Fracking sand company sees its stock almost halve on big customer loss
John Kingston Tuesday, November 12, 2019

The oil patch has become so depressed that a company that supplies frac sand saw its stock drop almost in half Nov. 11, after it said it may not be able to continue as a “going concern.”
Carbo Ceramics (NYSE: CRR), a Houston-based manufacturer of proppants, the industry name for frac sand, said in its third-quarter earnings that its largest frac sand client “intends to discontinue purchase of frac sand under our current contract,” Carbo President and CEO Gary Kolstad said in a conference call with investors. The identity of the buyer was not revealed.
“We are in discussions with this client to determine if there’s an agreeable alternative to this matter,” Kolstad said, according to a transcript of the earnings call supplied by Seeking Alpha.
The problem for the company is not only the loss of the revenue stream from the client, Kolstad said. It is also that the contract with the buyer “covered significant fixed costs associated with our distribution facility and railcar leases.”
It was in the company’s press release about the earnings that the issue of Carbo remaining a “going concern” was raised. A “going concern” notice posted by a company’s auditor in its financial statements is one that is issued only for a company in fairly dire straits.
“Given the existing North American oilfield market headwinds, expectations for these headwinds to continue into 2020 and the loss of revenues associated with this sand contract, there is an elevated risk associated with the company meeting its existing financial forecast, and the company may ultimately conclude it is unable to continue as a going concern in a future period,” Carbo said in its earnings release.
In his closing remarks on the earnings call, Kolstad noted how tough the market has become for companies supplying frac sand. It’s a market that has seen the North American land rig count, according to Baker Hughes, drop to 793 in the most recent weekly report from 1,057 a year ago.
“The U.S. onshore oilfield market is very tough,” Kolstad said in what could be viewed as a warning to everyone in the frac sand supply chain. “A low-quality reservoir rock combined with low oil and gas commodity prices has resulted in little or no returns for the industry. And that means activity pricing and the use of technology products is likely lower.”
The cuts the company is implementing are not just coming from halting operations. They also involve reducing railcar and distribution facility leases and other stops in the proppant supply chain. “In particular, the cost of distribution assets, which includes rail car leases and distribution facility leases … we have to lower those,” Kolstad said.
The end result of the announcement was that the stock of Carbo dropped roughly 48% on Nov. 11 to 82 cents per share. It’s down almost 85% in the last 52 weeks.
In the call and in the company’s earnings release, Kolstad and Carbo said it would look at asset divestitures and overhead reductions — SG&A — of 20% in the coming year. Its loss for the quarter was $1.03 per share, down from a loss of 62 cents per share in the third quarter of 2018. More ominously, its balance sheet showed a drop in cash on hand to $39.8 million from $72.7 million a year earlier.
Oil and gas is not the company’s only business. On the same day it announced the loss of its customer and its earnings, it also said it had signed a new significant deal in the agriculture sector.
John Kingston
John has an almost 40-year career covering commodities, most of the time at S&P Global Platts. He created the Dated Brent benchmark, now the world’s most important crude oil marker. He was Director of Oil, Director of News, the editor in chief of Platts Oilgram News and the “talking head” for Platts on numerous media outlets, including CNBC, Fox Business and Canada’s BNN. He covered metals before joining Platts and then spent a year running Platts’ metals business as well. He was awarded the International Association of Energy Economics Award for Excellence in Written Journalism in 2015. In 2010, he won two Corporate Achievement Awards from McGraw-Hill, an extremely rare accomplishment, one for steering coverage of the BP Deepwater Horizon disaster and the other for the launch of a public affairs television show, Platts Energy Week.
