Crowley Invests in Mobile Floating Dry Dock for Use with Floating Wind
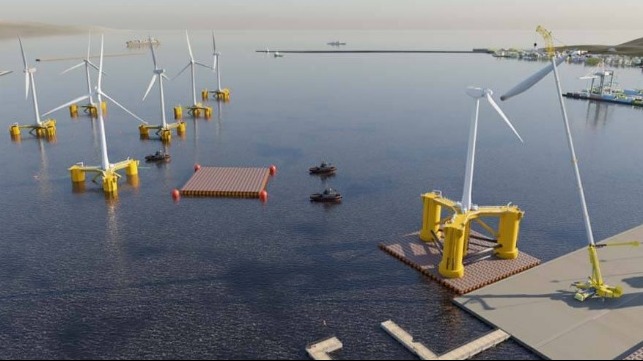
Crowley is investing in a UK-based startup, Tugdock, which is developing what is billed as the world's first road-transportable floating dry dock. The company plan to explore the potential use of the platforms especially to support the developing floating offshore wind applications in California and elsewhere in the U.S. It is the latest development of the U.S. maritime logistics company which has been moving to expand its role in the wind industry.
Found in 2017, Tugdock uses a patented marine buoyancy bag technology and a modular form that allows for the transport and assembly of floating dry docks that are delivered by road and assembled in port. The technology allows them to offer dimensions far wider than most of the world’s existing dry docks, which they note were not designed for the news of the floating wind industry. They report the submersible platforms can operate in as little as 5 meters (approximately 16 feet) draft, enabling a more efficient construction and the air lift bag design provides a large lifting capacity. Once assembled, the platform can then be towed to deeper water for the launching of the turbines. It can be provided either as a purpose-built permanent or temporary pre-assembly solution.
"The cost and time constraints associated with port infrastructure developments and submersible barge suitability are major bottlenecks holding back the growth of the floating offshore wind sector," said Lucas Lowe-Houghton, Director of Strategy and Growth at Tugdock "Our TSP technology helps overcome these issues, providing a ready-to-go solution that does not require planning or environmental permissions.”
According to the companies, the technology for the portable, submersible platform, was developed to be launched in ports that lack sufficient water depth. It can help ports that lack the assembly space required to build and loadout the massive floating substructures required to support offshore wind turbines. They highlight the potential opportunities in locations, such as the U.S. West Coast, where depth and conventional dry docks may be ill-suited for the logistics required.
The Tugdock product line comes in a range of deck sizes from 12m x 12m up to 120m x 120m with a total lift capacity of up to 35,000 tonnes. The company reports the system can lift vessels and other floating structures clear of the water at a fraction of the cost of standard dry docks.
"This important investment and collaboration with Tugdock strategically complement our vision and market-leading logistics capabilities to support wind energy development from beginning to end," said Bob Karl, senior vice president and general manager, of Crowley Wind Services.
Crowley Wind Services is developing and planning wind terminals in California, Louisiana, and Massachusetts. At the California Port of Humboldt Bay, Crowley is progressing on an agreement to build and operate a terminal for manufacturing, installation, and operation of offshore wind floating platforms. They are planning for the use of large heavy cargo vessels and to provide crewing and marshaling services for the Pacific waters recently approved for leases for wind energy.
Humboldt and other West Coast installations they note will rely upon floating offshore wind turbines due to the water depths and topography of the continental shelf. Globally they highlight that about 80 percent of the world's offshore wind power potential lies in waters deeper than 60 meters, according to the Global Wind Energy Council, which means that development will be contingent on the development of floating wind applications.
