy values compared with high-performance electrochemical energy carriers.
Ni-MH batteries have become very well established in the marketplace, while Li-ion batteries are more recently commercialized. Li-air batteries (low) are a very promising future technology that is not yet commercial.
The U.S. Army still relies on carbon-based fuels, which will likely remain the primary fuel, according to a report released by Dr. David J. Gorsich and Dr. André Boehman.
Army’s chief scientist for ground vehicle systems Dr. David J. Gorsich and professor of mechanical engineering at the University of Michigan, director of the university’s Walter E. Lay Automotive Laboratory André Boehman noted in its report that the Army’s requirement calls for the highest energy-density fuel combined with the lowest mass and volume—and gasoline and diesel still win over alternative energy.
Army scientists’ report examined why isn’t the U.S. Army using alternative forms of energy and powertrains more extensively to reduce fuel usage for its vehicles?
Tesla is building large semitrucks, and UPS and FedEx are starting to order these vehicles for delivery operations. It seems the entire automotive industry is migrating toward electrification as battery costs have dropped dramatically and recharge times and range have improved accordingly. With all of the major automobile manufacturers moving toward hybrids and electric vehicles, it’s easy to get confused and wonder why the Army is so far behind.
The reality is that the Army is not behind. It has experts in all of these fields who have been conducting research on alternative energy sources and hybrids for military vehicles for more than 20 years. In fact, the Army Rapid Capabilities and Critical Technologies Office recently awarded BAE Systems a $32 million prototype agreement to integrate a hybrid electric drive system onto a Bradley Fighting Vehicle. The development program is part of the Army’s effort to increase vehicle efficiency and boost power generation to support integration of future technologies and improve mobility for combat vehicles on the battlefield.
However, the bottom line is that there is a good reason the Army hasn’t unilaterally decided to switch to alternative fuels. The Army has a unique set of operational requirements, and no current fuel source meeting those requirements contains as much energy, by weight, as diesel or gasoline. Nor is there an alternative form of energy that can be carried or generated on board that, in terms of size or volume, is not at least four to 10 times that of gas and diesel. Electrification of the Army’s ground fleet (for example, by fielding integrated starter generators on tactical vehicles), is very important, but it still relies on diesel as the primary energy source.
