U.S. Navy's Manning Shortage is Hurting Underway Maintenance
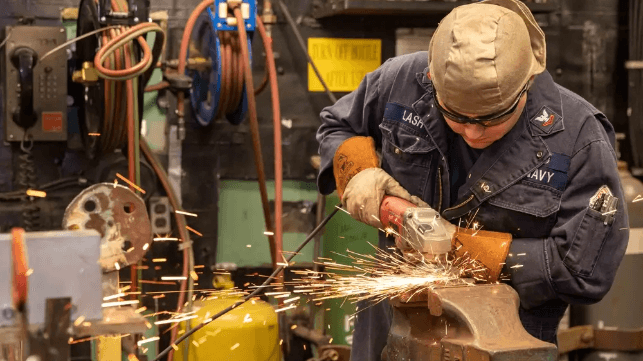
The U.S. Navy's growing manning gap is adding to its existing fleet maintenance issues, according to the Government Accountability Office. In a fleetwide survey, GAO found that most warship crews are having a hard time performing underway repairs and maintenance because they do not have enough people on board to do the work. As incomplete underway maintenance leads to more serious issues down the road, like increased rates of corrosion or mechanical wear, the challenges in getting the work done at sea are adding to the Navy's difficulty in completing timely repairs during drydock or pierside availabilities. Mission-limiting backlog counts rose measurably in 2023 rose from about 8,500 job items to about 9,000 job items, with most of the increase concentrated in the surface fleet.
The Navy is shorthanded by about 25,000 enlisted personnel, or about 10 percent short of target. GAO has previously reported that Navy crew sizes are too small, even by the Navy's own manning standards, and that crew reductions were increasing operational risk and impacting warships' material condition. Crew size was a factor in the two deadly destroyer collisions in 2017, and while the Navy vowed to make improvements after these devastating casualties, its recruiting shortfalls may make adequate manning more difficult than ever to achieve.
To gauge the service's ability to get work done at sea, GAO's inspectors visited 25 ships, interviewed 140 officers and petty officers, and surveyed the executive officers on 232 battle force ships across the fleet (including subs). 63 percent of the XOs consulted said that it was "moderately to extremely difficult" to complete repairs under way with the number of sailors that they had on board. Even sailors who are on board may not be available to help out with maintenance because their other duties and assignments prevent it - leaving more work for the others, particularly for senior personnel.
"More capable sailors that perform a lot of maintenance get burned out and tired of taking up the slack for other sailors and leave the Navy to do the same work for better pay and working conditions," one respondent told GAO in a survey.
Sailor training and skill level are also matters of serious concern. Two-thirds of XOs said that it is moderately or extremely difficult to get work done with sailors who underwent current classroom training, and another 75 percent said that sailors have a difficult time completing repairs. The numbers were significantly better for sailors who had completed practical on-the-job training led by experienced personnel.
U.S. Navy Gives Nonprofit $1B Contract for Sub Workforce Programs
The U.S. Navy is going all-in on its partnership with a recently-founded non-profit, the BlueForge Alliance, handing the organization a contract worth nearly $1 billion to strengthen worker recruitment and resourcing for the U.S. submarine industrial base. The gaps in the nuclear submarine workforce are among the Navy's biggest procurement concerns, as worker shortages at the two prime contractors and their suppliers are causing production delays for the Columbia-class ballistic missile subs and the Virginia-class attack subs.
BlueForge Alliance is based in College Station, Texas, and is best known for its BuildSubmarines.com advertising campaign. This initiative sponsors the RFK Racing NASCAR team, the Connecticut Sun WNBA team, the Cincinnati Reds Speedway Classic, and a variety of sports-related events. It also sponsors a growing roster of workforce nonprofits that bolster regional recruitment efforts for submarine manufacturing workers.
The scale of the challenge is daunting. The Navy's sub suppliers need to increase production fivefold in order to meet strategic needs, and the deadline for ramping up is just four years away. The Navy is on a tight timetable to build replacements for the aging Ohio-class ballistic missile subs, the most survivable element of the nation's nuclear triad, while also delivering more Virginia-class boats for export to Australia. This could take as many as 100,000 new civilian shipbuilders and subcontractors, according to the service.
"The Navy is on a generational journey to recapitalize its sea-based strategic deterrence and to guarantee a capable and enduring undersea presence," said Rear Admiral Scott Pappano, the head of the Navy's ballistic missile sub program, in a statement earlier this year. "Achieving that goal means strengthening supply chains to ensure America’s submarine industrial base has the capability, capacity, and skilled workforce to maintain our existing fleet and manufacture one Columbia and two Virginia class submarines per year."
The new sole-source contract with BlueForge is intended to address these needs. It provides $500 million in support for efforts to diversify the submarine supply chain, attract more workers, and improve retention. The program will also support R&D work to scale up and mature 3D printing and robotics technology for use in submarine construction, which is a technically demanding and precise type of shipbuilding.
If all options are exercised, the total contract award could rise to $980 million. Taken together with past awards, the Navy has given BlueForge contracts worth a total of $1.3 billion, roughly equal to the cost of one Constellation-class frigate.
No comments:
Post a Comment