JIMCO Technology Fund joins a $1.8bn funding round for fusion energy
Updated 02 December 2021
ARAB NEWS
https://arab.news/bg6py
The Saudi-based Jameel Investment Management Co. has participated in a $1.8billion funding round for a US fusion energy company, it has been announced.
JIMCO has invested an undeclared amount in Commonwealth Fusion Systems, a company founded in 2018 that is building the world’s first net-energy-giant fusion system.
“The world is ready to make big investments in commercial fusion as a key part of the global energy transition,” the chief executive officer of CFS, Bob Mumgaard, said.
The High-Temperature Superconducting magnet technology will be used in SPARC, a fusion device that is currently being constructed in Massachusetts and expected to demonstrate net energy from fusion by 2025.
This comes amid the parties’ steps towards a more sustainable future to mitigate climate change.
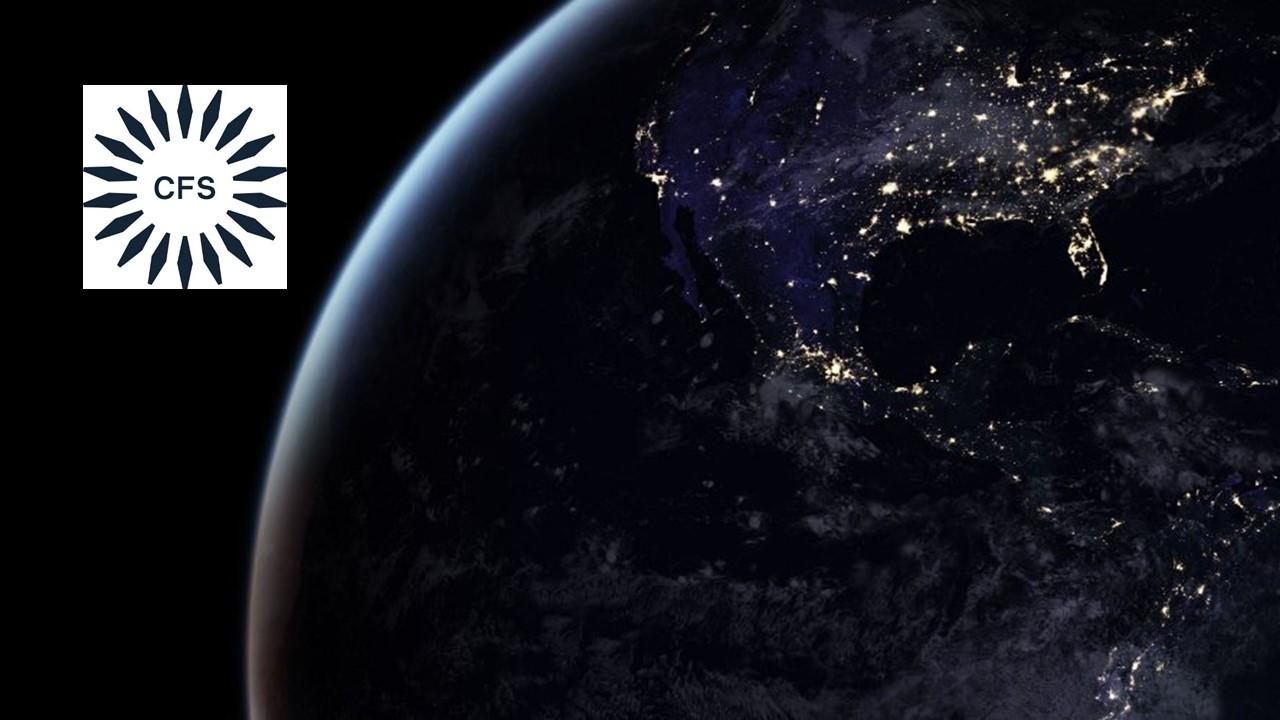
SOURCE: COMMONWEALTH FUSION SYSTEMS TWITTER
DEC. 2 2021
Commonwealth Fusion Systems (CFS) recently raised $1.8 billion from a group of prominent investors including Bill Gates and Salesforce CEO Marc Benioff. Many prospective investors want to know whether CFS stock is publicly traded and how to buy it before the Commonwealth Fusion Systems IPO.
The efforts to combat climate change have created many opportunities for investors. Some investors are picking up EV stocks like Tesla while others are investing in companies that build systems that produce renewable energy from wind, solar, or other clean sources. CFS belongs to the renewable energy producer category.
What does Commonwealth Fusion Systems do?
CFS is developing high-tech machines that can produce clean and renewable electricity through a nuclear fusion process. Its approach contrasts with the fission process used in current nuclear power plants.