BOEM Finds No Environmental Impacts for Gulf of Mexico Wind Leasing
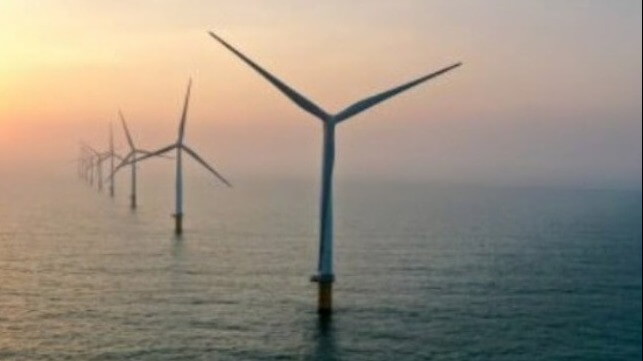
The Bureau of Ocean Energy Management (BOEM) issued a finding today that it believes there would be no significant impacts to environmental resources in the Gulf of Mexico if its proceeds with the proposed offshore wind leasing efforts in the Gulf. The bureau in October 2022 defined two initial target areas off Texas and Louisiana that would become the first wind lease sites in the area as it works to expand the country’s renewable energy supply.
The U.S. has developed a well-defined process of steps toward the leasing of offshore sites. BOEM in the latest development in the process, and preparing for the eventual auctions, today issued a final environmental assessment (EA). The process reviewed the potential impacts of offshore wind leasing on the U.S. Outer Continental Shelf in the Gulf of Mexico and used the analysis to determine potential issues with the selected sites.
“The completion of our environmental review is an important step forward to advance clean energy development in a responsible manner while promoting economic vitality and well-paying jobs in the Gulf of Mexico region,” said BOEM Director Liz Klein. “We will continue to work closely with our task force members, ocean users, and others to ensure that any development in the region is done responsibly and in a way that avoids, reduces, or mitigates potential impacts to ocean users and the marine environment.”
The findings for today’s announcement were based on the work of the Gulf of Mexico Intergovernmental Renewable Energy Task Force, a collaboration between, Federal, state, tribal, and local government agencies. It sought to use available science and indigenous knowledge to minimize conflicts between ocean uses. BOEM reports will continue to meet with the task force as the process moves forward.
The initial call area which comprises 30 million areas was announced in November 2021 and a year later BOEM announced the first two Wind Energy Areas offshore Texas and Louisiana that total about 682,000 acres. According to the bureau, the sites were selected as they represent offshore areas that appear to be the most suitable for wind energy development.
The environmental analysis was prepared for the entire 30-million-acre Call Area to allow greater flexibility for the possible identification of additional WEAs and to provide NEPA coverage in the event that non-competitive and research leases were proposed in the call area. The analysis considered potential environmental consequences of site characterization activities (i.e., biological, archeological, geological, and geophysical surveys and core samples) and site assessment activities (i.e., installation of meteorological buoys) associated with the possibility of issuing wind energy leases in the Gulf of Mexico.
BOEM announced on February 22, 2023, its proposal for the first offshore wind lease sale in the Gulf of Mexico. If BOEM decides to proceed with the sale, the bureau will publish a Final Sale Notice at least 30 days ahead of the sale. It is widely anticipated that they will proceed with the sale in the coming months.
For any proposed offshore wind projects, BOEM will also develop Environmental Impact Statements to analyze the specific environmental consequences of the projects before deciding whether to approve them. The environmental statements would be prepared in consultation with appropriate government agencies and informed by input provided by key stakeholders, tribes, ocean users, and the public.
Why We Need Better Anchoring Systems for Floating Offshore Wind
Without more investment in anchor technology to streamline installation, the potential of floating wind to help the energy transition will be greatly reduced.
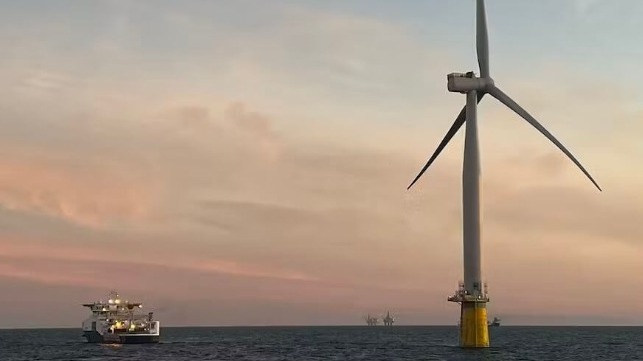
[By Benjamin Cerfontaine and Susan Gourvenec]
Growing demand for cleaner energy sources means offshore wind farms are being built all over the world. More than 5,000 turbines must be installed each year until 2050 to limit global warming to 1.5?.
