Kailynn Mannella says because there is no cure for MS, innovative ways to rehabilitate individuals are needed
By Bob Tymczyszyn Standard Photojournalist
Monday, July 3, 2023
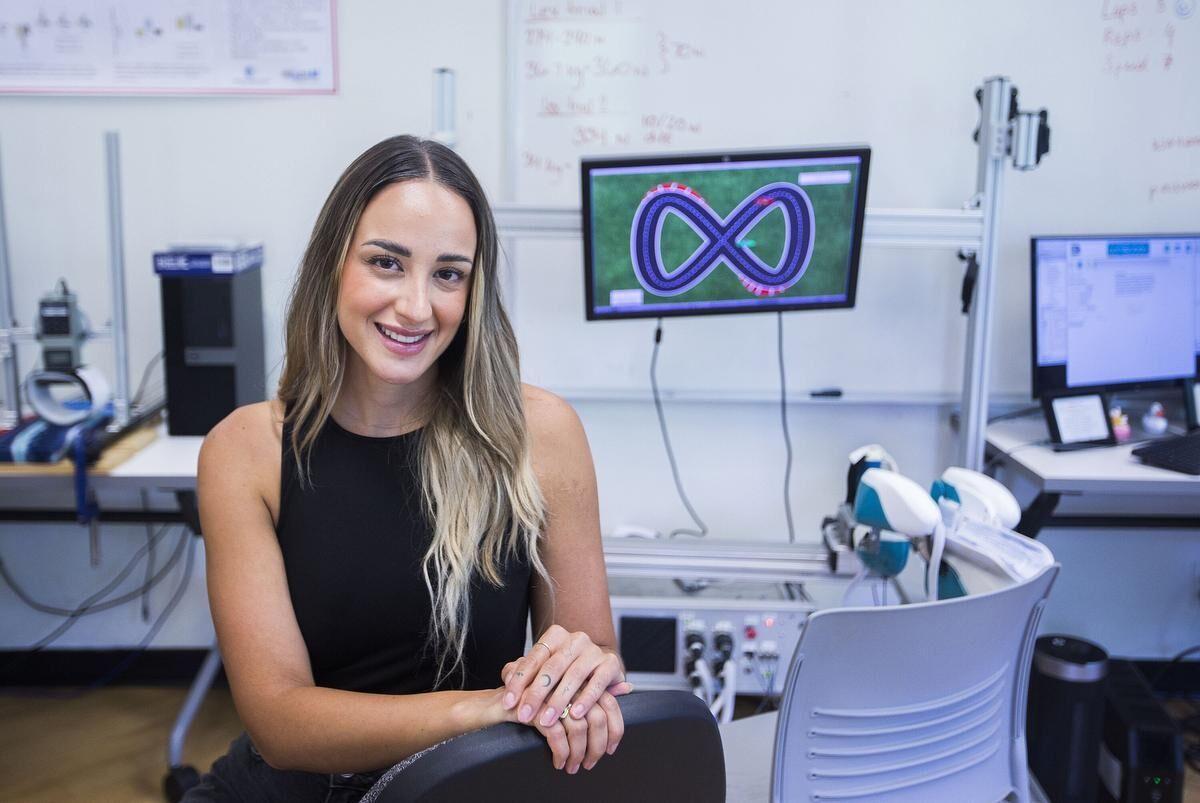
Kailynn Mannella is a PhD researcher at Brock University who is working with people who have multiple sclerosis.
A Brock University PhD researcher through the use of robotic rehabilitation is looking for ways to improve the lives of people living with multiple sclerosis.
Kailynn Mannella said because there is no cure for MS research is at a stage where new, innovative ways to rehabilitate individuals are needed.
“What we’re doing isn’t the best, we could be doing more and we (at Brock) want to contribute to that side of research, being able to use it in the real world.”
In Canada, roughly 100,000 people are living with the disease and the Niagara region is a hot spot.
“We just want to make a difference in our community,” said Mannella.
