Boasting a sea port, an ore mine and lots of renewable energy, northern Sweden is an ideal location for producing hydrogen-powered steel. But there's no lack of challenges to tackle.

The mining town of Kiruna in northern Sweden has big plans
Lulea in northern Sweden is only about 100 kilometers (62 miles) away from the Arctic Circle. It has some 80,000 inhabitants, almost one-third of all people living in Norrbotten province.
In winter, you need icebreakers to access the port of Lulea. It's the second-biggest port on Sweden's eastern coast after Stockholm.
The port of Lulea predominantly handles coal, steel and ore iron. It's located on one end of the Scandinavian ore railroad track, with Narvik in Norway being on the on the opposite end. In between there's Lapland with its mining town Kiruna and an eponymous mine that is considered to be the world's most productive ore mine. In Lulea, steel is produced from Kiruna ore with the help of coal coming from across the Baltic Sea.
Steelmaking reinvented
But this way of making steel will soon come to an end as Sweden's steel industry aims to emulate national power utilities that have done completely without coal for almost a year now.
CO2 emissions from steelmaking will have to be reduced drastically in Sweden and elsewhere if the world wants to meet its emissions targets. Crude steel production accounted for 5.4% of global greenhouse gas emissions in 2018. According to the International Energy Agency (IEA), some 75% of all energy consumed in the process was generated from using coal.
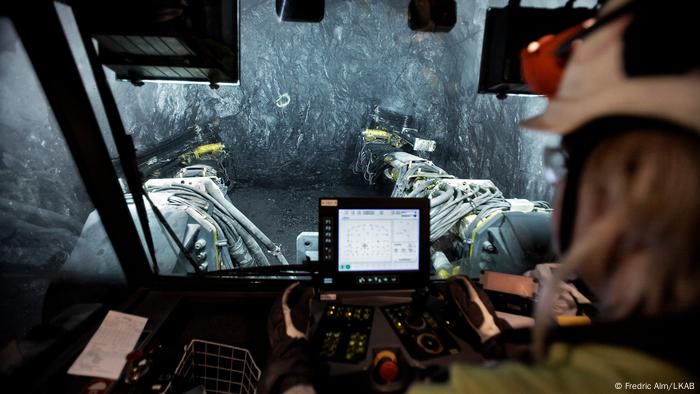
According to mining company LKAB, Kiruna mines enough iron ore for six Eiffel towers per day
Water vapor instead of carbon dioxide?
But as in cement production, emissions from steelmaking cannot simply be reduced by using electricity from renewables. This is because carbon from coal binds oxygen which is necessary to make crude steel and later steel from iron ore. Carbon and oxygen together result in carbon dioxide.
Steelworkers have begun to develop new techniques enabling them to free the oxygen from iron ore with the help of hydrogen instead of carbon. This way you get water vapor as a waste gas, rather than carbon dioxide.
A number of companies are currently testing such techniques, including Thyssenkrupp and Salzgitter from Germany. Lulea in Sweden, however, is willing to take the lead in producing steel with the help of hydrogen.
Swedish pioneers and German partners
Sweden's SSAB is among the technology leaders in this field. Together with iron ore producer LKAB from Kiruna and power utility Vattenfall, SSAB launched the HYBRIT project in its Lulea plant. In September of last year, a test facility went operational there that started making steel without using coal.
Stockholm-based Vargas Holding, which is behind battery producer Northvolt, is also willing to make CO2-free steel in the region. The resulting consortium, H2 Green Steel, involves Swedish utility vehicle manufacturer Scania as well as German-based steelmaker Bilstein and plant manufacturer SMS Group, also from Germany.
First major project of its kind globally
H2 Green Steel wants to build the first global mass production plant for emissions-free steel. An entire production facility including a hydrogen production unit is to emerge in the town of Boden.
By 2026, the plant is to produce 2.5 million tons of hydrogen-powered steel annually, and 5 million tons from 2030. To put those figures in perspective: Germany makes some 40 million tons of steel per year.
