Bloomberg News | April 24, 2024 |
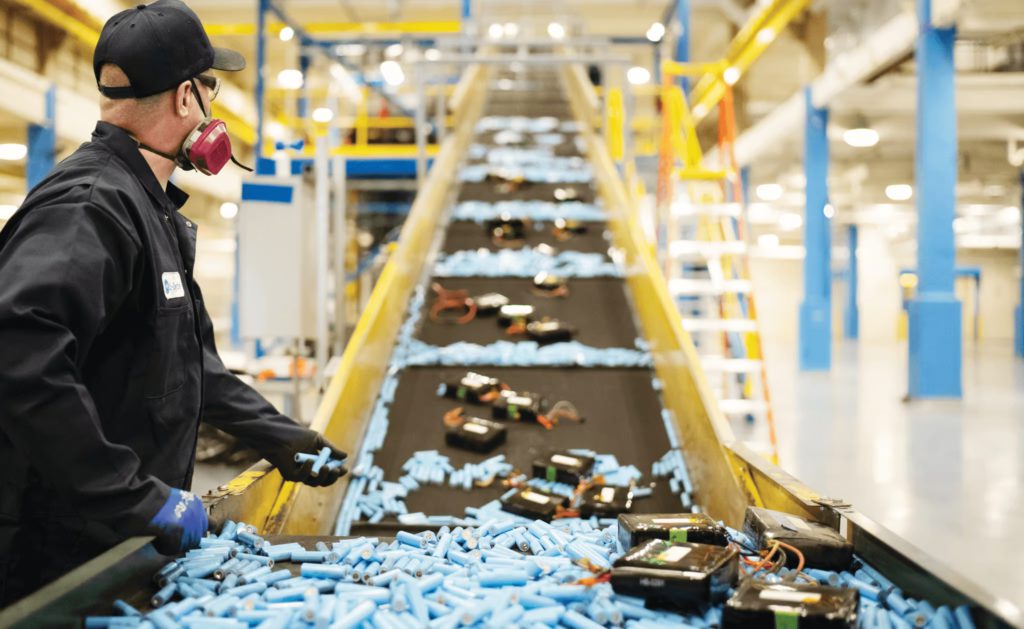
Credit: Li-Cycle
Making a battery for an electric vehicle typically requires mining hundreds of pounds of hard-to-extract minerals. That’s put a spotlight on batteries’ heavy environmental toll, at least upfront.

But the latest advances in battery recycling, including by leading US battery recycler Redwood Materials, are shrinking EVs’ footprint.
Traditional methods of ripping materials out of the ground and refining them for battery backs requires enormous amounts of energy. As a result, the initial carbon footprint of an EV is higher than a comparable internal combustion engine vehicle. Those upfront emissions are paid back over time with the superior efficiency of electric motors, leading to a 70% reduction in total emissions over the average life of the vehicle.
In the US, it takes about 25,500 miles (41,000 kilometers) of driving for an EV to break even, according to a BloombergNEF analysis. That payback figure, however, assumes that every EV is made with newly mined lithium, nickel and cobalt — as if all the materials will end up in a landfill at the end of a vehicle’s life. But that’s not what’s happening. EV batteries are simply too valuable to toss out, and a new industry of recyclers is busy snatching them all up.
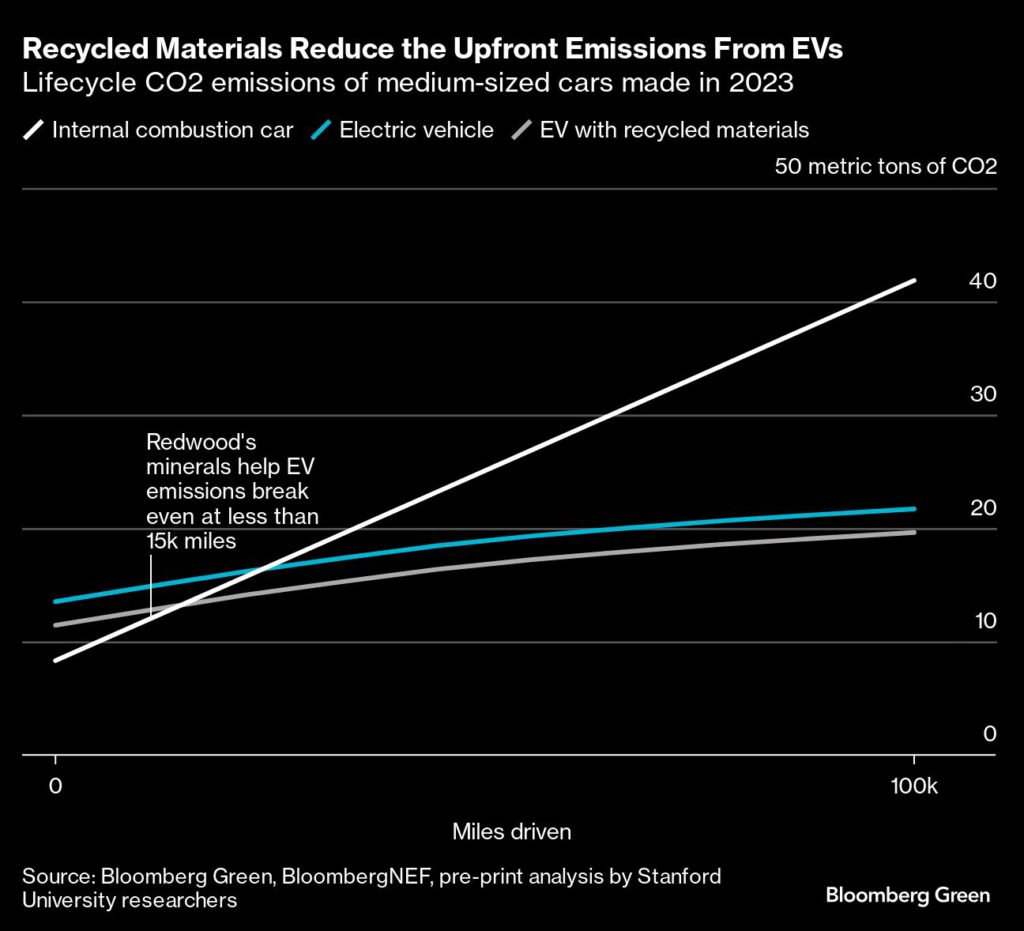
Though still in its infancy, EV recycling is already profitable and capable of recovering more than 95% of the key minerals. A new analysis by Stanford University researchers, which is still under peer review, found that Redwood Materials’ recycling process produces up to 80% fewer emissions than the traditional supply chain using CO2 belching refineries. That’s enough to shorten an average EV’s environmental breakeven time with an internal combustion vehicle to less than 15,000 miles. Every mile thereafter is a carbon win against the internal combustion engine.
Clean electricity matters
