By Euronews • Updated: 08/11/2021 -
.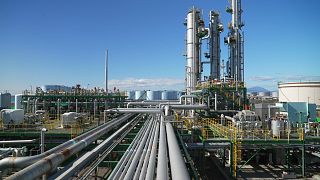
Copyright euronews
In this episode of Green Japan we focus on the latest innovations to capture and recycle carbon and develop zero-carbon concrete.
Carbon dioxide is the main cause of global warming. In the western wing of Tomakomai port, Japan has shown that CO2 can be captured and stored. Experts are confident the technology implemented at the Tomakomai CCS demonstration project centre will be crucial for reaching net-zero emissions in Japan and worldwide.
“CCS is an acronym for Carbon dioxide Capture and Storage. It is a technology aimed at preventing global warming by capturing CO2 generated from industrial activities and storing it underground,” explains Nakajima Toshiaki, President of Japan CCS.
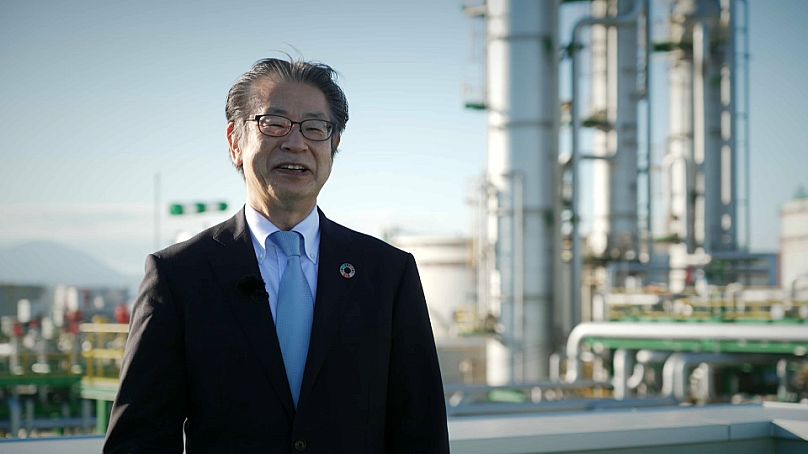
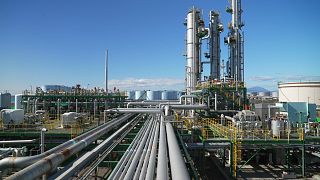
Copyright euronews
In this episode of Green Japan we focus on the latest innovations to capture and recycle carbon and develop zero-carbon concrete.
Carbon dioxide is the main cause of global warming. In the western wing of Tomakomai port, Japan has shown that CO2 can be captured and stored. Experts are confident the technology implemented at the Tomakomai CCS demonstration project centre will be crucial for reaching net-zero emissions in Japan and worldwide.
“CCS is an acronym for Carbon dioxide Capture and Storage. It is a technology aimed at preventing global warming by capturing CO2 generated from industrial activities and storing it underground,” explains Nakajima Toshiaki, President of Japan CCS.
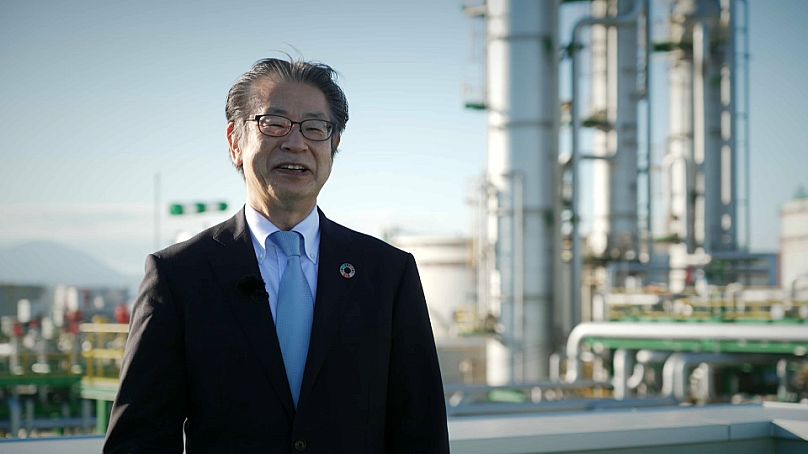
President of Japan CCS Nakajima Toshiaki explains carbon dioxide and storage technology.Euronews
The CO2 source is a gas supply facility at Idemitsu Kosan Hokkaido Refinery, adjacent to the Tomakomai CCS Center. A gas containing carbon dioxide is sent by pipeline to the Capture Facility.