This analysis focuses on energy density (the amount of energy stored in a system per unit of volume), conversion of that energy, as well as mass and volume requirements, to determine how they compare to current sources. The full technical paper was published in the Journal of Energy Resources Technology by Andrew Mansfield et al. Titled “Assessment of conventional and alternative energy carriers for use in military vehicle platforms,” the paper was published online Aug. 31, 2020.
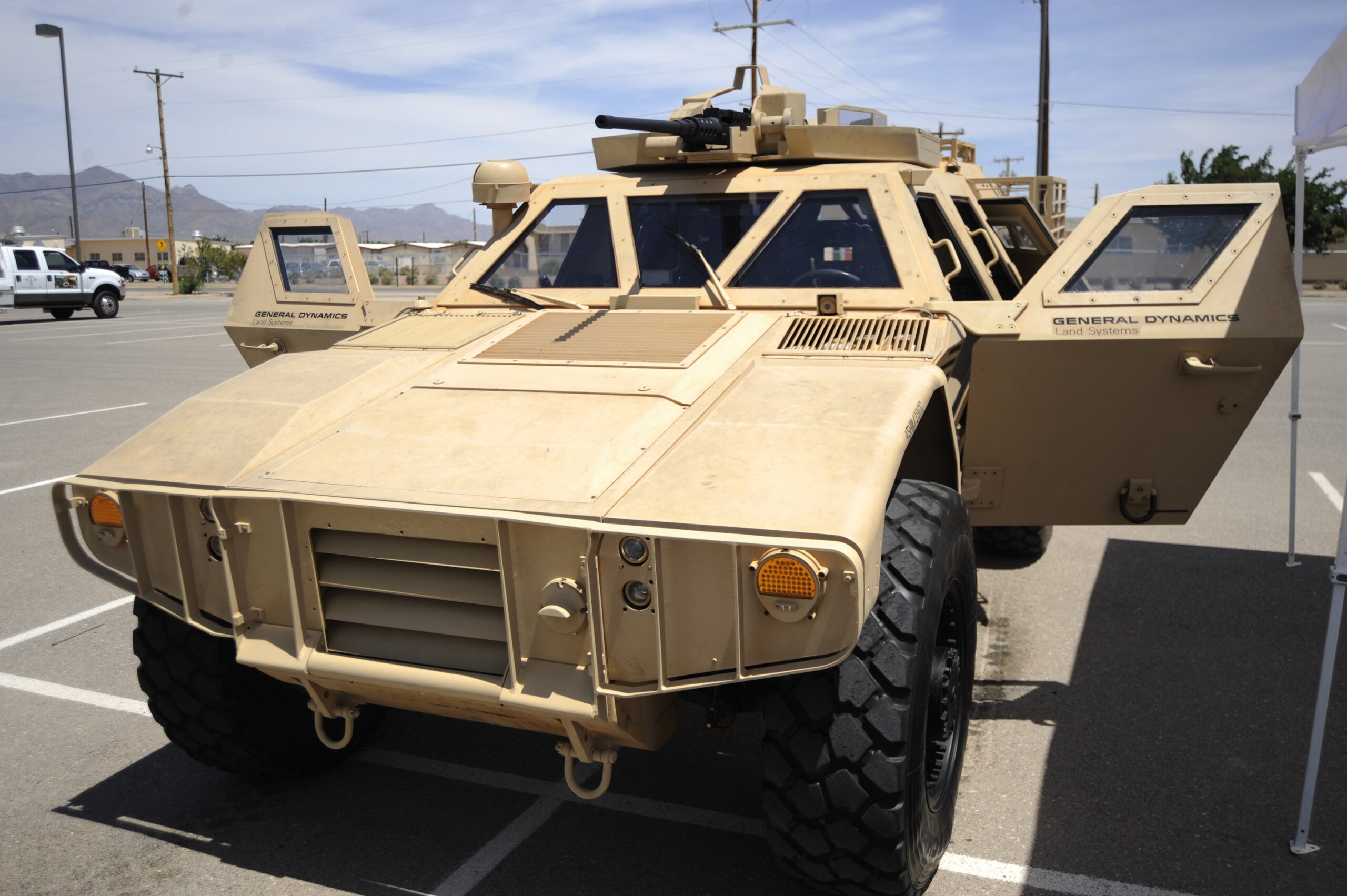
This study builds on past studies conducted primarily through the U.S. Army Hybrid-Electric Vehicle Experimentation and Assessment program. To understand why the Army still relies on diesel and gas, we need to understand the Army’s requirements, operating environment, and how energy is stored and transformed into vehicle motion.
That’s done through a process that starts with an energy carrier, which is a substance (fuel) or “material state” that stores energy that can be later converted to other forms such as mechanical work or power. We use the term “energy carrier” because it refers to energy that can exist in a variety of forms and can be converted from one form to another. Such carriers may include springs, flywheels, electrical batteries, pressurized air, hydrogen, petroleum, coal, wood and natural gas. A flywheel is a spinning mechanical device that is used to store rotational energy that provides continuous energy when the energy source, say torque from the engine, is intermittent.
Thus, energy carriers are the vehicle’s onboard store of energy, which is transformed into useful mechanical energy through a conversion device, such as combustion engines, electric motors or fuel cells. This process provides mechanical energy that can drive a vehicle transmission, which then can produce power such that:
Energy Carrier → Conversion Device → Mechanical Energy
There are several categories of transportation-applicable energy carriers, i.e., those that can reasonably be stored on board a vehicle, such as chemical and mechanical energy carriers. The various energy carriers and conversion devices considered in this analysis are illustrated in Figure 1, below. They are: hydrocarbon fuels (gas or diesel), batteries, supercapacitors, hydrogen (fuel cell) and flywheels.