The Boden plant is to produce hydrogen from water for which H2 Green Steel wants to build an 800-megawatt electrolyzer on the ground.
Large quantities of green electricity needed
The 800 megawatt mentioned above would currently be 2% of Sweden's total annual electricity consumption. On top of that, you need energy for the steelmaking process itself. During a recent online presentation of the project, H2 Chief Project Officer Maria Persson Gulda said that energy efficiency was key.
But the need to heat up the steel to over 1,000 degrees Centigrade (1832 degrees Fahrenheit) will require enormous amounts of energy no matter what. Part of the waste heat will be fed into the regional heating grid. The question remains where the required green electricity will come from. Without it, hydrogen-powered steelmaking would not be emissions-free.
Northern Sweden an ideal location?
Choosing the right location for such a project is crucial. In Norrbotten province alone, Vattenfall operates 15 hydroelectric power plants. Some 100 kilometers to the south, a group of companies is building the Markbydgen windfarm, which is to become Europe's largest onshore windfarm.
Together, both sources of energy would be in a position to come up with 25 terawatt-hours of renewable energy, almost one-fifth of Sweden's current total energy generation.
But there is even more going for Lulea and Boden. "The region really is Sweden's mining and metalworking mecca," H2 supervisory board member Harald Mix said during the online presentation, adding that this also meant being able to draw on the big expertise of employees.
This article was adapted from German.
Choosing the right location for such a project is crucial. In Norrbotten province alone, Vattenfall operates 15 hydroelectric power plants. Some 100 kilometers to the south, a group of companies is building the Markbydgen windfarm, which is to become Europe's largest onshore windfarm.
Together, both sources of energy would be in a position to come up with 25 terawatt-hours of renewable energy, almost one-fifth of Sweden's current total energy generation.
But there is even more going for Lulea and Boden. "The region really is Sweden's mining and metalworking mecca," H2 supervisory board member Harald Mix said during the online presentation, adding that this also meant being able to draw on the big expertise of employees.
This article was adapted from German.
How hydrogen could change the face of steel production as we know it
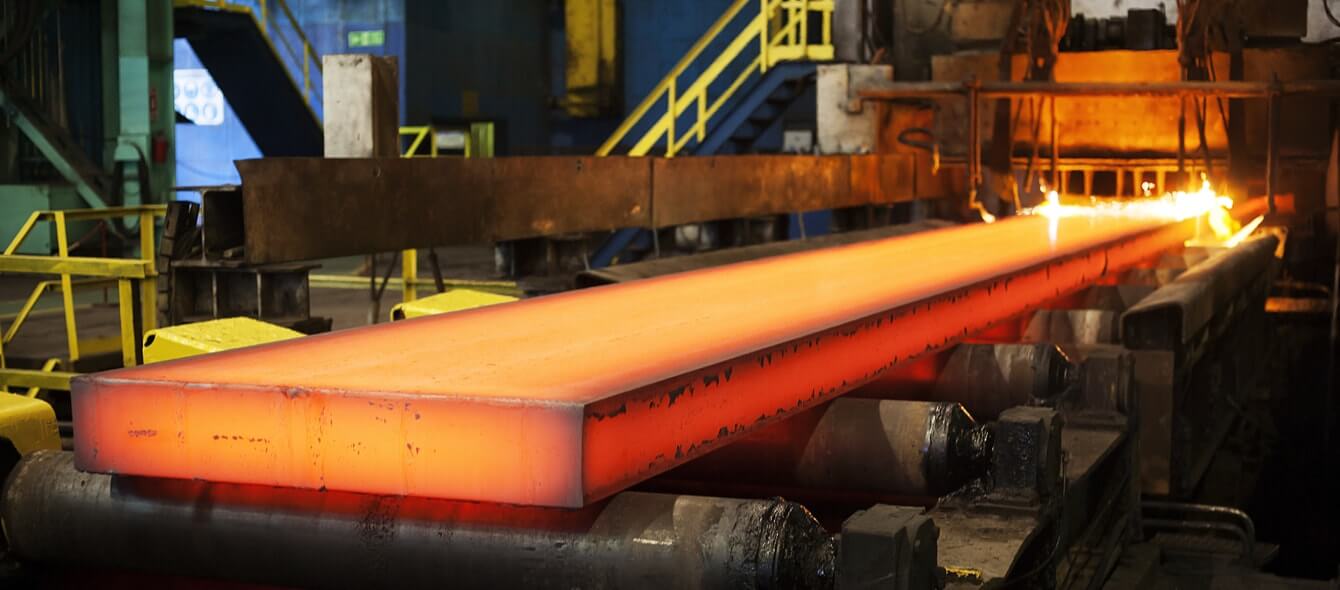
2019-05-29
In order to reduce its emissions, the steel industry needs technical innovation.
