The Future of Recycling? New Catalyst Transforms Waste into Valuable and Eco-Friendly Products
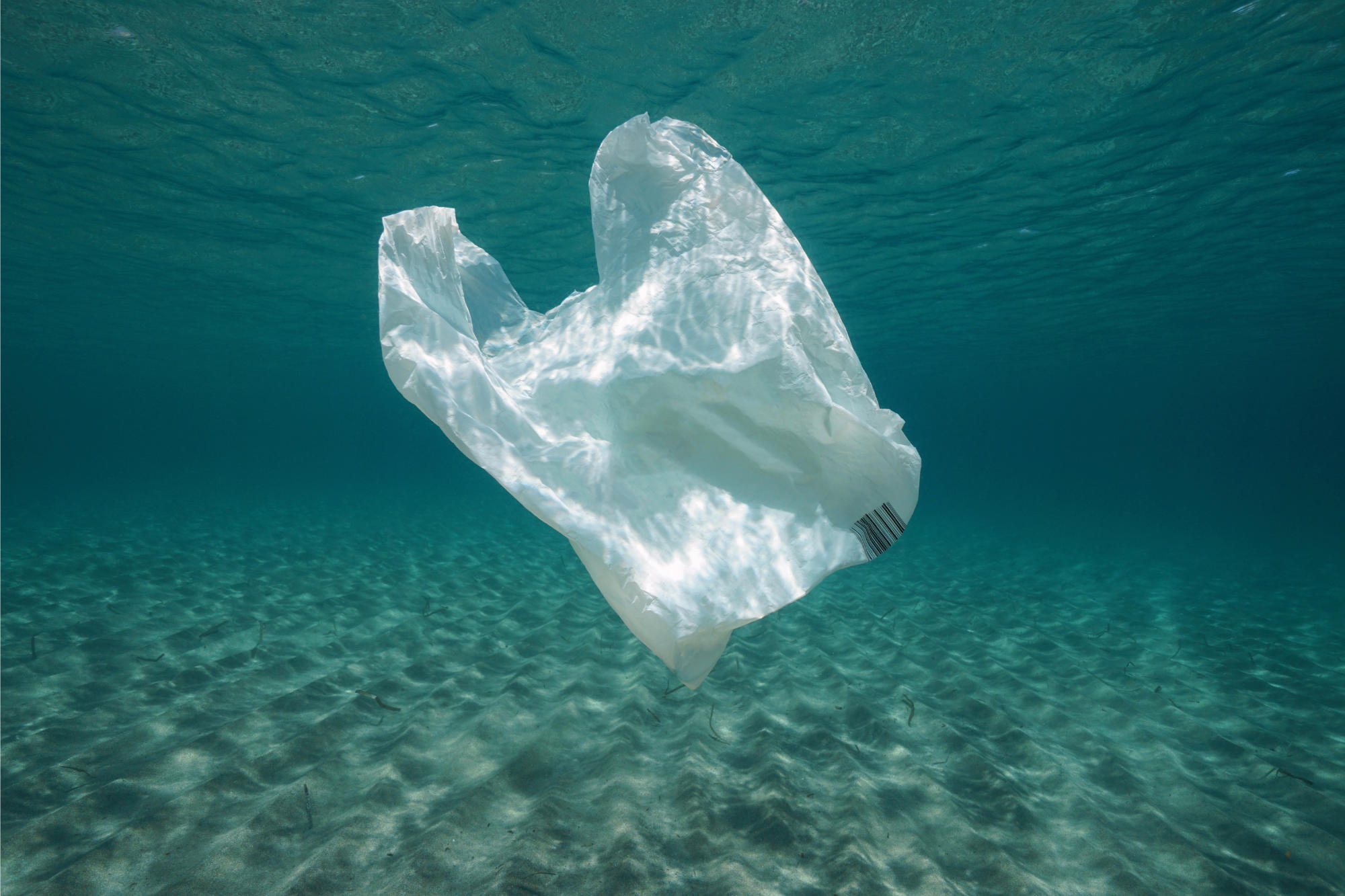
Photo of a plastic bag underwater
A team of scientists, led by Aaron Sadow, a researcher at Ames National Laboratory, Professor of Chemistry at Iowa State University, and Director of the Institute for Cooperative Upcycling of Plastic (iCOUP), have developed a new catalyst that transforms hydrocarbons into higher-value chemicals and materials that are more recyclable and environmentally friendly. This catalyst can convert materials such as motor oil, single-use plastic bags, water or milk bottles, caps, and even natural gas into more sustainable substances.
