H2 NEWZ
Hydrogen hubs too reliant on fossil fuels, expert says
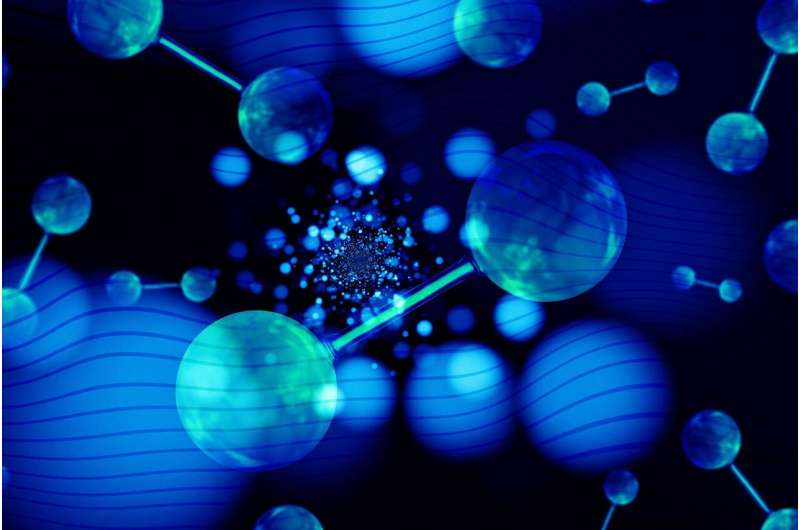
The Biden administration has announced the locations of seven regional manufacturing hubs that will receive a portion of $7 billion in initial funding to help jumpstart a hydrogen industry.
Hydrogen is seen by some as a cleaner alternative to fossil fuels. But others note that that the process still relies heavily on fossil fuels as a source feedstock.
Robert Howarth is a professor of ecology and environmental biology and a faculty fellow at Cornell's Atkinson Center for Sustainability. Howarth's research shows that "blue hydrogen," which uses methane from natural gas, may harm the climate more than burning fossil fuel.
Howarth says, "It is extremely disappointing to see the Biden administration provide funds for hydrogen hubs which will be based on fossil fuels, even with the carbon capture. It takes a lot of natural gas to make hydrogen, since the methane in the natural gas is the chemical feedstock for the process, and natural gas is also burned to power the chemical process of breaking the methane down into hydrogen and carbon dioxide. So, the emissions of carbon dioxide are quite high.
"'Blue hydrogen' is an invention of the oil and gas industry, a marketing term they came up with only within the last eight years. The concept is to capture the carbon dioxide that is released when the methane breaks down. Unfortunately, this capturing also takes energy, which is met by burning even more natural gas. And the carbon capture is far from perfect: significant amounts of carbon dioxide are still released to the atmosphere.
"It is simply not possible to develop, process, transport, and store natural gas without some of it being emitted to the atmosphere unburned as methane. The quantity may seem low, but methane is an incredibly powerful greenhouse gas, more than 80 times more powerful than carbon dioxide as an agent of global warming.
"As for the future of hydrogen in a decarbonized energy future, there is a role, but only for 'green hydrogen,' that is hydrogen made from 100% renewable electricity used to break water down into hydrogen and oxygen, in a process called 'electrolysis,' with no release of carbon dioxide."
by Raven Wuebker, Texas A&M University
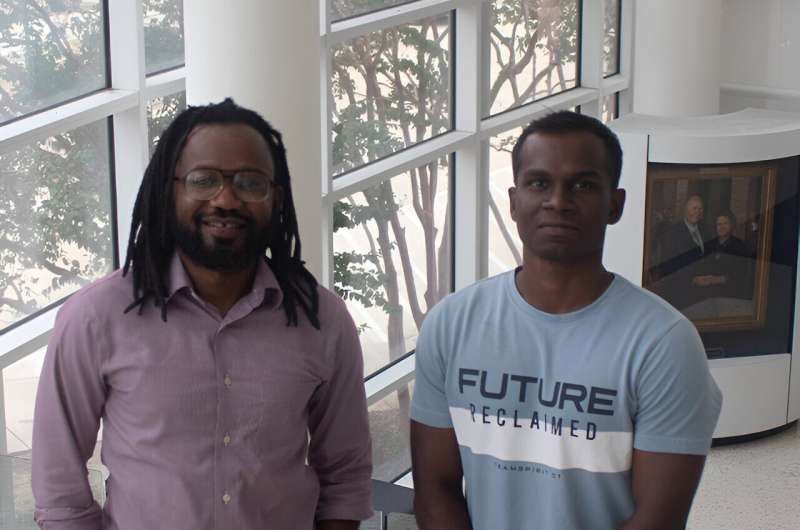
A sustainable route to green hydrogen production is becoming possible through the use of efficient electrocatalysts in research by Texas A&M University chemical engineering professor Dr. Abdoulaye Djire.
