Future material demand for automotive
lithium-based batteries
by Thamarasee Jeewandara , Tech Xplore
by Thamarasee Jeewandara , Tech Xplore
DECEMBER 24, 2020 FEATURE
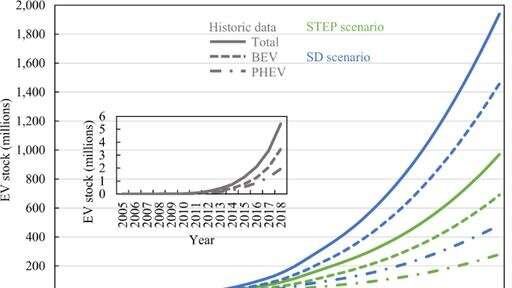
Global EV stock development projected until 2050. BEV battery electric vehicle, PHEV plug-in hybrid electric vehicle, STEP scenario the Stated Policies scenario, SD scenario Sustainable Development scenario. Credit: Nature Communications Materials, doi: 10.1038/s43246-020-00095-x
As the world shifts to electric vehicles to reduce climate change, it is important to quantify future demands for key battery materials. In a new report, Chengjian Xu, Bernhard Steubing and a research team at the Leiden University, Netherlands and the Argonne National Laboratory in the U.S. showed how the demands of a lithium, nickel, cobalt and manganese oxide dominated battery will increase by many factors between 2020 to 2050. As a result, supply chains for lithium, cobalt and nickel will require significant expansion and likely additional resource discovery. Nevertheless, uncertainties are large relative to the development of electrical vehicle fleets and battery capacities per vehicle. While closed-loop recycling plays a minor but increasingly important role to reduce the primary material demand until 2050, researchers must implement advanced recycling strategies to economically recover battery-grade materials from end-of-life batteries. This work is now published on Nature Communications Materials.
The evolution of electric vehicles (EVs)
Electric vehicles (EVs) have a reduced climate impact compared to vehicles with internal combustion engines. This advantage has led to a massive increase in demand, where global fleets have grown from a few thousand from just a decade ago, up to 7.5 million in 2019. However, the global average market of the vehicles is still limited, while future growth is expected to dwarf past growth in absolute numbers. Lithium-ion batteries (LIBs) are presently the dominant technology for electric vehicles, and typical automotive LIBs contain lithium, cobalt and nickel in the cathode, with graphite in the anode, alongside aluminum and copper in other components. Battery technology is currently advancing for new and improved chemistries. In this work, Xu et al. studied the global material demand for light-duty electric vehicle batteries from lithium, nickel, and cobalt to graphite and silicon and connected the material demands to the ongoing production capacities and known reserves to discuss key factors to improve batteries. The work will assist the transition to electric vehicles by providing insight to the future battery material demand, alongside key factors driving it.
As the world shifts to electric vehicles to reduce climate change, it is important to quantify future demands for key battery materials. In a new report, Chengjian Xu, Bernhard Steubing and a research team at the Leiden University, Netherlands and the Argonne National Laboratory in the U.S. showed how the demands of a lithium, nickel, cobalt and manganese oxide dominated battery will increase by many factors between 2020 to 2050. As a result, supply chains for lithium, cobalt and nickel will require significant expansion and likely additional resource discovery. Nevertheless, uncertainties are large relative to the development of electrical vehicle fleets and battery capacities per vehicle. While closed-loop recycling plays a minor but increasingly important role to reduce the primary material demand until 2050, researchers must implement advanced recycling strategies to economically recover battery-grade materials from end-of-life batteries. This work is now published on Nature Communications Materials.
The evolution of electric vehicles (EVs)
Electric vehicles (EVs) have a reduced climate impact compared to vehicles with internal combustion engines. This advantage has led to a massive increase in demand, where global fleets have grown from a few thousand from just a decade ago, up to 7.5 million in 2019. However, the global average market of the vehicles is still limited, while future growth is expected to dwarf past growth in absolute numbers. Lithium-ion batteries (LIBs) are presently the dominant technology for electric vehicles, and typical automotive LIBs contain lithium, cobalt and nickel in the cathode, with graphite in the anode, alongside aluminum and copper in other components. Battery technology is currently advancing for new and improved chemistries. In this work, Xu et al. studied the global material demand for light-duty electric vehicle batteries from lithium, nickel, and cobalt to graphite and silicon and connected the material demands to the ongoing production capacities and known reserves to discuss key factors to improve batteries. The work will assist the transition to electric vehicles by providing insight to the future battery material demand, alongside key factors driving it.