The EU is taking climate protection very seriously. Both increasingly stricter environment and climate protection regulations and rising costs through emissions trading are turning up the heat for the industry. By 2030, greenhouse gas emissions in the European Union are to be reduced by at least 40 percent compared the corresponding levels from 1990. By 2050, they are to be cut by as much as 80 to 95 percent.
This affects the steel industry in particular, given that it is considered to be one of the main industrial sources of the climate-damaging gas carbon dioxide. As a result, European steel producing companies are trying to fundamentally change their manufacturing processes through a number of pilot projects and test facilities in order to reduce these unwanted emissions.
‘Hybrit’ – a game-changer for the traditional production process
The joint endeavours of a project of three Swedish companies, the steel group SSAB, the mining group LKAB and the energy group Vattenfall, are already coming along swimmingly. ‘Hybrit’, short for ‘Hydrogen Breakthrough Ironmaking Technology’, is set to produce zero carbon steel from 2020 onwards. At a plant in Luleå in northern Sweden, the conventional production method is being given a dramatic facelift.
The production of pig iron, which is later made into crude steel, uses iron ore as a basic material together with what is referred to as a reducing agent, which removes oxygen from the iron ore. Traditional pig iron manufacturing processes usually use coke as a reducing agent. However, in doing so carbon and oxygen produce the climate-damaging gas carbon dioxide.
Video explaining the function of Hybrit
The aforementioned new production process uses hydrogen instead of coke, which also reacts with the oxygen in the iron ore, but the result is water vapour rather than carbon dioxide. The hydrogen itself is produced climate-neutrally with electricity from renewables. As such, the process could ultimately produce genuinely ‘green steel’.
Hydrogen process to drastically reduce emissions
The Swedish Energy Agency has calculated that this process could reduce the CO2 emissions of the entire country by up to ten percent. It is supporting the development of the plant, which is costing around 150 million euros, with a subsidy of 50 million euros – according to the agency, this is the largest amount of funding ever allocated.
Initially, Hybrit will only produce a comparatively modest amount of one metric ton of steel per hour. Moving forward, however, production is to be expanded to churn out the usual industrial quantities of around 100 to 200 times this figure. According to the feasibility study, the associated costs are currently still 20 to 30 percent higher than those of the traditional process, mainly because hydrogen production is complex and energy-intensive. However, according to Mårten Görnerup, who heads up the project, this price tag should also become competitive by 2035. He bases this forecast on the fact that emission certificates will become significantly more expensive in coming years, while renewable energy will be available at increasingly affordable prices.

Difference between conventional steelmaking and the new Hybrit process: The Hybrit process uses hydrogen instead of coke, which produces no CO2 but only water (Source: Hybrit).

Difference between conventional steelmaking and the new Hybrit process: The Hybrit process uses hydrogen instead of coke, which produces no CO2 but only water (Source: Hybrit).
