Copper and Bronze: The Far-Reaching Consequences of Metallurgy
FLORIN CURTA
“Bronze is the mirror of the form.” —Aeschylus, frg. 384
Abstract
Historians and archaeologists have long viewed the discovery of metals and the invention of metallurgy as a revolutionary step in the history of humanity. But metallurgy was more than a technical revolution; its invention in the Bronze Age was primarily a social revolution. This chapter introduces the technological innovations associated with the manipulations of metal by smelting and casting, and the economic and social problems that came with the development of this early metallurgy. At the same time, the chapter highlights the role of trade and its connection to the rise of metallurgical, proto-industrial centers across Europe and the Middle East. The ensuing social and political complexities, disparities, and military conflicts are direct results of that connection and of the competition for resources inherent for metallurgy. Finally, the chapter points to the rise of a class of material specialists in society, forerunners to our contemporary engineers.
Introduction
We can make tools, jewelry, toys, kitchenware, furniture, and almost any other item from metal. Useful though metals are, they are sometimes less than perfect for the jobs we need them to do. That is why most of the “metals” we use are not actually metals at all but alloys—metals combined with other substances to make them stronger, harder, lighter, or better in some other ways. For example, copper is good in some ways, but bronze is far better. Thus, the exploration of copper in this chapter is a way to introduce not only the discovery of metals in human prehistory, but also the invention of metallurgy, the manipulation and alloying of those metals to meet human needs. Understanding the social and political implications of introducing these new materials—alloys—is crucial for the engineers of the future, who will find ways of using and improving existing materials, and will create new ones.
The Revolutionary Role of Metals and Alloys
The revolutionary aspects of discovering the properties of metals and, particularly, alloys, has long been recognized by scholars seeking to explain the social changes that led to our modern civilizations. As introduced by Gillespie in her earlier chapter on Clay, the idea that even the (pre) history of humanity could be divided into “ages” on the basis of the materials out of which humans made their tools and weapons is relatively new. It originated with Danish archaeologist Christian Jürgensen Thomsen (1788–1865; Figure 5.1).[1]
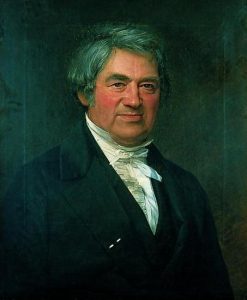
He studied Greek and Latin in Paris, and was very fond of the Roman poet Lucretius (99–55 BCE), the author of a philosophical poem entitled De rerum natura (“On the Nature of Things”). In that poem, Lucretius describes how the first tools humans used were “hands, and nails, and teeth, and stones and branches torn from trees,” before they discovered bronze and iron. With bronze, men “tilled the soil” and “roused the waves of war,” before “the sword of iron came forth,” and, as they despised “bronze sickle’s curving blade,” they began to “cleave the earth” with iron.[2] Inspired by Lucretius, Thomsen invented the so-called Three-Age System still used in prehistoric archaeology. That we still refer to one of those chronological divisions as Bronze Age underscores the significance of metallurgy for the history of humanity.
It is easy to overstate the importance of discovering metals and alloys. However, the invention and practice of metallurgy were not the most important developments, as Lucretius and Thomsen thought. On one hand, metallurgy remained in some parts of the world a secondary activity without any substantial cultural and social impact (see below). On the other hand, the same techniques were used both in societies with a low level of organization and in complex societies such as those in Mesopotamia and Egypt.
Metallurgy and Social Innovation
Metallurgy consists of a series of complicated operations, from finding and extracting the metal ore to smelting and processing it with heat and specialized tools. Using metals considerably shortened the time necessary for the production of tools or weapons (previously made through a complicated flintknapping process as discussed in Sassaman’s chapter on ceramics), and allowed for the mass production of identical, or at least similar, artifacts. A key component of metallurgy is mastering a great number of physical and chemical reactions and processes, as well as the precise sequence of operation and its timing, the chaîne opératoire also mentioned in a different context in Sassaman’s chapter. That is why the first metals used for metallurgy were those that could be extracted and processed without too much of an intellectual and technological effort. The Bronze Age came before the Iron Age, as Thomsen put it, because iron metallurgy is much more complicated and involves a lot more knowledge and advanced technological processing than bronze metallurgy. In a very fundamental sense it was easier to smelt copper and bronze from copper ore than it was to smelt iron from iron ore.
In certain parts of the world, for various reasons early metallurgical knowledge was lost at some moment in time and the technology for producing bronze had to be reintroduced at a later time. People with metalworking knowledge must have therefore moved around for metallurgy to spread. One way for that to happen involved specialists moving into new territories, thus gradually spreading their knowledge. Another was to have people learning the trade in one place, under the direction of specialists, and then moving to new territories or returning to their own communities with the skills to produce metal objects. Either way, the demand for copper preceded the actual movement of specialists and/or their apprentices. However, both in the Far East (northeastern Thailand and China) and in the New World (Mexico and Peru), copper and bronze metallurgy was invented independently, without any contacts with the centers in the Near East and the Mediterranean region.