The new catalyst is designed to add functional groups to aliphatic hydrocarbons, which are organic compounds consisting solely of hydrogen and carbon. These hydrocarbons usually do not mix with water and form separate layers due to their lack of functional groups. By incorporating functional groups into these hydrocarbon chains, the properties of the materials can be significantly altered and made more recyclable.
“Methane in natural gas is the simplest of hydrocarbons with nothing but carbon-hydrogen (CH) bonds. Oils and polymers have chains of carbon atoms, linked by carbon-carbon (CC) bonds,” Sadow explained.
Aliphatic hydrocarbons make up a lot of petroleum and refined petroleum products, such as plastics and motor oils. These materials “don’t have other functional groups, which means they are not easy to biodegrade,” Sadow said. “So, it has long been a goal in the field of catalysis to be able to take these kinds of materials and add other atoms, such as oxygen, or build new structures from these simple chemicals.”
Unfortunately, the conventional way to add atoms to hydrocarbon chains requires considerable energy inputs. First petroleum is “cracked” with heat and pressure into small building blocks. Next, those building blocks are used to grow chains. Finally, the desired atoms are added at the end of the chains. In this new approach, existing aliphatic hydrocarbons are converted directly without cracking and at low temperatures.
Sadow’s team previously used a catalyst to break the CC bonds in these hydrocarbon chains and simultaneously attached aluminum to the ends of the smaller chains. Next, they inserted oxygen or other atoms to introduce functional groups. To develop a complementary process, the team found a way to avoid the CC bond-breaking step. “Depending on the starting material’s chain length and the desired properties of the product, we might want to shorten chains or simply add the oxygen functional group,” Sadow said. “If we could avoid the CC cleavage, we could, in principle, just transfer the chains from the catalyst to aluminum and then add air to install the functional group.”
Sadow explained that the catalyst is synthesized by attaching a commercially available zirconium compound onto commercially available silica-alumina. The substances are all earth-abundant and inexpensive, which is beneficial for potential future commercial applications.
Additionally, the catalyst and reactant are advantageous in terms of sustainability and cost. Aluminum is the most abundant metal on earth, and the aluminum reactant used is synthesized without creating waste by-products. The zirconium alkoxide-based catalyst precursor is air-stable, readily available, and activated in the reactor. “So unlike a lot of early organometallic chemistry that’s extremely air sensitive, this catalyst precursor is easy to handle,” Sadow said.
This chemistry is a step towards being able to affect the physical properties of a variety of plastics, such as making them stronger and easier to color. “As we develop the catalysis more, we expect that we’ll be able to incorporate more and more functional groups to affect the physical properties of the polymers,” Sadow said.
Sadow credited the success of this project to the collaborative nature of iCOUP. Perras’ group at Ames National Laboratory studied catalyst structures using Nuclear Magnetic Resonance (NMR) spectroscopy. Coates’, LaPointe’s, and Delferro’s groups from Cornell University and Argonne National Laboratory investigated polymer structure and physical properties. And Peters’ group at the University of Illinois statistically modeled polymer functionalization. “Project successes in the center build on contributions of many groups’ expertise,” Sadow said. “This work highlights the benefits of team science.”
Reference: “Zirconium-Catalyzed C–H Alumination of Polyolefins, Paraffins, and Methane” by Uddhav Kanbur, Alexander L. Paterson, Jessica Rodriguez, Andrew L. Kocen, Ryan Yappert, Ryan A. Hackler, Yi-Yu Wang, Baron Peters, Massimiliano Delferro, Anne M. LaPointe, Geoffrey W. Coates, Frédéric A. Perras and Aaron D. Sadow, 25 January 2023, Journal of the American Chemical Society.
DOI: 10.1021/jacs.2c11056
The work has also been featured in JACS Spotlight, “A Versatile New Tool for Making Commodity Chemicals.”
The research was conducted by the Institute for Cooperative Upcycling of Plastics (iCOUP), led by Ames National Laboratory. iCOUP is an Energy Frontier Research Center consisting of scientists from Ames National Laboratory, Argonne National Laboratory, UC Santa Barbara, University of South Carolina, Cornell University, Northwestern University, and the University of Illinois Urbana-Champaign.
No comments:
Post a Comment