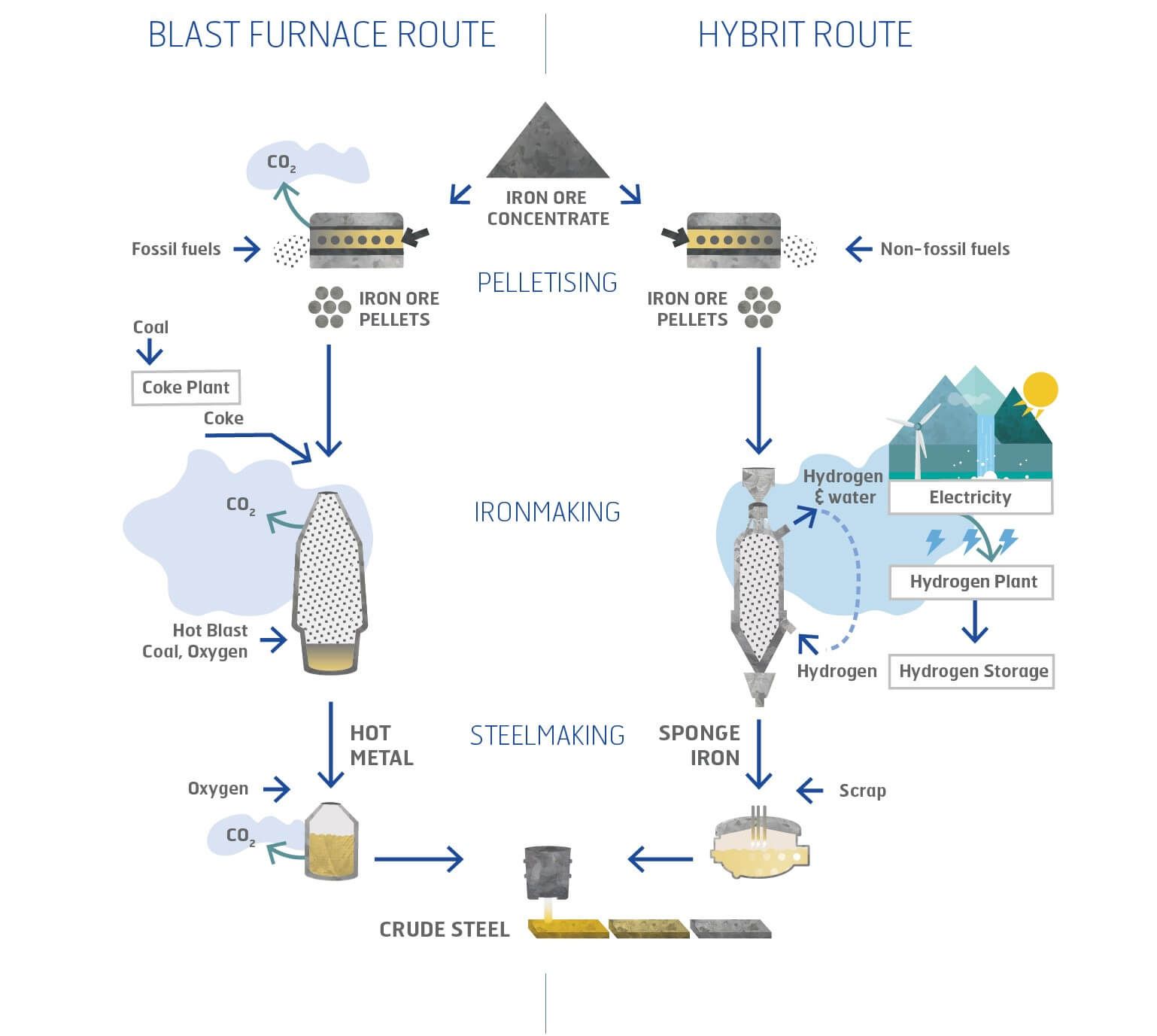
Difference between conventional steelmaking and the new Hybrit process: The Hybrit process uses hydrogen instead of coke, which produces no CO2 but only water (Source: Hybrit).