In short, metallurgy implies a long process of learning and professional specialization. Unlike pottery, for example, metallurgy cannot be done “on the side” of other external work or domestic activities, at least not when the goal is to produce a large number of similar artifacts. In other words, someone involved, for example, in agriculture on a regular basis cannot do some metallurgy during his or her spare time. The learning process is long and complicated, and that requires time and dedication. That is the main reason that metallurgy cannot spread as a diffusion of ideas from person to person. Rather, metalworking needs to be taught by a specialist to another person. Metallurgy implies not only the existence of specialists, but also a complex process of learning, which sets it apart from other technologies, the spread of which was simply based on diffusion. Put simply, while the products made through metallurgy impacted societies by addressing immediate needs, the process of metallurgy also impacted society by creating a new class of professional specialists in the social order.
Copper and Smelting
Copper was fashioned into artifacts as early as the 7th millennium BCE. Some of the earliest artifacts—tubular beads and other dress accessories—are from Çatalhöyük in Turkey (ca. 6500 BCE), the archaeological site most prominently featured in the previous chapter on clay. There are good reasons to believe that the copper in those artifacts was extracted from ore rather than created from native copper, copper in its pure metallic state. This extraction process is called smelting. A copper axe was found with the mummified body of a man who died in the Austrian Alps ca. 3300–3200 BCE. The axe was smelted from copper ore. “Ötzi,” as this extraordinary mummy came to be known, was a hunter, but possibly also a shaman, in which case the axe was not necessarily a tool, but an object used in rituals.[3] (Figure 5.2)
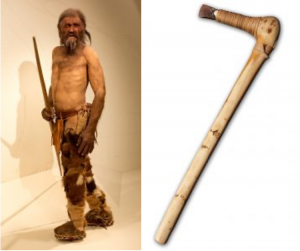
The earliest use of metal, therefore, had no economic role, as most metal artifacts were either dress accessories or objects of ritual use.
Native copper is still available in regions of the world such as Australia, France, China, Namibia, and Iran, where it appears in the form of distorted masses or extremely distorted crystals. Native copper does not have impurities, so it can be shaped by hammering. The copper artifacts from Çatalhöyük were hammered, possibly with stone tools. Hammering can induce dislocations or imperfections in the copper, making it both harder but also more brittle (a process known as work hardening). Applying heat removes some of these dislocations and renders copper less brittle, an operation known as annealing. These processes initially served for the fashioning of durable cutting edges (e.g., for axes or knives). Such artifacts were sometimes collected and deposited in the earliest hoards known to history, but none of them show any wear and tear, a clear indication that their function was not utilitarian, but ritual. In other words, these early metal artifacts were produced for storing a materials (copper or bronze), which due to the challenges of smelting were rare and therefore precious. Why would metal be regarded as rare and precious? The first worked copper was the native variety that was dug out of the earth’s surface (Figure 5.3). Because native copper is not commonly found copper in general was perceived to be rare.
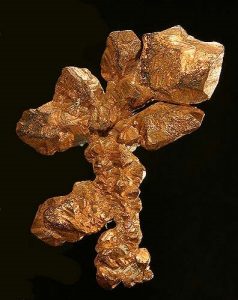
The introduction of impurities in the copper can increase the strength and hardness of the metal. The mixture is called an alloy. One of the most frequent impurities is arsenic, which is present in such ores as arsenopyrite, enargite, and especially tennantite. The addition of arsenic creates a copper alloy, which is called bronze. Tennantite seems to have been a common starting material for obtaining arsenical bronze. During the bronze formation process the arsenic mixed with the reduced copper to create the alloy of bronze, and thus it was possible to obtain copper mixed with impurities without very complicated technologies. Indeed, some of the halberds (particular kinds of weapon combining a spear with a battle-axe) that archaeologists discovered in England, Ireland, and China are made of copper mixed with large amounts of arsenic, and have rivets of pure (and therefore more malleable) metal (Figure 5.4).

When the primary copper ores that contain arsenic are heated in a process sometimes called roasting, they turn into copper arsenate (olivenite). Further reduction of the copper arsenate by heating with charcoal yields a copper-arsenic alloy (bronze). During the heating process, however, a very large quantity (over 50 percent) of arsenic is lost as As2O3. Roasting and alloy formation may well be a relatively simple technology, but the production of copper-arsenic alloys was challenging due to the difficulty of controlling the arsenic content and the release of arsenic gas, which is highly toxic to the craftsman.
Key Concept: Hoard
Collecting valuables either for display or for reuse at a later time seems like a permanent dimension of human history. In reality, this social phenomenon starts in earnest in the Bronze Age and is directly connected to metallurgy. The earliest such collections contained precious but also practical items (some of them deliberately broken in advance), jewelry, and weapons. The logic behind the Bronze-Age deposits of collections of items has nothing to do with economic security. Most hoards were found in or next to bodies of water and were probably meant to be irretrievable. In other words, such collections are the only surviving parts of complex rituals, which may have involved a conceptual association between valuable metal objects and the divine.
