A greener, simpler way to create syngas
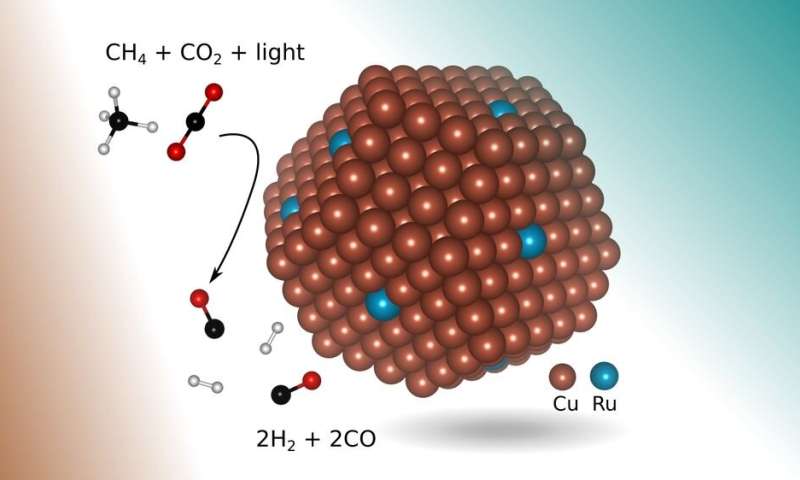
It’s possible that I shall make an ass of myself. But in that case one can always get out of it with a little dialectic. I have, of course, so worded my proposition as to be right either way (K.Marx, Letter to F.Engels on the Indian Mutiny)
Researchers realize direct synthesis of isoparaffin-rich gasoline from syngas
DALIAN INSTITUTE OF CHEMICAL PHYSICS, CHINESE ACADEMY SCIENCES
A research team led by Prof. PAN Xiulian and Prof. BAO Xinhe from the Dalian Institute of Chemical Physics (DICP) of the Chinese Academy of Sciences realized the direct synthesis of isoparaffin-rich gasoline from syngas using ZnAlOx-SAPO-11 oxide-zeolite (OXZEO) catalysts.
They elucidated the active sites of isoparaffin formation, which provided guidance for the one-step synthesis of high-quality gasoline from syngas.
This study was published in ACS Energy Letters on March 23.
Previously, the DICP team proposed a new catalyst concept based on metal OXZEO bi-functional catalysts, and it enabled the direct conversion of syngas to a variety of chemicals and fuels with high selectivity, such as light olefins, ethylene, gasoline, aromatics and oxygenates. The OXZEO concept provided a new technology platform for the highly efficient utilization of coal and other carbon resources.
In this study, they achieved 34% CO conversion and 82% gasoline selectivity by modulating the acid sites distribution of zeolite, in which the iso/n-paraffins ratio was as high as 38. By optimizing the reaction conditions, they increased the ratio of iso/n-paraffins as high as 48, which was the highest value of the iso/n-paraffins ratio reported so far.
Moreover, a 150-hour on stream test of the catalyst indicated rather stable activity in syngas-to-gasoline.
Further studies showed that the external acid sites of the zeolite could be the active sites for the formation of branched, especially the multi-branched isoparaffins.
"This study provided important guidance for the one-step synthesis of high-quality gasoline from syngas and even CO2," said Prof. PAN.
The above work was supported by the Ministry of Science and Technology of China, the National Natural Science Foundation of China, the Dalian High-level Talent Innovation Program, and the Youth Innovation Promotion Association of CAS.
ACS Energy Letters
Commentary/editorial
Not applicable
Direct Synthesis of Isoparaffin-rich Gasoline from Syngas
DALIAN INSTITUTE OF CHEMICAL PHYSICS, CHINESE ACADEMY SCIENCES
IMAGE: SCHEMATIC MECHANISM OF THE PHOTOINDUCED PCET PROCESS OVER [SO4]/CDS view more
CREDIT: DICP
Photocatalytic biomass conversion is an ideal way of generating syngas (H2 and CO) via C-C bond cleavage, which is initiated by hydrogen abstraction of O/C-H bond. However, the lack of efficient electron-proton transfer limits its efficiency. Conversional gasification of biomass into syngas needs to be operated at high temperature (400-700 °C).
Recently, a group led by Prof. WANG Feng from the Dalian Institute of Chemical Physics (DICP) of the Chinese Academy of Sciences (CAS), in collaboration with Prof. WANG Min from Dalian University of Technology, proposed a new method to realize photocatalytic conversion of biopolyols to syngas at room temperature with high efficiency.
This study was published in Journal of the American Chemical Society on April 27.
