by New Jersey Institute of Technology
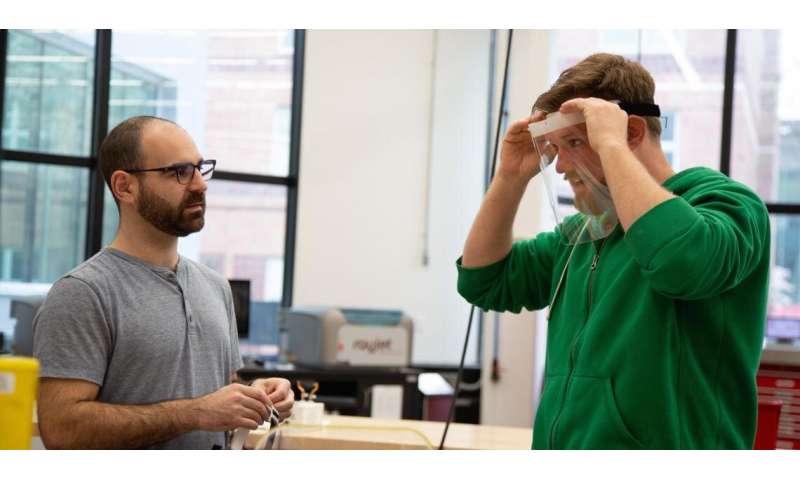
Justin Suriano and Daniel Brateris try on a face shield they designed and fabricated in the Makerspace at NJIT. Credit: New Jersey Institute of Technology
As emergency response teams in the region scramble to acquire dwindling medical supplies to combat the surge in COVID-19 (coronavirus) infections, diverse members of the New Jersey Institute of Technology (NJIT) community—from engineers to physicists to advanced manufacturing specialists to students—are designing and fabricating devices to help address the shortfall.
After consulting with emergency room physicians on specifications, a team in the Makerspace at NJIT designed and manufactured a prototype of a face shield that can be used by various emergency workers. The front of the mask is a long piece of clear polycarbonate plastic, while the frame is made from HDPE plastic—the material used in plastic milk bottles—which pathogens have difficulty clinging to. The shield covers most of the face and is held in place by a simple strap. It can withstand even industrial grade cleansers.
"Our goal was to build something as cleanly as possible that is easily sanitized and reusable," said Daniel Brateris, director of experiential learning at NJIT's Newark College of Engineering (NCE). Cutting the masks with lasers from sheets of plastic, rather than 3-D-printing them, allowed the effort to avoid the "little cavities that develop when objects are built up layer by layer," he said.
By early April, the team plans to send a batch of 100 shields, put together in safely spaced assembly lines, to New Jersey state agencies for testing. While requests for supplies have begun flowing in at a steady clip, NJIT didn't wait for them, said Moshe Kam, NCE's dean.
"We have the capability, so we started to work on designs, make prototypes and see who could use them," Kam said, adding, "As we are working on these face shields, other efforts have been launched."
The Makerspace team is working with a group from a public hospital in Michigan on a field ventilator for short-term use for patients waiting for standard ventilators to become available. They also are reviewing a request from a hospital in Ohio to make specialized vent filters.
"As long as this crisis continues, the Makerspace at NJIT will be fully dedicated to the design of prototypes, making and testing of these prototypes, and delivery of ready-to-manufacture designs of needed devices to industry," Kam said.
NJIT's fabricators are collaborating with researchers, including as part of NJIT's partnership in the New Jersey Alliance for Clinical and Translational Science (NJ ACTS) led by Rutgers Biomedical and Health Sciences, on studies that will, for example, better elucidate the rates and risk factors for transmission of SARS-CoV-2 among health care workers.
NJIT physicists John Federici and Ian Gatley and their team are developing a swab that will be used in a study at Rutgers Biomedical and Health Sciences that seeks to characterize the factors related to viral transmission and disease severity in a large healthcare system, both in healthcare settings and in health care workers' households. The swabs, which are mostly 3-D-printed, will be used to collect serial biospecimens over a six-month period from a cohort of 500 health care workers and 250 age- and sex-matched staff members outside of clinical settings, all from within the same health care system.
"As COVID-19 spreads rapidly around the world, health care workers are the frontline of defense and highly vulnerable to acquiring the infection. In this sense, COVID-19 poses a double threat, endangering lives not only through its effects on the body and immune response, but through its potential to devastate workers essential for treating the sickest infected patients," said Rutgers University's Reynold Panettieri, the program director of NJ ACTS. "Our long-term goal is to protect the health care workforce caring for SARS-CoV-2-infected patients, their families, communities and the general population."
Procuring supplies for a research study, however timely and focused, has been an enormous challenge. "It is critical to do this sort of study right now, while the pace of infections is growing and the need is most time-sensitive," noted Federici, director of NJIT's Additive Manufacturing Laboratory (AddLab), which develops innovative manufacturing techniques in conjunction with embedded electronics.
Answering the call from a local emergency room physician, NJIT's Albert Dorman Honors College sponsored a design competition for both face shields and masks. Students were directed to follow CDC guidelines to ensure regulatory compliance and to use specified materials, and nearly two dozen took up the challenge. The winner of the face shield contest, whose design was approved by a regional medical system, produced more than 500 shields that were delivered to the Valley Hospital in Ridgewood. The winner of the mask competition sent 100 triple-cotton masks to Mount Sinai Hospital in Manhattan.