But in certain regions, like California, it is difficult to build wind turbines directly on the seafloor due to the steep drop-off of the continental shelf.
Even in areas with shallow coastal waters, such as the North Sea, congestion from shipping lanes, fishing activities, marine protected areas, tourism and existing energy infrastructure all impede new turbine construction.
So it’s hardly surprising that many of these new turbines will have to be located in deeper waters further out to sea.
Floating wind turbines are emerging as a promising solution. But turbines are also getting bigger at a rapid rate – allowing electricity to be produced at a lower cost.
The blades of Hywind Scotland, the world’s first commercial floating wind farm, tower 175 metres above the sea surface – the same height as the London skyscraper known as The Gherkin.
This represents a huge technical challenge. Located in deep waters, these large floating structures must withstand the relentless push and pull of the ocean while maintaining stability to ensure ongoing energy generation.
So, how do these colossal structures remain in place?
The four types of floating wind farm platform. Acteon, CC BY-NC-ND
The floating wind turbine
The mast of a floating wind turbine is connected to a platform, which is designed to provide stability. Several different types of floating platform exist, each with the dimensions of a football pitch.
Beneath the water, mooring lines keep the turbine stable and prevent it from drifting away. Mooring lines can be either very large steel chains or synthetic ropes. Each of the three steel chains used for Hywind Scotland, for example, are approximately 900 metres long and weigh 400 tonnes.
The mooring lines are attached to the seabed with a ground anchor. Most people will be familiar with anchoring a boat or securing the guy ropes of a tent with pegs.
In both cases, the anchor (or peg) is embedded into the ground, making it harder for the anchor to become dislodged as the weight and strength of the ground has to be overcome to pull the anchor out. The anchors used for floating wind turbines are based on the same principle, but at a far greater scale.
Three main types of anchor are used to fix the floating platform to the seabed, each with unique characteristics.
Drag anchors are similar to traditional boat anchors, but can have a 6 metre wingspan and weigh up to 50 tonnes. They are dragged into the seabed by an installation vessel and embed themselves into the ground until the required holding resistance is achieved.
Pile anchors are like very large (up to 60 metres in length) but hollow nails. These anchors are hammered into the ground using an extremely heavy hammer. If the turbine is being installed above very hard soils or a rocky seabed, then a hole can be drilled to facilitate the pile installation.
Suction pile anchors are also hollow cylindrical tubes, but a sealed top cap creates suction pressure when water is pumped from inside of the pile. This forces the pile into the seabed without the need for hammering (an effect similar to the use of a plunger to unclog a drain). This is the type of anchor used to secure Hywind Scotland.
The mooring chain for a floating wind turbine at Polarbase, Hammerfest, Norway. Øyvind Gravås and Even Kleppa/Equinor, CC BY-NC-ND
Choosing the right anchor
Floating wind farms are being planned for areas such as the Celtic Sea and coastal waters west of France. However, the presence of hard rock seabeds in both areas means drag anchors will be difficult to use.
Even in dense sand, a drag anchor may only partly enter the seabed, creating inadequate support for the largest turbines. Drilled piles are the best way to anchor floating turbines to hard rock, so in this case, a driven pile might be the only option.
But driving these piles into the ground generates significant underwater noise that can be harmful for marine species. Research has also found that the movement behaviour of Atlantic cod subtly changed in response to pile driving in the North Sea.
Even small changes in movement behavior could affect individual growth and reproduction rates, potentially influencing the growth rate of entire populations.
Several techniques have now been devised to reduce noise. This includes air bubble curtains to limit the ecological impact of floating wind farms. But these techniques may result in additional costs that could make pile anchors too expensive.
The world needs a lot more wind turbines, and technology now allows installation further out to sea. But, as identified in our recent review paper, these environmental and technical challenges for anchoring the structures in place must be addressed.
