Flawed Propeller Blade Leads to Loss of Propulsion on Containership
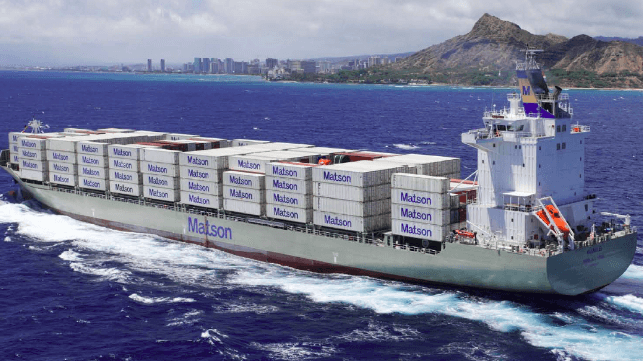
A new report from the National Transportation Safety Board (NTSB) is out examining the causes of a pollution incident and loss of propulsion on a Matson containership while it was sailing along the Pacific coast in 2022 requiring the vessel to be towed to port. Although the engineers aboard the Maunalei (33,771 dwt) had initially suspected a failed blade seal caused a 1,632-gallon hydraulic oil leak and $3 million in damage to the ship, a later analysis points to a flaw in the propeller blade and manufacturing.
The containership, which was built in 2006 at what is now the Philly Shipyard, has a single in-line 7-cylinder, slow-speed, two-stroke diesel engine designed by MAN B&W coupled to a controllable pitch propeller system designed by MAN Energy Solution SE. NTSB reports the propeller system was installed and commissioned at COSCO Nantong Shipyard, in Nantong, China, in October 2020. The ship is 681 feet long with a capacity for 1,992 TEU, and typically operated at speeds of 22 knots. It sails between the U.S. West Coast, Hawaii, Guam, and Southeast Asia.
After loading in Tacoma, Washington on August 4, 2022, the ship departed for Anchorage, Alaska. While running north along the coast near Vancouver Island, Canada, the engineers began receiving an alarm, which they discovered was coming from the lubricating system for the propeller system. The head tank which should have contained hydraulic oil was empty.
They replenished the oil but over the next three days sailing north observed that it was leaking leading to the assumption the vessel was experiencing a failed blade seal. They discovered running at slower speeds the rate of loss was less.
The vessel asked for and received USCG permission to dock in Anchorage on August 7. The technicians, port engineer, and crew determined it could not be repaired at the dock. The plan was to return to Vigor Shipyard in Portland, Oregon for an emergency drydocking.
The leak continued during the trip and finally, the crew was running out of their reserve stock of hydraulic oil. A technician told them to use fresh water but by the afternoon of August 11, they discovered the stern tube lubricating system’s hydraulic oil was being contaminated with water. At that point, the determination was made while the vessel was still about 245 miles northwest of the entrance to the Columbia River, that they had to shut down the main propulsion engine. The Maunalei had to be towed to the shipyard where it finally arrived on August 15.
USCG photo showing the location of the fractures discovered on the blades
Divers discovered fractures at the base of the numbers 2 and 4 blades on the prop. When the vessel was drydocked, they also found free surface cracks on the number two blade near bolt holes and a fracture in the hub of the number 4 blade.
Post-casualty testing found no evidence of significant corrosion, wear, or impact damage to the blades. However, there was progressive cracking which they determined was caused by high-cycle fatigue that initiated at the bolt hole counterbore edges. Subsequent testing of a specimen from the number 4 blade revealed that the tensile test results did not conform to the manufacturer's specification. It did not meet the tensile strength minimum, yield stress minimum, or elongation minimum.
The conclusion was that “high-stress concentrations…combined with the large load variations in normal service operation could have caused the incident.” Modifications made after the incident to the blade foot machining reduced the high-stress concentration on the blade foot.
The NTSB traces the problem to the manufacturing issues with the propeller blades. They believe it was likely an isolated occurrence. The manufacturer revised the recommendations for the bolt hole counterbores to improve fatigue fracture resistance.
No comments:
Post a Comment