Fusion power plants promise many benefits over existing fission nuclear reactors. For example, fusion plants will be more efficient in converting fuel to electricity and won't produce radioactive wastes
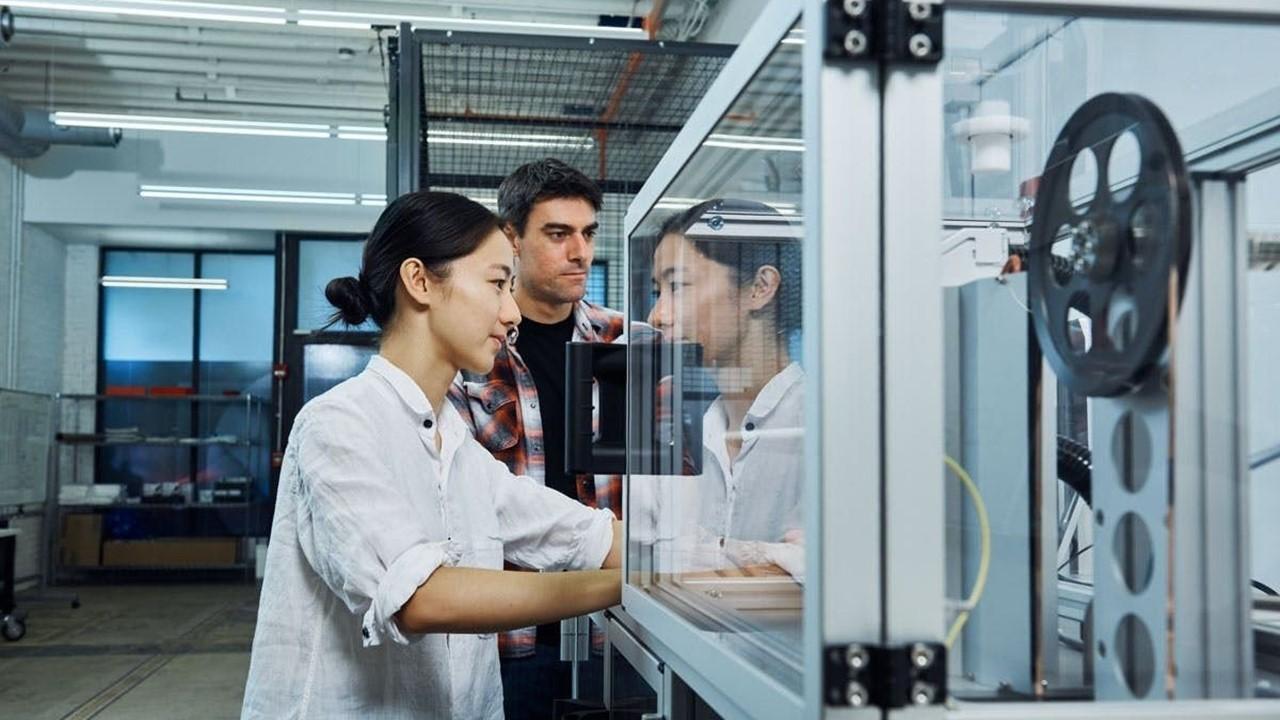
SOURCE: COMMONWEALTH FUSION SYSTEMS
What other companies are building fusion power reactors?
A growing number of startups are joining the fusion electricity efforts and many deep-pocketed investors are coming out to back them. In addition to Commonwealth Fusion Systems, the other fusion startups are Helion Energy, Zap Energy, and Canada-based General Fusion.
Helion raised $500 million in November 2021 and might access an additional $1.7 billion if it meets certain targets. General Fusion recently raised $130 million from investors including Jeff Bezos. General Fusion is preparing for another fundraising in 2022 that could bring it even more money.
CFS has raised more than $2 billion since its founding in 2018. It plans to use the $1.8 billion fund raised recently to develop and operate a pilot fusion plant and start the work on a commercial plant.
Who owns Commonwealth Fusion Systems?
CFS started as a project of the Massachusetts Institute of Technology before it branched out. But it continues to collaborate with MIT on the fusion electricity program. After separating from MIT, the startup received $50 million in initial funding from Italian energy company Eni. The Italian multinational is excited about fusion energy prospects and it’s willing to put more money on promising projects.
In 2019, CFS raised $115 million in an investment round that also included Eni and investors like Bill Gates and Vinod Khosla. The startup is also backed by George Soros and John Doerr. The other investors are Singapore's Temasek, Google, Norway's Equinor, and JIMCO Technology.
Is Commonwealth Fusion Systems a publicly traded company?
Massachusetts-based Commonwealth Fusion Systems is a private company. The business is led by CEO Bob Mumgaard. The executive has said that the world is ready to invest in fusion electricity, which has a huge potential in accelerating the global energy shift.