The researchers prepared surface sulfate ions modified CdS catalyst ([SO4]/CdS), which could simultaneously increase both the electron and proton transfer, thereby facilitating the generation of syngas mixture from biopolyols with high activity and selectivity.
In situ characterizations combined with theoretical calculations demonstrated that the surface sulfate ion [SO4] was bifunctional, serving as the proton acceptor to promote proton transfer, and increasing the oxidation potential of the valence band to enhance electron transfer.
Compared with pristine CdS, [SO4]/CdS exhibited 9-fold higher CO generation rate and 4-fold higher H2 generation. Through this method, a wide range of sugars, such as glucose, fructose, maltose, sucrose, xylose, lactose, insulin, and starch, were facilely converted into syngas.
This study reveals the pivotal effect of surface sulfate ion on electron-proton transfer in photocatalysis and provides a facile method for increasing photocatalytic efficiency.
###
AMERICAN CHEMICAL SOCIETY
Starting a new year, many people pledge to enact self-care routines that improve their appearance. And facial sheet masks soaked in skin care ingredients provide an easy way to do this. However, these wet masks and their waterproof packaging often contain plastics and preservatives. Now, a study in ACS Applied Materials & Interfaces reports a dry-packaged hydrating facial mask that is made of biobased and sustainable materials.
Consumers in the beauty industry are increasingly concerned about the sustainability and sourcing of personal care items, in terms of both products’ ingredients and packaging. Facial sheet masks are popular cosmetic products advertised to benefit and enhance the skin. But they are typically made with plastic backing fabrics and are packaged with wet ingredients, requiring preservatives and disposable water-tight pouches. A more environmentally friendly option would be to package the facial masks dry. So, Jinlain Hu and coworkers aimed to design a facial sheet mask with biobased materials that could be enveloped in paper and later activated to deliver moisture and nutrients.
The researchers developed a facial mask with a sheet of plant-based polylactic acid (PLA), which could repel water, and they coated it in a layer of gelatin mixed with hyaluronic acid and green tea extract. They deposited the top layer as either tiny fibers or microspheres, using electrospinning or electrospray, respectively, and tested how well the masks could transfer moisture. They found:
Finally, the team investigated how its mask’s ingredients impacted mouse cells as a proxy for reactions on skin. Fewer cells showed signals of aging when grown on the mask compared with cells grown in control conditions; the researchers attribute this to the antioxidant properties of the green tea extracts. The team says the beneficial properties of the natural ingredients and the one-way moisture-delivery design make this mask a promising alternative with a lesser environmental impact compared to traditional, wet-packed products.
The authors acknowledge funding from the City University of Hong Kong, the National Natural Science Foundation of China, and Shenzhen-Hong Kong-Macau Science & Technology Fund.
###
The American Chemical Society (ACS) is a nonprofit organization chartered by the U.S. Congress. ACS’ mission is to advance the broader chemistry enterprise and its practitioners for the benefit of Earth and all its people. The Society is a global leader in promoting excellence in science education and providing access to chemistry-related information and research through its multiple research solutions, peer-reviewed journals, scientific conferences, eBooks and weekly news periodical Chemical & Engineering News. ACS journals are among the most cited, most trusted and most read within the scientific literature; however, ACS itself does not conduct chemical research. As a leader in scientific information solutions, its CAS division partners with global innovators to accelerate breakthroughs by curating, connecting and analyzing the world’s scientific knowledge. ACS’ main offices are in Washington, D.C., and Columbus, Ohio.
To automatically receive news releases from the American Chemical Society, contact newsroom@acs.org.
Note: ACS does not conduct research, but publishes and publicizes peer-reviewed scientific studies.
Follow us: Twitter | Facebook | LinkedIn | Instagram
ACS Applied Materials & Interfaces
Electrosprayed Environment-Friendly Dry Triode-Like Facial Masks for Skincare
Lithuanian researchers investigate the possibilities of plasma gasification as an eco-friendly technique to convert used surgical masks into clean energy.
Peer-Reviewed PublicationKAUNAS UNIVERSITY OF TECHNOLOGY
IMAGE:
SAMY YOUSEF, A CHIEF RESEARCHER AT KTU FACULTY OF MECHANICAL ENGINEERING AND DESIGN
view moreCREDIT: KTU
During the COVID-19 pandemic, thousands of tons of used surgical masks were dumped every month without a real vision to manage them. Although the world has successfully passed the critical period, a serious industrial eco-solution must be developed to deal with this waste.
Researchers from Kaunas University of Technology (KTU) and Lithuanian Energy Institute, aiming to design a solution for surgical mask waste management are investigating the possibilities of plasma gasification as an eco-friendly technique to convert surgical mask waste into clean energy products.
