Driving down the costs of hydrogen fuel: Prototype achieves 99% yield 8 times faster than conventional batch reactors
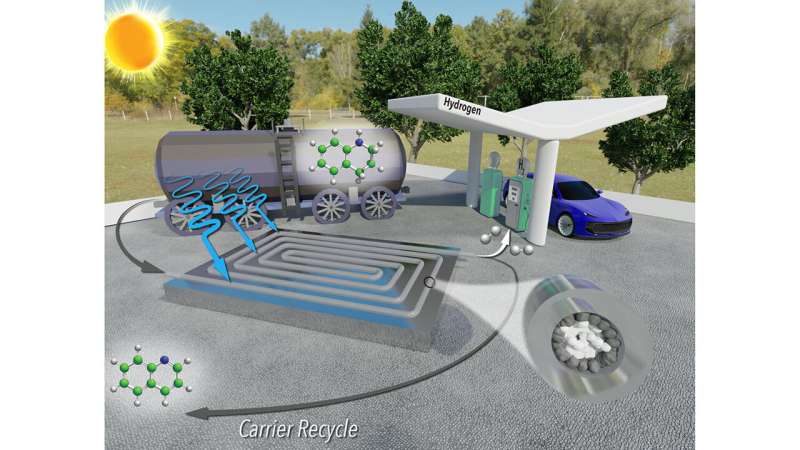
Researchers from North Carolina State University have developed a new technique for extracting hydrogen gas from liquid carriers that is faster, less expensive and more energy efficient than previous approaches.
"Hydrogen is widely viewed as a sustainable energy source for transportation, but there are some technical obstacles that need to be overcome before it can be viewed as a practical alternative to existing technologies," says Milad Abolhasani, corresponding author of a paper on the new technique and an associate professor of chemical and biomolecular engineering at NC State. "One of the big obstacles to the adoption of a hydrogen economy is the cost of storage and transportation."
Hydrogen fuel does not result in CO2 emissions. And hydrogen refueling stations could be located at existing gas stations, taking advantage of existing infrastructure. But transporting hydrogen gas is dangerous, so hydrogen needs to be transported via a liquid carrier. A key obstacle for this strategy is that extracting hydrogen from the liquid carrier at destination sites, such as fueling stations, is energy intensive and expensive.
"Previous research has shown that it is possible to use photocatalysts to release hydrogen gas from a liquid carrier using only sunlight," Abolhasani says. "However, existing techniques for doing this were laborious, time consuming and required a significant amount of rhodium—a metal that is very expensive."
"We've developed a technique that applies a reusable photocatalyst and sunlight to extract hydrogen gas from its liquid carrier more quickly and using less rhodium—making the entire process significantly less expensive," says Malek Ibrahim, first author of the paper and a former postdoctoral researcher at NC State. "What's more, the only byproducts are hydrogen gas and the liquid carrier itself, which can be reused repeatedly. It's very sustainable."
One key to the success of the new technique is that it is a continuous-flow reactor. The reactor resembles a thin, clear tube packed with sand. The "sand" consists of micron-scale grains of titanium oxide, many of which are coated with rhodium. The hydrogen-carrying liquid is pumped into one end of the tube. The rhodium-coated particles line the outer part of the tube, where sunlight can reach them. These particles are photoreactive catalysts that, in the presence of sunlight, react with the liquid carrier to release hydrogen molecules as a gas.
The researchers precisely engineered the system so that only the outer grains of titanium oxide are coated with rhodium, ensuring the system uses no more rhodium than is necessary.
"In a conventional batch reactor, 99% of the photocatalyst is titanium oxide and 1% is rhodium," Abolhasani says. "In our continuous flow reactor, we only need to use 0.025% rhodium, which makes a big difference in the final cost. A single gram of rhodium costs more than $500."
In their prototype reactor, the researchers were able to achieve a 99% yield—meaning that 99% of the hydrogen molecules were released from the liquid carrier—in three hours.
"That's eight times faster than conventional batch reactors, which take 24 hours to reach 99% yield," Ibrahim says. "And the system should be easy to scale up or scale out to allow for catalyst reuse on commercial scale—you can simply make the tube longer or merge multiple tubes running in parallel."
The flow system can run continuously for up to 72 hours before its efficiency decreases. At this point, the catalyst can be "regenerated" without removing it from the reactor—it's a simple cleaning process that takes about six hours. The system can then be restarted and run at full efficiency for another 72 hours.