MS is an autoimmune disease. The immune system instead of protecting from viruses and bacteria attacks tissues in the body. In the case of MS, communication between nerve cells is disrupted, and the body does not receive instructions necessary to perform functions such as speaking, seeing, walking and learning.
“Nobody knows what the cause of MS is and that’s primarily why there’s no cure at the moment,” said Mannella. “It could be genetic, it could be environmental, we’re not sure, it’s a guessing game, and it is a very rapidly progressive disease.
“Because there is no cure, we have a bigger need to develop rehab strategies to help people live with MS to have a more functional life.”
In a Brock lab, the only one of its kind in Canada, a robotic device is used for rehabilitation, to help somebody bring back function in an upper limb.
“We’ve been collecting data since January. Right now we’re just trying to reach some more people with MS in the community, it’s an ongoing project and will be going on until next January.
“We’ve had 18 come through and we’re looking for 10 more. If we got more we would prolong the study. It helps the research but is also free rehab for whoever is in need of it.”
While there is a lot of stroke research, and robotic rehab has many good effects on stroke patients, Mannella said the two are very different and there is a lack of research as it relates to MS.
Brock teamed up with the Italian Institute of Technology, which built and programmed the robot used for rehab purposes.
“We’ve seen some really great strength improvements with some of the individuals with MS. We’ve also seen some motor control, which means all the muscles of their upper limb being able to communicate with each other.
“But we need a few more (participants) to make some firm conclusions.”
Participants come in for a pre-assessment, baseline values are measured, along with muscular strength and neuro-physiological assessments. Then participants attend the lab three times a week for eight weeks to train with the device before a final assessment to see how much they have improved.
“Some people have told me they are able to paint their nails or squeeze lemons when they bake, which they couldn’t do before. And many love coming here because they would not have done any kind of exercise unless they have this kind of program in place for them.”
Mannella said the research has three purposes, with one being the introduction of robotics in treatment.
“They use robots in Europe a lot, but we don’t have them here in rehab clinics and we don’t have them in hospitals so the goal would be to implement these devices where they would be very useful and just to prove that this is very useful for someone with MS.”
A second reason for the study is to determine the severity of the disease, which can be subjective, whereas robotic assessments can determine someone’s level of severity or their progress.
Lastly, Mannella says they are interested said there is interest in training one limb and seeing if there are any improvements in the untrained limb.
“MS is a bilateral disease but oftentimes there is one more-affected limb. We want to see if we can use that good limb for improvement.
“These are the three avenues that we want to see to help people with MS and then we want clinicians to be able to look at our research and use and adapt that to their rehab strategy.”
While Brock is looking for at least 10 more people, Mannella said it would welcome more participants, and anyone with any severity of the disease is welcome.
Mannella and her team can be contacted directly via email at km14ta@brocku.ca.
Bob Tymczyszyn
Bob Tymczyszyn is a photojournalist with the St. Catharines Standard.
New ferroelectric material could give robots muscles
IMAGE: ACTUATION OF FERROELECTRIC POLYMERS DRIVEN BY JOULE HEATING. view more
CREDIT: QING WANG
UNVERSITY PARK, Pa. — A new type of ferroelectric polymer that is exceptionally good at converting electrical energy into mechanical strain holds promise as a high-performance motion controller or “actuator” with great potential for applications in medical devices, advanced robotics, and precision positioning systems, according to a team of international researchers led by Penn State.
Mechanical strain, how a material changes shape when force is applied, is an important property for an actuator, which is any material that will change or deform when an external force such as electrical energy is applied. Traditionally, these actuator materials were rigid, but soft actuators such as ferrroelectric polymers display higher flexibility and environmental adaptability.
The research demonstrated the potential of ferroelectric polymer nanocomposites to overcome the limitations of traditional piezoelectric polymer composites, offering a promising avenue for the development of soft actuators with enhanced strain performance and mechanical energy density. Soft actuators are especially of interest to robotics researchers due to its strength, power and flexibility.
“Potentially we can now have a type of soft robotics that we refer to as artificial muscle,” said Qing Wang, Penn State professor of materials science and engineering and co-corresponding author of the study recently published in Nature Materials. “This would enable us to have soft matter that can carry a high load in addition to a large strain. So that material would then be more of a mimic of human muscle, one that is close to human muscle.”
