The life-or-death race to improve carbon capture
The technology works, but we’ll need better chemistry and engineering to reach the scale required to avoid a climate disaster
by Craig Bettenhausen
July 18, 2021 | A version of this story appeared in Volume 99, Issue 26
Credit: National Carbon Capture Center | A solvent tower at the National Carbon Capture Center, a research facility near Birmingham, Alabama
Carbon capture isn’t about saving Earth. Earth is a wet rock floating through space; it doesn’t care if we drown our coastal cities or turn our farmland into desert. Rather, carbon capture is one of the technologies we will need if we want Earth to continue to be a tolerable place for humans to live.
IN BRIEF
The carbon-capture chemistry we have today is too expensive. It works, and it makes economic sense in a few settings. But to meet the global-consensus goal of net-zero carbon dioxide emissions by 2050 and dodge the worst consequences of climate change, we need to deploy more than 150 times as much carbon-capture capacity as we have now. That means reducing costs and making more options available for a wide range of CO2 emission sources. Read on about the growing number of businesses, government labs, nonprofits, and academic researchers racing to bring the next generation of carbon-capture technology up to scale and into the market.
In 2020, we sent 40 billion metric tons (t) of carbon dioxide into Earth’s atmosphere. We need to cut that number to 0 by 2050 if we are to avoid the worst consequences of climate change, according to the Intergovernmental Panel on Climate Change (IPCC). If we don’t, the natural systems that keep Earth’s climate relatively peaceful and comfortable will start to tip. The shift will be chaotic, and the new normal might not be conducive to life as we know it.
To reach net-zero CO2 emissions by 2050, we need an all-of-the-above approach. Efficiency improvements can reduce our energy needs, and renewable and nuclear power may eventually be able to supply enough electricity for our homes, offices, and cars. But nuclear power is expensive and lacks public support, and renewables are struggling to find the land they need to be deployed at scale. On top of that, activities such as aviation and iron smelting are currently impossible to carry out commercially without releasing CO2.
That’s where carbon capture comes in. Removing carbon dioxide from point sources such as the flue gas of power plants and locking it away underground can be a big part of the path to net zero. Related technologies known as direct air capture can remove CO2 that is already in the ambient air. But all of it depends on carbon capture getting a lot bigger, cheaper, and more efficient—and doing so quickly.
SLOW START
Capturing the CO2 from power plants’ flue gas is where most of the action is. “Decarbonization of the power sector becomes the backbone that the decarbonization of the rest of the economy happens on,” says John Northington, director of the National Carbon Capture Center, a research facility near Birmingham, Alabama.
WHAT’S YOUR GAS STREAM?
Different emission sources require different carbon-capture methods.
Ammonia, ethanol, natural gas processing: Emit gas streams with more than 80% CO2. The CO2 is captured with compression and dehydration, membranes, or physical solvents.
Chemical plants, iron, steel and paper mills: Emit gas streams with 15–80% CO2. The CO2 can be captured with physical solvents, solid sorbents, or membranes.
Coal and natural gas power plants and boilers: Emit gas streams with less than 15% CO2. The CO2 can be captured with chemical solvents.
Ambient air: Has a CO2 concentration around 0.041%. The CO2 can be captured with metal-organic frameworks or chemical systems.
Sources: Global CCS Institute, National Petroleum Council.
But just one commercial power plant has carbon capture: the coal-fired Boundary Dam Power Station in Saskatchewan, which captures 1 million t of CO2 per year on one of its four generators. Carbon capture elsewhere on other industrial processes, such as natural gas production, adds another 27 plants and gathers 25 million t per year. Not nearly enough.
The people developing the technology that will make capturing carbon practical have gained unlikely allies in the past couple of years: the oil and gas companies responsible for the lion’s share of CO2 emissions. Though these firms have had their eyes on carbon capture for some time, Northington says, they’re investing serious money in it now.
Data from the patent research firm Patent Seekers bear that notion out. Oil companies have gotten the largest number of carbon-capture patents in recent years, followed by government agencies and research institutes, universities, and engineering and technology companies.
