From trash to jet fuel in 60 minutes—and 220º C
Researchers found a way to make fuel from plastic—critics wonder if it's practical.
DOUG JOHNSON - 5/24/2021, ARS TECHNICA
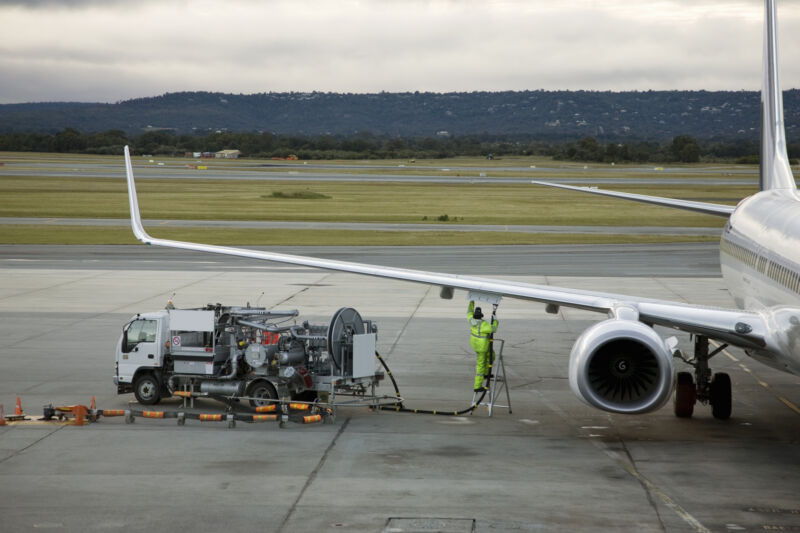
Enlarge
Tobias Titz / Getty Images
The world has a lot of plastic—8.3 billion tonnes of the stuff has been produced since 1950. It has so much plastic that humans have started trying to figure out ways to use the vast quantities of plastic waste we're accumulating. For some, that means recycling; for others, that means making art. For a team of researchers based out of Washington State University, it means making jet fuel.
Turning waste plastic into fuel isn’t a new idea. Many researchers have achieved it through a process called pyrolysis, which involves heating plastic to between 300º C and 900º C in an oxygen-free environment. This breaks the substance down into fuel, along with some additional chemicals. Hongfei Lin, associate professor with The Gene and Linda Voiland School of Chemical Engineering and Bioengineering at WSU, thinks that he and his team have discovered a way to make the process more efficient and environmentally friendly.
The team has a track record of making fuels from biomass sources. A year and a half ago, however, they decided to look into chemically deconstructing polyethylene, one of the most common forms of plastic in the world. The team began trying out pretreating the plastic with different combinations of solvents and catalysts prior to heating.
“Initially, we didn't know what would happen,” Lin told Ars.
Solving for the solvent
According to Lin, the solvents they tested penetrated the plastics and changed their physical properties, making them more accessible to the catalysts and maximizing the reaction rates. After testing a few different compounds, they found that n-hexane is the best solvent for producing the most fuel, while methylcyclohexane is the best option for producing more high-quality lubricant, another product of the process.
The team also used a ruthenium-on-carbon catalyst, which cleaved the covalent bonds between the carbon atoms in the plastic. After heating the plastic for an hour at 220º C—and injecting hydrogen into the reactor—the team found that 90 percent of it turned into the components of jet fuel and lubricant. The remaining 10 percent was converted to gases such as methane. The team can tinker with the different chemicals involved to produce more fuel or lubricant, as desired, he said.
This concept can also be applied to different types of plastics, though some (such as polyesters) have different types of chemical bonds. Therefore, those would need different treatments. The team tested the process in a relatively small reactor in their laboratory, but it could be scaled up to produce high-value products like lubricants and fuels from waste plastics, Lin said.
“We used polyethylene as a demonstration ... We found that it is very good as a proof of concept,” he said.
The process is more energy efficient than other pyrolysis approaches, he said, which rely on much higher temperatures. Besides the environmental benefits of losing less energy in the process, the process could also have an edge in the market if scaled up. “When it comes to recycling, cost is the key,” Lin said.
According to Lin, the team is working with WSU’s commercialization office and hopes to one day see it scaled up and used more broadly. He said that there has already been some early interest in the process from investors, but they can’t say from whom. In all, he believes that this method could be a potential tool for reducing plastic waste around the globe.Advertisement
“Worldwide, [plastic] is a very pressing environmental problem. We need to address this problem as soon as possible.”
But should we?
Not everyone’s quite as enamored with the idea, however. Andrew Rollinson, an independent consultant on the topic and former academic, called the process “totally pie-in-the-sky and impractical.”
Pyrolysis is an old technology, Rollinson told Ars. It was used to make things like creosote and methanol from wood, prior to the widespread use of petrochemicals, he said. Since the 1950s, attempts have been made to use the process on plastics. So far, it has not worked out, according to Rollinson.
Though the paper says the process is high-efficiency, it’s likely not, Rollinson says, as it requires a good deal of hydrogen pressure. Reaching the necessary pressure requires a lot of energy. Making and storing hydrogen also takes a lot of energy, reducing any green benefits. He said that the experiment was only in a laboratory setting. It would require a far greater amount of hydrogen and energy to pressurize it, if introduced at a commercial scale.
Further, Rollinson noted that the catalyst and solvents used would also need to be scaled up for larger amounts of plastics. Hexane, the solvent, is toxic, explosive, and environmentally harmful if released into the wild, he added. There’s also an energy input in the process of making these chemicals. In an email to Ars, Lin acknowledged that solvent recovery and reuse would add costs, but the technology itself would work to keep costs low. All the same, Rollinson has his doubts.
“No way it’s a go-er at all,” he said. “For science’s sake, it’s quite interesting. But as a practical answer to plastic … it’s not workable.”
Chem Catalysis, 2021. DOI: 10.1016/j.checat.2021.04.002 (About DOIs).
No comments:
Post a Comment