by University of Bayreuth
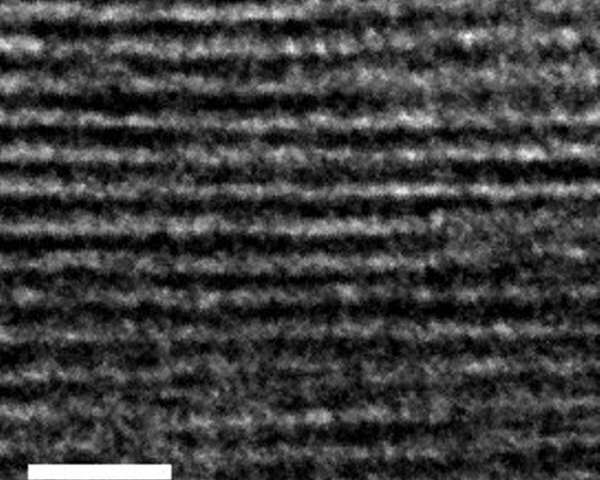
Electron microscopic cross-sectional image of the new hybrid material. It was possible to produce the glass platelets very precisely and, interrupted by spacers, to layer them on top of each other. Credit: Martin Rieß
Chemists at the University of Bayreuth have developed a material that could well make an important contribution to climate protection and sustainable industrial production. With this material, the greenhouse gas carbon dioxide (CO₂) can be specifically separated from industrial waste gases, natural gas, or biogas, and thereby made available for recycling. The separation process is both energy efficient and cost-effective. In the journal Cell Reports Physical Science the researchers present the structure and function of the material.
The Green Deal presented by the European Commission in 2019 calls for the net emissions of greenhouse gases within the EU to be reduced to zero by 2050. This requires innovative processes that can separate and retain CO2from waste gases and other gas mixtures so that it is not released into the atmosphere. The material developed in Bayreuth has one fundamental advantage over previous separation processes: It is capable of completely removing CO2from gas mixtures without chemically binding CO2.
These gas mixtures can be waste gases from industrial plants, but also natural gas or biogas. In all these cases, CO2accumulates in the cavities of the material solely due to physical interaction. From there, it can be released without great expenditure of energy, to be made available again as a resource for industrial production. Hence, the separation process works, chemically speaking, according to the principle of physical adsorption. Like a spacious storage tank, the new material can be filled with and emptied of carbon dioxide in an energy-efficient way. In Bayreuth laboratories, it was designed in such a way as to only separate out CO2and no other gas from the most varied gas mixtures.
"Our research team has succeeded in designing a material that fulfils two tasks at the same time. On the one hand, the physical interactions with CO2are strong enough to free and retain this greenhouse gas from a gas mixture. On the other hand, however, they are weak enough to allow the release of CO2from the material with only a small amount of energy," says Martin Rieß M.Sc., first author of the new publication and doctoral researcher at the Inorganic Chemistry I research group at the University of Bayreuth.
The new material is an inorganic-organic hybrid. The chemical basis is clay minerals consisting of hundreds of individual glass platelets. These are only one nanometre thick each, and arranged precisely one above the other. Between the individual glass plates there are organic molecules that act as spacers. Their shape and chemical properties have been selected so that the pore spaces created are optimally tailored to accumulate CO2. Only carbon dioxide molecules can penetrate into the pore system of the material and be retained there. In contrast, methane, nitrogen, and other exhaust gas components must remain outside due to the size of their molecules. The researchers have used the so-called molecular sieve effect to increase the material's selectivity for CO2. They are currently working on the development of a membrane system based on clay minerals, designed to allow the continuous, selective, and energy-efficient separation of CO2 from gas mixtures.
The development of a hybrid material tailor-made for the separation and supply of CO2was made possible thanks to a special measuring system set up in the Bayreuth laboratories which allows the precise determination of quantities of adsorbed gases and of the selectivity of the adsorbing material. This has enabled industrial processes to be reproduced realistically. "All criteria relevant to the evaluation of industrial CO2separation processes have been completely fulfilled by our hybrid material. It can be produced cost-effectively, and stands to make an important contribution to reducing industrial carbon dioxide emissions, but also to the processing of biogas and acidic natural gas," says Rieß.
