[By Ryan C. Walker]
Popular history and historians in public service have encouraged the public to view the production capacity of the United States during as World War II (WWII) as a “miracle.”1 The production was recognized by the Allies as pivotal to victory and the first studies appear to have sought to understand the process behind the miracle. Academic interest in the subject dates at least to 1956, when Francis Walton wrote the book that likely coined the term, Miracle of World War II: How American Industry Made Victory Possible.2
Research did not end there, however, as Alan L. Gropman wrote a McNair Report in 1996, Mobilizing US Industry in World War II: Myth and Reality, which sought to dispel notions of a spontaneous miracle and identify how this process occurred. Gropman believed the importance of dispelling the “halo” surrounding the production was identifying the constituent causes as:
“…there were enormous governmental, supervisory, labor-management relations and domestic political frictions that hampered the effort—and there is no reason to think that these problems would not handicap future mobilization efforts. With enormous threats looming in the mid 1930s and increasing as Europe exploded into war at the end of the decade, the United States was in no way unified in its perception of the hazards, nor was there any unity in government or business about what to do about it.”3
Gropman identified one of his primary influences as Gary E. Weir.4 Weir has been one of the primary influences in identifying these processes specifically for shipyards and submarine production, with his focus on 1940-61.5 Weir argues the “wartime blend of naval, industrial, and scientific resources,” would eventually coalesce into what he termed the “naval-industrial complex,” which was a result of “[t]he wartime blend of naval, industrial, and scientific resources,” that constituted modern submarine construction.6 The previous focus of these studies has been macro-observations, centering primarily on the larger players, but the problems of today seem to match closely to the problems facing the USN in the 1930s, potentially offering insight into solutions of the present context.
The current production of ships, particularly submarines, has become a subject of interest as geopolitical circumstances become increasingly uncertain. Solutions to increase shipyard productivity, which include building new facilities in Lorain County, Ohio, are primarily long-term solutions that seek to reverse the post-Cold War atrophy of the defense industrial base and are hindered by the necessity of building supply chains for new Naval-Capital Towns.7 As investment has maintained a smaller industrial base since 1991, for the foreseeable future, the shipyards that are producing and repairing today are all that can be reasonably depended on in the short-term (3-5 years).
The United States can do well by recognizing this fact and looking at alternative methods to increase production in existing areas, such as returning to shift work seven days a week on a modified Dupont schedule used in facilities requiring 24-hour support. The modification would be the shift work time availability and switching to a gold-blue crew working two 10-hour first and second shifts, on a four day on/four day off schedule, henceforth referred to as an 8-4-2-10 schedule (eight-day work week, four days per crew, two primary shifts working ten-hour days).
The Challenges to Navigate and Consider
A shipyard, particularly for submarines that fall under SUBSAFE requirements, is one of the most complex production environments. The shipyard worker is employed in a dynamic environment including challenges such as limited spaces; ventilation; exposure to the elements; or the heat and cold associated with an interior of a ship that does not have services to control atmosphere. Further, maritime industries are a relatively unknown niche that only directly or indirectly employed 393,390 people in the United States during 2020, of which 83.1 percent of the directly employed were concentrated in ten states.8
Due to the declining significance and lack of prestige associated with blue-collar work, shipyards that need workers such as General Dynamics Electric Boat have resorted to hiring on the spot and creating elaborate advertisement outreach campaigns. Thus, compounding the shipyard shortage is a shortage of laborers willing to work on a shipyard in any capacity (directly onsite or supporting).9
Creating any solution must be palatable to a variety of stakeholders, Federal, State and Local governments, business and organizational interests, and labor interests. For any radical departure from the status quo outlined in this work, concessions must be made to all stakeholders. For government and naval officials, this proposal would assume a higher expenditure for funds that are already tightly spread amongst the Department of the Navy. For business interests, the schedule will interrupt long-standing processes and require a new business environment, the type of overhaul that necessitates organizational unrest.
Similarly, labor interests will have to change their normal work schedule of eight hours, five days a week, with a rigid weekday and weekend divide (which has come under recent pressure anyway). Recognizing these challenges and then designing collaborative strategies that find true win-wins among the stakeholders is a major goal of this article and is meant to be thought-provoking rather than a delineation of true guidelines.