In CHEM Catalysis, Djire, chemical engineering graduate student David Kumar Yesudoss and materials science and engineering professor Dr. Miladin Radovic explain their research using MXenes—a new class of 2D-layered material—as a catalyst supporting Ru-atom for hydrogen evolution reaction (HER) catalysis for green hydrogen production.
The goal is to produce green hydrogen using cheap, earth-abundant materials that use renewable electricity. Platinum—an expensive noble metal—is the current benchmark catalyst for this reaction. Using these inexpensive catalysts instead of platinum will significantly reduce the cost of the resulting hydrogen technology, Djire said.
"My work is centered around designing and evaluating materials to be used as catalysts for sustainable chemical production," Yesudoss said. "We have been able to reduce the cost of catalysts that are used in producing green hydrogen by half, which I think is really significant."
More than 95% of hydrogen used in the chemical industry is produced through steam methane reforming—a fossil fuel method with negative environmental impacts, Djire said.
The existing commercial method of producing hydrogen is not sustainable and adds to global warming. Djire said this work will pave the way for sustainable hydrogen technologies.
"We showed the reaction rate of the electrochemical conversion processes could be increased by modifying the electrochemical responses of these 2D nanostructured materials (called MXenes) fabricated in our laboratory at Texas A&M University," Djire said. "By inserting metal, we were able to tune inexpensive materials and enhance their performance to match closely that of noble metals. Specifically, into the structure of the material, we can enhance the electro-catalytic performance of the material significantly."
Ultimately, the group aims to further lower the cost of the system by refining the particle size down to individual atoms.
"Such noble metals are hard to mine; our approach will make sure each atom is effectively utilized for green hydrogen production," Yesudoss said. "Roughly, the size of one atom is less than a nanometer. So, we are talking about 50,000 times smaller than a human hair."
The group used density functional theory to show synergistic effects between Ru and MXene that was performed by their collaborator Dr. Kingsley Obodo from North-West University in South Africa. This collaboration was established through the U.S.-Africa Frontiers of Science, Engineering and Medicine symposium in Nairobi, Kenya, last year, where Djire and Obodo were both invited participants.
"In this study, we opened an avenue for one more, and possibly most promising, application of MXenes as catalysts for HER," Radovic said.
Results showed the Ru atoms attach preferably to the surfaces of the MXene. From these findings, a new approach of tuning the electrocatalytic activity of MXenes was found to accelerate the development of cost-effective, efficient and sustainable hydrogen technology.
"If further developed, this technology has the potential to revolutionize the chemical industry," Djire said.
Additional participating collaborators include graduate student Ekenedilichukwu Uwadiunor and undergraduate student Hoang Nguyen from the Artie McFerrin Department of Chemical Engineering at Texas A&M along with graduate students Vrushali Kotastane and Eugenie Pranda from the Department of Materials Science and Engineering at Texas A&M and Dr. Kingsley Obodo from HySa Infrastructure at North-West University in South Africa.
During the U.S.-Africa Frontiers symposium last year, Djire met Obodo and noticed his work involves computational work, where they use machine learning, density and functional theory. From there, the partnership began.