Sand deposit could be 'game-changer' for North Dakota oil
Oct 13, 2019
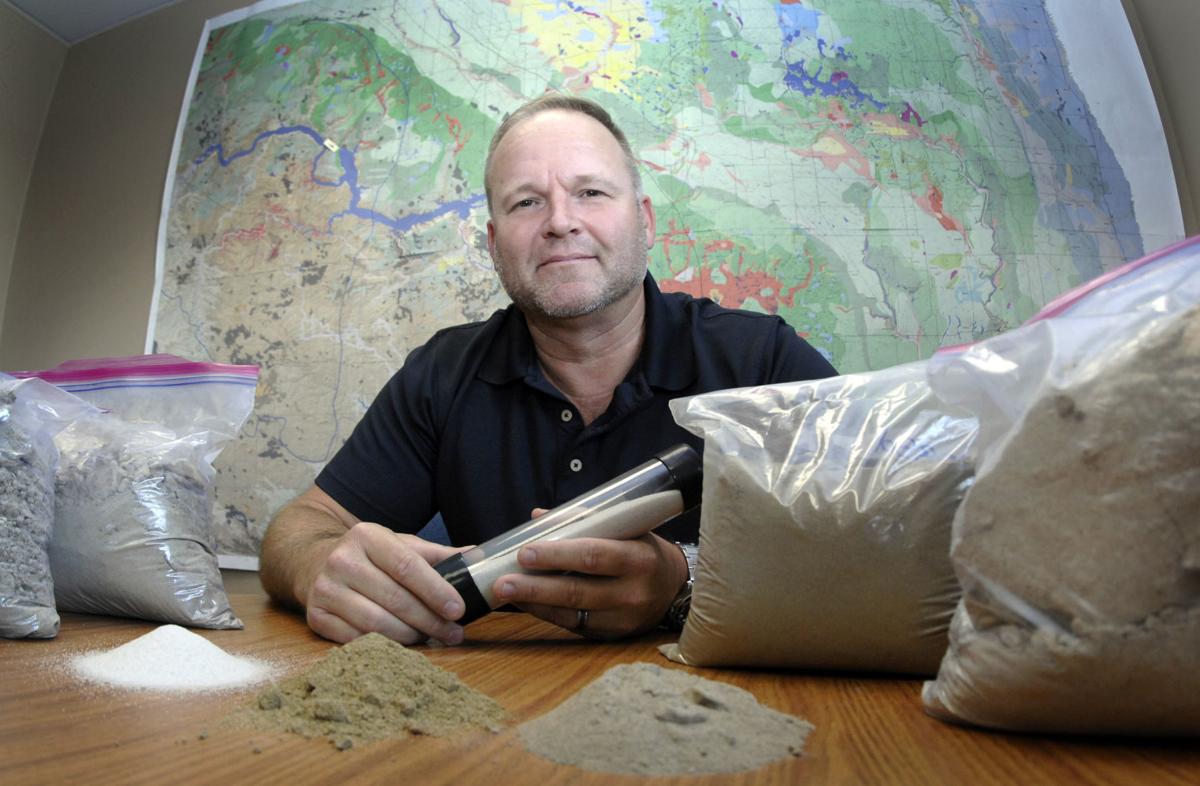
Fred Anderson, a geologist with the North Dakota Geological Survey in
Oil and gas is not the company’s only business. On the same day it announced the loss of its customer and its earnings, it also said it had signed a new significant deal in the agriculture sector.
John Kingston
John has an almost 40-year career covering commodities, most of the time at S&P Global Platts. He created the Dated Brent benchmark, now the world’s most important crude oil marker. He was Director of Oil, Director of News, the editor in chief of Platts Oilgram News and the “talking head” for Platts on numerous media outlets, including CNBC, Fox Business and Canada’s BNN. He covered metals before joining Platts and then spent a year running Platts’ metals business as well. He was awarded the International Association of Energy Economics Award for Excellence in Written Journalism in 2015. In 2010, he won two Corporate Achievement Awards from McGraw-Hill, an extremely rare accomplishment, one for steering coverage of the BP Deepwater Horizon disaster and the other for the launch of a public affairs television show, Platts Energy Week.