The Miracle of Production was fuelled in no small part by hard work and coordination at all levels of production, from the apprentice standing a Firewatch to the Admirals who oversaw the programs, getting an increase in production today will likely require a similar level of shiftwork, dedication, and expense seen in the previous era. There is a defense industrial base to build on today, and the USN, private shipyards, and policymakers would do well to seek to maximize the current output in addition to planning new facilities.
The shift work this article seeks to create is similar to the nearly around the clock production seen in World War II. It also maintains a period of third shift where evolutions that require minimal personnel presence or would be too costly to be effective, and the 8-4-2-10 schedule could be implemented to offer a sustainable long-term solution. First, though, it is important to understand why this would be more desirable/efficient than the current status quo.
Shift Work as Practiced Today
In 1920, then Rear Admiral Joseph R. DeFrees was approached by Thomas Edison on the “best ways to expedite construction.”10 With Edison’s input, Defrees recommended uninterrupted construction programs, increased uniformity in construction, improved labor and facilities, as well as devoting more hours to production, improving labor relations to reduce strikes, and encouraging more efficient utilization of skilled workers who could not do shift work.11 Similar issues, such as labor shortages, plagued submarine construction prior to WWII as well, but Weir notes the Commandant of Portsmouth Naval Shipyard adopted several of these recommendations, such as “employing shifts, permitting overtime, and hiring as many skilled workers as possible,” though the primary yards were stymied by a limited two-year construction program.12
While shift and weekend work is still practiced in many yards, the ability of the second and third shifts to match production is limited primarily by the structure of society emphasizing a five-day, 40-hour work week, primarily conducted between 0600-1700. The result of the slowdown in defense spending, the schedules have shifted to a ‘normal’ workweek that emphasizes much of the work is primarily done during first shift. Work conducted aboard a submarine is conducted in tight spaces, often falling prey to the Law of Diminishing Marginal Productivity, wherein adding labor units to a fixed space will increase productivity at a decreasing rate, until adding additional units becomes negative. Further, the difficulty of coordination in an environment with so many stakeholders means much of the time that could be spent for labor is often spent in meetings (which are important, but do represent an opportunity cost). Currently, shipyards are facing the issue of too much simultaneous work is conducted during first shift, increasing frustration for the work force.
Cutting corners in safety is not acceptable in the USA and is certainly not acceptable in a NAVSEA or NAVSEA-certified private facility producing SUBSAFE boats, reducing hours for any reason is likely not a tenable solution as each evolution has a purpose. If there has been a benefit in the slowdown in the past thirty years, it is that much of the waste associated with naval production has been identified and mitigated to the best of the respective facilities’ ability. In this case, the root cause is the reliance on one shift to do much of the current work in a limited space.
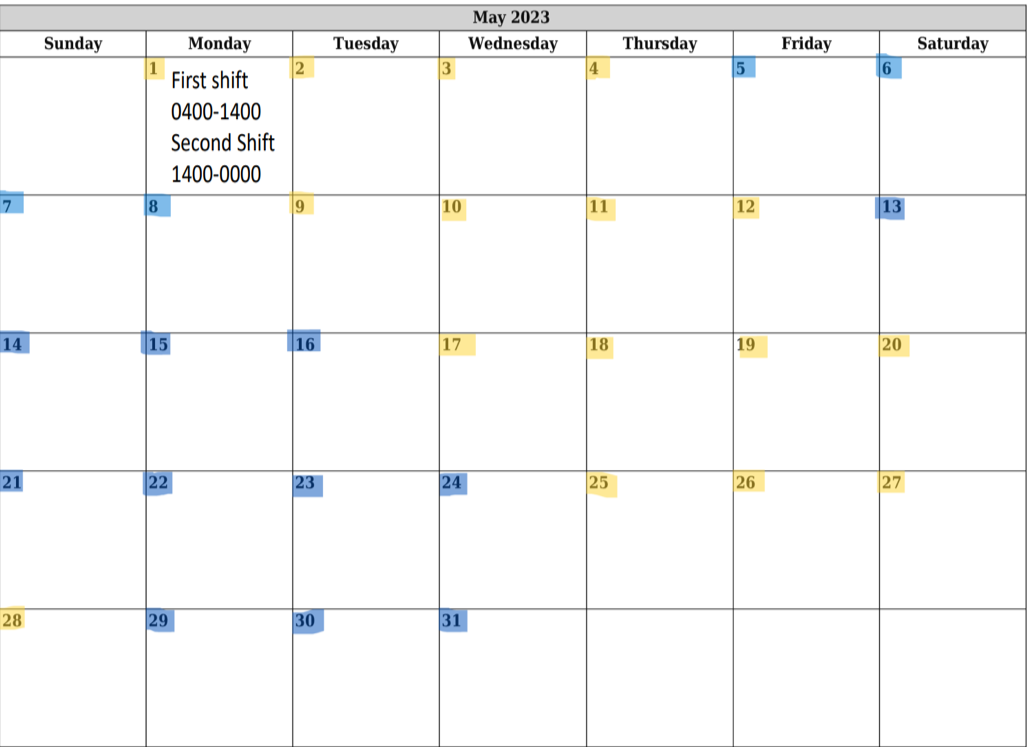
Figure 1: Potential outline of May 2023 if 8-4-2-10 modified Dupont schedule were to be adopted. (Author graphic)
