CREATING METHANE FROM CAPTURED CARBON DIOXIDE AND THE FUTURE OF CARBON CAPTURE
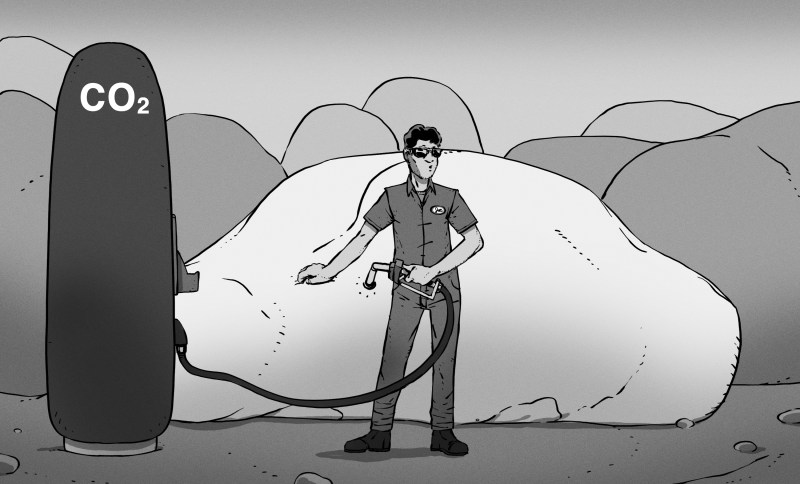
There’s something intrinsically simple about the concept of carbon (CO2) capture: you simply have the CO2 molecules absorbed or adsorbed by something, after which you separate the thus captured CO2 and put it somewhere safe. Unfortunately, in physics and chemistry what seems easy and straightforward tends to be anything but simple, let alone energy efficient. While methods for carbon capture have been around for decades, making it economically viable has always been a struggle.
This is true both for carbon capture and storage/sequestration (CCS) as well as carbon capture and utilization (CCU). Whereas the former seeks to store and ideally permanently remove (sequester) carbon from the atmosphere, the latter captures carbon dioxide for use in e.g. industrial processes.
Recently, Pacific Northwest National Laboratory (PNNL) has announced a breakthrough CCU concept, involving using a new amine-based solvent (2-EEMPA) that is supposed to be not only more efficient than e.g. the previously commonly used MEA, but also compatible with directly creating methane in the same process.
Since methane forms the major component in natural gas, might this be a way for CCU to create a carbon-neutral source of synthetic natural gas (SNG)?
CARBON CAPTURE IN A NUTSHELL
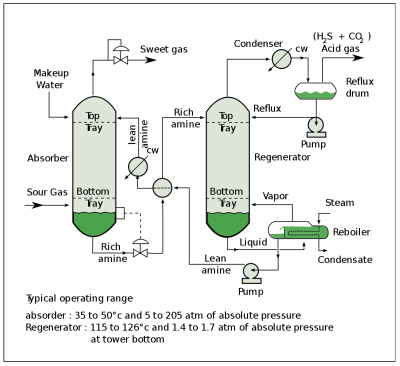
The most common type of carbon capture (CC) system is a CO2 scrubber that is used with fossil fuel power plants or similar sources of flue gas. This gas is led through the liquid solvent, typically amine-based. Amines are derivatives of ammonia, with at least one of its three hydrogen atoms having been replaced by a substituent. Monoethanolamine (C2H7NO, MEA) is a primary amine that in a water-based solution can efficiently absorb CO2 and H2S from flue gas.
When the resulting CO2 rich amine solvent is then led into a regenerator unit which heats up the rich solvent to about 118 °C at 69 kPa, it causes the absorption to be reversed and the gases to be released. Most of the MEA is recovered in this manner and can then be returned to absorb more CO2 from the flue gas.
Problems with MEA include the high water content in the solvent. Water has a high specific heat, which means it takes a lot of energy to get hot. MEA also reacts with carbonyl sulfide (COS) and carbon disulfide (CS2) to form heat-stable salts, which remove MEA from the process and require an additional process step to be removed.
After the CO2 gas has been captured this way, it is generally compressed before transport for use, storage or sequestration. The heating up of the rich amine solvent in the regeneration process, as well as the compression of the captured carbon dioxide all cost considerable amounts of energy. This is where the economics of CC are not very favorable, and prefer input gases that are already rich in the gas that is to be captured.
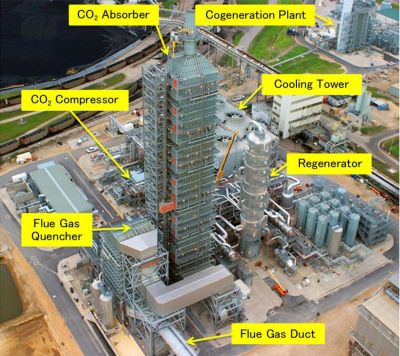
Over the years, various alternatives have been developed to MEA which require less water, and processes that omit or reduce the compression step. Examples of the former are for example Shell’s Cansolv capture technology and Mitsubishi Heavy Industry’s KM CDR process with its proprietary KS-1 solvent. These all have the same goals: use less water, reduce the amount of amine solvent caught in the flue gas that’s emitted into the atmosphere and improvement of the recovery rate of the solvent while reducing energy requirements.
None of these processes are suitable for something like direct air CCS, though. Although one can technically lead atmospheric air through one of these capture plants, the difference in CO2 content in the air versus flue gas is immensely different (>9% in flue gas versus 0.04% in air), leading to a very low efficiency rating.
Even so, with flue gas the capture rate of CO2 is generally above 90%, but <99% (claimed 98% for Cansolv, >90% for KM CDR). This means that although most of the CO2 is indeed captured, some of it still is emitted with the flue gas, along with amine solvents.