Klaus Lackner, an engineering professor working on direct air capture at Arizona State University, says the change in attitude is a result of pressure from two directions: competition from cheap renewable energy and public demand for low-carbon options. Major changes are coming to the energy market, Lackner says. “The question isn’t ‘Will we have a transition?’ We will. The Exxons and Shells and other companies have to figure out how to make it through that transition. Their business model falls apart if you can’t have liquid fuels.”
Lackner says he’s been pushing fossil fuel companies on this point for years, telling them, “Your societal license to dump CO2 into the air will go away. You need to figure out how to operate without needing that license.”
Matt Steyn, a senior adviser with the advocacy wing of the Global CCS Institute (GCCSI), a carbon-capture-and-storage think tank, says the change is also driven by the scientific consensus expressed by the IPCC and the International Energy Agency. “The target has been set; the timeline has been set,” he says. The conversation has shifted from “What do we do?” to “How do we do it?”
As we deploy more plants, costs will come down, just as they have done in every other sector.
Steve Oldham, CEO, Carbon Engineering
Carbon capture of all types is a gas-separation problem. The goal is pure CO2, ideally at high pressure so it can go into a pipeline and be injected safely underground. For some industrial processes, the capture technology available today works fine. In ammonia and corn ethanol plants, for example, the gas exiting exhaust pipes is 80% or more CO2 and just needs to be dried and compressed for transport.
As the CO2 in emissions gets more dilute, the energy required to extract it rises. The emissions coming from steel plants and many chemical processes tend to be between 15 and 80% CO2. The flue gas from fossil fuel combustion in air, such as in coal or natural gas–fired power plants, is generally less than 15% CO2.
CAPTURE WITH SOLVENTS
Carbon dioxide–rich flue gas flows up a contact tower and mixes with a solvent that is trickling down (left). Reduced-CO₂ gas vents from the top, while CO₂-rich solvent exits at the bottom and flows to the top of a stripping tower. There, the solvent is heated, usually by steam, as it trickles down. The heat forces the CO₂ out of solution and up to a collection system. The refreshed solvent heads back to the contact tower to start again
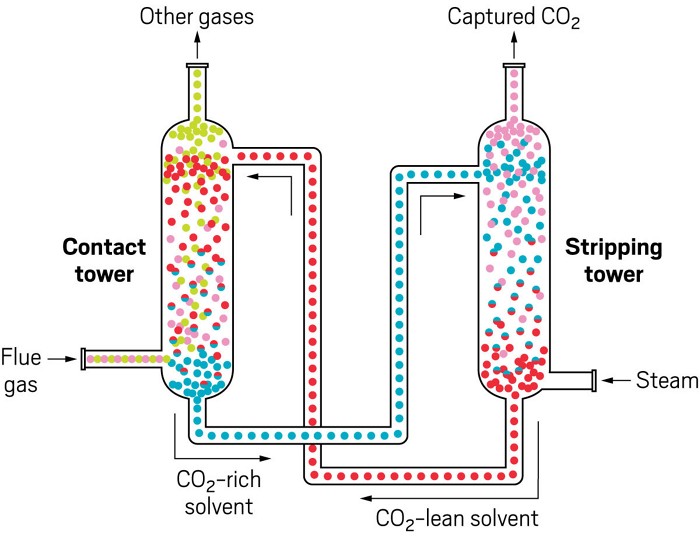
Credit: Adapted from CO2CRC
Ironically, oil companies are some of the biggest practitioners of carbon capture today because they use solvents, membranes, and other technologies to remove CO2 from natural gas deposits found in locations such as Russia and west Texas. When they use or sell that CO2 instead of venting it, that counts as carbon capture. That’s why ExxonMobil can claim to capture more CO2 than any other company, even if it uses most of that to push more oil out of the ground.
Amine-based extraction systems developed for natural gas processing have been adapted for other CO2 sources, such as the power plant in Saskatchewan, but the energy cost of using such systems on more dilute streams is crushingly high. Second-generation solvent systems are poised to come to market next, followed by membranes and solid sorbents. And numerous innovative and experimental approaches are racing to catch up.
Syrie Crouch, vice president for carbon capture and storage at Shell, which built the Saskatchewan plant, says deploying capture where it’s simple is an important start. US ethanol makers, for example, capture only 3 million t of the 43 million t of CO2 their plants produce each year. “The key is to capture that lowest-hanging fruit first and then work on down the cost curve,” she says.