In the recommended 8-4-2-10 modified Dupont schedule, the two ten-hour shifts will be equally divided in terms of personnel and workload. Assuming the actual labor time per shift can be increased to seven hours per 20 hours of effective labor availability per day, with the average extended across all seven days, would mean an effective 140 hours of potential production per week. This compares to the current (1.5 full shift capability, for 12 hours of potential production, five days a week) for 60 hours, which can be extended two more full shifts during the weekend for a likely peak efficiency at 76 hours per week.
These hours are illustrative and substantiated only by the author’s personal experience in the naval facilities; they may not be accurate or paint the full picture for every shipyard or even each department. For best results, the best insight would be garnered by surveying each department if the 8-4-2-10 schedule is best for their work as the answer may be different depending on the type of work conducted.
The greatest potential increase comes from increased weekend work, but in the current five-day workweek, working overtime or weekend work in addition to a normal workweek could cause burnout and cause prospective personnel to shy away from the shipyard due to a reputation of burnout. To prevent that, creating a two-crew system that allows laborers to have four days off will preserve their well-being while also ensuring production continues. Overtime opportunities will still be present: if a person is ill or on vacation during their scheduled shift, two workers could be present to offer their time in six consecutive days of labor, while also ensuring two days of rest occur.
If a pandemic such as COVID-19 occurred once again and a person on one shift were sick, this could ensure the further division of the labor force to ensure around-the-clock production continues. This is an incredibly desirable practice, which guarantees labor force happiness even during the upheaval associated with a dramatic organizational restructuring. The generous time off practice would become a beacon for employees seeking a more favorable work environment with better benefits and prevent a union, group, or laborers to argue they are being taken advantage of.
Having two primary shifts, first and second, that extend to be ten-hour swathes as opposed to eight, will keep the third shift in a steward/setup role. Manning a third shift as an equal shift would be impracticable, as it is an undesirable shift for many, thus spreading two hours that are traditionally third shift to the other shifts would assist in week-to-week work. Further it creates new opportunities for deckplate leaders, who coordinate with managers that oversee the transition and ensure work continues as the shift changes.
The 8-4-2-10 also prevents the Law of Diminishing Marginal Productivity while also preventing the shortage of parking from which most naval facilities suffer, a quality-of-life improvement many desire. Further, it would offer more opportunities to build the workforce to avoid future shipyard labor shortages or expansion to new facilities like the production of submarines in the Manitowoc Shipyard in Wisconsin during WWII. While this is a future envisioned for shipyards, if executed successfully it could be replicated in essential programs within the DOD.
Returning to the Manitowoc example, should a potential conflict erupt, the shifts also build the available pool of experienced labor to act as advisors for yards who need to be rapidly stood up. As Don Walsh recalled:
“In early 1940 the Manitowoc Shipbuilding Company was asked to build the most complex of ships: the submarine. This was a radical, almost unimaginable, proposal for a company of shipbuilders, many of whom had never set eyes on a submarine…In September 1940, the Navy awarded a contract for the initial run of ten subs. Teams of experts from the Electric Boat Company came to Manitowoc under contract to the yard to help with the early stages of this program. Manitowoc personnel, in turn, visited Electric Boat and the Portsmouth Naval Shipyard to observe submarine construction that was under way at those sites.