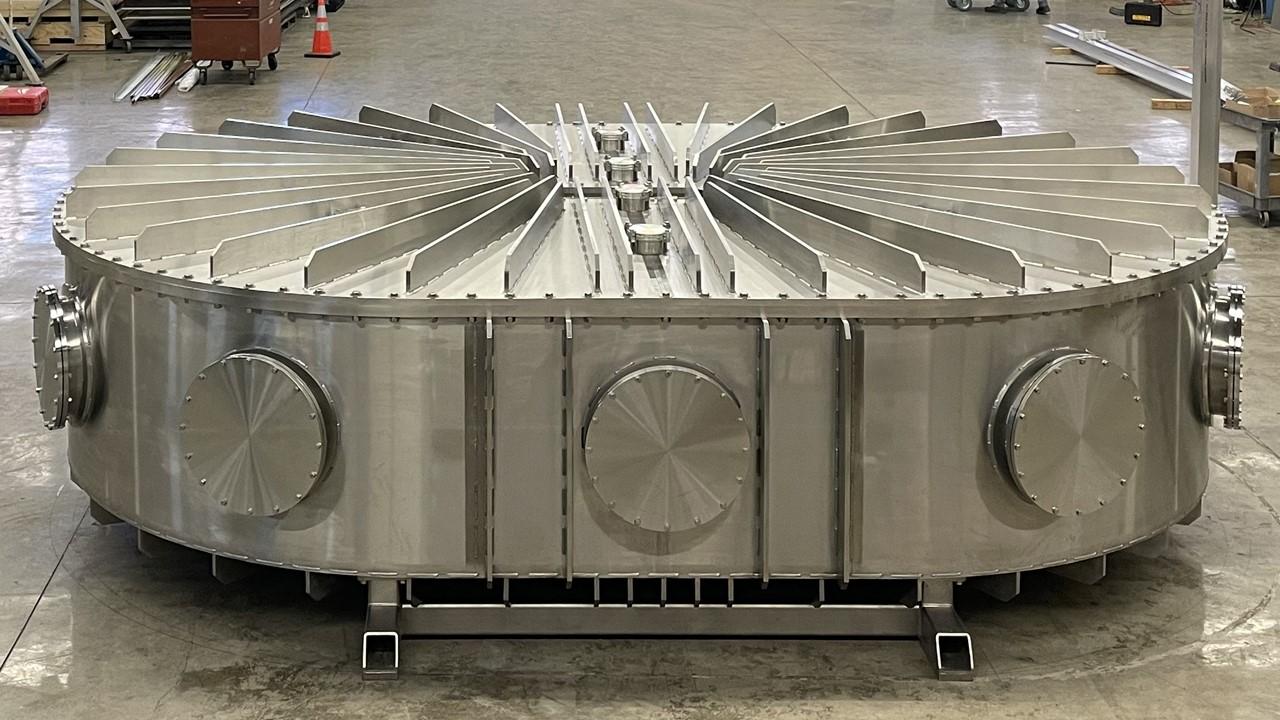
SOURCE: COMMONWEALTH FUSION SYSTEMS FACEBOOK
Does Commonwealth Fusion Systems have an IPO plan?
CFS joins Elon Musk-led SpaceX as another highly anticipated IPO. Many investors think that they could be lucrative investments. Until now, neither Mumgaard nor investors like Gates have publicly discussed IPO plans for the startup.
However, sooner or later Commonwealth Fusion Systems might want to go public to raise more money as its cash need grows. The startup might need about $3 billion to set up the first commercial fusion reactor that it aims to get ready to start generating electricity by the early 2030s. CFS also plans to build more power plants in the future and even sell its fusion machines.
Investors can buy Commonwealth Fusion Systems stock before the IPO.
If you can’t wait for the Commonwealth Fusion Systems IPO, you can try to buy the stock in the private capital market. However, that might be a tall order for retail investors with small money. To participate in the private capital market, you might need to have $1 million in net worth or meet accredited investor requirements outlined in the SEC regulations.