Copper ores are typically of two kinds: carbonates (malachite) and sulfide ores (peacock ore or fahlerz). The distribution of both kinds on the surface of the planet is very uneven. The earliest evidence of copper ore mining was to source copper silicates and malachite (copper carbonate). In order to extract copper from malachite, one needs to separate the metal from carbon and oxygen and other impurities. This was possible only through smelting, a new technology for processing copper ores that gained enormous importance in early metallurgy.
A form of extractive metallurgy, smelting is based on the idea of bringing the ore to a temperature sufficiently high for melting the metal. A reducing agent decomposes the ore, thus separating the other elements as gases or slag and leaving the metal base behind. The reducing agent most commonly used in the past was charcoal, which produced CO upon heating in a reducing environment. The reducing environment consisted of an air-starved furnace, in which the incomplete combustion of carbon created CO, which subsequently took the excess oxygen from the metal ore and left the metal behind. Copper smelting involves high temperatures and a reducing environment, two conditions that characterize pottery kilns. It is therefore possible that the process was discovered during experiments with firing pottery. In other words, while playing with “cooking” copper ore, early potters may have discovered smelting, and in the process became the earliest metallurgists.
Activity: Watch a video
Smelting can be done either in a crucible or in a furnace—a single or multiple bowl-like feature over which a clay superstructure was built to contain the ore and the charcoal. This video demonstrates the process of copper smelting in a pit (https://www.youtube.com/watch?v=8uHc4Hirexc).
What were the critical ingredients used in the smelting and what facilities were necessary?
Smelting in furnace first appeared in the Near East, specifically in the lands now within Israel and the Sinai Peninsula (Egypt) during the 5th millennium BCE. Probably the most famous of the earliest smelting sites is Timna, where the earliest evidence of smelting in furnace has been radiocarbon-dated to 4460–4240 BCE.[4] Smelting at Timna released impurities either as gas (CO2) or as slag (primarily silicates), which was tapped off, while the copper sank to the bottom of the furnace, where it was collected in the form of plane-convex ingots. In the Mediterranean region, however, pure copper was formed into ingots of a special form—the so-called “oxhide ingots”—probably in order to be transported at long distance (Figure 5.5).
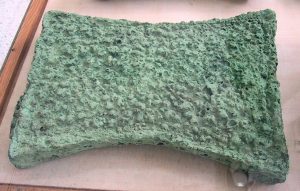
The earliest such ingots have been found in Hazor (northern Israel) and dated between the 17th and the 16th centuries BCE. Lead isotope analysis revealed that the copper in those ingots actually came from Cyprus, which implies regular and quite intensive commercial contacts between the Mediterranean island and northern Israel.[5] However, oxhide ingots appear as far to the north and to the northwest as Bulgaria and Germany, and they also appear in Egyptian wall paintings.[6] The trade connections made possible by the need to procure good copper for metallurgy seems therefore to have extended very far in a relatively short period of time.
Metallurgy, Alloys, and Trade
Because pure copper is soft and malleable, the idea of adding other minerals may have come from the production of copper-arsenic alloys. The addition of other metals is useful, because it reduces the temperature at which copper melts, while at the same time increasing the hardness of the finished metal. Copper melts at 1,085 degrees Celsius, which implies the use of an enclosed furnace and of forced draught or the introduction of overpressure of air. By adding only 10 percent tin to the alloy (bronze), its melting temperature drops to 1,000 degrees Celsius, which still requires a furnace, but not forced draught. On the Brinell scale of hardness, the value of pure copper varies between 35 (for cast copper) and 110 (for copper altered by means of cold working) (in comparison glass has a hardness of 1550) . The addition of 10 percent tin increases the hardness to a value ranging from 70 (cast) to 230 (when the copper is fully cold-worked). It is perhaps unsurprising, then, that beginning with the 16th century BCE, alloys produced in Transcaucasia (between northern Turkey and Russia) mixed tin with copper, as demonstrated by the metallographic analysis of artifacts found in Stepanakart (Azerbaijan), Sengavit (Armenia), and Mekegni (Daghestan). The metallographic analysis showed that the particular choice of ingredients for the alloy was not just a matter of available materials, but also a component of careful planning, since specific artifacts required specific alloys.
Tin for creating bronze came from tin ore (tinstone or cassiterite), which has an even more uneven distribution on planet Earth. Tin for prehistoric bronzes came from Sardinia, Brittany (France), Cornwall (England), Iran, or Bohemia. There is no tin in the Near East or the Eastern Mediterranean, despite the fact that some of the earliest centers of metallurgy were located there. It’s therefore no surprise that by 800 BCE, tin appears in lists of commodities as a precious metal, along with such luxuries as gold, silver, iron, elephant hides, ivory, and purple-dyed cloth.[7] The rarity of tin, as well its importance for some of the hardest and most durable copper-alloys, explains why the development of metallurgy encouraged the development of long-distance exchanges and of trade.