Difference between conventional steelmaking and the new Hybrit process: The Hybrit process uses hydrogen instead of coke, which produces no CO2 but only water (Source: Hybrit).

Difference between conventional steelmaking and the new Hybrit process: The Hybrit process uses hydrogen instead of coke, which produces no CO2 but only water (Source: Hybrit).
Blast furnaces in Duisburg to be extinguished by 2050
In Duisburg, things aren’t quite as far along as in Sweden. Thyssen Krupp Steel has created a ‘Roadmap for hydrogen-based steel production’, as Andreas Goss, Head of the Steel Division, explained to Handelsblatt earlier this year. All blast furnaces at the Duisburg-Bruckhausen site will have been extinguished by 2050 at the latest. Before then, the group plans on investing ten billion euros in the development of processes for zero carbon steel production.
Special reduction facilities, rather than blast furnaces, will be needed for the hydrogen process. This is why Thyssen Krupp is planning on slowly upgrading or replacing existing facilities with new ones. The company is still in the process of looking into things, and Dr. Arnd Köfler, head of production, sees “many unanswered questions” in the supply of hydrogen.
New blast furnace replaces coking plants
In the Netherlands, Tata Steel Europe, Europe’s second-largest steel producer, is testing another way to reduce emissions from steel production. According to the group, the production of one metric ton of steel at the Ijmuiden plant currently creates 1.7 metric tons of carbon dioxide. This is significantly less than other plants (which emit around 4 metric tons of CO2), but is also very close to the absolute baseline of what can be achieved with current production process.
The group considers the opportunities in this area to be exhausted – significant reductions are only possible through the development of “groundbreaking new technologies”. One such technology could be what is known as the Hisarna process. Back in 2010, a plant based on this process was built at the Ijmuiden steelworks to the tune of 20 million euros. Since then, millions more have been invested and a number of test runs have been carried out.
A state-of-the-art cyclone-converter furnace is at the heart of the process, and reaches temperatures that allow direct feeding of iron ore and coal. Normally, the materials would have to be prepared before processing – with the help of this new furnace type, this is no longer necessary. “This process significantly reduces the number of energy-intensive steps required for the conventional steel-making process,” the company says. This also reduces energy consumption and emission levels. While in the beginning there was talk of “at least 20 percent” less CO2 emissions, long-term testing has shown that it could in fact be as much as 50 percent. According to the company, a plant is currently being planned that will use this process to produce liquid iron on an industrial scale. It will be operational in about seven years.
Which process is ultimately adopted across the board remains to be seen. A current study of the Fraunhofer Institute for System and Innovation Research initiated by the European Commission has come to a similar conclusion: emissions in the EU could be reduced by 95 percent through “innovative CO2-neutral technologies and far-reaching technical changes”. The steel industry has taken the first steps. ‘Green steel’ could one day become a reality.