A controllable membrane to pull carbon dioxide out of exhaust streams
More information: Martin Rieß et al. Diammonium-Pillared MOPS with Dynamic CO2 Selectivity, Cell Reports Physical Science (2020). DOI: 10.1016/j.xcrp.2020.100210
A controllable membrane to pull carbon dioxide out of exhaust streams
by David L. Chandler, Massachusetts Institute of Technology
Chemists at the University of Bayreuth have developed a material that could well make an important contribution to climate protection and sustainable industrial production. With this material, the greenhouse gas carbon dioxide (CO₂) can be specifically separated from industrial waste gases, natural gas, or biogas, and thereby made available for recycling. The separation process is both energy efficient and cost-effective. In the journal Cell Reports Physical Science the researchers present the structure and function of the material.
The Green Deal presented by the European Commission in 2019 calls for the net emissions of greenhouse gases within the EU to be reduced to zero by 2050. This requires innovative processes that can separate and retain CO2from waste gases and other gas mixtures so that it is not released into the atmosphere. The material developed in Bayreuth has one fundamental advantage over previous separation processes: It is capable of completely removing CO2from gas mixtures without chemically binding CO2.
These gas mixtures can be waste gases from industrial plants, but also natural gas or biogas. In all these cases, CO2accumulates in the cavities of the material solely due to physical interaction. From there, it can be released without great expenditure of energy, to be made available again as a resource for industrial production. Hence, the separation process works, chemically speaking, according to the principle of physical adsorption. Like a spacious storage tank, the new material can be filled with and emptied of carbon dioxide in an energy-efficient way. In Bayreuth laboratories, it was designed in such a way as to only separate out CO2and no other gas from the most varied gas mixtures.
"Our research team has succeeded in designing a material that fulfils two tasks at the same time. On the one hand, the physical interactions with CO2are strong enough to free and retain this greenhouse gas from a gas mixture. On the other hand, however, they are weak enough to allow the release of CO2from the material with only a small amount of energy," says Martin Rieß M.Sc., first author of the new publication and doctoral researcher at the Inorganic Chemistry I research group at the University of Bayreuth.
The new material is an inorganic-organic hybrid. The chemical basis is clay minerals consisting of hundreds of individual glass platelets. These are only one nanometre thick each, and arranged precisely one above the other. Between the individual glass plates there are organic molecules that act as spacers. Their shape and chemical properties have been selected so that the pore spaces created are optimally tailored to accumulate CO2. Only carbon dioxide molecules can penetrate into the pore system of the material and be retained there. In contrast, methane, nitrogen, and other exhaust gas components must remain outside due to the size of their molecules. The researchers have used the so-called molecular sieve effect to increase the material's selectivity for CO2. They are currently working on the development of a membrane system based on clay minerals, designed to allow the continuous, selective, and energy-efficient separation of CO2 from gas mixtures.
The development of a hybrid material tailor-made for the separation and supply of CO2was made possible thanks to a special measuring system set up in the Bayreuth laboratories which allows the precise determination of quantities of adsorbed gases and of the selectivity of the adsorbing material. This has enabled industrial processes to be reproduced realistically. "All criteria relevant to the evaluation of industrial CO2separation processes have been completely fulfilled by our hybrid material. It can be produced cost-effectively, and stands to make an important contribution to reducing industrial carbon dioxide emissions, but also to the processing of biogas and acidic natural gas," says Rieß.
A controllable membrane to pull carbon dioxide out of exhaust streams
More information: Martin Rieß et al. Diammonium-Pillared MOPS with Dynamic CO2 Selectivity, Cell Reports Physical Science (2020). DOI: 10.1016/j.xcrp.2020.100210
A controllable membrane to pull carbon dioxide out of exhaust streams
by David L. Chandler, Massachusetts Institute of Technology
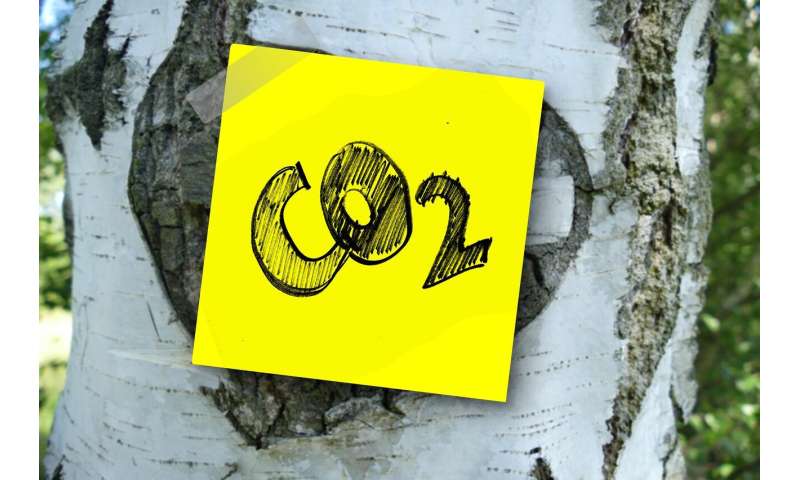
Credit: CC0 Public Domain
A new system developed by chemical engineers at MIT could provide a way of continuously removing carbon dioxide from a stream of waste gases, or even from the air. The key component is an electrochemically assisted membrane whose permeability to gas can be switched on and off at will, using no moving parts and relatively little energy.