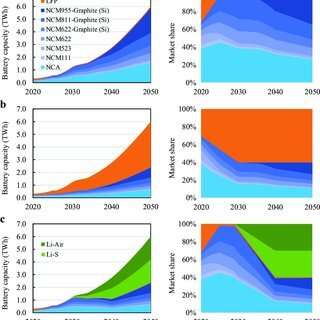
Battery market shares and yearly EV battery sales until 2050 for the fleet development in the STEP scenario. (a) NCX scenario. (b) LFP scenario. (c) Li-S/Air scenario. LFP lithium iron phosphate battery, NCM lithium nickel cobalt manganese battery, Numbers in NCM111, NCM523, NCM622, NCM811, and NCM955 denote ratios of nickel, cobalt, and manganese. NCA lithium nickel cobalt aluminum battery, Graphite (Si) graphite anode with some fraction of silicon, Li-S lithium-sulphur battery, Li-Air lithium-air battery, TWh 109 kWh. Credit: Nature Communications Materials, doi: 10.1038/s43246-020-00095-x
The fleet growth of electric vehicles (EVs)
The team projected the EV fleet growth based on two scenarios of the International Energy Agency (IEA) until 2030. These include the stated policies (STEP) relative to existing government policies and the sustainable development (SD) scenario compatible with the Paris Agreement climate goals of reaching a 30 percent global sale for EVs by 2030. In this analysis, Xu et al. extended these scenarios until 2050. To meet the STEP scenario, a battery capacity of approximately 6 TWh will be required annually by 2050. The material requirements will depend on the choice of battery chemistries used with three battery chemistries currently in consideration.
The most likely scenario will follow the current trend of the widespread use of lithium nickel cobalt aluminum (NCA) and lithium nickel cobalt manganese (NCM) batteries (henceforth known as the NCX, in which X stands for aluminum or manganese). This will lead to the evolution of battery chemistries by 2030. The lithium iron phosphates (LFP) that can constitute the lithium-ion battery cathode material are expected to be in use increasingly for electric vehicles in the future. While their lower specific energy can affect the fuel economy and range of EVs, the LFPs are advantageous due to lower production costs, better thermal stability and longer life cycle. Although the use of LFP batteries is currently common in commercial transport vehicles such as buses, there are also prospects for widespread use in light-duty EVs, including Teslas.
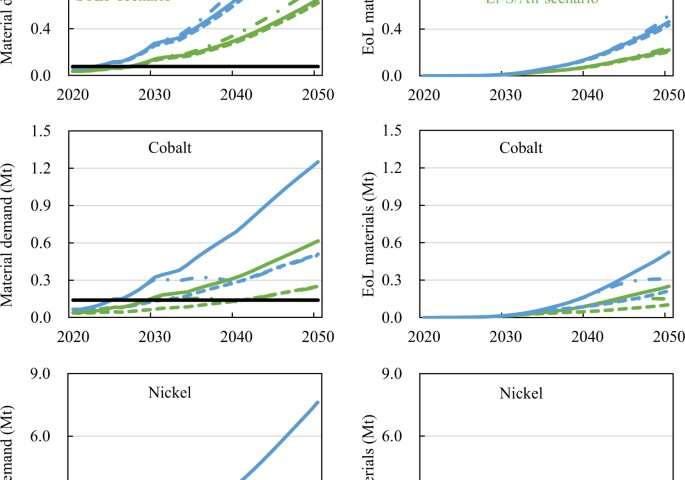
The fleet growth of electric vehicles (EVs)
The team projected the EV fleet growth based on two scenarios of the International Energy Agency (IEA) until 2030. These include the stated policies (STEP) relative to existing government policies and the sustainable development (SD) scenario compatible with the Paris Agreement climate goals of reaching a 30 percent global sale for EVs by 2030. In this analysis, Xu et al. extended these scenarios until 2050. To meet the STEP scenario, a battery capacity of approximately 6 TWh will be required annually by 2050. The material requirements will depend on the choice of battery chemistries used with three battery chemistries currently in consideration.