Sand deposit could be 'game-changer' for North Dakota oil
Oct 13, 2019
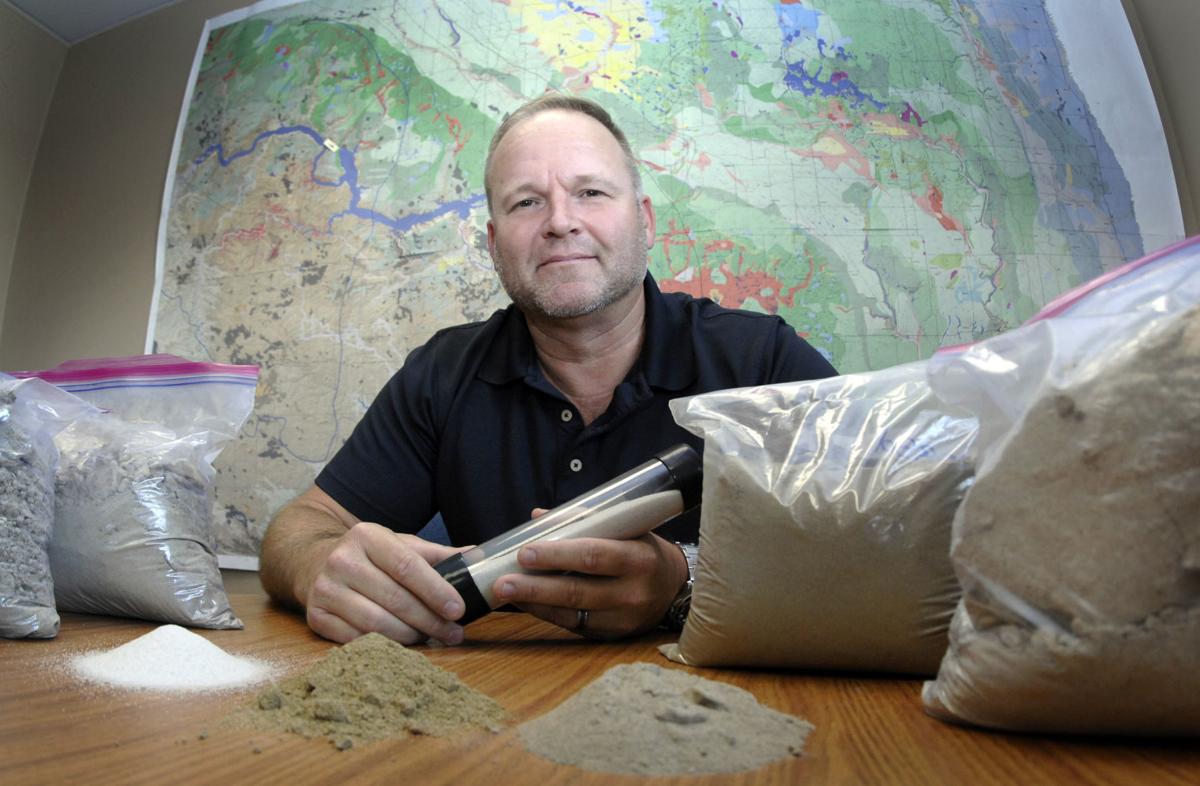
Fred Anderson, a geologist with the North Dakota Geological Survey in
Bismarck, shows samples of sand extracted from soil in the state used
to research and locate the appropriate type of sand used for fracking
in the oil industry. Mike McCleary
WILLISTON — A deposit of sand in north-central North Dakota could be a boon to the state's oil industry.
The sand — a variety specifically needed in the process of hydraulic fracturing — has been found in McHenry County, roughly 160 miles west of Grand Forks between the towns of Rugby and Minot. Another has been found in Mercer County, northwest of Bismarck.
Fred Anderson, a North Dakota Geological Survey geologist, said the sand could be a "game-changer" for the state
“The reduction in cost would be high,” Anderson said. “It’s a huge deal for the state of North Dakota."
Asgard Resources, of Williston, has received a permit to dig sand in McHenry County, the auditor’s office there confirmed. Asgard Resources also applied for a permit to excavate sand in Mercer County, the Mercer County auditor’s office said.
“We know it’s being developed and shipped, but we don’t know where it’s going,” Anderson said.
Hydraulic fracturing, commonly called “fracking,” is an oil extraction method that injects water, sand and chemicals into underground formations. Sand, or “proppant,” is used to hold open the fracture in the rock so oil and gas can flow from the rock formation into the wellbore. Fracking is the process that prompted the Bakken oil boom in western North Dakota, but the sand required for the process is unique and typically found elsewhere.
The North Dakota Geological Survey began researching whether North Dakota sand could be used for fracking about 10 years ago, and learned it was marginal, Anderson said. The North Dakota “windblown,” or quartz, sand contains minerals, so it typically is not the proppant sand preferred for fracking.