Batteries and supercapacitors (electrochemical devices similar to batteries but designed to produce very high specific power, i.e. for use in regenerative brakes on hybrid vehicles) are often compared in terms of their energy and power. Batteries have a higher energy density (the amount of energy that the system can store), compared with supercapacitors, which have a higher power density (the rate of energy that the system can release).
That makes supercapacitors particularly suitable for storing and releasing large amounts of power relatively quickly, whereas batteries are capable of storing large amounts of energy over long periods of time.
Key military requirements assume that fuels will need to be transported to the battlefield, so there is a need for high-energy dense fuels with low weight, as well as a way to generate electricity. That’s because a typical Soldier carries four or five electronic devices—and in the future that burden will likely double—and such devices are useless without electrical power generation. Modern lithium ion (Li-ion) batteries cannot keep up with demand even if a Soldier could carry a large supply.
Figure 2 summarizes the performance characteristics of commercial energy carriers and promising future technologies, and illustrates the distinct superiority of diesel and gasoline fuels. They are by far the most widely used energy carriers and are used in conjunction with internal combustion engines or gas turbines with varying levels of commercialization.
Commercialization (COM) refers to the mass-market availability of a particular technology. Generally, the cheaper a technology is, the more widely available it will be for Army use. Therefore, the higher the commercialization ((↑) signifies increasing, and (↓) decreasing), the more practical the fuel is for implementation in Army vehicles. Subsequently, it becomes a factor in our best energy carrier options, and the new equation is as follows:
(Energy Carrier + Conversion Device) + (↑) COM = Mechanical Energy (Best Performance Characteristics)
Factors such as cost, reliability and commercialization strongly impact the usefulness of some of the options in Figure 2. Typical fuels (with their ease of commercialization given in parentheses), can be liquid, such as kerosene (high), diesel (high), gasoline (high) and ethanol (medium); or gaseous, such as methane and natural gas (medium to high). Lithium air (Li–air) batteries and hydrogen are middle to low performers, with similar energy density to fuels but an order-of-magnitude lower specific energy. Li-ion (medium to high) and nickel-metal hydride (Ni-MH; high) batteries, as well as flywheels (high) are at the lower end of performance with an order-of-magnitude lower energy density and specific energy values compared with high-performance electrochemical energy carriers.