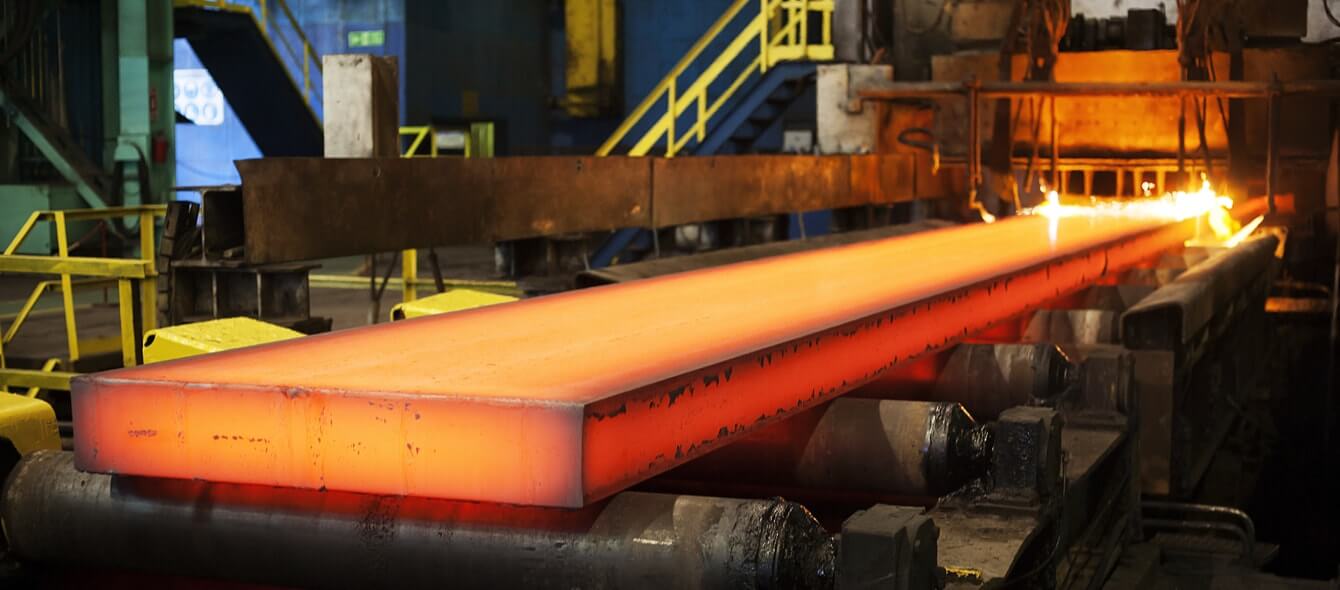
2019-05-29
How hydrogen could change the face of steel production as we know it
In order to reduce its emissions, the steel industry needs technical innovation.
Sweden has one possible solution
The EU is taking climate protection very seriously. Both increasingly stricter environment and climate protection regulations and rising costs through emissions trading are turning up the heat for the industry. By 2030, greenhouse gas emissions in the European Union are to be reduced by at least 40 percent compared the corresponding levels from 1990. By 2050, they are to be cut by as much as 80 to 95 percent.
This affects the steel industry in particular, given that it is considered to be one of the main industrial sources of the climate-damaging gas carbon dioxide. As a result, European steel producing companies are trying to fundamentally change their manufacturing processes through a number of pilot projects and test facilities in order to reduce these unwanted emissions.
‘Hybrit’ – a game-changer for the traditional production process
The joint endeavours of a project of three Swedish companies, the steel group SSAB, the mining group LKAB and the energy group Vattenfall, are already coming along swimmingly. ‘Hybrit’, short for ‘Hydrogen Breakthrough Ironmaking Technology’, is set to produce zero carbon steel from 2020 onwards. At a plant in Luleå in northern Sweden, the conventional production method is being given a dramatic facelift.
The production of pig iron, which is later made into crude steel, uses iron ore as a basic material together with what is referred to as a reducing agent, which removes oxygen from the iron ore. Traditional pig iron manufacturing processes usually use coke as a reducing agent. However, in doing so carbon and oxygen produce the climate-damaging gas carbon dioxide.
Video explaining the function of Hybrit
The aforementioned new production process uses hydrogen instead of coke, which also reacts with the oxygen in the iron ore, but the result is water vapour rather than carbon dioxide. The hydrogen itself is produced climate-neutrally with electricity from renewables. As such, the process could ultimately produce genuinely ‘green steel’.
Hydrogen process to drastically reduce emissions
The Swedish Energy Agency has calculated that this process could reduce the CO2 emissions of the entire country by up to ten percent. It is supporting the development of the plant, which is costing around 150 million euros, with a subsidy of 50 million euros – according to the agency, this is the largest amount of funding ever allocated.