If oil companies can use North Dakota sand for fracking, it will mean they no longer must haul it in from other places, Anderson said. The change could boost the margin for the companies in western North Dakota.
Bakken completions can require about 4,000 to 5,000 tons of sand per well, the North Dakota Department of Mineral Resources said. The sand can cost as much as $34 per ton, Anderson said.
Spencer Stone, vice president of business development for a company called TracFrac Inc., said Friday that a more regional-sourced supply of sand could mean substantial savings for wells in the Bakken region of North Dakota.
“Sand mined in North Dakota could reduce costs for new Bakken wells by $150,000 to $300,000,” Stone said. “It levels the footing between Bakken operators and its Permian counterparts, who are able to utilize sand mined in Texas.”
Generally, oil companies want to use sand for fracking that has crush-resistant values up to 8,000 to 9,000 pounds per square inch, Anderson said. Results of laboratory tests conducted on McHenry County sand show lower crush-resistant values.
“What we’ve seen is our sands are coming in from five to seven,” Anderson said.
That sand can be processed to make it more crush resistant, but that increases its cost, Anderson said.
“Most people want to dig it out of the ground, wash it and get it to the well site,” he said.
While the McHenry County sand has lower crush resistance than is optimal, sampling and testing work by the North Dakota Geological Survey, in conjunction with EOG Resources, showed that deposits of wind-blown sand in the Hazen-Stanton area of Mercer County may be viable sources of proppant sand. The dunes in that area cover about 34 square miles, the study said.
WILLISTON — A deposit of sand in north-central North Dakota could be a boon to the state's oil industry.
The sand — a variety specifically needed in the process of hydraulic fracturing — has been found in McHenry County, roughly 160 miles west of Grand Forks between the towns of Rugby and Minot. Another has been found in Mercer County, northwest of Bismarck.
Fred Anderson, a North Dakota Geological Survey geologist, said the sand could be a "game-changer" for the state
“The reduction in cost would be high,” Anderson said. “It’s a huge deal for the state of North Dakota."
Asgard Resources, of Williston, has received a permit to dig sand in McHenry County, the auditor’s office there confirmed. Asgard Resources also applied for a permit to excavate sand in Mercer County, the Mercer County auditor’s office said.
“We know it’s being developed and shipped, but we don’t know where it’s going,” Anderson said.
Hydraulic fracturing, commonly called “fracking,” is an oil extraction method that injects water, sand and chemicals into underground formations. Sand, or “proppant,” is used to hold open the fracture in the rock so oil and gas can flow from the rock formation into the wellbore. Fracking is the process that prompted the Bakken oil boom in western North Dakota, but the sand required for the process is unique and typically found elsewhere.
The North Dakota Geological Survey began researching whether North Dakota sand could be used for fracking about 10 years ago, and learned it was marginal, Anderson said. The North Dakota “windblown,” or quartz, sand contains minerals, so it typically is not the proppant sand preferred for fracking.
If oil companies can use North Dakota sand for fracking, it will mean they no longer must haul it in from other places, Anderson said. The change could boost the margin for the companies in western North Dakota.
Bakken completions can require about 4,000 to 5,000 tons of sand per well, the North Dakota Department of Mineral Resources said. The sand can cost as much as $34 per ton, Anderson said.
Spencer Stone, vice president of business development for a company called TracFrac Inc., said Friday that a more regional-sourced supply of sand could mean substantial savings for wells in the Bakken region of North Dakota.
“Sand mined in North Dakota could reduce costs for new Bakken wells by $150,000 to $300,000,” Stone said. “It levels the footing between Bakken operators and its Permian counterparts, who are able to utilize sand mined in Texas.”
Generally, oil companies want to use sand for fracking that has crush-resistant values up to 8,000 to 9,000 pounds per square inch, Anderson said. Results of laboratory tests conducted on McHenry County sand show lower crush-resistant values.
“What we’ve seen is our sands are coming in from five to seven,” Anderson said.
That sand can be processed to make it more crush resistant, but that increases its cost, Anderson said.
“Most people want to dig it out of the ground, wash it and get it to the well site,” he said.