With requests flowing in, the Honors College is following up with a competition to build shields and masks for local emergency responders and other area hospitals as well.
The Makerspace at NJIT is central to both the university's hands-on learning mission and its growing relationship with New Jersey's manufacturing community. Students and faculty use it on a daily basis to create devices for research experiments, club team contests and research capstone projects, among other ventures. But it also is available to industrial partners to participate as mentors, trainers, and instructors, for companies to collaborate with students and faculty members on research and development projects, and for employees to receive customized training tailored to their needs.
The equipment inside ranges from small 3-D printers to large industrial machines such as an additive metal 3-D printer that uses powdered stainless steel to print parts, an optical scanner that effectively digitizes real life objects, enabling reverse engineering, and a continuous fiber 3-D printer that is capable of depositing strands of carbon fiber, fiberglass or Kevlar inside 3-D-printed parts, to add considerable strength. Labs across the campus, including the AddLab, also design and create prototypes for novel devices.
"Traditional factories are designed to manufacture specific products at very large volumes, while additive manufacturing labs are much more versatile. We instead fabricate whatever is required as the need arises, in much smaller amounts," said Samuel Gatley, the AddLab's senior additive manufacturing technician. "One day, we might make face masks and the next day, swabs."
NJIT labs also are donating supplies. In the early days of the regional surge in coronavirus cases, researchers emptied their closets of hundreds of gloves, goggles and gowns to donate to the Essex County Office of Emergency Management.
"As we respond to COVID-19, while keeping the well-being of students, faculty and staff at the forefront, NJIT is still operating. We are rethinking our approaches and making difficult decisions in real-time, from moving all our classes online, to carrying out our business functions remotely, to conducting our research computationally and sharing our laboratory supplies with our local community," said NJIT Provost Fadi Deek.
He added, "More importantly, NJIT is leading and collaborating with partner universities and government agencies to contribute to the collective fight against the coronavirus by rapidly developing in our additive manufacturing and prototyping facilities swabs, shields and masks, as well as other medical devices, to deliver into the hands of doctors and nurses."
"As COVID-19 spreads rapidly around the world, health care workers are the frontline of defense and highly vulnerable to acquiring the infection. In this sense, COVID-19 poses a double threat, endangering lives not only through its effects on the body and immune response, but through its potential to devastate workers essential for treating the sickest infected patients," said Rutgers University's Reynold Panettieri, the program director of NJ ACTS. "Our long-term goal is to protect the health care workforce caring for SARS-CoV-2-infected patients, their families, communities and the general population."
Procuring supplies for a research study, however timely and focused, has been an enormous challenge. "It is critical to do this sort of study right now, while the pace of infections is growing and the need is most time-sensitive," noted Federici, director of NJIT's Additive Manufacturing Laboratory (AddLab), which develops innovative manufacturing techniques in conjunction with embedded electronics.
Answering the call from a local emergency room physician, NJIT's Albert Dorman Honors College sponsored a design competition for both face shields and masks. Students were directed to follow CDC guidelines to ensure regulatory compliance and to use specified materials, and nearly two dozen took up the challenge. The winner of the face shield contest, whose design was approved by a regional medical system, produced more than 500 shields that were delivered to the Valley Hospital in Ridgewood. The winner of the mask competition sent 100 triple-cotton masks to Mount Sinai Hospital in Manhattan.
With requests flowing in, the Honors College is following up with a competition to build shields and masks for local emergency responders and other area hospitals as well.
The Makerspace at NJIT is central to both the university's hands-on learning mission and its growing relationship with New Jersey's manufacturing community. Students and faculty use it on a daily basis to create devices for research experiments, club team contests and research capstone projects, among other ventures. But it also is available to industrial partners to participate as mentors, trainers, and instructors, for companies to collaborate with students and faculty members on research and development projects, and for employees to receive customized training tailored to their needs.
The equipment inside ranges from small 3-D printers to large industrial machines such as an additive metal 3-D printer that uses powdered stainless steel to print parts, an optical scanner that effectively digitizes real life objects, enabling reverse engineering, and a continuous fiber 3-D printer that is capable of depositing strands of carbon fiber, fiberglass or Kevlar inside 3-D-printed parts, to add considerable strength. Labs across the campus, including the AddLab, also design and create prototypes for novel devices.
"Traditional factories are designed to manufacture specific products at very large volumes, while additive manufacturing labs are much more versatile. We instead fabricate whatever is required as the need arises, in much smaller amounts," said Samuel Gatley, the AddLab's senior additive manufacturing technician. "One day, we might make face masks and the next day, swabs."
NJIT labs also are donating supplies. In the early days of the regional surge in coronavirus cases, researchers emptied their closets of hundreds of gloves, goggles and gowns to donate to the Essex County Office of Emergency Management.
"As we respond to COVID-19, while keeping the well-being of students, faculty and staff at the forefront, NJIT is still operating. We are rethinking our approaches and making difficult decisions in real-time, from moving all our classes online, to carrying out our business functions remotely, to conducting our research computationally and sharing our laboratory supplies with our local community," said NJIT Provost Fadi Deek.
He added, "More importantly, NJIT is leading and collaborating with partner universities and government agencies to contribute to the collective fight against the coronavirus by rapidly developing in our additive manufacturing and prototyping facilities swabs, shields and masks, as well as other medical devices, to deliver into the hands of doctors and nurses."
No comments:
Post a Comment