December 02, 2021
Bruce Gellerman
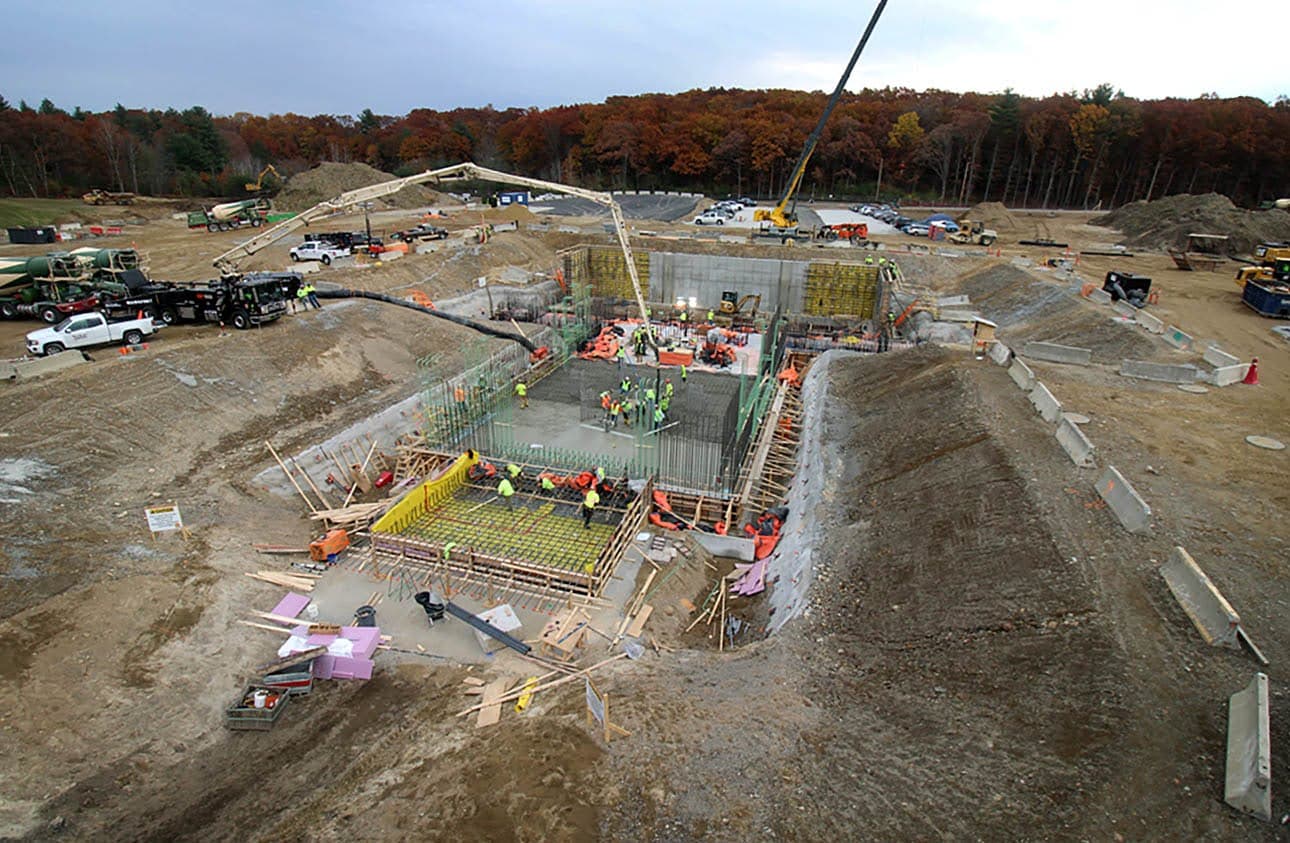
Some of the same billionaires who pioneered the commercialization of space are now using their fortunes to fund companies to create the energy source of the stars on earth. And a new round of funding is sending MIT spin-off Commonwealth Fusion Systems into orbit.
The start-up company just closed on a $1.8 billion funding round making it the largest in Massachusetts history. Among the backers were billionaire Bill Gates, George Soros and venture capitalist John Doerr.
WBUR is a nonprofit news organization and our coverage relies on your financial support. Please give today.
Commonwealth Fusion predicts it will have the world’s first net-energy fusion device by 2025 and is already building a factory in Devens to make the machine.
Work is in high gear as Richard Holcomb, director of construction and facilities, walks the 47 acre site in Devens.
"Careful," he says, stepping over a just poured foundation wall.
Holcomb has worked on a lot of big projects, but he’s never built anything like this. The concrete walls? They’re 8 feet thick.
"All of it screamed at me like … wow, this is going to be amazing," Holcomb says. "So if there was an opportunity I had to be a part of it."
Holcomb works for Cambridge-based Commonwealth Fusion Systems. The campus he's building will be home to a factory producing devices that do what the stars do: convert mass into energy.
The first two buildings at Devens will house the company's headquarters and magnet manufacturing operation.
The second building will be home to its SPARC device, designed to be the world’s first net-positive fusion machine. It's a half-size prototype of a commercial device the company predicts will generate low cost, carbon-free electricity to the grid.
SPARC uses hydrogen, the most abundant element in the universe. With one proton, one electron and no neutrons, it's the simplest element found in the universe.