While the McHenry County sand has lower crush resistance than is optimal, sampling and testing work by the North Dakota Geological Survey, in conjunction with EOG Resources, showed that deposits of wind-blown sand in the Hazen-Stanton area of Mercer County may be viable sources of proppant sand. The dunes in that area cover about 34 square miles, the study said.
Sand deposit could be 'game-changer' for ND oil industry
Finding the sand in North Dakota could mean a savings of $150,000 to $300,000 per new Bakken well.

A deposit of sand in north-central North Dakota could be a boon to the state's oil industry.
The sand – a variety specifically needed in the process of hydraulic fracturing – has been found in McHenry County, roughly 160 miles west of Grand Forks between the towns of Rugby and Minot. Another has been found in Mercer County, northwest of Bismarck.
Fred Anderson, a North Dakota Geological Survey geologist, said the sand could be a "game-changer" for the state.
“The reduction in cost would be high,” Anderson said. “It’s a huge deal for the state of North Dakota."
Asgard Resources, of Williston, has received a permit to dig sand in McHenry County, the auditor’s office there confirmed to the Grand Forks Herald. Asgard Resources also applied for a permit to excavate sand in Mercer County, the Mercer County auditor’s office said.
“We know it’s being developed and shipped, but we don’t know where it’s going,” Anderson said.
Hydraulic fracturing, commonly called “fracking,” is an oil extraction method that injects water, sand and chemicals into underground formations. Sand, or “proppant,” is used to hold open the fracture in the rock so oil and gas can flow from the rock formation into the wellbore. Fracking is the process that prompted the Bakken oil boom in western North Dakota, but the sand required for the process is unique and typically found elsewhere.
The North Dakota Geological Survey began researching whether North Dakota sand could be used for fracking about 10 years ago, and learned it was marginal, Anderson said. The North Dakota “windblown,” or quartz, sand contains minerals, so it typically is not the proppant sand preferred for fracking.
If oil companies can use North Dakota sand for fracking, it will mean they no longer must haul it in from other places, such as Minnesota and Wisconsin, Anderson said. The change could boost the margin for the companies in western North Dakota.
Bakken completions can require about 4,000 to 5,000 tons of sand per well, the North Dakota Department of Mineral Resources said. The sand can cost as much as $34 per ton, Anderson said.
Spencer Stone, vice president of business development for a company called TracFrac Inc., told the Herald Friday that a more regional-sourced supply of sand could mean substantial savings for wells in the Bakken region of North Dakota.
“Sand mined in North Dakota could reduce costs for new Bakken wells by $150,000 to $300,000,” Stone said. “It levels the footing between Bakken operators and its Permian counterparts, who are able to utilize sand mined in Texas.”
Generally, oil companies want to use sand for fracking that has crush-resistant values up to 8,000 to 9,000 pounds per square inch, Anderson said. Results of laboratory tests conducted on McHenry County sand show lower crush-resistant values.
“What we’ve seen is our sands are coming in from five to seven,” Anderson said.
That sand can be processed to make it more crush resistant, but that increases its cost, Anderson said.
“Most people want to dig it out of the ground, wash it and get it to the well site,” he said.
While the McHenry County sand has lower crush resistance than is optimal, sampling and testing work by the North Dakota Geological Survey, in conjunction with EOG Resources, showed that deposits of wind-blown sand in the Hazen-Stanton area of Mercer County may be viable sources of proppant sand. The dunes in that area cover about 34 square miles, the study results said.
Frac Sand Prices Forecast to Remain Flat Through 2024
Although demand for frac sand is expected to increase in the U.S. hydraulic fracturing market through 2024, prices for Northern White and Permian proppant sand are forecast to remain more or less flat over the next five years, according to a new report released this month by Rystad Energy.
The energy research and business intelligence company’s latest Proppant Market Report posits that prices for Northern White sand will bounce between $20/ton to $25/ton from 2019 to 2024. Prices for in-basin Permian sand from West Texas are projected to range from $19/ton to $23/ton during the same period.
In 2018, one ton of Northern White sand sold for $34, while one ton of Permian sand went for $35. The report’s authors note that frac sand prices “have been under pressure for some time thanks to oversupply in the market.”

