As the global push towards Net Zero emissions intensifies, carbon capture, utilisation and storage (CCUS) technologies have emerged as necessary tools for reducing industrial greenhouse gas emissions.
However, as more industries adopt these technologies, the need for precise carbon dioxide (CO2) purity monitoring becomes increasingly crucial. Thermo Fisher Scientific offers advanced solutions that ensure the integrity and effectiveness of carbon capture systems, particularly through the use of Fourier Transform Infrared Spectroscopy (FTIR).
During a showcase webinar held today, 20th August, Trevor Tilmann, Applications Engineer at Thermo Fisher Scientific, Environmental and Process Monitoring, highlighted the importance of monitoring CO2 purity in CCUS networks.
He revealed that impurities in captured CO2 can have significant implications for both the safety of pipelines and the overall success of carbon sequestration efforts.
“The number one reason for continuously monitoring a CO2 stream is for safety of both the people around the pipeline and the pipeline itself,” Tilmann explained.
“Moisture, sulphonated species, oxides of nitrogen, and CO2 itself can react to create acidic conditions within the pipeline. This can cause corrosion, which is a major concern given that many of these pipelines are repurposed from existing oil and gas infrastructure made of carbon steel.”
The rise in carbon capture facilities, particularly in hard-to-abate sectors like cement and steel production, underscores the critical need for reliable monitoring solutions.
According to industry projections shared by Thermo Fisher, the number of operational carbon capture plants is expected to grow from approximately 40 today to over 500 by 2030. As these facilities increase in number and diversity, so too does the complexity of the CO2 streams they handle.
Tilmann noted that the variability in impurities, depending on the source of the CO2 and the capture technique used, further complicates the monitoring process. “It’s really important that we monitor these impurities as they can have an effect on the overall integrity of the pipeline,” he said.
For instance, CO2 streams captured from combustion sources might contain oxides of nitrogen and sulphur species, while those from ammonia production could carry traces of ammonia and methane. Such impurities, if not adequately monitored, could lead to pipeline degradation or even failures.
To address these challenges, Thermo Fisher Scientific has developed the Max-Bev CO2 Purity Monitoring System, a solution originally designed for the beverage industry but now adapted for carbon capture applications. “The Max-Bev gets its name because it was originally designed for monitoring impurities in beverage-grade CO2,” Tilmann explained. “But it has since been applied to the carbon capture industry with great results.”
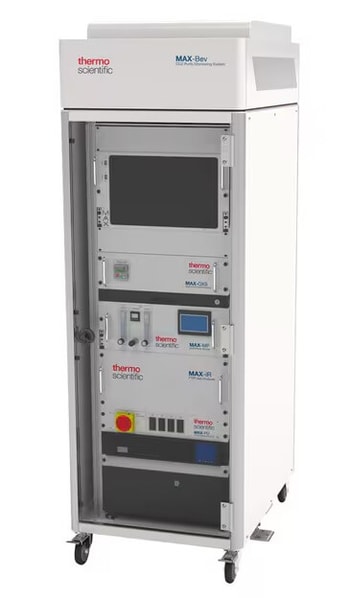
©Thermo Fisher Scientific. The Max-Bev CO2 Purity Monitoring System.
The Max-Bev system leverages FTIR technology to provide real-time measurements of CO2 purity and potential impurities, enabling operators to ensure the safe and efficient transport of captured carbon.
One of the key features of the system is its dynamic range, which allows it to measure compounds from the parts-per-billion level up to 99.99% CO2 concentration. According to Tillmann, this capability is particularly important given the varying impurity levels that can be present in different industrial settings.
The system’s ability to continuously monitor CO2 purity is also vital for companies seeking to qualify for government tax credits, which are often tied to the accurate measurement of sequestered CO2. “We offer a reliable solution with 99.7% uptime that is ready to install in less than 24 weeks,” Tilmann stated.
“As more industries adapt carbon capture and storage, the need for precise, reliable monitoring solutions will become ever more critical. Thermo Fisher is committed to supporting this transition with cutting-edge technology that not only meets but exceeds the rigorous demands of the carbon capture industry.”
The full webinar is available to watch ‘On demand’ at www.gasworld.tv
No comments:
Post a Comment