The most likely scenario will follow the current trend of the widespread use of lithium nickel cobalt aluminum (NCA) and lithium nickel cobalt manganese (NCM) batteries (henceforth known as the NCX, in which X stands for aluminum or manganese). This will lead to the evolution of battery chemistries by 2030. The lithium iron phosphates (LFP) that can constitute the lithium-ion battery cathode material are expected to be in use increasingly for electric vehicles in the future. While their lower specific energy can affect the fuel economy and range of EVs, the LFPs are advantageous due to lower production costs, better thermal stability and longer life cycle. Although the use of LFP batteries is currently common in commercial transport vehicles such as buses, there are also prospects for widespread use in light-duty EVs, including Teslas.
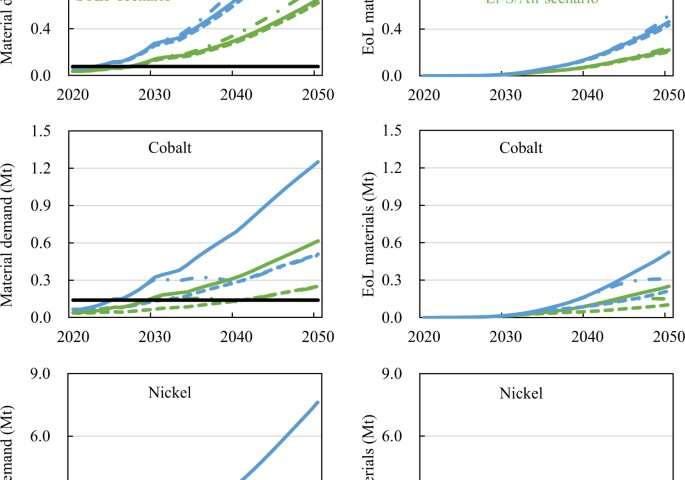
Battery material flows from 2020 to 2050 for lithium, nickel, and cobalt in the NCX, LFP, and Li-S/Air battery scenarios. (a) Primary material demand. (b) materials in end-of-life batteries. STEP scenario the Stated Policies scenario, SD scenario Sustainable Development scenario, Mt million tons. Credit: Nature Communications Materials, doi: 10.1038/s43246-020-00095-x
Battery material demand and recycling potentials
The scientists then assessed the global demand for EV (electric vehicle) batteries and noted the growing demand for lithium to only be slightly influenced by the specific chemistry of the battery, while the specific battery chemistries of nickel and cobalt had a stronger influence on their demand. The team further projected an increased demand for lithium-ion batteries, followed by the demand for nickel from 2020 to 2050. In this way, they predicted the cumulative demand from 2020 to 2050 to range from 7.3 to 18.3 million tons (Mt) for Li, 3.5–16.8 Mt for Co, and 18.1–88.9 Mt for Ni.
Xu et al. next showed the materials present in end-of-life batteries across time and discussed how recovering them would help reduce primary material production. The existing commercial recycling methods for EV batteries include pyrometallurgical and hydrometallurgical processing. Pyrometallurgical recycling includes smelting entire batteries or battery components after pre-treatment. Hydrometallurgical processing is based on acid leaching and the subsequent recovery of battery materials via solvent extraction and precipitation methods. In closed loop recycling, pyrometallurgical processing can be followed by hydrometallurgical processing to convert an alloy into metal salts. Direct recycling aims to recover cathode materials while maintaining their chemical structures for economic and environmental advantages, however, this method is still in its early stages of development.
Battery material demand and recycling potentials
The scientists then assessed the global demand for EV (electric vehicle) batteries and noted the growing demand for lithium to only be slightly influenced by the specific chemistry of the battery, while the specific battery chemistries of nickel and cobalt had a stronger influence on their demand. The team further projected an increased demand for lithium-ion batteries, followed by the demand for nickel from 2020 to 2050. In this way, they predicted the cumulative demand from 2020 to 2050 to range from 7.3 to 18.3 million tons (Mt) for Li, 3.5–16.8 Mt for Co, and 18.1–88.9 Mt for Ni.