PNNL’S 2-EEMPA
In PNNL’s paper by Heldebrant et al. (2021) titled Integrated Capture and Conversion of CO2 to Methane using a Water-lean, Post-Combustion CO2 Capture Solvent a number of claims are made:
- >90% conversion of captured CO2 to hydrocarbons (mostly methane).
- More efficient than the usual Sabatier process (skipping the CO2 compression & transport steps).
- Process conditions are 170 °C and <15 bar H2 pressure with ruthenium catalyst.
- Better performance of 2-EEMPA than MEA.
There are a number of steps involved in this process, from absorbing the CO2, to getting it to the point where it can react with the hydrogen that is added to create the hydrocarbons. Heldebrant et al. first describe the Sabatier process, using a combined cycle natural gas turbine plant equipped with Shell’s Cansolv (using a 50% by weight amine solvent) process as example:
- CO2 captured in the absorber & released in the stripper (regenerator) at 2 bars of pressure.
- Pure CO2 is compressed and mixed with hydrogen.
- Mixture is added to methanation reactor for the Sabatier reaction.
- The Sabatier reaction runs at 350 °C and 30 bar with an Ru/Al2O3 catalyst.
- The exothermic reaction provides heat for the stripper unit and power generation.
The PNNL version does not use the proprietary Cansolv process, but instead its own 2-EEMPA (N-(2-ethoxyethyl)-3-morpholinopropan-1-amine). Heldebrant et al. claim a CO2 capture efficiency of >95% with coal-derived flue gas. 2-EEMPA-based solvent is projected to have a ~4% water content by weight in operation. At this water ratio, 74% of the CO2 captured by 2-EEMPA (as EEMPA-carbamate) is converted to hydrocarbons when hydrogen is introduced and with an Ru/Al2O3 catalyst present. Of these, 92% of these were methane.
At the same conditions, MEA showed a conversion ratio to hydrocarbons of <20%. The entire process chain can be summarized as in the following graphic:
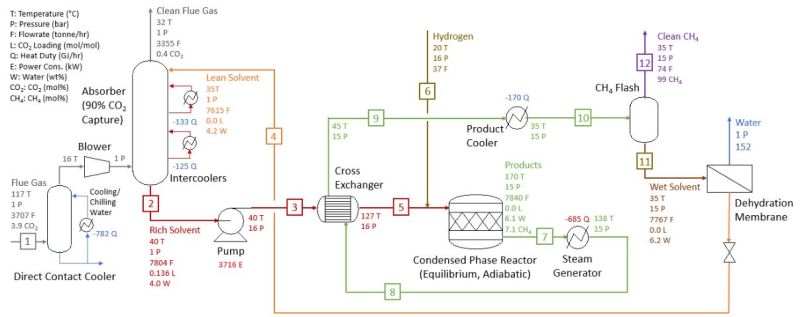
The benefits compared to the traditional Sabatier process are a lower reaction temperature (170 °C instead of 350 °C), lower pressure (15 vs 30 bar) and lower cost for constructing and maintaining the equipment.
A STORY OF EXTERNAL FACTORS
As alluded to earlier in this article, a major consideration with carbon capture is the efficiency of the process. If we consider that CCU as proposed here relies on a rich source of CO2, as well as a pure source of hydrogen, it would appear that the former would have to come from flue gas and similar waste streams from the fossil fuel industry. For the latter, things are more problematic if we wish to not create additional waste.
Currently virtually all hydrogen on the market is produced through steam reforming (SMR) of natural gas. This makes it not carbon-neutral: if it requires natural gas as input for SMR to create the hydrogen needed to create the SNG, one may as well directly use the natural gas.
This is further illuminated by Howarth et al., whose recent study details the effectiveness of so-called ‘blue hydrogen’, which uses CCS with SMR of NG and came to the conclusion that it’s more effective to just burn the NG directly. This leaves then only so-called ‘green’ hydrogen as viable input for this SNG process to conceivably make it carbon-neutral.
In 2020, only 4% of worldwide hydrogen was produced via electrolysis, some of it from low-carbon power sources. Even if all hydrogen at these SNG production facilities came from electrolysis facilities powered by VRE or nuclear power, that would still leave the CO2 as an issue. If this came from fossil fuels, then it merely postpones the moment this carbon enters the atmosphere to when the SNG is burned.
True carbon-neutral fuel is conceivable, but so far no viable source of carbon has been found. Carbon from flue gas costs about $7.5 per ton, extracting carbon from sea water as carbonic acid would cost about $50 per ton and direct air carbon capture between $94 and $232 per ton. This then leaves PNNL’s process primarily as a way to use the carbon from fossil fuels (coal or NG) twice, though at a considerable energy investment.
NO FREE LUNCH
In light of these considerations and also based on PNNL’s own press release, it would seem clear that the ability to generate methane using this method is mostly transitional, to support the transition to low-carbon ways to power the modern world. The only likely exception to this is probably extra-terrestrial exploration, where in-situ resource utilization (ISRU) is likely to become a big thing.
One of the reason why SpaceX’s Mars-bound Raptor rocket engines are methane-fueled is due to the relative ease with which methane can be produced even on locations like the surface of Mars. When the nearest source of terrestrial methane is suddenly a planet away, the electrical and others costs of even DACC and electrolysis of water to slowly create a trickle of methane fuel for the trip back or to sustain a colony do not seem as outrageous any more.
One major benefit of water-lean solvents like 2-EEMPA is also likely to be the more efficient capturing of CO2 at fossil fuel plants. Whether this is enough to make big players like MHI and Shell sit up and pay attention is still anyone’s guess, but it’s hard to deny the benefit of more efficient CCS at fossil fuel plants.
No comments:
Post a Comment