INCUMBENT AMINES
The most mature carbon-capture technologies today use solvents. These systems pump emissions through a solution that absorbs CO2 but lets through other gases, such as nitrogen. The CO2-rich solvent then flows into a boiler, where heat drives the pure CO2 back out of solution. That stripping step is the energy hog.
Though the terminology is harsh to a chemist’s ears, carbon-capture solvents are considered either chemical or physical. Chemical solvents, mostly amines such as the industry standard 30% monoethanolamine in water, get a CO2-solubility boost through reversible chemical reactions with water and CO2 that form carbonates, bicarbonates, and carbamates.
Physical solvents such as methanol rely on intermolecular interactions to dissolve CO2. Companies including Linde, Air Products, and UOP offer such systems commercially. They use less energy than chemical solvents but require high pressures and low temperatures. They’re not suitable for combustion flue gas but have been used for many years to remove CO2 from natural gas.
ALMOST LIKE A FILTER
Membranes separate gas mixtures on the basis of size or chemical properties. Some molecules can pass through, and others cannot.
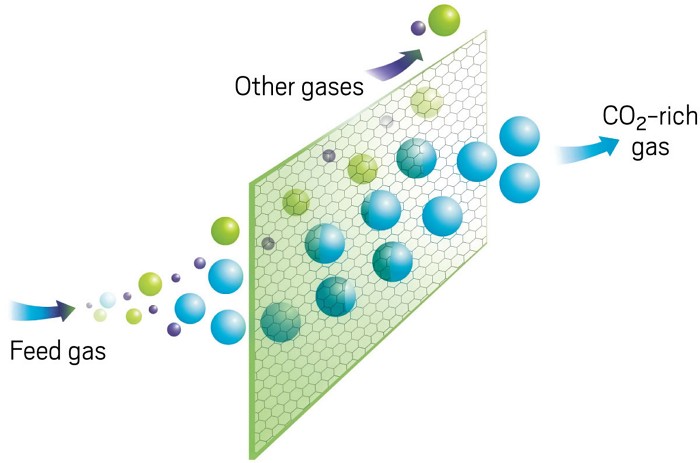
Credit: Adapted from CO2CRC
Amine solvents have the advantage of being mature technology. The systems are well understood, with well-characterized economics and risk profiles that investors know how to analyze. Dow, Shell, Fluor, and others offer monoethanolamine solutions for carbon capture. Boundary Dam Unit 3 uses amines, as did NRG Energy’s Petra Nova plant in Texas, which captured more than 1 million t of CO2 per year from 2017 until NRG shut it down in 2020.
BASF, Linde, General Electric, and the start-up Carbon Clean are among those working on advanced amines. These systems use chemicals such as piperazine alongside or instead of monoethanolamine to get better stability, kinetics, and thermodynamics. The US Department of Energy recently awarded Linde and the University of Illinois at Urbana-Champaign $47 million to build a 200 t per day pilot facility using an advanced amine solvent from BASF at a coal-fired power plant near Springfield, Illinois.
But capturing CO2 with amines comes at a steep cost. Fitted onto a power plant’s systems, they consume 30–50% of the plant’s energy output. Most experts, including Shell’s Crouch, expect that amine systems can get only 10–20% more efficient. At the same time, amines can seem like a safe bet compared with a next-generation technology. “If you’re making your first investment in carbon capture and storage, you don’t necessarily want to be taking massive risks on something new and untested,” the GCCSI’s Steyn says.
THE NEXT GENERATION
At the National Carbon Capture Center (NCCC) and the Wyoming Integrated Test Center (ITC), two next-generation carbon-capture technologies that look promising are solid sorbents and membranes.

Credit: Saipem
CO2 Solutions, now part of Saipem, engineered carbonic anhydrase to fit the demands of carbon capture.
The NCCC and ITC sites are essentially coal-fired power plants that can pipe their flue gas into a series of testing bays. The NCCC tests systems at scales from less than 1 t per day up to about 25 t per day; tests at the ITC run between 25 and 450 t per day. The sites, which use a combination of public and private financing, serve as technology development bridges between lab-scale carbon-capture concepts and pilot-scale tests on commercial power plants.