Yamagishi Kazuyuki, from CCS, explains the process.
“We receive a maximum of 25 tonnes of CO2 per hour which is equivalent to 600 tonnes a day. Our target was to process 100,000 tonnes in one year. We achieved the injection of 300,000 tonnes two years ago.”
Once the gas containing CO2 arrives at the demonstration plant, CO2 is separated from the gas and captured by chemical absorption inside three towers, which are part of the main CCS facilities. The CO2 now needs to be stored.
“The captured CO2 is sent to the inlet of this well, after a certain amount of pressure is applied. Through this pipe, the CO2 is sent to the geological layers below the seabed,” Kazuyuki says.
The two injection wells of the project were drilled from onshore towards offshore sub-sea bed reservoirs. One well targeted a sandstone layer between the depths of 1,000 to 1,200 metres. The other one reached a volcanoclastic layer between 2,400 to 3,000 metres deep.
Japan is convinced this technology will become a key approach for reducing the impact of global warming once it reaches the implementation phase.
“"The International Energy Agency estimates in 2050 we'll have to be capable of storing over 7 billion tons of CO2 per year with CCS systems in order to achieve net-zero. This would allow to use fossil fuels in a cleaner way, or to capture CO2 directly from the atmosphere and store it underground,” says Japan CCS President Nakajima Toshiaki.
Carbon negative concrete
While CO2 can be captured before entering the atmosphere and stored in the ground, Japan has also found a way to use CO2 to produce a carbon negative concrete, called CO2-SUICOM.
“Ordinary concrete emits approximately 288 kg of CO2 per cubic metre during its production, but CO2-SUICOM has achieved minus 18kg,” says Watanabe Kenzo, the General Manager of the concrete and construction materials group, Kajima Technical Research Institute.
This is the first concrete in the world that is not only carbon negative, but is also capable of absorbing CO2 during the curing process.
The key to making this happen is the addition of a special material, which is a chemical by-product, and then exposing the concrete to CO2.
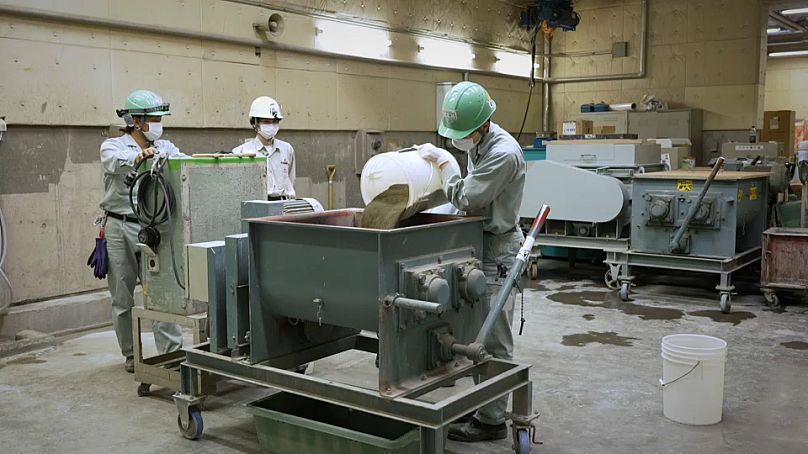
The CO2 source is a gas supply facility at Idemitsu Kosan Hokkaido Refinery, adjacent to the Tomakomai CCS Center. A gas containing carbon dioxide is sent by pipeline to the Capture Facility.
Yamagishi Kazuyuki, from CCS, explains the process.
“We receive a maximum of 25 tonnes of CO2 per hour which is equivalent to 600 tonnes a day. Our target was to process 100,000 tonnes in one year. We achieved the injection of 300,000 tonnes two years ago.”
Once the gas containing CO2 arrives at the demonstration plant, CO2 is separated from the gas and captured by chemical absorption inside three towers, which are part of the main CCS facilities. The CO2 now needs to be stored.