More information: Ekenedilichukwu Uwadiunor et al, Pt-like catalytic activity from an atomistically engineered carbonitride MXene for sustainable hydrogen production, Chem Catalysis (2023). DOI: 10.1016/j.checat.2023.100634
Journal information: Chem Catalysis
Provided by Texas A&M University
Cheap and efficient catalyst could boost renewable energy storage
New catalyst could provide liquid hydrogen fuel of the future
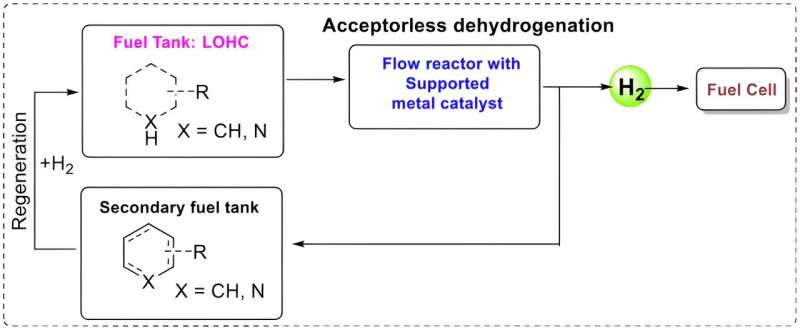
Researchers at Lund University in Sweden are investigating a car fuel comprised of a liquid that is converted to hydrogen by a solid catalyst. The used liquid is then emptied from the tank and charged with hydrogen, after which it can be used again in a circular system that is free from greenhouse gas emissions.
Lund researchers have demonstrated that the method works, and while it is still basic research, it has the potential to become an efficient energy-storage system in the future.
"Our catalyst is one of the most efficient around, at least if you look at publicly available research," says Ola Wendt, professor at the Department of Chemistry at Lund University, and one of the authors.
The findings are published in the journal Catalysis Science & Technology.
Finding alternative ways of producing, storing and transforming energy in order to reduce carbon dioxide emissions from fossil fuels is necessary to reduce the impact on the climate. One way involves much-talked-about hydrogen gas, which many see as a future solution for energy storage. Nature stores energy in chemical bonds, and hydrogen contains the highest energy density in relation to its weight.
"However, gas can be difficult to handle, so we are looking at liquid fuel charged with hydrogen that can be delivered at a pump, in a way broadly similar to what happens at petrol stations today," says Wendt.
The concept is known as LOHC (liquid organic hydrogen carriers) and is not new as such. The challenge is in finding as efficient a catalyst as possible, that can extract the hydrogen from the liquid.
The system is intended to work using a liquid that is "charged" with hydrogen. The liquid is pumped through a solid catalyst which extracts the hydrogen. This can be used in a fuel cell—which converts chemical fuel to electricity—while the "spent" liquid carries on to another tank. The only emission is water.
The spent liquid can then be emptied at a filling station before refueling with new, charged liquid. This would probably mean large scale production of the substance, comparable to today's oil refineries.
"We converted more than 99 percent of the hydrogen gas that was present in the liquid," says Wendt.
Researchers have also been calculating whether it might be possible to use the fuel for larger vehicles such as buses, trucks and aircraft.
"With the large tanks that they have, it might be possible to cover almost the same distance as you can with a tank of diesel. You would also convert around 50 percent more energy compared to compressed hydrogen," Wendt explains.
The liquids used are isopropanol (which is a common ingredient in screenwash) and 4-methylpiperidine.
Does this sound a little too good to be true? Yes—for now at least, a number of challenges remain. One is that the lifespan of the catalyst is rather limited. Another is that iridium, which the catalyst is based on, is a precious metal.
Wendt cautions, "But we estimate that you need about two grams of iridium per car. This could be compared to today's exhaust-cleaning catalytic converters, which contain about three grams of platinum, palladium and rhodium, which are also precious metals."
This is a technical solution based on basic research. If a decision were made to go for a finished product, Wendt believes that the concept could be ready in ten years' time—provided that it is economically viable and that there is interest from society.
Another problem is how hydrogen is produced—today, most production is not climate-friendly. The hydrogen then must be stored and transported in an effective way, which is not that straightforward today. There are also the risks of refueling with compressed hydrogen. The Lund researchers hope to solve this with their method.
"Ninety-eight percent of all hydrogen today is fossil-based, produced from natural gas. The biproduct is carbon dioxide. From an environmental point of view, the notion of producing hydrogen for steel, batteries and fuel is pointless if it is done using natural gas," says Wendt, but he explains that there is a lot of research going on into how "green hydrogen" might be produced by splitting water into hydrogen and oxygen with the help of renewable energy.
At the same time, he believes that political decisions are required for renewable and climate-friendly alternatives to gain a proper foothold.
"It needs to be cheaper, and it takes political decisions. Renewables have no chance of competing with something that you just dig out of the ground, where transport is almost the only cost, as is the case with fossil fuels," he concludes.