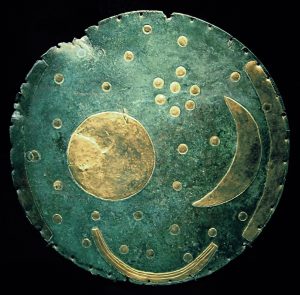
Long-distance trade already existed in the Neolithic period, to circulate lithic materials (such as obsidian, mentioned in Chapter 3) or amber, for example. However, both the density and the intensity of commercial exchanges increased considerably during the Bronze Age, which led to the establishment of “fixed routes” along which goods were moved from northern to southern Europe, and from there to the Near East (western Asia, Turkey and Eqypt) and beyond. The exchange of these material goods encouraged the exchange of ideas, technologies, and ornamental patterns. Bronze-Age human communities, at least in the Old World (Mediterranean region to China), were much more interconnected than ever before. Moreover, the exceptional position of some communities, either close to raw materials or strategically positioned at the crossroads of important trade routes, led to unprecedented levels of economic prosperity, as well as aggression. For example, with no tin resources in the vicinity, the archaeological sites attributed to the Únětice culture in Central Europe (2300–1600 BCE) reveal an abundance of bronze artifacts, some of which are ingots, an indication that bronze moved up and down along the trade routes from the Baltic to the Aegean Seas in both raw and manufactured form. Moreover, Únětice sites have also produced evidence of contacts with the British Isles, the main source of the tin that went into the alloy produced on sites in Europe and the Near East (Figure 5.6).
While copper and tin moved in one direction, other goods came from the opposite direction (Figure 5.7). For example, originating from the southern coast of the Baltic Sea, amber is found on many sites in the Near East and Transcaucasia in the form of beads, pendants, or even cups.[8] Many gold artifacts found on Mycenaean sites in Greece are made of metal from Transylvania, while the silver axes from hoards discovered in Romania have a decoration most typical for Mycenaean weapons.[9]
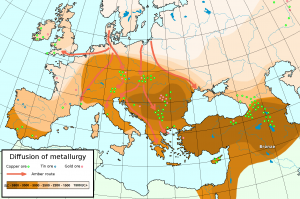
In the Mediterranean region, long-distance trade is also documented by means of copper and tin ingots from some of the earliest shipwrecks that underwater archaeologists have discovered. A ship went down before 1300 BCE at Uluburun, off the south coast of Turkey, together with a cargo of copper and tin, as well as other rare goods, such as cedar and ebony wood, terebinth resin, elephant tusks, tortoise shells, and ostrich eggshells. There were no fewer than 354 oxhide ingots on the ship, some of which were marked by incision, most likely upon receipt or export, and probably as a warranty of their quality for export.[10] To take another example, the lead isotope analysis of oxhide copper ingots found in Sardinia—an island off the coast of Rome, Italy, with clear evidence of copper smelting in the Bronze Age—showed that they had originated in Cyprus (over 2,000 kilometers away).[11] The invention of metallurgy thus put a high trade premium on metals and spurred the development of long-distance trade in response to a high demand in the emerging centers of metallurgical production.
Metallurgy and Social-political Complexity
The movement of metals in the form of ingots along these long-distance trade routes led to the rise of metallurgical centers in regions otherwise devoid of any local resources for alloying metal. Some of the most intriguing sites with abundant evidence of bronze metallurgy appear in areas with no copper or tin ores. For example, Hacınebi, in southeastern Turkey, was a proto-industrial center specializing in the purification and casting of copper coming from the area farther to the north. The end products were then exported to the southern part of the Near East to be further processed there into local bronzes on the basis of imported tin. The excavations carried out in Hacınebi provided evidence for every aspect and each step of the smelting process, including slags, fragments of slag-accreted crucibles, clay molds, and smelting furnaces. Trade contributed to the success of Hacinebi. But also there was a wealth of knowledge there as well. There is even a fragment of tuyere (a tube through which air is blown into a furnace), the shape of which indicates that it was used at the end of a reed blowpipe, and not for actual bellows. In order for a temperature of 2,192 degrees Fahrenheit to be maintained inside a furnace with an internal diameter of 25 centimeters, no fewer than three adults had to blow continuously into pipes such as those that may have been used for the Hacınebi tuyere. In other words, smelting was a labor-intensive operation and clearly required craft specialization.[12]
In fact, the archaeological evidence suggests that smelting was developed far beyond cottage production and involved the existence of specialized workshops. Scanning electron microscopy was used to examine a slag-accreted crucible from Hacınebi and it was discovered that sulfide ores were utilized for smelting. The copper ores in question came from at least 200 km (124 miles) to the northwest from the site. Metallurgy at Hacınebi required organization and planning, special trade deals with the northern neighbors to ensure a constant supply of ore, and special trade deals with various neighbors to the south, who purchased the copper made in Hacinebi.
Moreover, sites similar to Hacınebi were often fortified, and probably inhabited primarily by smelters who were brought there from somewhere else. This strongly suggests that proto-industrial centers such as Hacınebi could not have existed without some form of political organization guaranteeing the stability of the trade routes and the safety and security of the specialists residing within their walls. Elsewhere, fortified settlements seem to have operated as power centers. For example, Early Bronze Age Lerna (in Greece) had a double ring of defense walls with gates and towers. Inside the fortification, there was a palace or administrative center in a central building that archaeologists called the “House of Tiles” (Figure 5.8). Many proto-industrial centers were also power centers. The invention of metallurgy triggered a whole set of transformations in society, some of them with far-reaching consequences for such things as labor division and the rise of early states.