Fully assessing when an EV hits its breakeven point depends on the source of electricity used for battery manufacturing and charging the vehicle. Cleaner electricity means a shorter payback period, but even in regions that still get electricity from coal, EVs eventually win out.
The boom in renewable energy will make EVs even less polluting. Solar installations have set annual records worldwide for 22 consecutive years, and the pace appears to be accelerating, according to data from the International Energy Agency. By 2030, when the US grid is expected to get two thirds of its power from carbon-free sources, an EV built with recycled materials could break even on emissions in a matter of months.
The Stanford report found that recycling batteries used 79% less energy and resulted in 55% fewer CO2 emissions compared to traditional refining. Additional savings come from keeping the recycling supply chain local compared to the globe-circling refining process for freshly extracted minerals. Closing the loop brings the total CO2 savings to 80%.
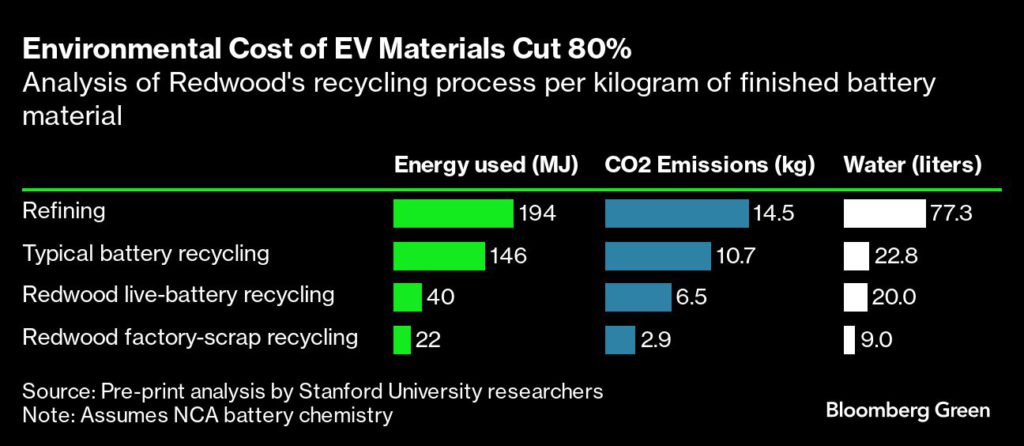
The benefits of recycling are only just beginning to accrue, according to Will Tarpeh, an assistant professor of chemical engineering and one of the Stanford paper’s senior authors. That’s because EVs are still new, and only relatively small numbers are ready for the recycling heap.
Still, the world is already on track to recycle twice as much lithium-ion battery supply in 2024 as it manufactured in 2014. When considering the environmental toll of an EV, it’s increasingly important to measure the footprint of the materials going in and how it shrinks when some inevitably get a second life.
As recycling grows to rival traditional mining and refining operations, simplicity will become more central to battery design, said Tarpeh.
“Recycling is just catching up to the batteries that we’ve made,” Tarpeh said. “Not very many people are looking at recyclability when they develop battery chemistry, but I think that’s really starting to change.”
(By Tom Randall)
No comments:
Post a Comment