The first Manitowoc boat, the USS Peto (SS-265), was laid down in June 1941. She was launched in April 1942—228 days ahead of schedule—and went off to war just one year after the attack on Pearl Harbor. Early delivery of subs was to be a way of life for this fine shipyard. And as they got out into the Fleet, their crews even began to send back thank-you letters for the quality and strength of those boats. These satisfied ‘customers’ offered the best kind of praise for the Manitowoc employers, who earned Navy Department production “E” awards every year during the war.”13
The teams of Electric Boat advisors were pivotal to this rapid success, along with allowing the workers from those areas to observe production in existing sites. In an ideal world, the short-term solution would also be pursued simultaneously with longer-term solutions, each fueling the other’s success. As labor is at the center of each challenge, any solution that increases the available pool of labor should be considered.
Challenges Reconsidered
The ultimate question is whether or not the potential increase in production is worth it. Manning production around the clock will likely increase the cost of doing business in private or public yards. Are policy-makers and the USN willing to spend the money? Even if the plan received backing from leadership, where would that money come from? Would private and labor interests buy-in?
Perhaps attempting this on a smaller scale, such as only shipyard trades or on a smaller project would be more palatable to start with. Once that is accomplished, larger projects can be attempted once actual production increases can be observed and measured as worth the expense. Further, there may be money to develop a new production site or to increase production; the former will likely be more efficient in the long-run and the latter for the short-run. Manitowoc was stood up, but experienced personnel from other yards helped the push, expanding the pool of experienced labor can only aid these long-term projects positively.
For naval officials, this program would likely cause questions of how to adequately supervise and maintain control over essential procedures, particularly those requiring approval and oversight. Changes to management structures to become a fulcrum between the two shifts, splitting their time equally between the two shifts, will be necessary. In some cases, stoppages are inevitable, but the goal in this schedule would be to resolve the issue discovered on one shift, before they return to work the next day, or at least make progress. Overall, the least amount of resistance is expected from naval officials, as this is a recognized and much discussed topic.
While the government will ultimately bear much of the cost, businesses will be required to spend more money on more laborers, particularly benefits for full-time employees. However, considering the potential “deal” laborers would receive, there likely would be no shortage and the production scheduling issues that have plagued them could be resolved without burning out the workforce. There is even the potential that reducing the amount spent on overtime labor will reduce costs and the shipyard itself would become increasingly resilient.
On the surface, one could look at this potential schedule and sense the laborers receive the greatest benefit and have no room to complain. This would ignore how fundamental the first shift, 40-hour work week has become for American society. Working 9 to 5 (or any other iteration of an eight-hour work day) is cherished by many and it would take a long time for towns to cater to the workers on different shifts. For a single person there is not much lost, but many who work have families.
Adopting the 8-4-2-10 would be asking for a fundamental change in the work week, affecting availability for family events, dinners, sport events, and many other familial practices and commitments. A labor union, which many shipyards have, would have to sell that this is not only a good idea, but a benefit to the people they represent.
The guarantee of four days off per 8-day work week and at least 15 days of paid time off (which seems to be the industry standard as is) would help sell this as a deal that cannot be refused: a win-win for all. Make no mistake, despite the benefits, the greatest burden will be carried by the labor force should this plan be enacted; and leaders should seek to empower and support their mission.
Conclusion
How to return to WWII production pace in an unsure geopolitical environment that requires ever more ships? The first step should not be asking where can we produce more and spending resources, but rather asking how can current facilities be operated at the maximum efficiency? This article forwards a proposal based on a return to around the clock production, modified to meet the needs of all stakeholders. The 8-2-4-10 modified Dupont schedule could increase shipyard productivity in the short-term to levels needed, once an adjustment period associated with an initial learning curve is overcome.
The inspiration we should look for is not a “miracle,” but rather a slow progressive increase in production efficiency coupled with nurturing the labor force to ensure labor issues are also resolved. This is potentially a radical solution that may ultimately be unpalatable but should start the conversation in a direction that emphasizes reinforcing current production, rather than spending a generation waiting on another Miracle of Production.
This article appears courtesy of CIMSEC and may be found in its original form here.