But fusing atoms isn't easy and harnessing the power released from the process has eluded scientists for 70 years. But now, using a variety of technologies, they are closer than ever to making a fusion device that can produce more energy than it took to start the reaction.
An MIT breakthrough and spinoff
The technology behind SPARC was created and tested in a cavernous lab on the campus of MIT in a building that was once a Nabisco cookie warehouse.
"We needed to be a fairly large room because we built the world’s largest fusion magnet in this room," says Bob Mumgaard, CEO and founder of Commonwealth Fusion Systems. Mumgaard got his Ph.D at MIT’s Plasma Science and Fusion Center.
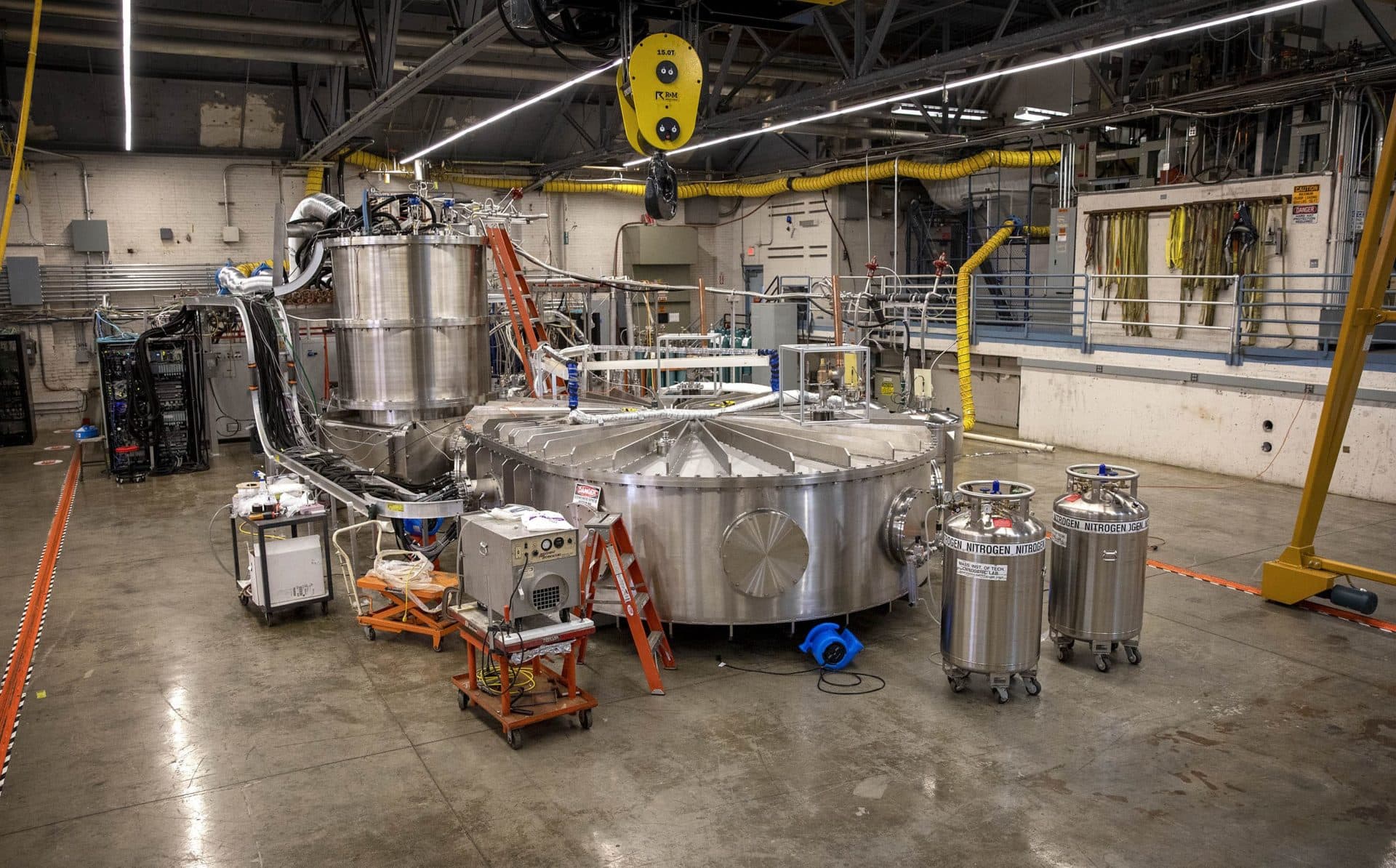
The research center and Mumgaard’s company are collaborating to build a device that replicates on earth what intense gravity does in the center of stars. In stars, gravity compresses and heats hydrogen atoms into a plasma. The super hot conditions rip the atoms apart, releasing their protons and electrons, which under the intense stellar gravity, fuse together creating a tiny amount of helium and a huge amount of energy. Think the stuff that is used in balloons and Einstein's famous equation: E=MC2. Energy equals Mass times the speed of light (186,000 miles a second) squared. That's a lot of energy from a small amount of mass.
