SWITCH Maritime is set to launch the Sea Change, a hydrogen fuel cell-powered electric ferry in the San Francisco Bay. The zero-emission vessel is designed to accommodate around 75 passengers.
Skip Descant
GOVTECH
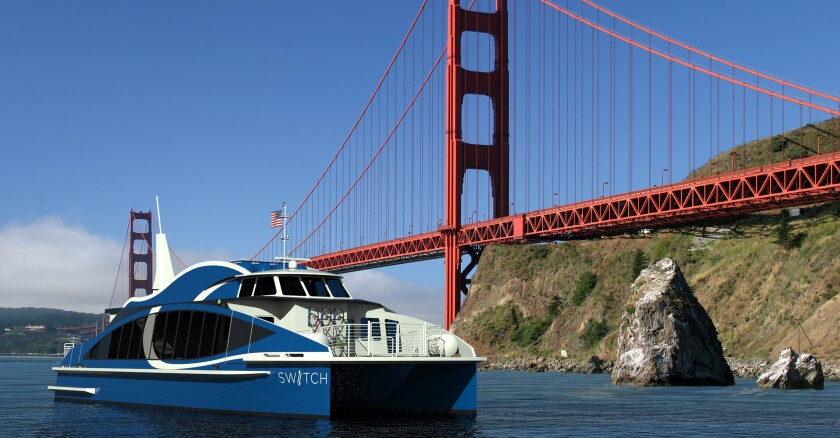
The “Sea Change” is a hydrogen fuel cell-powered electric ferry which will soon undergo testing and deployment in the California Bay Area.
Submitted Photo: SWITCH Maritime
The nation’s first hydrogen fuel cell electric ferry is set to launch in the California Bay Area. SWITCH Maritime will launch the Sea Change in the San Francisco Bay for its initial testing and data collection phase before launching the new vessel into full ferry service.
The 75-passenger ferry is nearing manufacturing completion at a ship facility in Washington state, and will launch in the San Francisco region in the fall. From there, the ferry will undergo a three-month data collection and testing phase where the boat will operate in a number of different service profiles to test the fuel cell system in different modes and applications. The project was awarded a $3 million grant by the California Air Resources Board (CARB).
“The objective of that is to make public this data, and for the state to understand a techno-economic analysis on the fuel cell system, and the viability of that to apply to other hovercraft and the like,” said Elias Van Sickle, director of commercial development and operations at SWITCH Maritime.
Hydrogen fuel cell vehicles are powered by an electric motor. The technology involves mixing hydrogen — the most common element in the universe — with oxygen to create electricity. The electrification of the transportation sector has evolved primarily in the direction of storing energy in batteries, as is the case with numerous models of electric cars on the market. However, hydrogen fuel cell technology has been identified as a better fit for large vehicles, like maritime vessels, transit buses or even airplanes.
“You’ll see more of hydrogen playing a role in those heavy-duty applications. Because they’re really hard to decarbonize, these big energy requirements,” said Van Sickle.
“This vessel is electric. It has an electric motor, and the only question is where do those electrons come from?” Van Sickle pointed out. “They can come from a battery. They can come from a fuel cell, or they can come from a combination of both.”
A shorter route, with lower energy requirements and suitable charging opportunities, tends to serve battery-electric power fairly well, he added. Longer routes requiring faster speeds and extensive operational duration tend to be better served by hydrogen fuel cells.
“This boat is relatively small, still. But when you scale up to much bigger ships, you really run into some limitations in how much energy you can fit onboard a boat to make it go the distance that it needs to,” said Van Sickle.
The goal is to also demonstrate that the technology “is modular and scalable, and can power some of the larger types of vessels as well,” he added.
The ferry will be fueled from a delivery truck. The company has plans to establish its own infrastructure and supply chains to support more vessels as the company grows the fleet.
Organizations like the Water Emergency Transportation Authority (WETA) in the Bay Area — an operator of the San Francisco Bay Ferry service — are already exploring projects to develop waterside hydrogen refueling, said Thomas Hall, public information and marketing manager at WETA.
“We are currently studying shoreside infrastructure needs for zero-emission ferries and working with the California Air Resources Board to accelerate a move from diesel to zero-emission technology on our vessels,” said Hall.
“WETA is excited to learn more about this application of hydrogen fuel cells in a maritime setting as we work toward moving our fleet toward zero emissions,” he added.
There are about 1,000 passenger ferries in operation in the U.S., most powered by diesel engines. SWITCH would like to see hydrogen fuel cell technology continue to develop for these applications, as an alternative for when older ferries are retired.
“They’re all aging assets,” Van Sickle said of the older ferries. “And we have this window of opportunity where, rather than replacing those aging assets with more diesel-powered ferries for the next 30 years of pollution, we really want to accelerate that energy transition, and really make those go over to zero-carbon options.”

Skip Descant
Skip Descant writes about smart cities, the Internet of Things, transportation and other areas. He spent more than 12 years reporting for daily newspapers in Mississippi, Arkansas, Louisiana and California. He lives in downtown Sacramento.
SEE MORE STORIES BY SKIP DESCANT