Bringing the biggest turbines to deep waters is an engineering challenge.
TIM DE CHANT - 5/25/2021
ARS TECHNICA
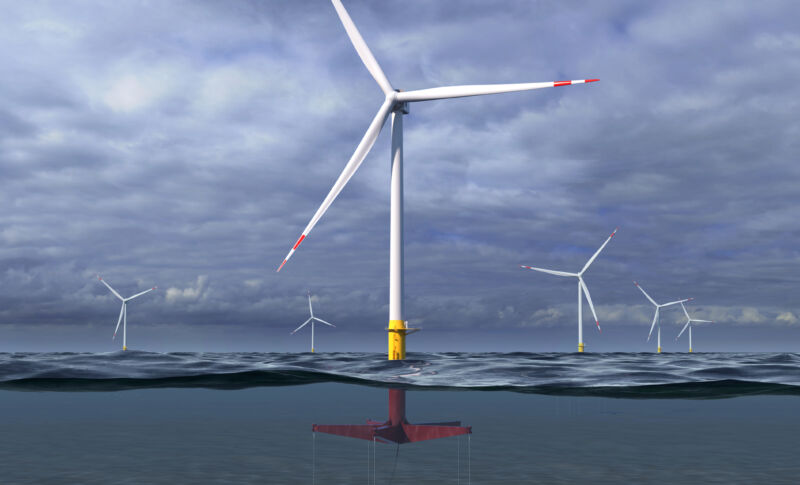
Enlarge / A rendering of GE and Glosten's actively managed tension leg platform for floating offshore wind projects.
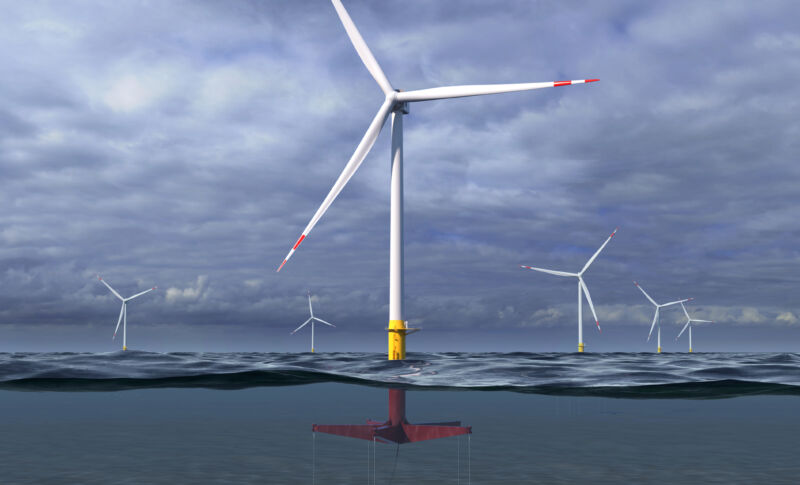
Enlarge / A rendering of GE and Glosten's actively managed tension leg platform for floating offshore wind projects.
The US took its first steps toward embracing offshore wind power earlier this month with the approval of the Vineyard Wind 1 project off the coast of Massachusetts. When the site is complete, 62 massive wind turbines anchored in the continental shelf will crank out 800 MW of electricity, giving the East Coast its first taste of a large, nearby, and renewable power source. And while the project shows the promise of offshore wind, the industry’s future may lie even deeper in the ocean.
After many delays, Massachusetts’ Vineyard Wind is finally approvedIn US waters alone, 58 percent of offshore wind capacity—some 4,200 TWh per year—is beyond the reach of fixed-foundation wind turbines, which are commercially limited to depths of less than 60 m. Offshore wind represents a massive untapped resource and could go a long way toward addressing the approximately 4,000 TWh of electricity used in the US last year.
To access offshore wind power, companies have been experimenting with floating platforms that would support the industry’s largest turbines. Yesterday, General Electric and Glosten, an engineering consultancy, announced a new design and control scheme that could significantly lower the cost of floating offshore wind as part of the ARPA-E ATLANTIS program.
Researchers from GE began with their company’s latest design, the 220-meter rotor Haliade X turbine that produces anywhere between 12 and 14 MW of power. “The Halide X turbine is a massive machine,” Rogier Blom, senior principal engineer at GE and the project’s lead, said to Ars. “To have a floating platform that can support that, these platforms need to be pretty massive. The state-of-the-art is to design the platform independent from the turbine.”
That design philosophy results in massive platforms that require more materials than may be necessary, driving up costs and making installation more challenging. Many of today’s floating platforms rely on gravity to keep turbines upright, and the platforms weigh up to three times more than the turbines. Other platforms are simply tethered to the seafloor, a situation that can make controlling the turbine more challenging.
“The reality is the platform behavior—its motions back and forth, its tilting behavior as a result of the waves—are very dynamically coupled with the behavior of the turbine, the bending of the tower, for example,” Blom said. “By separately designing turbine and platform, you’re essentially ignoring that coupling. That’s what’s driving inefficiency of overall design.”
Blom and his colleagues investigated whether they could design a dynamic platform that could communicate with the turbine so the two could work together to manage the myriad forces acting on the combined structure. The researchers landed on a tension leg platform, which essentially looks like a pirate ship’s anchor with many flukes instead of just two. Each of those flukes is then tethered to the seafloor.