Ni-MH batteries have become very well established in the marketplace, while Li-ion batteries are more recently commercialized. Li-air batteries (low) are a very promising future technology that is not yet commercial.
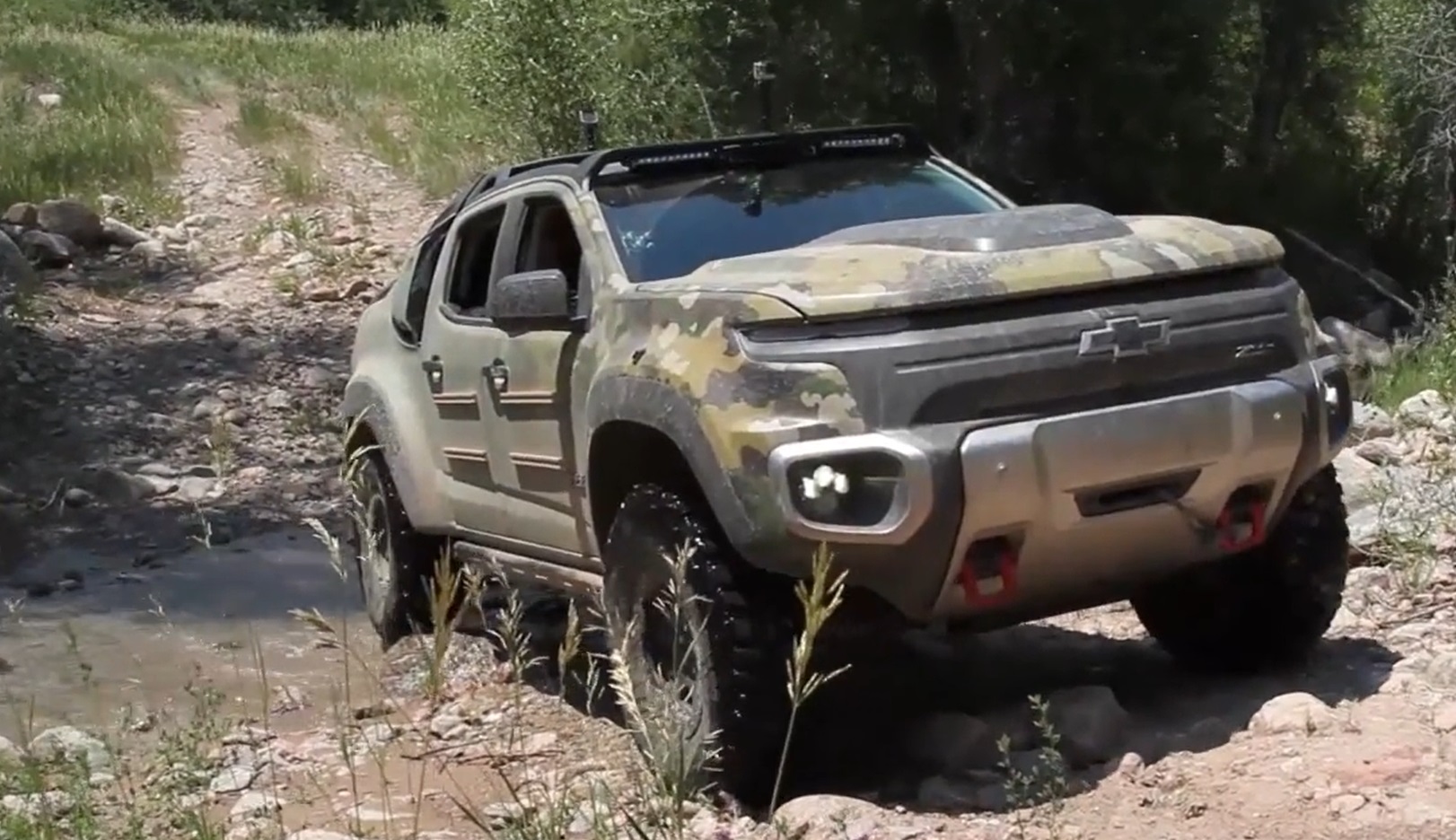
Army’s ZH2 fuel-cell electric vehicle
Many full or partially electric vehicles from the past decade use Ni-MH batteries. Newer electric automotive vehicle manufacturers, such as Tesla, have chosen to use Li-ion batteries.
The conversion devices considered were combustion engines, electric motors, and fuel cells. Their performance characteristics can be seen in Figure 3, which shows a measurement of the actual performance of each power source versus its power output. Electric motors have the highest level of performance, but, as we saw earlier, they are connected to batteries that don’t have enough stored energy to last for military applications. Gasoline and diesel combustion engines are next, with methane engines at the lowest level.
Another important factor when considering alternative energy carriers is how much vehicle space will be required to transport the requisite fuel as well as all of the ancillary equipment necessary to operate and adequately power the vehicle system.
In order to assess and compare approximately how much onboard space each alternative energy carrier would require, researchers evaluated the approximate space claims by comparing the energy carrier volume and powertrain mass associated with each carrier with regard to the High Mobility Multipurpose Wheeled Vehicle (HMMWV) and Family of Medium Tactical Vehicles (FMTV) platforms. Figure 4 illustrates the predicted total powertrain mass and energy carrier volume for various single and dual hybrid energy carriers for the two vehicle systems. The results indicate that diesel and gasoline fuels are clearly the optimal energy carriers for both vehicle systems, with the lowest total powertrain masses and low energy carrier volumes.
This is true of the results for both single energy carriers in the left-side graphs of Figure 4 and for dual hybrid carriers (diesel + battery or supercapacitor) in the right-side graphs. Of the dual hybrid energy carriers, diesel fuel + Li-air hybrid is clearly optimal, yielding the greatest rate of hybridization (50 percent diesel and 50 percent Li-air) considering the relatively small mass and volume increases. These results also clearly indicate the dramatic benefits of Li-ion and Li-air battery technology over more traditionally used Ni-MH.