The NCCC’s Northington says the incumbent amine systems can capture carbon at a cost of $60–$65 per metric ton. Advanced amines and other second-generation solvents are about $40 per metric ton. A handful of commercial installations that will use advanced amines are in early-stage engineering now, he says. Solid sorbents, membranes, and other transformational technologies will reach $30 or less per metric ton, he predicts.
“We want choice in the marketplace,” says William Morris, technical director of the ITC. “People are really trying to figure out what works for them, not only in their industry but in their specific circumstance.”
Solid sorbents include zeolites, metal-organic frameworks (MOFs), activated carbon, and porous silica particles. They’re often functionalized with amine groups to increase their activity and make them more selective for CO2.
MERRY-GO-ROUND
In Svante's solid-sorbent capture system, flue gas first flows down (left) through a rotating disk loaded with a sorbent material that removes the carbon dioxide. At the next station (right), steam flows through the sorbent, stripping the now-pure CO2 out for collection. A third station (rear) refreshes the sorbent on the way back around to the flue gas station.
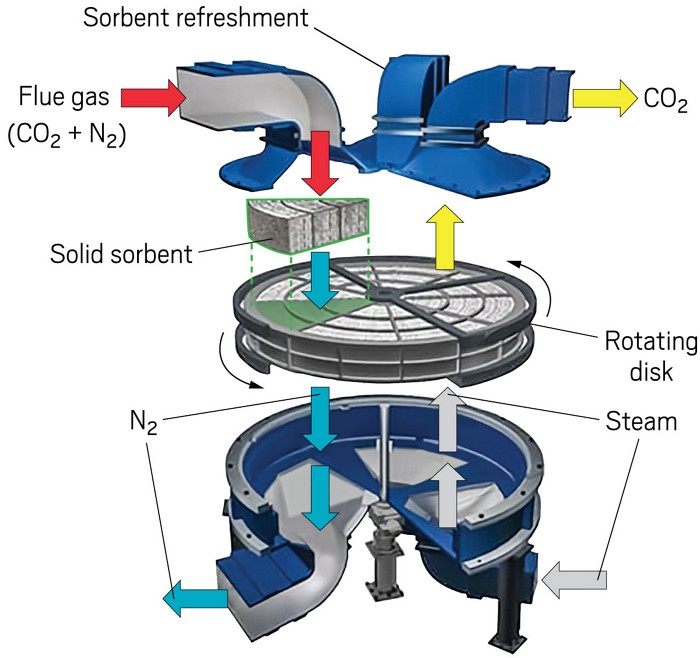
Credit: Svante
Generally, solid sorbents have faster absorption kinetics than amines and require less energy to release the CO2 again. They can also hold more CO2 per unit volume than most solvents. That means that solid-sorbent systems can be smaller, reducing capital costs, and can be stripped of their CO2 using vacuum or modest heat.
The start-up Svante forms solid sorbents into large, nanoporous disks divided into slices like a pizza. On a giant turntable, the disk slowly rotates each slice through a flue gas stream, a CO2-stripping module, and one or two sorbent preparation stations. The firm has a 10,000 t per year demonstration plant on a natural gas–fired boiler in Canada. It raised $75 million in February to advance a design for cement plants.
In addition to Svante, ExxonMobil, Kawasaki Heavy Industries, TDA Research, and others are testing solid-sorbent systems for flue gas capture. Shell, which is shifting its R&D to solid sorbents, tested a system that uses amine-functionalized solid sorbents on a wood-burning power plant in Austria; it is now readying a scaled-up test at a manure-to-power plant in the Netherlands. After these trials, Crouch says, Shell will offer the technology on the open market.
Membranes are even further along than solid sorbents, Morris says. Membrane systems use selectively permeable materials that exploit the small chemical and physical differences between CO2 and the rest of a gas mixture to achieve separation. Like amines, membranes are already being used in natural gas processing and other areas where CO2 pressure and content are high.
“The next technology outside of amines that will deploy will be membranes,” Morris predicts. He says membranes are coming fast for capturing CO2 from flue gas at power plants. And Northington expects membranes will play a big role in carbon capture for the chemical industry and heavy manufacturing, which have moderate to high CO2 concentrations.