Without more investment in anchor technology to streamline installation, improve anchor performance and limit damage to the natural world, the potential of floating wind to help the energy transition will be greatly reduced.
Benjamin Cerfontaine is a Lecturer in Geotechnical Engineering, University of Southampton.
Susan Gourvenec is the Royal Academy of Engineering Chair in Emerging Technologies - Intelligent & Resilient Ocean Engineering, University of Southampton.
This article appears courtesy of The Conversation and can be found in its original form here.
The opinions expressed herein are the author's and not necessarily those of The Maritime Executive.
Wind Turbine Components Arrive as Offshore Work Starts for Vineyard 1
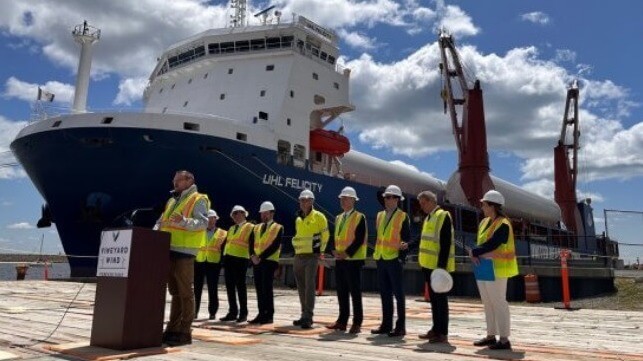
In another sign that the U.S.’s ambitions to catch up and start its offshore wind power industry are finally showing progress, the first turbine components for the Vineyard Wind project off Massachusetts arrived at the terminal in New Bedford while offshore work is scheduled to start in days. Company and government officials were on hand to mark the clear sign of progress for what is expected to be the first commercial-scale offshore wind farm in the United States.
The heavy lift vessel UHL Felicity arrived in New Bedford on May 24 carrying the components, the first load for the wind farm which will consist of 62 wind turbines. The project is using General Electric Haliade-X turbines, each capable of generating 13 megawatts of electricity, with a total output of 800 MW. The wind farm is to be located 15 miles south of Martha’s Vineyard and is scheduled to begin producing power before the end of 2023.
The tower sections for the turbines will be arriving in three sections. Once onshore in New Bedford, they will be staged at the terminal and partially assembled. They will be shipped out to the site on specialized barges with installation scheduled to begin this summer.
“After a long road, the first day of component arrival is finally here,” said Vineyard Wind CEO Klaus Moeller. “This is a great milestone for New Bedford, Vineyard Wind, and the country. We’ve been working together with Mayor Mitchell for years to achieve this and are now finally seeing the result. I am proud to introduce this technology to the US and to see the many jobs that this industry will create in action on the site to today.”
Work is accelerating at the site as company officials note that the project which is years in the planning is finally moving into construction and becoming a reality. Vineyard 1 is being developed in a joint venture between Copenhagen Infrastructure Partners (CIP) and AVANGRID. The company also reported that DEME's installation vessel the Orion is due to start the installation of the first six monopile foundations and accompanying transition pieces on May 29. After the initial foundation work, the Orion will shift to the substation installation and then return to the additional monopiles. Work is due to be completed by December.
“The arrival of turbine components for the Vineyard Wind project represents the clearest manifestation yet of what we’ve been working on for more than a decade, namely, to position New Bedford as the leading offshore wind port on the East Coast,” said New Bedford Mayor Jon Mitchell. The mayor noted that it was fitting to see the industry developing in New Bedford, which in the 19th century was also a hub in the energy industry as the leading whaling port in the United States.
While the companies were marking the delivery of the first components into the United States, in Denmark they were also marking the send-off of other key elements for Vineyard 1. The 3,200-ton substation for the wind farm was completed and departed from Semco Maritime’s facility along with a 2,000 tons jacket foundation with four piles, which form the permanent anchorage to the seabed. These components were loaded aboard a heavy lift vessel and are being shipped to Massachusetts. Vineyard will oversee the installation and Semco Maritime and Bladt Industries will oversee the offshore commissioning during the summer.