A prime candidate for alternative-energy carrier for military vehicles would include an optimized fuel source and conversion device, a high level of commercialization, as well as a system mass and volume as small as possible. In general, smaller (↓) mass and volume (M&V) alternatives increase the operational effectiveness of vehicles and, therefore, become part of our equation as follows:
(Energy Carrier → Conversion Device) + (↑) COM + (↓) M&V = Mechanical Energy (Best Performance Characteristics)
With respect to batteries in both single and dual energy systems, the three alternative energy technologies considered here resulted in dramatically different total powertrain mass and energy carrier volumes—much larger than for diesel fuel systems. Use of Ni-MH batteries results in a total mass 15 to 22 times larger and energy carrier volume 25 times larger than the diesel fuel system. Li-ion batteries are a dramatic improvement over Ni-MH, resulting in a total mass only 4.5 to 7 times larger and energy carrier volume 4 times larger than the diesel fuel system.
Even with this improvement, the large mass and volume increase over a diesel fuel system presents a significant challenge to its implementation, as driving performance and usable volume would likely fall dramatically. The effect of large mass and volume increases for Li-ion battery systems in similar large vehicles is evident in the short 300 – 500 mile range of the Tesla semitruck, which uses Li-ion batteries, compared with a more typical 1,000-mile range for a diesel semitruck.
Relative to diesel fuel, both hydrogen and methane yield similar total powertrain masses but significantly larger (3-5 times) energy carrier volumes. This highlights the primary issue with the low energy density of gaseous fuels and indicates that at existing and near-term technology levels, if these fuels are used as the single energy carrier for military ground vehicles, a large portion of their usable payload carrying capacity (volume) would be lost.
The Army has a unique set of requirements that cannot currently be better satisfied with anything other than gas or diesel as the primary energy carrier. Considering the high torque performance of diesel combustion engines, diesel fuel is clearly the optimal energy carrier for the Army’s ground vehicle platforms, from the perspective of both the total powertrain mass (energy carrier + conversion device), and stored energy volume.
Military applications provide common and unique challenges for energy storage systems and energy density, with regard to mass and volume, and are critical challenges for commercial and military energy storage systems. Energy storage systems for military applications must be able to be stored and operate reliably at low and high temperatures (minus 46 to 88 Celsius) and under greater shock and vibration conditions than commercial systems. Cooling systems for military energy storage and export power solutions are complicated by the harsh environmental conditions they must withstand. Consequently, this combined scenario continues to drive the Army toward liquid fuels and their physical properties.
In the future, for the Army to consider a fleetwide, wholesale change that moves away from hydro carbon fuels, it needs to develop a very detailed strategy and step-by-step paths to acquire any new technologies. This hasn’t happened yet because there are still too many obstacles that need to be resolved before alternative energy carriers can become a viable option for full-scale use. It is unlikely, in terms of scale and scope, that the Army will transform to something else in the next 10 years. While alternative power-generation exists now in many different forms, alternative fuels aren’t ready for prime time when it comes to large-scale Army use.
Colton Jones
Colton Jones is technology editor for Defenсe Blog. He has written about emerging technology in military magazines and elsewhere.
Many full or partially electric vehicles from the past decade use Ni-MH batteries. Newer electric automotive vehicle manufacturers, such as Tesla, have chosen to use Li-ion batteries.
The conversion devices considered were combustion engines, electric motors, and fuel cells. Their performance characteristics can be seen in Figure 3, which shows a measurement of the actual performance of each power source versus its power output. Electric motors have the highest level of performance, but, as we saw earlier, they are connected to batteries that don’t have enough stored energy to last for military applications. Gasoline and diesel combustion engines are next, with methane engines at the lowest level.
Another important factor when considering alternative energy carriers is how much vehicle space will be required to transport the requisite fuel as well as all of the ancillary equipment necessary to operate and adequately power the vehicle system.