Xu et al. next showed the materials present in end-of-life batteries across time and discussed how recovering them would help reduce primary material production. The existing commercial recycling methods for EV batteries include pyrometallurgical and hydrometallurgical processing. Pyrometallurgical recycling includes smelting entire batteries or battery components after pre-treatment. Hydrometallurgical processing is based on acid leaching and the subsequent recovery of battery materials via solvent extraction and precipitation methods. In closed loop recycling, pyrometallurgical processing can be followed by hydrometallurgical processing to convert an alloy into metal salts. Direct recycling aims to recover cathode materials while maintaining their chemical structures for economic and environmental advantages, however, this method is still in its early stages of development.
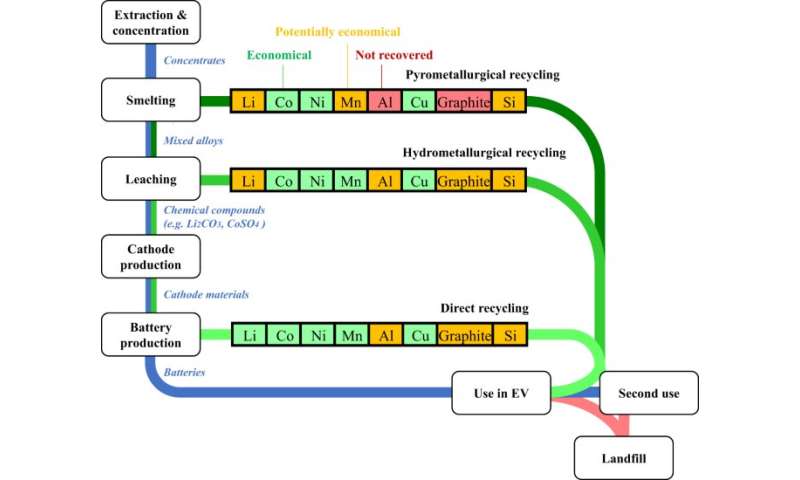
Conceptual schematic showing how the three considered recycling scenarios close battery material loops and which materials are recovered. In reality not all materials go through all processing steps. For example, pyrometallurgical recycling (smelting) still requires hydrometallurgical processing (leaching) before cathode materials can be produced, while direct recycling is designed to recover cathode materials directly. In pyro- and hydrometallurgical recycling the recovery of Li may not be economical and in pyrometallurgical recycling graphite is incinerated and Al not recovered from the slag. Credit: Nature Communications Materials, doi: 10.1038/s43246-020-00095-x
Outlook for electric vehicles (EVs)
In this way, Chengjian Xu, Bernhard Steubing and colleagues developed models to show how battery production capacity for lithium, nickel and cobalt will have to increase significantly since demands for electric vehicles could outgrow current production rates even before 2025. The battery materials can be supplied without exceeding existing production capacities, although supplies will have to increase to meet demands from other sectors. The outlined supply risks can change with the potential discovery of new reserves. The demand for battery capacity will depend on technical factors such as vehicle design, weight and fuel efficiency as well as the fleet size and consumer choices relative to the size and range of EVs.
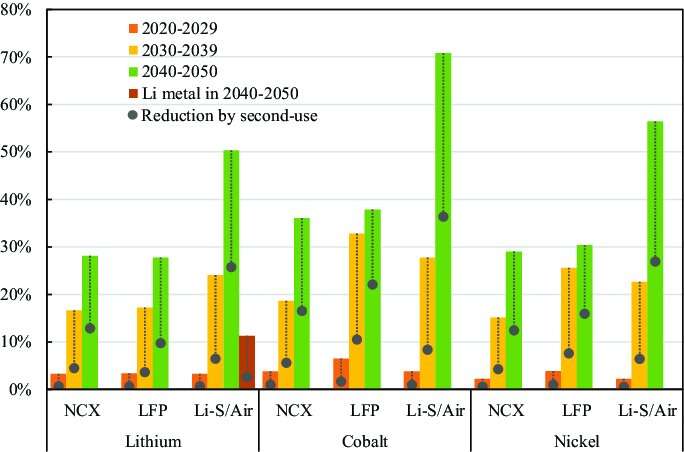
Outlook for electric vehicles (EVs)
In this way, Chengjian Xu, Bernhard Steubing and colleagues developed models to show how battery production capacity for lithium, nickel and cobalt will have to increase significantly since demands for electric vehicles could outgrow current production rates even before 2025. The battery materials can be supplied without exceeding existing production capacities, although supplies will have to increase to meet demands from other sectors. The outlined supply risks can change with the potential discovery of new reserves. The demand for battery capacity will depend on technical factors such as vehicle design, weight and fuel efficiency as well as the fleet size and consumer choices relative to the size and range of EVs.