After conducting a series of experiments, they obtained synthetic gas (aka syngas) with a high abundance of hydrogen.
“There are two ways of converting waste to energy – by transforming solid waste into liquid product, or gases. Gasification allows converting huge amounts of waste to syngas, which is similar to natural and is a composition of several gases (such as hydrogen, carbon dioxide, carbon monoxide, and methane). During our experiments, we played with the composition of this synthetic gas and increased its concentration of hydrogen, and, in turn, its heating value,” says Samy Yousef, a chief researcher at Kaunas University of Technology, Lithuania.
For the conversion of surgical masks, the researchers applied plasma gasification on defective FFP2 face masks, which were shredded beforehand into a uniform particle size, and then converted to granules that could be easily controlled during treatment.
The highest yield of hydrogen was obtained at an S/C (steam-to-carbon ratio) of 1.45. Overall, the obtained syngas showed a 42% higher heating value than that produced from biomass.
Traditional waste management technique was improved
Yousef’s research team, composed of scientists from two Lithuanian research institutions, KTU and Lithuanian Energy Institute, are working on the topics of recycling and waste management, and are always looking for waste, which is present in huge amounts and has a unique structure. In their work, they have conducted pyrolysis experiments on cigarette butts, used wind turbine blades, and textile waste, which have all shown promising results for upscaling and commercialization. Yet, this time, for the recycling of surgical masks, a different method was applied.
“Gasification is a traditional waste management technique. Differently from pyrolysis, which is still a new and developing method we don’t need much investment in developing infrastructure. Arc plasma gasification, which we have applied for the decomposition of surgical masks, means that under high temperatures generated by arc plasma, we can decompose face masks to gas within a few seconds. In pyrolysis, it takes up to an hour to get the final product. In advanced gasification, the process is almost instantaneous,” explains Yousef.
He says that advanced gasification techniques, such as plasma gasification, are more efficient in obtaining a better concentration of hydrogen (up to 50%) within synthetic gas production. Moreover, plasma gasification decreases the amount of tar in the syngas, which makes its quality higher.
Hydrogen-rich gas has better heating values
According to Yousef, plasma gasification is one of the best methods to obtain synthetic gas, which is rich in hydrogen.
“Hydrogen increases the heating value of the synthetic gas,” explains Yousef and continues describing the different types of hydrogen: grey is obtained from natural gas or methane, green – from green sources (e.g., electrolysis), blue – from steam reforming.
“Maybe we could call our black hydrogen, as it’s made from waste?” he says half-jokingly.
The yield of syngas was around 95% of the total amount of feedstock. The remaining products were soot and tar. The analysis revealed that benzene, toluene, naphthalene and acenaphthylene were the main compounds in collected tar. According to the researchers, it can be used as a clean fuel in different industries with low carbon emissions.
The soot was formulated in the last stage of plasma gasification. Its main component is black carbon, which can have numerous applications related to energy, wastewater treatment, and agriculture, or can be used as a filler material in composites.
The researchers believe that their proposed method for surgical mask waste recycling has a high potential to be commercialized. According to Yousef, a researcher from KTU, their main aim was to obtain synthetic gas, which is rich in hydrogen. Although hydrogen can be separated from the obtained syngas, it can also be used as a mixture of gases. As such, it already has half a higher heating value than that produced from biomass.
International Journal of Hydrogen Energy
Experimental study
Not applicable
Plasma steam gasification of surgical mask waste for hydrogen-rich syngas production
Mohammad Asadi partners with SHV Energy to distribute electrolyzer device that can convert carbon dioxide into propane in a way that is economically viable and scalable
ILLINOIS INSTITUTE OF TECHNOLOGY
IMAGE: ILLUSTRATION OF ELECTROLYZER, WHICH USES A NOVEL CATALYST TO CONVERT CARBON DIOXIDE INTO PROPANE. view more
CREDIT: ILLINOIS INSTITUTE OF TECHNOLOGY
CHICAGO—August 18, 2023—A paper recently published in Nature Energy based on pioneering research done at Illinois Institute of Technology reveals a promising breakthrough in green energy: an electrolyzer device capable of converting carbon dioxide into propane in a manner that is both scalable and economically viable.
As the United States races toward its target of net-zero greenhouse gas emissions by 2050, innovative methods to reduce the significant carbon dioxide emissions from electric power and industrial sectors are critical. Mohammad Asadi, assistant professor of chemical engineering at Illinois Tech, spearheaded this groundbreaking research.
“Making renewable chemical manufacturing is really important,” says Asadi. “It’s the best way to close the carbon cycle without losing the chemicals we currently use daily.”