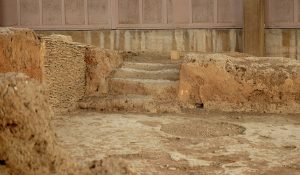
Geographic factors have long influenced political relationships. There were significant changes in the geopolitics of the Bronze Age. As discussed earlier in this chapter, our knowledge of Bronze-Age tools and weapons is primarily based on deposits (hoards, or caches of objects buried for safe-keeping). Some of the largest hoards have been found in the central European regions of modern-day Hungary and Transylvania (western and central Romania). Although both regions lack tin, throughout the Bronze Age they witnessed the rise of complex societies clearly geared towards war and conquest. By developing contacts with other societies located at a long distance (for example, Mycenae, in Greece), Bronze-Age communities in central Europe were able to procure the raw materials necessary for bronze metallurgy. They also borrowed from their trade partners techniques for the metallurgy of gold and silver, of which they had more abundant resources. As a matter of fact, the development of metallurgy in the Bronze Age involved not only copper, but also gold and silver, as well as lead as will be discussed in the following chapter.
With a relatively low melting point at 621 degrees Fahrenheit, lead was one of the easiest metals to process in ancient times. It was first employed for making rivets to be used for repairing broken containers such as found at Phylakopi on the island of Melos and Chalandriani on the island of Syros, both in the Aegean Sea. Lead ingots discovered on both sites indicate a local production of lead, as well as trade with lead in the same form and probably along the same routes as those used for copper and tin. In addition to utilitarian functions, metallurgy served the needs for most sophisticated representation of social status and political power. Lead, instead of tin, was in fact used as a substitution alloy in the production of shaft-hole axes such as found in Belgium and Scandinavia. By contrast, the earliest artifacts made of gold—ring- or disc-shaped pendants—appear in the the 5th millennium BCE on sites attributed to the Gumelniţa and Tiszapolgár cultures of Southeastern and East Central Europe, respectively (Figure 5.9). The jewelry and decorations from the “Royal Tombs” at Alaca Hüyük (Turkey) are among the earliest silver artifacts known and have been dated to the 3rd millennium BCE.
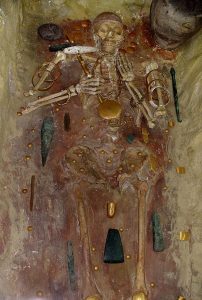
The Use of Metallurgy: Bronze Artifacts
Unlike gold and silver, bronze was initially used for the production of daggers, axes, and swords. Throughout the Bronze Age, tools continued to be made out of stone. Only later did iron metallurgy put an end to the use of stone as raw material for tools. So what was copper used for at origin?
The first implements made of copper were daggers, probably for ritual and not practical use. Such daggers have been found in Beycesultan and Alaca Hüyük, both in Turkey. The earliest axes were flat or adze-like (e.g., palstave), much like the axe found with Ötzi’s mummy. Those were not very efficient tools, and some may have had only a special, probably ritual function. By contrast, the earliest functional axes were shaft-hole specimens discovered on sites of the Tiszapolgár and Gumelniţa cultures. Saws (first documented archaeologically at Los Millares, in Spain) and sickles appeared later, around 3000 BCE and 1500 BCE, respectively. Except for harvesting tools such as sickles, there were no agricultural implements; the plowshare is an Iron Age, not a Bronze Age, invention.
The most impressive artifacts of the Bronze Age are the weapons. The dagger appears to be a Near Eastern invention, and the sword a European invention. Bronze Age swords were made by casting, after which the edges were hammered. This type of weapon originated in the region around, and especially north of, the Black Sea, probably as a further development of the dagger. The technology to produce blades is first documented archaeologically in the Aegean peninsula, where both copper-tin and copper-arsenic alloys were used to produce swords around 1700 BCE. They were of course longer than daggers, with blades in excess of 100 centimeters (over 3 feet).
A great diversity of swords existed in the Middle Bronze Age (1500–1400 BCE, some of which originated in the Mediterranean (Mycenaean Greece) and others in the northwest (Ireland). One of the most important weapon types of the Bronze Age, and the longest-lasting sword of prehistory, is the so-called Naue II type (named after a German archaeologist who first described such swords in the late 19th century). Such swords produced in Europe were highly valued in the Near East, but were quickly replaced after 1200 BCE with iron blades.
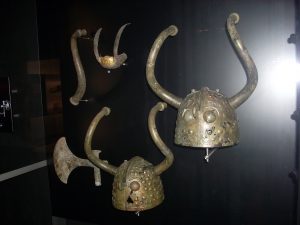
While iron blades were also produced in Europe, it was in China that bronze swords remained in use the longest, the latest being produced during the Han dynasty (3rd century BCE–3rd century CE). An equally European origin may be attributed to the battle-axe, which makes its appearance around 1500 BCE, followed after two centuries or so by helmets, shields, and armor (Figure 5.10).[13] Thus it’s clear that the desire for ever-better weapons drove much of the innovation in metallurgy.