Getting any new carbon capture technology to market won’t be cheap. Morris says getting a robust set of data from testing at the ITC can cost seven figures. One membrane maker, Membrane Technology and Research (MTR), won $52 million in funding in May from the US Department of Energy to do just that. MTR ran a 20 t per day version of its system for 1,400 h at the NCCC in 2015 and will use the funds to scale it up to 150 t per day in Wyoming. The company expects to demonstrate capture at less than $40 per metric ton.
MTR’s membrane polymers are isoporous, meaning their pores are uniform in size and arranged geometrically, unlike the randomly arranged, multisize pores in most gas-separation membranes. The regular pore pattern lets molecules flow more smoothly through the material, lowering the amount of pressure needed relative to conventional membranes. And a tighter distribution of pore sizes increases selectivity for CO2.
Another membrane maker, Compact Membrane Systems (CMS), also seeks to decrease costs by reducing pressure. CMS uses facilitated transport membranes, which are specialized fluoropolymers coated onto a porous substrate. CEO Erica Nemser likens the mechanism to Tarzan swinging through the jungle on vines. The CO2 is Tarzan, and fluoropolymers decorated with activating groups act as the vines, passing CO2 along, with minimal pressure needed.
The firm’s systems are already being used to separate olefins from paraffins and to remove water and dissolved gases from solvents, oils, and lubricants. The system that will capture CO2 in flue gas will be a modification of one that’s in field trials now for removing CO2 from biomethane. Chemical changes to the fluoropolymer make the membrane selective toward different chemical species, Nemser says.
CMS’s units are built around membrane cartridges about twice the size of a can of spray paint—hence the “compact” in the company’s name. The bigger the gas stream to be treated, the more cartridges the system uses. Chief Technology Officer Hannah Murnen says such modular systems will make carbon capture accessible for a wide range of CO2 point sources. In contrast, the towers needed to mix amine solvents with a gas stream and strip the CO2 out later make economic sense only at enormous scales, she says.
CMS says it will be able to deliver carbon capture for as little as $20 per metric ton. “It’s time for membranes. It’s membranes’ day in the sun,” Murnen says.
TOMORROW’S TECH
Amines may dominate carbon capture today, and membranes and solid sorbents may be right on their heels, but a need this serious—and a market this big—is attracting plenty of other contenders. And a good-enough concept could leap ahead if the people behind it can show it works and is scalable.
Saipem and Chart Industries both hope to adapt technology and equipment already in use in other chemical processes.
In January 2020, Saipem, an energy technology and engineering firm, acquired CO2 Solutions, a start-up that is using enzymes to boost the carbon-capture kinetics of aqueous potassium carbonate. K2CO3 reacts with CO2 and water to form potassium bicarbonate, KHCO3. The bicarbonate solution releases its CO2 at relatively low temperatures—around 75 °C under reduced pressure—meaning it can tap low-grade heat that most industrial processes would waste.
That chemistry has been used to scrub CO2 from the air in submarines and other closed environments and in some high-CO2-concentration settings. The trouble is that the absorption kinetics are too slow for it to work well at flue gas concentrations and pressures; the contact towers would have to be even bigger than those used with amines.
To solve that problem, Saipem catalyzes the reaction with the enzyme carbonic anhydrase. Natural carbonic anhydrase is already one of the fastest enzymes, speeding up the formation of HCO3– by a factor of 107. The team at CO2 Solutions modified the enzyme to make it even faster and keep it active at higher temperatures.
“The first time I saw carbon capture with the enzyme, my jaw just dropped, because the catalyst is magic,” says Richard Surprenant, who came to Saipem from CO2 Solutions and is now commercial manager for carbon-capture technologies.
Any industrial or postcombustion application is fair game for the firm’s technology, Surprenant says, and anywhere with low-grade waste or geothermal heat is an opportunity, because it doesn’t need the high-grade heat, a resource many plants already use in other ways. The firm is in the midst of restarting CO2 Solutions’ first commercial plant, a 30 t per day facility in Quebec that extracts CO2 from a paper mill and sells it to a nearby greenhouse.
Chart Industries, an energy and industrial gas equipment firm, is also moving into carbon capture through acquisition and investment. In late 2020, Chart acquired Sustainable Energy Solutions, a start-up making cryogenic carbon-capture systems for combustion flue gas. In June of this year, it invested in Earthly Labs, which uses cryogenics to capture CO2 from breweries.