Those tethers, or tendons, are key to the new GE design. “We’re looking to make the platform active, allow it to adjust its positioning through active tendons, to ride with the waves, control the positioning as it’s being moved back and forth, up and down with the waves, to ensure that it’s safe,” Blom said. “But we also want to ensure that all of those mechanical loads that the turbine would experience are as low as possible, while maximizing the resulting energy the turbine produces.”
Wind turbines already actively manage the pitch of their blades and the torque of their generator to optimize energy production while minimizing fatigue. The new tension leg platform that Blom and his colleagues designed coordinates the turbine’s responses with the tensioning or loosening of each tendon. All of this happens several times a second to continuously adjust the entire system.
The active design could trim up to 35 percent of the total mass of the platform, GE says, allowing wind developers to cut a significant driver of costs. It could also mean that a future platform may help install itself. Today, tension leg platforms require a special ship to bring the platform down to the correct depth. An active system could winch itself down, further reducing costs. How much money could be saved remains to be seen—the team has yet to do a full analysis of how the system would change the levelized cost of electricity, a key metric used to compare different sources of power, though it’s in the team's plans. Currently, ARPA-E is looking to the next two-year phase of the project, which would result in a prototype that could be tested out at sea.
Offshore wind in Europe won’t need subsidies much longerOffshore wind developers have already begun eyeing floating platforms in addition to more traditional fixed-platform projects. Winds offshore are more favorable than onshore, and floating platforms allow developers to site turbines in even more beneficial locations. Plus, floating platforms can be placed beyond the horizon, tackling one of offshore wind’s most challenging issues—NIMBYism.
As the offshore wind industry has matured, prices have dropped significantly. In Europe, costs of fixed platforms have fallen so much that the platforms may not require government subsidies. That could free up money for floating platforms, which remain pricier.
Blom said that his group isn’t seeking to replace fixed platforms; instead, it wants to open new swaths of the ocean to wind development.
To access offshore wind power, companies have been experimenting with floating platforms that would support the industry’s largest turbines. Yesterday, General Electric and Glosten, an engineering consultancy, announced a new design and control scheme that could significantly lower the cost of floating offshore wind as part of the ARPA-E ATLANTIS program.
Researchers from GE began with their company’s latest design, the 220-meter rotor Haliade X turbine that produces anywhere between 12 and 14 MW of power. “The Halide X turbine is a massive machine,” Rogier Blom, senior principal engineer at GE and the project’s lead, said to Ars. “To have a floating platform that can support that, these platforms need to be pretty massive. The state-of-the-art is to design the platform independent from the turbine.”
That design philosophy results in massive platforms that require more materials than may be necessary, driving up costs and making installation more challenging. Many of today’s floating platforms rely on gravity to keep turbines upright, and the platforms weigh up to three times more than the turbines. Other platforms are simply tethered to the seafloor, a situation that can make controlling the turbine more challenging.
“The reality is the platform behavior—its motions back and forth, its tilting behavior as a result of the waves—are very dynamically coupled with the behavior of the turbine, the bending of the tower, for example,” Blom said. “By separately designing turbine and platform, you’re essentially ignoring that coupling. That’s what’s driving inefficiency of overall design.”
Blom and his colleagues investigated whether they could design a dynamic platform that could communicate with the turbine so the two could work together to manage the myriad forces acting on the combined structure. The researchers landed on a tension leg platform, which essentially looks like a pirate ship’s anchor with many flukes instead of just two. Each of those flukes is then tethered to the seafloor.
Those tethers, or tendons, are key to the new GE design. “We’re looking to make the platform active, allow it to adjust its positioning through active tendons, to ride with the waves, control the positioning as it’s being moved back and forth, up and down with the waves, to ensure that it’s safe,” Blom said. “But we also want to ensure that all of those mechanical loads that the turbine would experience are as low as possible, while maximizing the resulting energy the turbine produces.”
Wind turbines already actively manage the pitch of their blades and the torque of their generator to optimize energy production while minimizing fatigue. The new tension leg platform that Blom and his colleagues designed coordinates the turbine’s responses with the tensioning or loosening of each tendon. All of this happens several times a second to continuously adjust the entire system.
The active design could trim up to 35 percent of the total mass of the platform, GE says, allowing wind developers to cut a significant driver of costs. It could also mean that a future platform may help install itself. Today, tension leg platforms require a special ship to bring the platform down to the correct depth. An active system could winch itself down, further reducing costs. How much money could be saved remains to be seen—the team has yet to do a full analysis of how the system would change the levelized cost of electricity, a key metric used to compare different sources of power, though it’s in the team's plans. Currently, ARPA-E is looking to the next two-year phase of the project, which would result in a prototype that could be tested out at sea.
Offshore wind in Europe won’t need subsidies much longerOffshore wind developers have already begun eyeing floating platforms in addition to more traditional fixed-platform projects. Winds offshore are more favorable than onshore, and floating platforms allow developers to site turbines in even more beneficial locations. Plus, floating platforms can be placed beyond the horizon, tackling one of offshore wind’s most challenging issues—NIMBYism.
As the offshore wind industry has matured, prices have dropped significantly. In Europe, costs of fixed platforms have fallen so much that the platforms may not require government subsidies. That could free up money for floating platforms, which remain pricier.
Blom said that his group isn’t seeking to replace fixed platforms; instead, it wants to open new swaths of the ocean to wind development.
No comments:
Post a Comment