The membranes themselves, made of anodized aluminum oxide, have a honeycomb-like structure made up of hexagonal openings that allow gas molecules to flow in and out when in the open state. However, gas passage can be blocked when a thin layer of metal is electrically deposited to cover the pores of the membrane. The work is described in the journal Science Advances, in a paper by Professor T. Alan Hatton, postdoc Yayuan Liu, and four others.
This new "gas gating" mechanism could be applied to the continuous removal of carbon dioxide from a range of industrial exhaust streams and from ambient air, the team says. They have built a proof-of-concept device to show this process in action.
The device uses a redox-active carbon-absorbing material, sandwiched between two switchable gas gating membranes. The sorbent and the gating membranes are in close contact with each other and are immersed in an organic electrolyte to provide a medium for zinc ions to shuttle back and forth. These two gating membranes can be opened or closed electrically by switching the polarity of a voltage between them, causing ions of zinc to shuttle from one side to the other. The ions simultaneously block one side, by forming a metallic film over it, while opening the other, by dissolving its film away.
When the sorbent layer is open to the side where the waste gases are flowing by, the material readily soaks up carbon dioxide until it reaches its capacity. The voltage can then be switched to block off the feed side and open up the other side, where a concentrated stream of nearly pure carbon dioxide is released.
By building a system with alternating sections of membrane that operate in opposite phases, the system would allow for continuous operation in a setting such as an industrial scrubber. At any one time, half of the sections would be absorbing the gas while the other half would be releasing it.
"That means that you have a feed stream coming into the system at one end and the product stream leaving from the other in an ostensibly continuous operation," Hatton says. "This approach avoids many process issues" that would be involved in a traditional multicolumn system, in which adsorption beds alternately need to be shut down, purged, and then regenerated, before being exposed again to the feed gas to begin the next adsorption cycle. In the new system, the purging steps are not required, and the steps all occur cleanly within the unit itself.
The researchers' key innovation was using electroplating as a way to open and close the pores in a material. Along the way the team had tried a variety of other approaches to reversibly close pores in a membrane material, such as using tiny magnetic spheres that could be positioned to block funnel-shaped openings, but these other methods didn't prove to be efficient enough. Metal thin films can be particularly effective as gas barriers, and the ultrathin layer used in the new system requires a minimal amount of the zinc material, which is abundant and inexpensive.
"It makes a very uniform coating layer with a minimum amount of materials," Liu says. One significant advantage of the electroplating method is that once the condition is changed, whether in the open or closed position, it requires no energy input to maintain that state. Energy is only required to switch back again.
Potentially, such a system could make an important contribution toward limiting emissions of greenhouse gases into the atmosphere, and even direct-air capture of carbon dioxide that has already been emitted.
While the team's initial focus was on the challenge of separating carbon dioxide from a stream of gases, the system could actually be adapted to a wide variety of chemical separation and purification processes, Hatton says.
"We're pretty excited about the gating mechanism. I think we can use it in a variety of applications, in different configurations," he says. "Maybe in microfluidic devices, or maybe we could use it to control the gas composition for a chemical reaction. There are many different possibilities."
Lego-like assembly of zeolitic membranes improves carbon capture
More information: Electrochemically mediated gating membrane with dynamically controllable gas transport, Science Advances (2020). advances.sciencemag.org/lookup … .1126/sciadv.abc1741
Journal information: Science Advances
Provided by Massachusetts Institute of Technology
This story is republished courtesy of MIT News (web.mit.edu/newsoffice/), a popular site that covers news about MIT research, innovation and teaching.