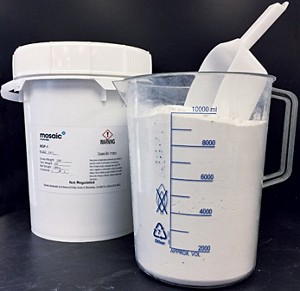
Credit: Mosaic Materials
Mosaic Materials' carbon-capturing metal-organic frameworks.
In the simplest terms, both cryogenic systems chill their target gas streams until the CO2 condenses into a solid or liquid. Nitrogen, still a gas at those temperatures, is pumped off. The basic process, often called cryogenic distillation, is already used to purify other industrial gases, such as oxygen and nitrogen.
The challenge for flue gas is in the engineering, not the chemistry, according to Chart CEO Jill Evanko. If water and CO2 freeze in the wrong places, they can clog pipes and block heat exchangers. But with clever heat management, system design, and integration with the rest of the equipment, Chart and its partners can deliver carbon capture of flue gas at half the cost of conventional amines, Evanko says, and make brewery carbon capture profitable enough to pay off the equipment in 18 months.
Several other technologies are in early-stage development. Solvents that use less water or no water at all, including organic solvents and ionic liquids, could reduce the amount of mass that needs to be heated to release the purified CO2. Allam cycle power plants burn hydrocarbons in a mix of O2 and CO2, sidestepping the need to separate CO2 from nitrogen. And FuelCell Energy is commercializing its molten carbonate fuel cell, which can capture flue gas carbon while generating additional electricity from natural gas.
It’s an exciting time for technology development, the ITC’s Morris says. “Decarbonization is going to be very, very difficult, and it’s probably not going to be possible without technologies that are currently in the development stage.”
STATE OF PLAY
Carbon capture is in its early days, especially for combustion flue gas, such as the emissions of a coal-fired power plant. Researchers are working on each of the technologies below to make them cheaper and more efficient and to get them to work on a wider variety of gas streams. A single commercial-scale installation could let a new technology pass its competitors or even take the lead.

Sources: Global CCS Institute, National Petroleum Council, International Energy Agency, C&EN reporting.
DIRECT AIR CAPTURE
Point-source carbon capture won’t be enough. The technology still lets 2–10% of the carbon through. And it’s hard to deploy on sources with diffuse or mobile emissions, such as airplanes, sprawling petrochemical plants, and wide-open wastewater treatment facilities. Besides, the atmosphere has too much carbon already. The goal of net-zero CO2 emissions will require methods to remove carbon from the air.
This direct air capture, or DAC, works on chemical principles similar to those for point-source capture. The big difference is that our ambient air, although overloaded, is still only 410 ppm, or 0.041%, CO2, much lower than even the most dilute industrial point sources. And that changes a lot about the devices and their economics.
Because flue gas and other point sources are releasing new carbon into the atmosphere, the goal is to capture as much of it as possible—90% is a common target. In DAC, the amount of carbon left behind isn’t important; it’s all about how much CO2 can be removed per dollar spent. “My goal is not to make CO2-free air. My goal is to take CO2 out of the air, and I can choose where the optimal efficiency is,” says Lackner, the Arizona State engineer, who is also developing DAC technology.
But however you look at it, DAC is expensive. Carbon capture at an ethanol plant can cost as little as $10 per metric ton. At a coal-fired power plant, the cost is around $60. DAC companies don’t like to talk about their costs, but industry insiders estimate they are around $500 per metric ton. Lackner and other experts generally peg $100 as the point at which DAC will become cost competitive with other decarbonization methods.
Oxy Low Carbon Ventures, a carbon-reduction subsidiary of Occidental Petroleum, thinks it can reach that level in partnership with the start-up Carbon Engineering. The firms plan to build in the southwestern US what they say will be the world’s first commercial-scale DAC plant. It will capture 1 million t of CO2 per year, to be used mainly to boost production in Occidental’s oil wells in the region. The largest existing DAC plant captures a mere 2,000 t per year, according to Ryan Edwards, low-carbon policy adviser for Oxy Low Carbon.