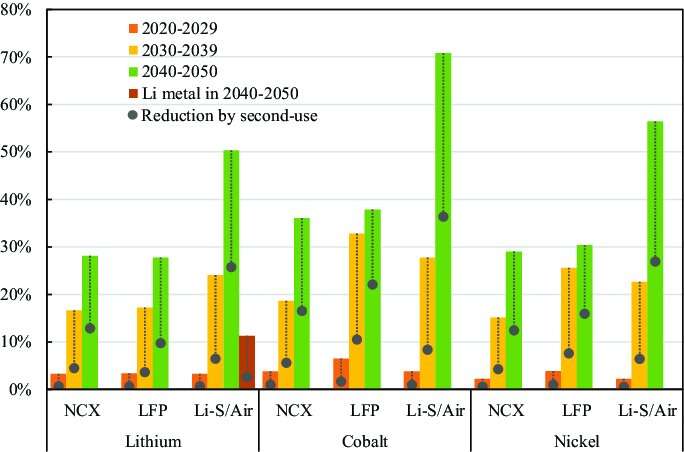
Closed-loop recycling potential of battery materials in periods of 2020–2029, 2030–2039, and 2040–2050 in the STEP scenario. Hydrometallurgical recycling is used for NCX and LFP batteries and mechanical recovery of Li metal for Li-S and Li-Air batteries. Gray dots show how second-use, which postpones the time of recycling, reduces the closed-loop recycling potentials and thus the availability of secondary materials in the coming decades.
Credit: Nature Communications Materials, doi: 10.1038/s43246-020-00095-x
The method of direct recycling is the most economic and environmentally favored closed-loop recycling process since it can allow the recovery of cathode materials without smelting and leaching processes. Successful transition to electric vehicles will depend on sustained material supply that can keep up with the growth of the sector. Scientific sustainability assessments including life cycle evaluations of chemistries will guide the selection of alternative battery chemistries and raw materials. The global demands projected in this work also provide a platform to monitor the global economic environmental and social impacts of electric vehicles and their batteries.
Explore further
The method of direct recycling is the most economic and environmentally favored closed-loop recycling process since it can allow the recovery of cathode materials without smelting and leaching processes. Successful transition to electric vehicles will depend on sustained material supply that can keep up with the growth of the sector. Scientific sustainability assessments including life cycle evaluations of chemistries will guide the selection of alternative battery chemistries and raw materials. The global demands projected in this work also provide a platform to monitor the global economic environmental and social impacts of electric vehicles and their batteries.
Explore further
New class of cobalt-free cathodes could enhance energy density of next-gen lithium-ion batteries
More information: Xu C. et al. Future material demand for automotive lithium-based batteries, Nature Communications Materials, doi.org/10.1038/s43246-020-00095-x
Knobloch, F., et al. Net emission reductions from electric cars and heat pumps in 59 world regions over time, Nature Sustainability doi.org/10.1038/s41893-020-0488-7
Ponrouch A. & Palacin R. A. Post-Li batteries: promises and challenges. Philosophical Transactions of the Royal Society A. doi.org/10.1098/rsta.2018.0297
More information: Xu C. et al. Future material demand for automotive lithium-based batteries, Nature Communications Materials, doi.org/10.1038/s43246-020-00095-x
Knobloch, F., et al. Net emission reductions from electric cars and heat pumps in 59 world regions over time, Nature Sustainability doi.org/10.1038/s41893-020-0488-7
Ponrouch A. & Palacin R. A. Post-Li batteries: promises and challenges. Philosophical Transactions of the Royal Society A. doi.org/10.1098/rsta.2018.0297
Journal information: Nature Sustainability , Philosophical Transactions of the Royal Society A
© 2020 Science X Network
No comments:
Post a Comment