Rystad Energy predicts that frac sand supply in the U.S. will grow by 10% this year and then dip by 2% in 2020 as operators shift away from Northern White sand. On the other hand, demand for the material is forecast to experience an uptick of 10% in 2019 and 17% in 2020. By 2024, supply is estimated to reach 239 million tons and demand is projected to hit 181 million tons.
“Adoption rates for in-basin sand in Eagle Ford will determine the future of Northern White sand. Lower quality, in-basin sand found in Eagle Ford may not be widely adopted due to higher downhole pressures found in that basin,” said Rystad Energy Senior Analyst Thomas Jacob in a statement.

A major takeaway from the report is that researchers expect industry to pivot away from use of Northern White sand in their operations in the coming years. Rystad Energy forecasts that Permian sand demand will grow from 55 million tons in 2019 to 85 million tons by 2024. The authors also opine that 35% to 40% of the supply of Northern White sand will come off the market by next year. The Eagle Ford Basin in south Texas is described in the report as a “key market to watch” in the proppant sand industry.
“In-basin sand mines in Eagle Ford have struggled to reach desired utilization levels in recent months, but we expect this issue to be solved in the near term,” Jacob said.
For more news headlines, articles, and equipment reviews, visit our Equipment Zones
Dec 11, 2019 - Just last month, CARBO Ceramics Inc. CRR, a seller of frac sand, raised doubt about its ability to continue as a going concern. Currently trading ...
Oct 30, 2019 - Shale slump: Lower hydraulic fracturing activity stings frac sand ... More: Read the latest oil and gas news from HoustonChronicle.com.
Sep 20, 2019 - One industry veteran provides his view on the evolving frac sand market and offers a look at what's coming down the pike.
Sep 9, 2019 - GlobalFrac Sand Market2019report provides key statistics on the market status of the Frac Sand Manufacturers and is a valuable source of ...
Frac Sand Producer In Wisconsin Faces Bankruptcy As ...
https://www.wpr.org › frac-sand-producer-wisconsin-faces-bankruptcy-ind...
May 13, 2019 - A major frac sand producer in Wisconsin is facing bankruptcy while a ... News of the restructuring agreement hit Emerge Energy stocks hard on ...
Mar 18, 2019 - The U.S. frac sand market has been turned on its head. Over the past three years, demand for the sand used in hydraulic fracturing has more ...
DAILY REPORTER MILWAUKEE WI.
DNR investigating western Wisconsin spill at frac-sand mine
The state Department of Natural Resources is investigating a spill at a Jackson County frac-sand mine.
Frac-sand producer files for bankruptcy, says it owes Wisconsin contractors $13M
The frac-sand company Emerge Energy Services says it owes at least $13 million to Wisconsin contractors in a bankruptcy case filed this week, on the heels of falling demand for the company's products.
Wisconsin frac-sand mines sit dormant as competition grows
Wisconsin's frac-sand industry is grappling with several idled mines amid increased competition from companies in Texas and Oklahoma.
Tagged with: FRAC SAND MINING
Wisconsin landowners sue frac-sand mines over health effects
Forty landowners in western Wisconsin are suing two frac-sand mines that they say are inundating their homes with dust, polluting their wells with sediment and driving down property values.
Tagged with: FRAC SAND MINING
DNR Secretary refuses to reinstate permit for sand plant
The state Department of Natural Resources' secretary has decided not to reinstate a permit for a $75 million sand-processing plant in Monroe County.
Wisconsin Supreme Court rejects annexation of sand mine
The state Supreme Court has rejected the city of Whitehall's attempt to annex land for a sand mine.
Tagged with: FRAC SAND MINING
Wisconsin frac sand under pressure from rival products
Competing with lower-cost mines in Texas, the frac-sand-mining company Hi-Crush recently announced it would be idling part of its plant on Highway Q in Whitehall.
Tagged with: FRAC SAND MINING FRACKING
State won’t cite mine for wastewater release
A frack sand mine won't be cited for releasing an estimated 10 million gallons of wastewater in order to rescue a worker trapped in a holding pond in western Wisconsin.
Hi-Crush to pause plant production at Whitehall frac-sand mine
Hi-Crush Partners, which operates one of the largest frac-sand mines in Wisconsin, has paused production at a plant in Whitehall, citing weak demand for its product.