NC State has filed a provisional patent for the technology.
The research was published in the journal ChemSusChem.
Hydrogen production method opens up clean energy possibilities
IMAGE: POSTDOCTORAL RESEARCHER JAMIE KEE AND PROFESSOR SU HA AND THE NOVEL REACTOR THEY DEVELOPED TO PRODUCE PURE COMPRESSED HYDROGEN. view more
CREDIT: WSU PHOTO SERVICES
PULLMAN, Wash. – A new energy-efficient way to produce hydrogen gas from ethanol and water has the potential to make clean hydrogen fuel a more viable alternative for gasoline to power cars.
Washington State University researchers used the ethanol and water mixture and a small amount of electricity in a novel conversion system to produce pure compressed hydrogen. The innovation means that hydrogen could be made on-site at fueling stations, so only the ethanol solution would have to be transported. It is a major step in eliminating the need to transport high-pressure hydrogen gas, which has been a major stumbling block for its use as a clean energy fuel.
“This is a new way of thinking about how to produce hydrogen gas,” said Su Ha, professor in the Gene and Linda Voiland School of Chemical Engineering and Bioengineering and corresponding author on the paper published in the journal, Applied Catalysis A. “If there are enough resources, I think it has a really good chance of making a big impact on the hydrogen economy in the near future.”
Using hydrogen as a fuel for cars is a promising but unrealized clean energy. Like an electric-powered car, a hydrogen fuel-cell powered car doesn’t emit any harmful carbon dioxide. Unlike an electric car, it can be filled up with hydrogen gas in minutes at hydrogen fueling stations.
Despite the promise of hydrogen technology, however, storing and transporting high-pressure hydrogen gas in fuel tanks creates significant economic and safety challenges. Because of the challenges, there is little hydrogen gas infrastructure in the U.S., and the technology’s market penetration is very low.
In their work, the WSU researchers created a conversion system with an anode and a cathode. When they put a small amount of electricity into the ethanol and water mixture with a catalyst, they were able to electrochemically produce pure compressed hydrogen. Carbon dioxide from the reaction is captured in a liquid form.
Instead of having to transport hazardous hydrogen gas, the conversion method would mean that the existing infrastructure for transporting ethanol could be used and that the compressed hydrogen gas could be easily and safely created on-demand at gas stations.
“We’re already using ethanol-containing gasoline at every gas station,” said Ha. “You can imagine that an ethanol water mixture can be easily delivered to a local gas station using our existing infrastructure, and then using our technology, you can produce hydrogen that is ready to pump into a hydrogen fuel cell car. We don’t need to worry about hydrogen storage or transportation at all.”
The electrochemical system the team developed uses less than half the electricity of pure water splitting, another method that researchers have studied for de-carbonized hydrogen production. Instead of working hard to compress the hydrogen gas later in the process, the researchers used less energy by instead compressing the liquid ethanol mixture, thereby directly producing an already compressed hydrogen gas.
“The presence of the ethanol in water changes the chemistry,” said graduate student Wei-Jyun Wang, a co-lead author on the paper. “We can actually do our reaction at a much lower electrical voltage than is typically needed for pure water electrolysis.”
Their system also doesn’t require an expensive membrane that other water splitting methods do. The resulting hydrogen from the electrochemical reaction is then ready for use.
“A process that offers a low-electrical energy cost alternative to water electrolysis and can effectively capture carbon dioxide while producing compressed hydrogen could have a significant impact on the hydrogen economy,” said Jamie Kee, a Voiland School postdoctoral researcher and one of lead authors on the paper. “It’s really exciting because there are a whole lot of aspects that play into improving the production methods of hydrogen.”
The researchers are working to scale up the technology and operate it in a continuous manner. They also are working to make use of the carbon dioxide captured in the liquid.
The work was funded by the Gas Technology Institute and the US Department of Energy’s RAPID Manufacturing Institute.
JOURNAL
Applied Catalysis
METHOD OF RESEARCH
Experimental study
SUBJECT OF RESEARCH
Not applicable
ARTICLE TITLE
Caustic Aqueous Phase Electrochemical Reforming (CAPER) of Ethanol for Process Intensified Compressed Hydrogen Production
ARTICLE PUBLICATION DATE
10-May-2022
No comments:
Post a Comment