Mold and “Lost-Wax” Casting
The ability to manipulate copper was due to a variety of technological and social developments: trade and professionalization as aforementioned, but also technologies of production such as molding and lost wax casting. This is true for other materials as you will see in the case of iron and steel. For example, molds were used extensively for bronze manufacturing. This relatively rapid development of artifact form and complexity would not have been possible without the parallel development of mold technology. Casting could be done in open one-piece molds carved onto the sides of stone blocks (sometimes even into the native rock). Molds composed of two identical halves were made first of stone, then of clay.
Activity: Watch a video
Claudio Cavazzuti, University of Bologna, demonstrates the process of creating a sandstone mold for casting an Early Bronze Age axe (https://www.youtube.com/watch?v=g5npVVVyWYg).
- What are the advantages and disadvantages of using molds for casting?
- What skill set would craftsmen need to possess in order to cast in molds?
For intricate forms, or for producing parts of larger objects, a new technique was invented ca. 3000 BCE—the “lost wax casting approach.”
Key Concept: “Lost Wax” Casting
The “lost wax” technique allows for the casting of objects with complicated shapes. The details of that shape are initially rendered in wax, after which the negative space created by melting the wax is filled with molten bronze (1,600 degrees Fahrenheit). This technique also allows for the casting of larger objects, including bronze statues, several components of which could be cast in a sequence of “lost wax”-casting events. During the Renaissance (late 15th century CE), the indirect lost-wax technique was developed, which made it possible to make copies of statues. The surface of the statue was divided mentally into different parts, and covered in clay placed over the designated segmented areas, much like a jigsaw puzzle around a 3D object. When the pieces hardened, the statue was removed, and the pieces reassembled and securely bound together. The empty space was filled with molten wax to create what is known as an “intermodel.” After the latter was freed from the piece mold, wax rods (sprues) were attached perpendicular to the surface of the intermodel to serve as the vents for the evacuation of air and gasses during the casting process. Another layer of clay was placed over the intermodel and the whole structure was baked to melt the wax. The resulting mold was then filled with molten metal, as in the traditional “lost-wax” technique.
One of the first free-standing bronze statues since Antiquity, Donatello’s David (1440s), now at the Bargello Museum in Florence, was cast in this manner. Bronze casting, however, is used not only by artists, but also to preserve original works of art. Leonardo da Vinci’s horse (known as Gran Cavallo), for example, was part of an equestrian statue of the duke of Milan, Ludovico il Moro (1494–1499), but the artist never managed to finish the work. The statue was meant to be the largest equestrian monument in the world. Based on Leonardo’s sketches, two full-size bronze casts were produced in 1998, one of which is now in Milan, the other in Grand Rapids. The indirect lost-wax technique led to a proliferation of copies, which in turn prompted the adoption of prohibitive laws. For example, in 1956, a French law limited the number of copies of each Rodin sculpture to twelve—eight to be purchased by anyone, and four to be in the exclusive possession of cultural institutions.
The Social Implications of Metallurgy
The range of forms to be produced by various casting techniques increased enormously throughout the Bronze Age. Perhaps more importantly, the practice of using the same master object for the production of clay molds allowed for the production of sets of identical end products in bronze. Some forging may have followed the casting, in order to produce sharp edges (as in the case of swords and axes, but not always for sickles), thin blades (of daggers), or to bend items to required shape. For the production of such dress accessories as torcs (neck ornaments), bracelets, or composite rings, wiredrawing was practiced by pulling red-hot metal between draw bars, which thinned the bars down. Thin sheets of copper were produced by hammering metal bars onto an anvil. Both wiredrawing and thin sheet hammering were techniques employed primarily in gold and silver metallurgy. Another technique invented during the Bronze Age for the decoration of objects made of thin gold or silver sheet is the so-called au repoussé. With this technique, bosses, dots, rosettes and other motifs were produced by pushing the metal sheet into wooden forms. The technological innovations accompanying the invention of metallurgy thus created a vast field of artisanal expertise, and made room for a conceptual distinction between craft and art and between artisan and artist.
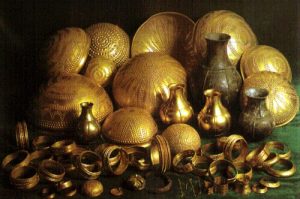
Much evidence for Bronze Age metallurgy comes from the analysis of hoards that were deposited in locations from which they were never retrieved for a wide variety of reasons. There are also hoards of gold artifacts, with a large array of spectacular objects, such as the bracelets, diadems, and gorgets from Villena in southern Spain (Figure 5.11).
Besides being an illustration of the parallel development of bronze and gold metallurgy—often with comparable techniques—the hoards testify to the concern with accumulating (and storing) wealth, which must have been a direct consequence of the social transformations triggered by the introduction of metallurgy (see Chapter 6). One of the most famous golden objects of the European Bronze Age, for example, is the mask found in 1876 in a cylindrical shaft grave inside the fortified settlement at Mycenae in southern Greece (Figure 5.12). The mortuary use of this gold mask is not unique; in fact, many gold and bronze objects (especially weapons) were deposited in graves. The northwest European equivalent of the rich burials in Mycenae is a number of large, circular barrows that appear in the Middle Bronze Age on sites of the Wessex culture in England. Early Bronze-Age barrows in Transcaucasia were often reserved for individuals of high status, buried with a large collection of artifacts, including chariots with wooden wheels.