Ryan C. Walker served in the United States Navy’s Submarine Force from 2014 to 2019, receiving an honorable discharge. He received his Bachelor of Arts in History from Southern New Hampshire University, he then received his Master of Arts in Naval History from the University of Portsmouth, receiving a Distinction. Walker has continued his studies at the University of Portsmouth as a PhD candidate, his current research interests are enlisted American submariners from 1915-40, British private men-of-war in the North Atlantic, and the development of American Naval-Capital-Towns. Walker has also held a variety of roles in the Defense Industry and is currently employed by General Dynamics Electric Boat as a Senior Test Engineer. The opinions and views expressed are those of the author alone and are presented in his private capacity.
Endnotes
1 The National WWII Museum, “Out-Producing the Enemy:’ American Production During WWII,” accessed May 5, 2023, https://www.nationalww2museum.org/sites/default/files/2017-07/mv-education-package.pdf; David Vergun, “During WWII, Industries Transitioned From Peacetime to Wartime Production,” accessed May 5, 2023, https://www.defense.gov/News/Feature-Stories/story/Article/2128446/during-wwii-industries-transitioned-from-peacetime-to-wartime-production/; National Parks Service, “World War II and the American Home Front,” accessed May 5, 2023, https://www.nps.gov/subjects/nationalhistoriclandmarks/upload/WWII_and_the_American_Home_Front-508.pdf.
2 Francis Walton, Miracle of World War II: How American Industry Made Victory Possible, (New York: Macmillan, 1956).
3 Alan L. Gropman, Mobilizing US Industry in World War II: Myth and Reality. McNair Report No. 50, Institute for National Strategic Studies, National Defense University, 1996, 2.
4 Gropman, Mobilizing US Industry, v.
5 Gary E. Weir, Forged in War: The Naval- Industrial Complex and American Submarine Construction,(Washington D.C.: Naval Historical Center Department of the Navy, 1993); Gary E. Weir, “The Search for an American Submarine Strategy and Design, 1916-1936.” Naval War College Review 44, no. 1 (1991): 34–48. http://www.jstor.org/stable/44637145.
6 Weir, Forged in War, 6.
7 Richard Payerchin, “Lorain: Submarines would Ride in Barges to get to Dry Dock,” accessed May 14, 2023, https://www.morningjournal.com/2022/02/14/lorain-submarines-would-ride-in-barges-to-get-to-dry-dock/; Megan Eckstein, Joe Gould and Bryant Harris, “How the US plans to Expand its Submarine Industrial Base for AUKUS,” accessed May 5, 2023, https://www.defensenews.com/naval/2023/03/15/how-the-us-plans-to-expand-its-submarine-industrial-base-for-aukus/; Sam LaGrone, “Navy Estimates 5 More Years for Virginia Attack Sub Production to Hit 2 Boats a Year,” accessed May 5, 2023, https://news.usni.org/2023/03/31/navy-estimates-5-more-years-for-virginia-attack-sub-production-to-hit-2-boats-a-year; Sam LaGrone, “Submarine Supply Chain Largest Barrier to Improving Virginia Attack Sub Schedule, Says Boykin,” accessed May 14, 2023, https://news.usni.org/2023/05/08/submarine-supply-chain-largest-barrier-to-improving-virginia-attack-sub-schedule-says-boykin.
8 Maritime Administration (MARAD), The Economic Importance of the U.S. Private Shipbuilding and Repairing Industry, Report, March 30, 2021. https://www.maritime.dot.gov/sites/marad.dot.gov/files/2021-06/Economic%20Contributions%20of%20U.S.%20Shipbuilding%20and%20Repairing%20Industry.pdf, 1, 8.
9 Dana Wilkie, “The Blue-Collar Drought: Why jobs that were once the backbone of the U.S. economy have grown increasingly hard to fill,” accessed May 14, 2023, https://www.shrm.org/hr-today/news/all-things-work/pages/the-blue-collar-drought.aspx; Brian Hallenbeck, “Electric Boat president can’t stress it enough: ‘We’re hiring!’” May 8, 2022, https://www.theday.com/local-news/20220121/electric-boat-president-cant-stress-it-enough-were-hiring/.
10 Weir, Forged in War, 14-15.
11 Weir, Forged in War, 15.
12 Weir, Forged in War, 15-16.
13 Walsh, “Those Stout Manitowoc Boats,” Website Reprint.
The opinions expressed herein are the author's and not necessarily those of The Maritime Executive.