More information: Kaushik Chakrabarti et al, Acceptorless dehydrogenation of 4-methylpiperidine by supported pincer-ligated iridium catalysts in continuous flow, Catalysis Science & Technology (2023). DOI: 10.1039/D3CY00881A
New catalyst could provide liquid hydrogen fuel of the future
Researchers at Lund University in Sweden are investigating a car fuel comprised of a liquid that is converted to hydrogen by a solid catalyst. The used liquid is then emptied from the tank and charged with hydrogen, after which it can be used again in a circular system that is free from greenhouse gas emissions.
In two research articles, Lund researchers have demonstrated that the method works, and while it is still basic research, it has the potential to become an efficient energy-storage system in the future.
“Our catalyst is one of the most efficient around, at least if you look at publicly available research,” says Ola Wendt, professor at the Department of Chemistry at Lund University, and one of the authors.
Finding alternative ways of producing, storing and transforming energy in order to reduce carbon dioxide emissions from fossil fuels is necessary to reduce the impact on the climate. One way involves much-talked-about hydrogen gas, which many see as a future solution for energy storage. Nature stores energy in chemical bonds, and hydrogen contains the highest energy density in relation to its weight.
“However, gas can be difficult to handle, so we are looking at liquid fuel charged with hydrogen that can be delivered at a pump, in a way broadly similar to what happens at petrol stations today,” says Ola Wendt.
The concept is known as LOHC (liquid organic hydrogen carriers) and is not new as such. The challenge is in finding as efficient a catalyst as possible, that can extract the hydrogen from the liquid.
The system is intended to work using a liquid that is “charged” with hydrogen. The liquid is pumped through a solid catalyst which extracts the hydrogen. This can be used in a fuel cell – which converts chemical fuel to electricity – while the “spent” liquid carries on to another tank. The only emission is water.
The spent liquid can then be emptied at a filling station before refuelling with new, charged liquid. This would probably mean large scale production of the substance, comparable to today’s oil refineries.
“We converted more than 99 per cent of the hydrogen gas that was present in the liquid,” says Ola Wendt.
Researchers have also been calculating whether it might be possible to use the fuel for larger vehicles such as buses, trucks and aircraft.
“With the large tanks that they have, it might be possible to cover almost the same distance as you can with a tank of diesel. You would also convert around 50 per cent more energy compared to compressed hydrogen,” says Ola Wendt.
The liquids used are isopropanol (which is a common ingredient in screenwash) and 4-methylpiperidine.
Does this sound a little too good to be true? Yes – for now at least, a number of challenges remain. One is that the lifespan of the catalyst is rather limited. Another is that iridium, which the catalyst is based on, is a precious metal.
“But we estimate that you need about two grams of iridium per car. This could be compared to today’s exhaust-cleaning catalytic converters, which contain about three grams of platinum, palladium and rhodium, which are also precious metals,” says Ola Wendt.
This is a technical solution based on basic research. If a decision was made to go for a finished product, Ola Wendt believes that the concept could be ready in ten years’ time – provided that it is economically viable and that there is interest from society.
Another problem is how hydrogen is produced – today, most production is not climate friendly. The hydrogen then needs to be stored and transported in an effective way, which is not that straightforward today. There are also the risks of refuelling with compressed hydrogen. The Lund researchers hope to solve this with their method.
“Ninety-eight per cent of all hydrogen today is fossil-based, produced from natural gas. The biproduct is carbon dioxide. From an environmental point of view, the notion of producing hydrogen for steel, batteries and fuel is pointless if it is done using natural gas,” says Ola Wendt, but he explains that there is a lot of research going on into how “green hydrogen” might be produced by splitting water into hydrogen and oxygen with the help of renewable energy.
At the same time, Ola Wendt believes that political decisions are required for renewable and climate-friendly alternatives to gain a proper foothold.
“It needs to be cheaper, and it takes political decisions. Renewables have no chance of competing with something that you just dig out of the ground, where transport is almost the only cost, as is the case with fossil fuels,” he concludes.
JOURNAL
Catalysis Science & Technology
ARTICLE TITLE
Acceptorless dehydrogenation of 4-methylpiperidine by supported pincer-ligated iridium catalysts in continuous flow