Carbon Engineering uses chemical looping to capture carbon from the air. In its process, intended to run on renewable energy, giant fans blow air over plastic surfaces that have aqueous potassium hydroxide flowing over it.
The KOH reacts with CO2 to form potassium carbonate, K2CO3, which then flows into a pellet reactor containing aqueous calcium hydroxide, Ca(OH)2. The calcium and potassium switch places to form CaCO3, which precipitates out as solid pellets, as well as KOH, which is ready to cycle back to the plastic surfaces. The pellets then pass into a calciner, a heater that decomposes the CaCO3 into solid CaO and pure CO2. The CO2 is cooled and pressurized, and the CaO heads back to the pellet reactor, where it mixes with water and re-forms Ca(OH)2.
The system sounds complicated, but it’s built mostly out of reactions and equipment already in use in industry. The pellet reactor is adapted from papermaking. Calciners running the same chemical reaction are central to cement production, and other versions come into play in glass, uranium, petroleum coke, and gypsum processing.

Credit: Wyoming ITC
The Dry Fork power station in Wyoming sends some of its flue gas to the Wyoming Integrated Test Center, where users test new carbon-capture technologies.
Carbon Engineering published its process in 2018, projecting costs between $94 and $232 per metric ton (Joule, DOI: 10.1016/j.joule.2018.05.006). CEO Steve Oldham says the firm is “extremely confident” its costs will be in that range and expects that second and third generations will ensure a cost of $100 or less. “As we deploy more plants, costs will come down, just as they have done in every other sector,” Oldham says.
Mosaic Materials, a developer of MOFs and one of C&EN’s 10 Start-Ups to Watch in 2019, pivoted to DAC from point-source capture 2 years ago, according to CEO Thomas McDonald. In the past 3 months, McDonald says, he’s seen a sharp increase in interest in DAC.
The firm’s MOFs use a flavor of CO2-amine chemistry that McDonald calls cooperative binding, in which the CO2 inserts itself between a magnesium ion and an amine ligand. The mechanism gives the material high capacity and fast kinetics, and it reverses at relatively low temperatures to release the CO2, according to McDonald.
MOFs are more expensive than other solid sorbents such as silica or activated carbon. Mosaic researchers are working to improve the materials’ capacity and stability to reduce operating costs, McDonald says. But the firm is focused more on lowering manufacturing costs and optimizing complete systems around its materials.
Mosaic worked with ExxonMobil on flue gas capture in 2017 and 2018 and has some ongoing work in that area, along with collaborations with NASA and the US Navy on life-support systems, McDonald says. But he sees DAC as the best way to build his company. “We see the fastest, least-capital-intensive, least-risky path is by achieving early scale on projects through direct air capture.”
We will require something roughly the size of the current oil and gas industry, but with the molecules going in reverse.
Syrie Crouch, vice president for carbon capture and storage, Shell
Lackner says DAC is a good fit with renewable energy. If a natural gas power plant is off because of low demand, so is any point-source carbon-capture device attached to it. DAC, on the other hand, can run on renewable energy and stabilize electricity prices by being a customer of last resort.
In addition to his academic work, Lackner is working to commercialize his own DAC concept, which he calls MechanicalTrees. The “trees” eliminate the cost of running fans by relying on wind to move air across sorbents loaded onto disks arranged in a tower. When saturated with CO2, the towers drop into a chamber where heat and vacuum remove the CO2 at roughly 95% concentration.
PAYING FOR IT
All cool ideas, but who’s putting up the cash? A provision of the US tax code called 45Q offers tax credits for capturing carbon. When the provision is fully in place in 2026, carbon that is captured and sequestered will be worth $50 per metric ton. CO2 used to extract more hydrocarbons, a widespread and controversial practice called enhanced oil recovery, gets $35.
That $35 credit plus the $40 per metric ton that enhanced oil recovery operators pay for CO2 on average make that market the most profitable for non-food-grade CO2, even with the lower credit (Front. Clim. 2019, DOI: 10.3389/fclim.2019.00005).
That makes the economic rationale for carbon-capture products dependent on the price of oil. That dynamic is what doomed the Petra Nova carbon-capture facility when the price of oil got too low during the pandemic. Still, Oxy Low Carbon executives are prepared to depend on enhanced oil recovery for their southwestern US DAC project.