Theoretically, a fusion reactor fueled with a quart of hydrogen derived from seawater could heat 10,000 homes for a year. It's estimated that just 70 tons of hydrogren in a fusion plant could replace the energy produced by all of India's coal power plants.
The key to making fusion working on earth is controlling the super-hot hydrogen plasma in a device known as a tokamak, a bagel-shaped machine that uses super-powerful magnets to compress the plasma.
An effort by 35 nations has spent more than $20 billion building an experimental tokamak in the south of France. Known as ITER, it will weigh four times as much as the Eiffel Tower, but is not designed to produce net energy. It's a research device.
Building a better bagel magnet
Commonwealth Fusion Systems took different approach.
"You basically have to put a sun in a bottle," says Mumgaard, "It turns out, if you build a magnetic bottle that can actually hold the fuel at the same conditions stars get to, you can create and sustain fusion."
The philosophy at Commonwealth Fusion Systems is that, by building a smaller device, they can make commercially fusion plants sooner and cheaper. SPARC will be just 1/40th the size ITER
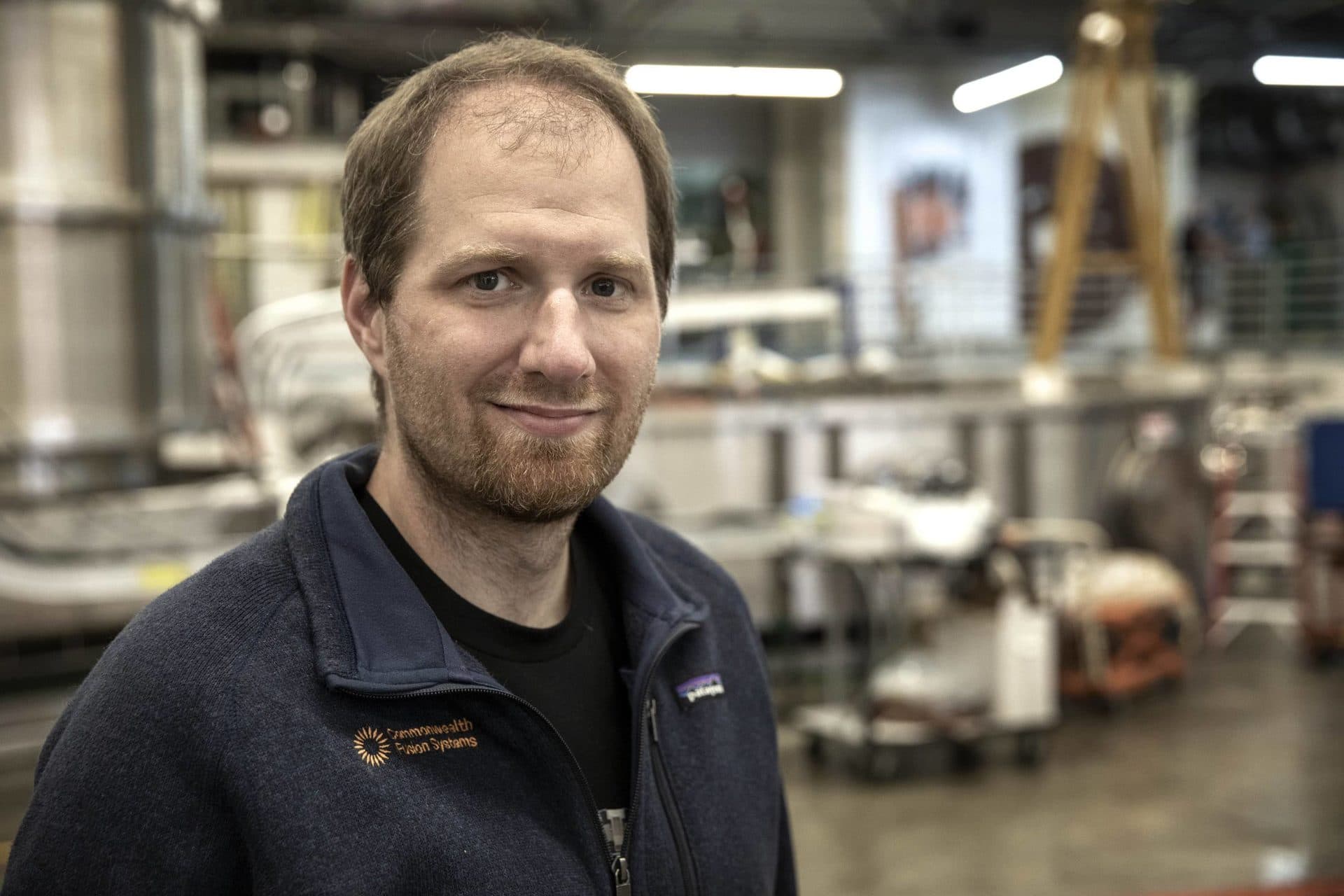
The critical component MIT and Commonwealth Fusion built was the world’s most powerful superconducting magnet. It's encased in a stainless steel vacuum chamber, surrounded by tanks of liquid nitrogen.