In the eyes of many, the complicated technological procedures involved in smelting and casting must have turned the full-time specialists in bronze metallurgy into individuals with extraordinary powers. The civilizing hero of Greek mythology, Prometheus, was a metallurgist providing “divine knowledge” to humanity. In ancient Roman religion, Vulcan (the god from whose name the English word “volcano” ultimately derives) was said to have stared for hours at the fire, before discovering that, when making the fire hotter with bellows, certain stones sweated silver or gold. Vulcan later fashioned thrones for all gods of the Roman mythology.
Thor, one of the main gods of the Norse mythology, is known for his hammer (Mjölnir), which was custom-made by the dwarves of Nidavellir, the quintessential blacksmiths of the North. Both in antiquity and in contemporary times traditional societies (such as those in East Africa, for example), smelters enjoy a much more prestigious status than smiths.[14]
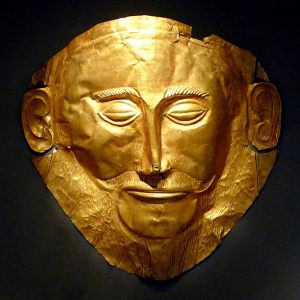
Part of the explanation for this may be that while the work of smiths is a fairly clear process of turning molten metal into objects, the work of smelters looks more like magic as it turns “stones” into metal ingots.
Conclusion
Alloys of a metal are generally stronger and harder but less ductile than the base metal. The invention of metallurgy during the Bronze Age, which was primarily geared towards the production of alloys, had several crucial consequences for societies of that time and later.
On a technological level, a series of new skills became at the same time necessary and commonplace. Such skills required long-term learning processes and apprenticeship, which transformed a group of people in society into specialists, and set apart their social position, both in lifetime and in death. A good parallel to that is the way in which nuclear energy is put to use in the modern world. It is simply not sufficient to build a reactor; a number of highly trained specialists are required as well. The modern use of nuclear technology offers another parallel to the early bronze metallurgy. The potential for use in military applications often advances the non-military or civilian applications.
From an economic point of view, even though bronze was not used for the production of tools as much as iron would be during the Iron Age, raw materials (copper, tin, lead in the form of ingots) and finished products (weapons or tools made of bronze) became more abundant. The early history of metallurgy also reveals the connections between technology and the rise and development of trade routes. Not only does knowledge still spread along trade routes, but there are still very good examples of industrial power-houses developing in regions of the world devoid of resources, much like in the Early Bronze Age. For example, “silicon valley” did not form because there was an abundance of silicon present there. Rather it developed because innovators and engineers who could manipulate silicon were there.
Perhaps more important from the point of view of this course is the fact that the introduction of metallurgy had social implications far beyond setting apart a class of specialists. The new artifact types made possible by metallurgy introduced the possibility of new scales of value and new ways to demonstrate social divisions. Accumulating objects made of bronze, gold, and silver was not just a way to store wealth. It was also a new way to set a group of people apart from the others, not as specialists, but as elites made socially distinct by means of economic privilege. The social disparities created by the adoption of new technologies and their use for the display of power symbols and social status, as illustrated by the archaeology of the Bronze Age, are still a matter of great concern in the 21st century.
Future engineers and their collaborators have much to learn from the lessons of the past. The introduction of bronze—a new technology—called for an unprecedented development of long-distance trade. Mastering the new technology required time- and energy-consuming training of a class of specialists that, for the first time in history, came to play a role in society clearly marked ideologically by their association with magic. Metallurgy also opened new paths for the development of warfare and the symbolic representation of power. Similarly, we should expect any new materials to change the trade patterns around the globe, to create new social categories and inequalities, and to have consequences in fields of human activity that may not have yet been designed.
Discussion Questions
- During the Bronze Age, objects of bronze, gold, and silver produced through complicated techniques were hoarded as valuables. What counted more for their being regarded as such—the intrinsic value of the metal, or the labor involved in producing them? Explain your answer.
- Silicon has a much wider distribution on the planet than either copper or tin, for it is the second most abundant element of the Earth’s crust. However, there is currently a high demand for silicon primarily because of its use in building materials (such as Portland cement), the semiconductor industry, and solar panels. Can you think of cities similar to Hacınebi, the Únětice culture, or Uluburun that were created from the worldwide trade with silicon, and its associated industries?
- Are there any groups of specialists in 21st-century societies around the globe that are remotely similar to the smelters of the Bronze Age? If so, who and in what ways?
Key Terms
alloy
annealing
ingot
metallurgy
native copper
proto-industrial center
smelting
Further Reading
Hanks, Bryan K. and Katheryn M. Linduff, eds., Social Complexities in Prehistoric Eurasia. Monuments, Metals, and Mobility. Cambridge/New York: Cambridge Univ. Press, 2009. https://doi.org/10.1017/CBO9780511605376.