However, there are a few obstacles to overcome before these materials can meet their promise, and potential solutions to these obstacles were proposed in the study. Ferroelectrics are a class of materials that demonstrate a spontaneous electric polarization when an external electric charge is applied and positive and negative charges in the materials head to different poles. Strain in these materials during the phase transition, in this case conversion of electrical energy to mechanical energy, can completely change properties such as its shape, making them useful as actuators.
A common application of a ferroelectric actuator is an inkjet printer, where electrical charge changes the shape of the actuator to precisely control the tiny nozzles that deposit ink on the paper to form text and images.
While many ferroelectric materials are ceramics, they also can be polymers, a class of natural and synthetic materials made of many similar units bonded together. For example, DNA is a polymer, as is nylon. An advantage of ferroelectric polymers is they exhibit a tremendous amount of the electric-field-induced strain needed for actuation. This strain is much higher than what is generated by other ferroelectric materials used for actuators, such as ceramics.
This property of ferroelectric materials, along with a high level of flexibility, reduced cost compared to other ferroelectric materials, and low weight, holds great interest for researchers in the growing field of soft robotics, the design of robots with flexible parts and electronics.
"In this study we proposed solutions to two major challenges in the soft material actuation field,” said Wang. "One is how to improve the force of soft materials. We know soft actuation materials that are polymers have the largest strain, but they generate much less force compared to piezoelectric ceramics.”
The second challenge is that a ferroelectric polymer actuator typically needs a very high driving field, which is a force that imposes a change in the system, such as the shape change in an actuator. In this case the high driving field is necessary to generate the shape change in the polymer required for the ferroelectric reaction needed to become an actuator.
The solution proposed to improve the performance of ferroelectric polymers was developing a percolative ferroelectric polymer nanocomposite — a kind of microscopic sticker attached to the polymer. By incorporating nanoparticles into a type of polymer, polyvinylidene fluoride, the researchers created an interconnected network of poles within the polymer.
This network enabled a ferroelectric phase transition to be induced at much lower electric fields than would normally be required. This was achieved via an electro-thermal method using Joule heating, which occurs when electric current passing through a conductor produces heat. Using the Joule heating to induce the phase transition in the nanocomposite polymer resulted in only requiring less than 10% of the strength of an electric field typically needed for ferroelectric phase change.
“Typically, this strain and force in ferroelectric materials are correlated with each other, in an inverse relationship,” Wang said. “Now we can integrate them together into one material, and we developed a new approach to drive it using the Joule heating. Since the driving field is going to be much lower, less than 10%, this is why this new material can be used for many applications that require a low driving field to be effective, such as medical devices, optical devices and soft robotics.”
Along with Wang, other researchers in the study include from Penn State Yao Zhou, postdoctoral scholar in materials science and engineering; Tiannan Yang, assistant research professor with the Materials Research Institute; Xin Chen, postdoctoral researcher in materials science and engineering; Li Li, research assistant in materials science and engineering; Zhubing Han, graduate research assistant in materials science and engineering; Ke Wang, associate research professor with the Materials Research Institute; and Long-Qing Chen, Hamer Professor of Materials Science and Engineering. From North Carolina State University, other researchers in the study include Hancheng Qin, graduate research assistant in physics; Bing Zhang, graduate student in physics; Wenchang Lu, research professor in physics; and Jerry Bernholc, Drexel Professor in Physics. From Huazhong University of Science and Technology in Wuhan, China, other researchers in the study include co-corresponding author Yang Liu, a former postdoctoral scholar in materials science and engineering at Penn State, now a professor of materials science and engineering.
The study was supported in part by the United States Department of Energy.
JOURNAL
Nature Materials
METHOD OF RESEARCH
Experimental study
SUBJECT OF RESEARCH
Not applicable
ARTICLE TITLE
Electro-thermal actuation in percolative ferroelectric polymer nanocomposites
No comments:
Post a Comment