"Buried inside there," says Mumgaard, "is a magnet that’s 10 tons, about 10 feet tall and it has the distinction of being made out of a material that allows it to go to a very high magnetic field."
The material is called high temperature superconducting wire. Actually, it's flat like a ribbon and the company is the largest buyer of the material in the world.
In a recent test, the new magnet was 400,000 times stronger than the earth’s magnetic field. Seven peer-reviewed research papers found if you could build magnets this powerful, it should be possible to build a working tokamak that produces net energy.
When you're hot you're hot. When you're not you're not.
"So the magnets will operate at 20 kelvin, roughly minus 400 degrees Fahrenheit," says Joy Dunn, head of operations for the company. That's relatively warm by superconducting standards. At this temperature the superconducting wires lose all resistance to the flow of electrons. This enables the magnets to compress the plasma to superhot temperatures and pressure, creating the conditions to make fusion energy inside the tokama.
"On the other side of the wall of the vacuum vessel, we’re operating the plasma at about 100 million degrees celsius, so it’s going to be largest thermal gradient in the world in just a matter of inches," Dunn says.
"If you look at what needs to be done for climate, to keep the planet in a livable range, we will not be able to build these things fast enough."BOB MUMGAARD
Inside the tokamak, the plasma fuel will be five times hotter than the center of the sun. But it's delicate, so there's nothing to be afraid of, says Mumgaard.
"Some people think of fusion as like lava … you know, hot like lava ... but that’s actually not what it is," he says. "It’s actually closer like a candle in the wind."
The conditions to make fusion in a tokamak are so difficult to create and sustain, which makes the devices inherently safe, says Mumgaard. They can't melt down.
"If you think about it, stars are out in space, they don’t touch anything," he says. "And that’s what you have to basically build in a fusion machine. And the minute it touches something, it doesn’t melt through like lava. It extinguishes like a flame."
Five years ago a tokamak at MIT's Plasma Science and Fusion Center produced, for a few milliseconds, the intense pressure and temperature needed to make fusion. The Center's director, Dennis Whyte, says the magnets used in that device, were made with ordinary copper wire.
"And when that turned on to produce that confining magnetic field, it consumed over 200 million watts of electrical power," he says. "So you say, 'Well, what a great scientific achievement; hotter than the center of the sun' ... but it's hard to imagine it as a practical power source because you're using so much electricity to generate the magnetic field."