What sets Asadi’s electrolyzer apart is its unique catalytic system. It uses inexpensive, readily available materials to produce tri-carbon molecules—fundamental building blocks for fuels like propane, which is used for purposes ranging from home heating to aviation.
To ensure a deep understanding of the catalyst’s operations, the team employed a combination of experimental and computational methods. This rigorous approach illuminated the crucial elements influencing the catalyst’s reaction activity, selectivity, and stability.
A distinctive feature of this technology, lending to its commercial viability, is the implementation of a flow electrolyzer. This design permits continuous propane production, sidestepping the pitfalls of the more conventional batch processing methods.
“Designing and engineering this laboratory-scale flow electrolyzer prototype has demonstrated Illinois Tech’s commitment to creating innovative technologies. Optimizing and scaling up this prototype will be an important step toward producing a sustainable, economically viable, and energy-efficient carbon capture and utilization process,” says Advanced Research Projects Agency-Energy Program Director Jack Lewnard.
This innovation is not Asadi’s first venture into sustainable energy. He previously adapted a version of this catalyst to produce ethanol by harnessing carbon dioxide from industrial waste gas. Recognizing the potential of the green propane technology, Asadi has collaborated with global propane distributor SHV Energy to further scale and disseminate the system.
“This is an exciting development which opens up a new e-fuel pathway to on-purpose propane production for the benefit of global users of this essential fuel,” says Keith Simons, head of research and development for sustainable fuels at SHV Energy.
Illinois Tech Duchossois Leadership Professor and Professor of Physics Carlo Segre, University of Pennsylvania Professor of Materials Science and Engineering Andrew Rappe, and University of Illinois Chicago Professor Reza Shahbazian-Yassar contributed to this work. Mohammadreza Esmaeilirad (Ph.D. CHE ’22) was a lead author on the paper.
Disclaimer: “Research reported in this publication was supported by the National Science Foundation under Award Number 2135173, the Advanced Research Projects Agency-Energy under Award Number DE-AR0001581, and SHV Energy. This content is solely the responsibility of the authors and does not necessarily represent the official views of the National Science Foundation, the Advanced Research Projects Agency-Energy, or SHV Energy.”
Mohammad Asadi, “Imidazolium Functionalized Transition Metal Phosphide Catalysts for Electrochemical Carbon Dioxide Conversion to Ethanol,” National Science Foundation; Award Number 2135173
Mohammad Asadi, “Direct Conversion of Flue Gas to Value-Added Chemicals Using a Carbon-Neutral Process,” Advanced Research Projects Agency-Energy; Award Number DE-AR0001581
Nature Energy
Experimental study
Not applicable
Imidazolium-functionalized Mo3P nanoparticles with an ionomer coating for electrocatalytic reduction of CO2 to propane
17-Aug-2023
by University of Colorado at Boulder
Researchers at the University of Colorado have developed a new and efficient way to produce green hydrogen or green syngas, a precursor to liquid fuels. The findings could open the door for more sustainable energy use in industries like transportation, steelmaking and ammonia production.
The new study, published Aug. 16 in the journal Joule, focuses on the production of hydrogen or syngas, a mixture of hydrogen and carbon monoxide that can be converted into fuels like gasoline, diesel and kerosene. The CU Boulder team lays the groundwork for what could be the first commercially viable method for producing this fuel, entirely using solar energy. That might help engineers to generate syngas in a more sustainable way.
The group was led by Al Weimer, professor in the Department of Chemical and Biological Engineering.
"The way I like to think about it is some day when you go to the pump you'll have, for example, unleaded, super unleaded and ethanol options, and then an additional option being solar fuel, where the fuel is derived from sunlight, water and carbon dioxide," said Kent Warren, one of two lead authors of the new study and a research associate in Chemical and Biological Engineering. "Our hope is that it will be cost-competitive to the fuels sourced from the ground."
Traditionally, engineers produce hydrogen gas through electrolysis, or using electricity to split molecules of water into hydrogen and oxygen gas. The team's "thermochemical" approach, in contrast, uses heat generated by solar rays to complete those same chemical reactions. The methods can also split molecules of carbon dioxide pulled from the atmosphere to produce carbon monoxide.
Scientists had previously shown that such an approach to making hydrogen and carbon monoxide was possible, but might not be efficient enough to produce syngas in a commercially viable manner.
In the new study, the researchers demonstrated that they can conduct these reactions at elevated pressures, in part by employing iron-aluminate materials, which are relatively inexpensive and abundant in the Earth. Those higher pressures allowed the team to more than double its production of hydrogen.
More information: Justin T. Tran et al, Pressure-enhanced performance of metal oxides for thermochemical water and carbon dioxide splitting, Joule (2023). DOI: 10.1016/j.joule.2023.07.016