“The captured CO2 is sent to the inlet of this well, after a certain amount of pressure is applied. Through this pipe, the CO2 is sent to the geological layers below the seabed,” Kazuyuki says.
The two injection wells of the project were drilled from onshore towards offshore sub-sea bed reservoirs. One well targeted a sandstone layer between the depths of 1,000 to 1,200 metres. The other one reached a volcanoclastic layer between 2,400 to 3,000 metres deep.
Japan is convinced this technology will become a key approach for reducing the impact of global warming once it reaches the implementation phase.
“"The International Energy Agency estimates in 2050 we'll have to be capable of storing over 7 billion tons of CO2 per year with CCS systems in order to achieve net-zero. This would allow to use fossil fuels in a cleaner way, or to capture CO2 directly from the atmosphere and store it underground,” says Japan CCS President Nakajima Toshiaki.
Carbon negative concrete
While CO2 can be captured before entering the atmosphere and stored in the ground, Japan has also found a way to use CO2 to produce a carbon negative concrete, called CO2-SUICOM.
“Ordinary concrete emits approximately 288 kg of CO2 per cubic metre during its production, but CO2-SUICOM has achieved minus 18kg,” says Watanabe Kenzo, the General Manager of the concrete and construction materials group, Kajima Technical Research Institute.
This is the first concrete in the world that is not only carbon negative, but is also capable of absorbing CO2 during the curing process.
The key to making this happen is the addition of a special material, which is a chemical by-product, and then exposing the concrete to CO2.
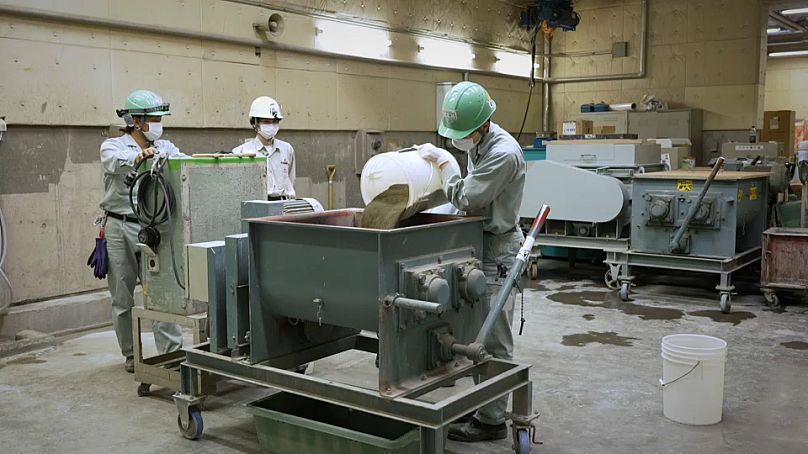
Developed in Japan, CO2-SUICOM is a carbon negative concrete.
Euronews
“We use CO2 gas instead of water for the CO2-SUICOM's curing process. CO2 is immobilised by bringing it into contact with the concrete while it is still hardening. We add a special mixture “γC2S”, we call it “magic powder” as it solidifies a large amount of CO2. The more we produce this “magic concrete” the more it reduces CO2 from the atmosphere,” says Kenzo.
This eco-friendly concrete has already been used in all sorts of infrastructure and building projects as a precast-material. SUICOM has already been used to build walls, ceiling panels and interlocking blocks. In the near future, developers intend to apply this technology to a wider range of construction materials. The carbon negative concrete could then be used as a common already-mixed concrete for cast-in place usage. This would open a new green way forward for construction.
“We use CO2 gas instead of water for the CO2-SUICOM's curing process. CO2 is immobilised by bringing it into contact with the concrete while it is still hardening. We add a special mixture “γC2S”, we call it “magic powder” as it solidifies a large amount of CO2. The more we produce this “magic concrete” the more it reduces CO2 from the atmosphere,” says Kenzo.
This eco-friendly concrete has already been used in all sorts of infrastructure and building projects as a precast-material. SUICOM has already been used to build walls, ceiling panels and interlocking blocks. In the near future, developers intend to apply this technology to a wider range of construction materials. The carbon negative concrete could then be used as a common already-mixed concrete for cast-in place usage. This would open a new green way forward for construction.
No comments:
Post a Comment