Staff Writer | April 3, 2023 |
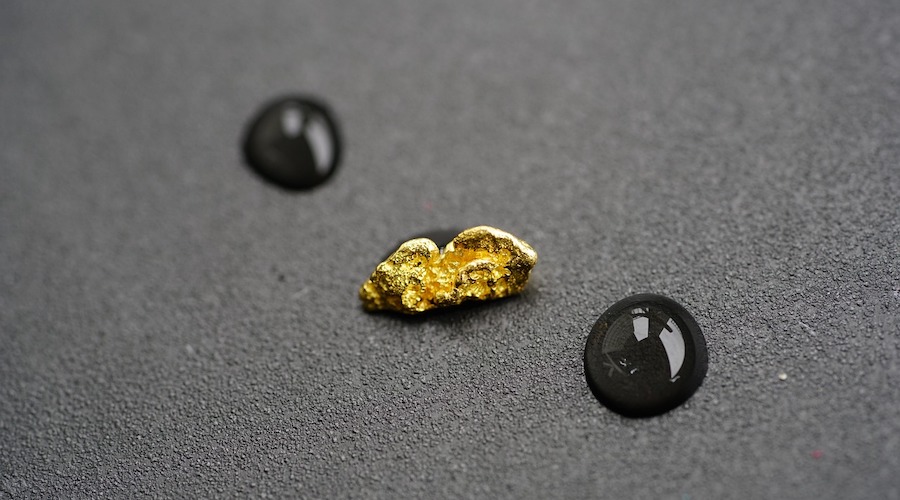
Gold nugget. (Reference image by Hans, Pixabay.)
Researchers at the Vienna University of Technology have found a way to melt nano gold nuggets using highly charged ions.

In detail, the scientists bombarded extremely small pieces of gold, consisting of a few thousand atoms and with a diameter in the order of ten nanometers, with multiply-ionized xenon atoms. This made it possible to change the shape and size of these gold pieces in a targeted manner.
In a paper published in the journal Small, the scientists explain that up to 40 electrons were removed from the atoms, so they are highly electrically charged.
The highly charged ions then hit small gold islands placed on an insulating substrate—and then different things happened: The gold islands became flatter, they melted, or they evaporated.
“Depending on how highly our ions are electrically charged, we can trigger different effects,” Gabriel Szabo, first author of the paper, said in a media statement.
The highly charged ions hit the tiny gold nuggets at elevated speed—at around 500 kilometres per second. Nevertheless, it was not the force of the impact that changed the gold islands.
“If you shoot uncharged xenon atoms at the gold islands with the same kinetic energy, the gold islands remain practically unchanged,” Szabo said. “So the decisive factor was not the kinetic energy, but the electrical charge of the ions. This charge also carries energy, and it is deposited exactly at the point of impact.”
Throwing gold out of balance
As soon as the positively charged ions hit the nano gold pieces, they snatched electrons away from the gold. In a large piece of gold, this would have no significant effect: Gold is an excellent conductor, the electrons can move freely, and more electrons would be supplied from other areas of the gold nugget.
But the nano-gold structures are so small that they can no longer be regarded as an inexhaustible reservoir of electrons.
“The charged energy of the impacting ion is transferred to the gold, thus the electronic structure of the entire nano-gold object is thrown completely out of balance, the atoms start to move and the crystal structure of the gold is destroyed,” head researcher Richard Wilhelm explained. “Depending on how much energy you deposit, it may even happen that the entire nano-gold piece melts or is vaporized.”
The effects of the ion bombardment can then be studied in an atomic force microscope. Depending on the charge of the ions, the height of the gold pieces is reduced to a lesser or greater extent.
“Just as our models had also predicted, we can control the impact of the ions on the gold—and not by the speed we give our projectiles, but rather by their charge,” Szabo reported.
According to the team, improved control and a deeper understanding of such processes are important for making a wide variety of nanostructures.
“It’s a technique that allows you to selectively edit the geometry of particularly small structures. That’s just as interesting for the creation of microelectronic components as it is for so-called quantum dots—tiny structures that allow very specific tailor-made electronic or optical effects due to their quantum physical properties,” Wilhelm said.