In order to assess and compare approximately how much onboard space each alternative energy carrier would require, researchers evaluated the approximate space claims by comparing the energy carrier volume and powertrain mass associated with each carrier with regard to the High Mobility Multipurpose Wheeled Vehicle (HMMWV) and Family of Medium Tactical Vehicles (FMTV) platforms. Figure 4 illustrates the predicted total powertrain mass and energy carrier volume for various single and dual hybrid energy carriers for the two vehicle systems. The results indicate that diesel and gasoline fuels are clearly the optimal energy carriers for both vehicle systems, with the lowest total powertrain masses and low energy carrier volumes.
This is true of the results for both single energy carriers in the left-side graphs of Figure 4 and for dual hybrid carriers (diesel + battery or supercapacitor) in the right-side graphs. Of the dual hybrid energy carriers, diesel fuel + Li-air hybrid is clearly optimal, yielding the greatest rate of hybridization (50 percent diesel and 50 percent Li-air) considering the relatively small mass and volume increases. These results also clearly indicate the dramatic benefits of Li-ion and Li-air battery technology over more traditionally used Ni-MH.
A prime candidate for alternative-energy carrier for military vehicles would include an optimized fuel source and conversion device, a high level of commercialization, as well as a system mass and volume as small as possible. In general, smaller (↓) mass and volume (M&V) alternatives increase the operational effectiveness of vehicles and, therefore, become part of our equation as follows:
(Energy Carrier → Conversion Device) + (↑) COM + (↓) M&V = Mechanical Energy (Best Performance Characteristics)
With respect to batteries in both single and dual energy systems, the three alternative energy technologies considered here resulted in dramatically different total powertrain mass and energy carrier volumes—much larger than for diesel fuel systems. Use of Ni-MH batteries results in a total mass 15 to 22 times larger and energy carrier volume 25 times larger than the diesel fuel system. Li-ion batteries are a dramatic improvement over Ni-MH, resulting in a total mass only 4.5 to 7 times larger and energy carrier volume 4 times larger than the diesel fuel system.
Even with this improvement, the large mass and volume increase over a diesel fuel system presents a significant challenge to its implementation, as driving performance and usable volume would likely fall dramatically. The effect of large mass and volume increases for Li-ion battery systems in similar large vehicles is evident in the short 300 – 500 mile range of the Tesla semitruck, which uses Li-ion batteries, compared with a more typical 1,000-mile range for a diesel semitruck.
Relative to diesel fuel, both hydrogen and methane yield similar total powertrain masses but significantly larger (3-5 times) energy carrier volumes. This highlights the primary issue with the low energy density of gaseous fuels and indicates that at existing and near-term technology levels, if these fuels are used as the single energy carrier for military ground vehicles, a large portion of their usable payload carrying capacity (volume) would be lost.
The Army has a unique set of requirements that cannot currently be better satisfied with anything other than gas or diesel as the primary energy carrier. Considering the high torque performance of diesel combustion engines, diesel fuel is clearly the optimal energy carrier for the Army’s ground vehicle platforms, from the perspective of both the total powertrain mass (energy carrier + conversion device), and stored energy volume.
Military applications provide common and unique challenges for energy storage systems and energy density, with regard to mass and volume, and are critical challenges for commercial and military energy storage systems. Energy storage systems for military applications must be able to be stored and operate reliably at low and high temperatures (minus 46 to 88 Celsius) and under greater shock and vibration conditions than commercial systems. Cooling systems for military energy storage and export power solutions are complicated by the harsh environmental conditions they must withstand. Consequently, this combined scenario continues to drive the Army toward liquid fuels and their physical properties.
In the future, for the Army to consider a fleetwide, wholesale change that moves away from hydro carbon fuels, it needs to develop a very detailed strategy and step-by-step paths to acquire any new technologies. This hasn’t happened yet because there are still too many obstacles that need to be resolved before alternative energy carriers can become a viable option for full-scale use. It is unlikely, in terms of scale and scope, that the Army will transform to something else in the next 10 years. While alternative power-generation exists now in many different forms, alternative fuels aren’t ready for prime time when it comes to large-scale Army use.
Colton Jones
Colton Jones is technology editor for Defenсe Blog. He has written about emerging technology in military magazines and elsewhere.
No comments:
Post a Comment