Initially, Hybrit will only produce a comparatively modest amount of one metric ton of steel per hour. Moving forward, however, production is to be expanded to churn out the usual industrial quantities of around 100 to 200 times this figure. According to the feasibility study, the associated costs are currently still 20 to 30 percent higher than those of the traditional process, mainly because hydrogen production is complex and energy-intensive. However, according to Mårten Görnerup, who heads up the project, this price tag should also become competitive by 2035. He bases this forecast on the fact that emission certificates will become significantly more expensive in coming years, while renewable energy will be available at increasingly affordable prices.

Difference between conventional steelmaking and the new Hybrit process: The Hybrit process uses hydrogen instead of coke, which produces no CO2 but only water (Source: Hybrit).

Difference between conventional steelmaking and the new Hybrit process: The Hybrit process uses hydrogen instead of coke, which produces no CO2 but only water (Source: Hybrit).
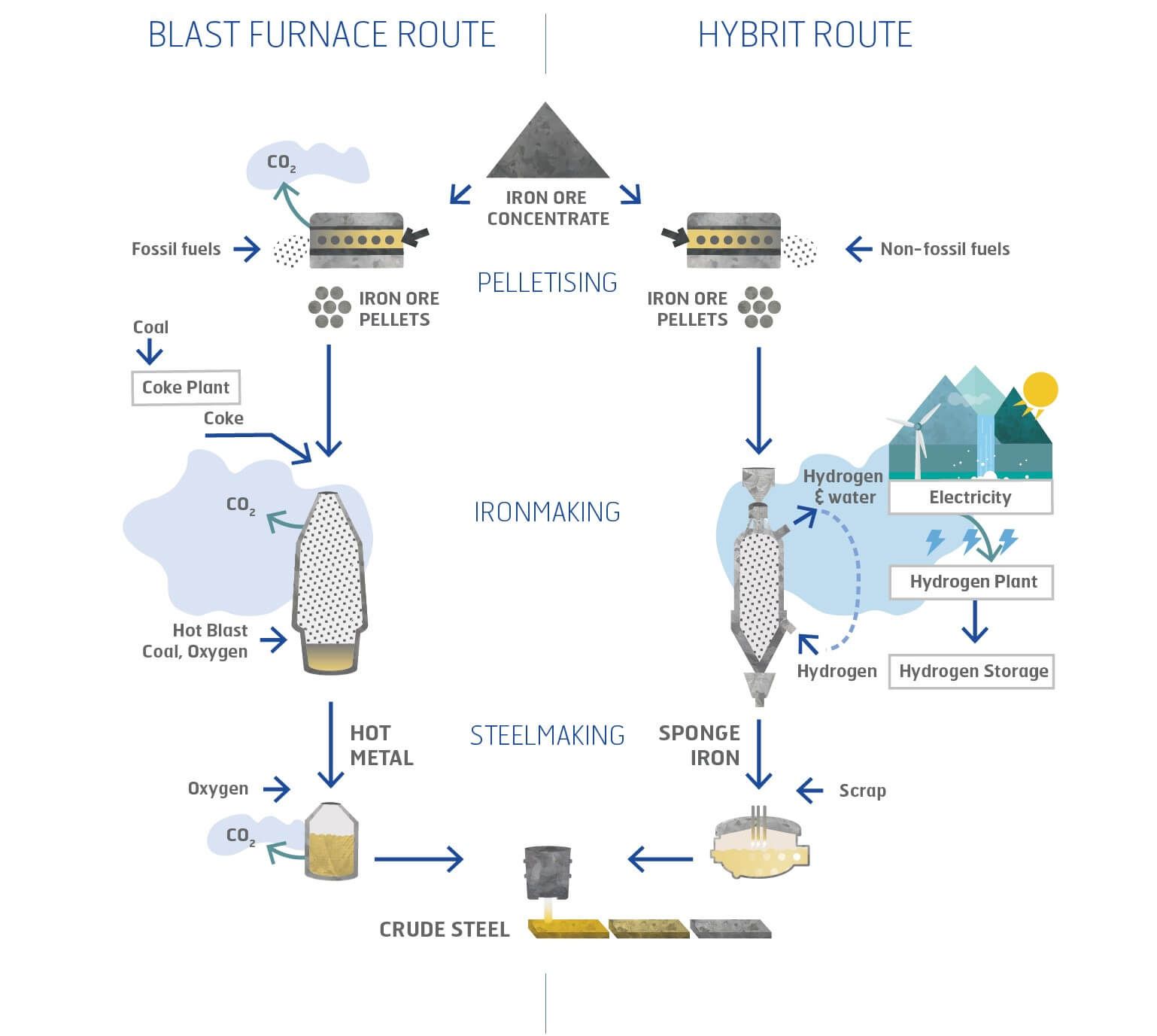
Difference between conventional steelmaking and the new Hybrit process: The Hybrit process uses hydrogen instead of coke, which produces no CO2 but only water (Source: Hybrit).