Despite such bumps, carbon capture offers a way to decarbonize combustion and other CO2-emitting processes so they can remain part of a net-zero world. That’s both a selling point and a point of criticism. Critics such as Greenpeace say carbon capture diverts resources away from renewables and keeps polluters in business.
Your societal license to dump CO2 into the air will go away. You need to figure out how to operate without needing that license.
Klaus Lackner, engineer, Arizona State University
Critics also point out that almost all the CO2 captured to date has been used in enhanced oil recovery. In the best cases, enough CO2 stays permanently in the ground after such oil extraction that the resulting fuel has net-negative CO2 emissions. But many enhanced oil recovery projects don’t meet that goal (Energies 2019, DOI: 10.3390/en12030448).
“To put it very brutally, in the beginning, I don’t care” where the captured CO2 goes, Lackner says. The technology needs to start scaling up now. He points to a recent report from the International Energy Agency detailing a path to net zero by 2050. In that scenario, point-source capture has to scale up from about 40 million t per year today to 6.6 billion t in 2050, and DAC has to grow from a few thousand metric tons per year to almost 1 billion t in 2050.
If enhanced oil recovery operators are willing to be early adopters that get carbon capture down to a cost that the market will bear, Lackner says, that’ll have to do. “The only way you get there is by learning. Most industries gain 10–20% in cost reduction for every doubling of cumulative output,” he says. “If we follow normal learning curves, I’m allowed to be optimistic. If it turns out we derail from that, the sooner we know, the better off we are.”
Shell’s Crouch agrees that industry needs to start deploying carbon capture now to reach the necessary scale. “We will require something roughly the size of the current oil and gas industry, but with the molecules going in reverse,” she says.
Building all those plants will cost $655 billion to $1,280 billion over the next 3 decades, according to a recent analysis by the GCCSI. That’s a lot of money, but Brad Page, CEO of the GCCSI, points out in a press release that “investing around one trillion dollars over almost 30 years is well within the capacity of the private sector which invested almost two trillion dollars in the energy sector in 2018 alone. Government decisions hold the key to enabling the requisite private sector capital being allocated for [carbon capture and storage] deployment.”
One proposal the US Congress is considering now would add a higher credit for carbon captured from the air. The idea has broad bipartisan support, according to Oxy Low Carbon’s Edwards. At a recent panel discussion hosted by the nonprofit OurEnergyPolicy, he expressed confidence that enhanced incentives, R&D and deployment support, and funding for infrastructure for CO2 transport and storage could all become law in the current session of Congress.
Jeremy Harrell, the managing director for policy at the energy-transition nonprofit ClearPath and another OurEnergyPolicy panelist, said he expects the Biden administration to launch a 50:50 cost-sharing initiative to deploy a first wave of carbon-capture facilities. “We think that sends a really important market signal to the private sector as they look to invest in these technologies,” he said at the event. “The politics here are going to play out well over the next 18 months, and people should stay tuned.”
The administration’s proposed budget for the next fiscal year includes a 61% increase in spending at the Department of Energy on carbon capture, use, and storage, though the $368 million total is far short of what many climate activists would like to see.
Edwards says 45Q has opened the door to commercial-scale carbon-capture projects. Since Congress extended 45Q in 2018 and removed the cap on the number of credits available, 30 to 40 new projects have been publicly proposed, he says, which would more than double the global number. Between projects that are being kept quiet for now and new ones that will be unlocked if Congress expands 45Q, that increase is “just the tip of the iceberg,” Edwards says.
It’ll need to be. Right now, 28 point-source capture and DAC plants are active, including at Boundary Dam and nonpower installations, according to the GCCSI. The world will need 2,000 large facilities by 2050, along with transportation and storage infrastructure, to reach net zero by then.
“The reality is, we’ve only got a certain amount of time left,” the GCCSI’s Steyn says. “We’re now pushing against the clock.” Considering how long it takes to finance, engineer, and build a trillion dollars of industrial equipment, he says, “If you’re going to actually make inroads toward net-zero 2050, it’s got to happen this decade. This is the make-or-break decade.”
Chemical & Engineering News
ISSN 0009-2347
Copyright © 2021 American Chemical Society