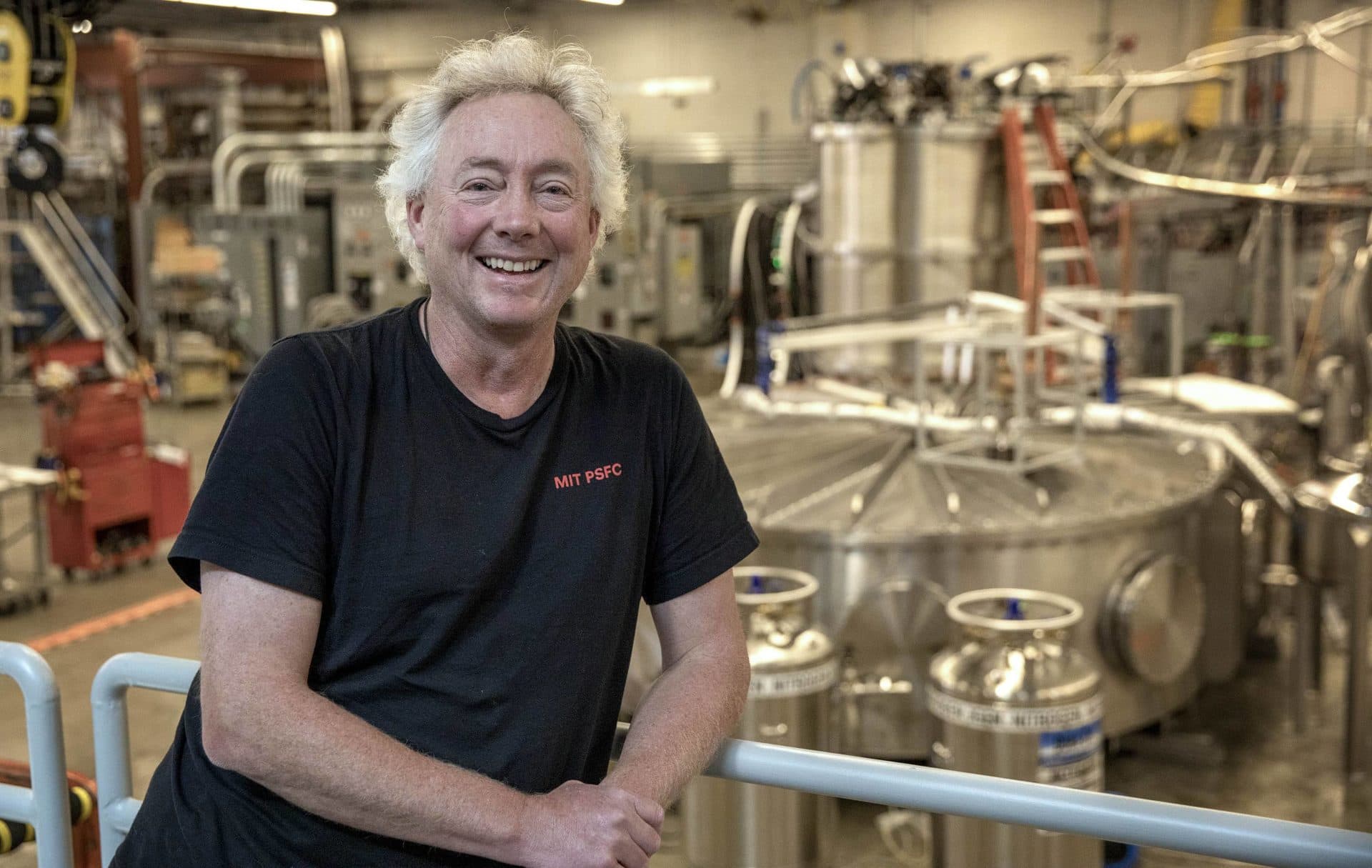
But the new high temperature superconducting magnet, like those that will be used in Commonwealth Fusion’s SPARC device, will consume just 20 watts,1/10,000,000th the amount of energy as the copper wire magnets. It means far lower costs to operate the company's device, making commercial fusion financially feasible.
"The idea is you get one major disruptive technological breakthrough and it speeds everything else up," Whyte says. "But the technology didn’t exist until it did a few weeks ago ... here."
MIT and Commonwealth Fusion Systems have formed a unique corporate-academic collaboration. They share a common agenda — making fusion energy viable — but have separate agendas. The company wants to make money; the University wants discoveries about the fundamental energy that powers the universe.
"Fusion is the greatest technological challenge that I think humanity has ever undertaken," says British plasma physicist Arthur Turrell. In his new book, “The Star Builders and The Race to Power the Planet,” he says we are closer than ever in achieving net energy from fusion devices and credits the emergence of private sector funding. "It’s not really about time," he said in a recent interview. "It’s about the investment that we’re putting into it as a society and the kind of priority that we give it and the number of people who are working on it."
The race to make commercial fusion heats up
There are about two dozen companies competing to produce fusion energy devices, promising unlimited safe power, free of carbon emissions.
Helion in Everett, Washington is backed by tech billionaire Peter Theil. Jeff Bezos is behind General Fusion in British Columbia, Canada, and Bill Gates has invested in Commonwealth Fusion Systems, which will have 300 workers when the Devens is
Mumgaard predicts that, by 2025, SPARC will produce ten times more energy than it consumes, and the company will have a commercial fusion device, capable of powering a town, in the early 2030s. He says the company will be selling them around the world.
"If you look at what needs to be done for climate, to keep the planet in a livable range, we will not be able to build these things fast enough," he says.
It’s a hopeful story, says Mumgaard. One that is unfolding in Devens, 35 miles west of MIT and 93 million miles from the sun.
This segment aired on December 2, 2021.
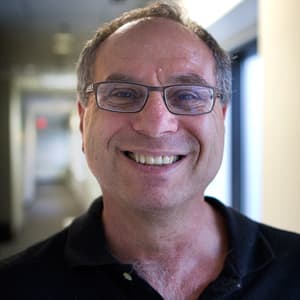
Bruce Gellerman Senior Reporter
Bruce Gellerman is an award-winning journalist and senior correspondent, frequently covering science, business, technology and the environment.