Difference between conventional steelmaking and the new Hybrit process: The Hybrit process uses hydrogen instead of coke, which produces no CO2 but only water (Source: Hybrit).

Difference between conventional steelmaking and the new Hybrit process: The Hybrit process uses hydrogen instead of coke, which produces no CO2 but only water (Source: Hybrit).
Blast furnaces in Duisburg to be extinguished by 2050
In Duisburg, things aren’t quite as far along as in Sweden. Thyssen Krupp Steel has created a ‘Roadmap for hydrogen-based steel production’, as Andreas Goss, Head of the Steel Division, explained to Handelsblatt earlier this year. All blast furnaces at the Duisburg-Bruckhausen site will have been extinguished by 2050 at the latest. Before then, the group plans on investing ten billion euros in the development of processes for zero carbon steel production.
Special reduction facilities, rather than blast furnaces, will be needed for the hydrogen process. This is why Thyssen Krupp is planning on slowly upgrading or replacing existing facilities with new ones. The company is still in the process of looking into things, and Dr. Arnd Köfler, head of production, sees “many unanswered questions” in the supply of hydrogen.
New blast furnace replaces coking plants
In the Netherlands, Tata Steel Europe, Europe’s second-largest steel producer, is testing another way to reduce emissions from steel production. According to the group, the production of one metric ton of steel at the Ijmuiden plant currently creates 1.7 metric tons of carbon dioxide. This is significantly less than other plants (which emit around 4 metric tons of CO2), but is also very close to the absolute baseline of what can be achieved with current production process.
The group considers the opportunities in this area to be exhausted – significant reductions are only possible through the development of “groundbreaking new technologies”. One such technology could be what is known as the Hisarna process. Back in 2010, a plant based on this process was built at the Ijmuiden steelworks to the tune of 20 million euros. Since then, millions more have been invested and a number of test runs have been carried out.
A state-of-the-art cyclone-converter furnace is at the heart of the process, and reaches temperatures that allow direct feeding of iron ore and coal. Normally, the materials would have to be prepared before processing – with the help of this new furnace type, this is no longer necessary. “This process significantly reduces the number of energy-intensive steps required for the conventional steel-making process,” the company says. This also reduces energy consumption and emission levels. While in the beginning there was talk of “at least 20 percent” less CO2 emissions, long-term testing has shown that it could in fact be as much as 50 percent. According to the company, a plant is currently being planned that will use this process to produce liquid iron on an industrial scale. It will be operational in about seven years.
Which process is ultimately adopted across the board remains to be seen. A current study of the Fraunhofer Institute for System and Innovation Research initiated by the European Commission has come to a similar conclusion: emissions in the EU could be reduced by 95 percent through “innovative CO2-neutral technologies and far-reaching technical changes”. The steel industry has taken the first steps. ‘Green steel’ could one day become a reality.