Mei, Jianjun, and Thilo Rehren, eds., Metallurgy and Civilisation. Eurasia and Beyond. Proceedings of the 6th International Conference on the Beginnings of the Use of Metals and Alloys (BUMA VI). London: Archetype, 2009. http://www.worldcat.org/oclc/928997914.
Pare, C.F.E., ed., Metals Make the World Go Round. The Supply and Circulation of Metals in Bronze-Age Europe. Proceedings of a Conference Held at the University of Birmingham in June 1997. Oxford: Oxbow, 2000. http://www.worldcat.org/oclc/45870233.
Weeks, Lloyd R. Early Metallurgy of the Persian Gulf. Technology, Trade, and the Bronze Age World. Leiden/Boston: Brill, 2004. http://www.worldcat.org/oclc/1025038005.
Yener, K. Aslihan. The Domestication of Metals. The Rise of Complex Metal Industries in Anatolia. Leiden/Boston: Brill, 2000. http://www.worldcat.org/oclc/43569376.
Author Biography
Florin Curta, Ph.D. in History (1998), Western Michigan University, is Professor of Medieval History and Archaeology at the University of Florida. He has published five monographs, over 40 chapters in collections of studies, and more than 100 articles. He is also editor of six collections of studies.
- Bo Gräslund, "The background to C. J. Thomsen's Three Age System," in Towards a History of Archaeology, ed. Glyn Daniel (London: Thames & Hudson, 1981), 45–50, http://www.worldcat.org/oclc/7757964. ↵
- Lucretius, On the Nature of the Universe, trans. Ronald Melville (Oxford: Oxford Univ. Press, 1997), 173, http://www.worldcat.org/oclc/858521823. ↵
- Michel Carrier, “Ötzi: the mummy from the cold,” Arts and Cultures 5 (2004): 47–59. ↵
- Beno Rothenberg and Tim C. Shaw, “Chalcolithic and Early Bronze Age IV copper mining and smelting in the Timna Valley (Israel): excavations 1984 and 1990,” in Ancient Mining and Metallurgy in Southeast Europe. International Symposium, Donji Milanovac, May 20–26, 1990, eds. Petar Petrović and Sladana Đurdekanović (Belgrade/Bor: Archaeological Institute/Museum of Mining and Metallurgy, 1995), 281–94, http://www.worldcat.org/oclc/490516020. ↵
- Noël H. Gale, “Copper oxhide ingots and lead isotope provenancing,” in Metallurgy: Understanding How, Learning Why. Studies in Honor of James D. Muhly, eds. Philip P. Betancourt and Susan C. Ferrence (Philadelphia: INSTAP Academic Press, 2011), 213–20, https://doi.org/10.2307/j.ctt3fgvzd. ↵
- Anthony Harding, “Oxhide ingots in the European north?” Antiquity 89 (2015), no. 343, 213–23, https://doi.org/10.15184/aqy.2014.5. ↵
- James D. Muhly, “Sources of tin and the beginnings of bronze metallurgy,” American Journal of Archaeology 89, no. 2 (1985): 275–91, https://www.jstor.org/stable/504330. ↵
- Anna J. Mukherjee et al., “The Qatna lion: scientific confirmation of Baltic amber in late Bronze Age Syria,” Antiquity 82 (2008), 49–59, https://doi.org/10.1017/S0003598X00096435. ↵
- Anthony Harding, “Trade and exchange,” in The Oxford Handbook of the European Bronze Age, eds. Harry Fokkens and Anthony Harding (Oxford: Oxford Univ. Press, 2013), 377, http://www.worldcat.org/oclc/859338044. ↵
- Andreas Hauptmann, Robert Maddin, and Michael Prange, “On the structure and composition of copper and tin ingots excavated from the shipwreck at Uluburun,” Bulletin of the American Schools of Oriental Research 328 (2002): 1–30, https://doi.org/10.2307/1357777. ↵
- Noël H. Gale, “Copper oxhide ingots: their origin and their places in the Bronze Age metal trade in the Mediterranean,” in Bronze Age Trade in the Mediterranean. Papers Presented at the Conference Held at Rewley House, Oxford, in December 1989, ed. Noël H. Gale (Jonsered: Paul Åströms förlag, 1991), 197–239, http://www.worldcat.org/oclc/489688081. ↵
- Hadi Özbal, Annemie Adriaens, and Bryan Earl, “Hacınebi metal production and exchange,” Paléorient 25, no. 1 (1999): 57–65, https://doi.org/10.3406/paleo.1999.988. ↵
- Marianne Mödlinger, “European Bronze-Age cuirasses. Aspects of chronology, typology, manufacture, and usage,” Jahrbuch des Römisch-Germanischen Zentralmuseums, 59 (2012): 1–49, https://doi.org/10.11588/jrgzm.2012.1.15311. ↵
- Duncan Miller, “Smelter and smith: Iron-Age metal fabrication technology in southern Africa,” Journal of Archaeological Science 29, no. 10 (2002): 1083–1131, https://doi.org/10.1006/jasc.2001.0758. ↵