Government looks at factory-built homes to increase supply
BNN Bloomberg
,The federal government hopes to utilize factory-built homes as one way to rapidly increase Canada’s housing supply, but experts and builders say regulatory issues stand in the way of widespread adoption.
Housing Minister Sean Fraser told BNN Bloomberg last month the next phase of housing policy in Canada will be focused on increasing supply – and factory-build homes will be part of that industrial strategy to rapidly increase the scale of production.
Fraser characterized the strategy as ambitious but achievable through collaboration with various levels of government and the private sector.
The Canada Mortgage and Housing Corp. has estimated that Canada will have around 3.5 million fewer homes by the end of the decade than what is needed to restore affordability, as average home prices top $1 million in some cities.
Housing starts rose 18 per cent in December compared to the previous month, CMHC said last week. On a seasonally adjusted annual basis, housing starts in December reached 249,255 units.
Factory-built homes, also known as modular homes, can help meet demand for housing, according to Sunil Johal, vice president of public policy at CSA Group, but getting them built is more complicated than it seems.
“Modular really represents an opportunity to give the construction sector different options to help meet that significant demand by fabricating different building components or modules in an off-site controlled factory environment,” Johal said in an interview with BNNBloomberg.ca.
However, Johal flagged barriers to wide-scale adoption of factory-built homes, including “limited awareness” among regulators, which can slow down the approvals process.
“They tend to take quite a bit of time to review and approve these projects. That really eats into one of the big advantages that modular offers, which is the speed and timeliness with which it can be delivered,” Johal said.
Targeted policy
The CSA Public Policy Centre released a report last week highlighting modular housing’s potential to help ease Canada’s critical shortage of housing. The report’s authors made recommendations for governments to capitalize on modular housing, including addressing gaps in building codes.
Johal said that will involve ensuring inspections and approvals are done in a “coordinated, streamlined fashion,” not just applying the same approaches from traditional construction to the modular market.
“Things are done differently and we need to make sure that we recognize that,” he said. “That could involve greater recognition of standards around how modular homes are built.”
The report also noted a need to develop training and guidance for the industry and regulators, and called for improved access to financing.
Builders at the ready
Some homebuilding companies are standing at the ready for a move to more modular building in Canada, and one is using new technology like AI to help speed up the homebuilding process.
Frank Cairo, co-founder and CEO of the Caivan Group of Companies, told BNNBloomberg.ca that his company leverages AI, generative design and various other technologies to automate large portions of the factory home-building process.
Caivan is active in over 50 communities in Ontario, primarily Ottawa and GTA. They are a top three builder in Ontario by volume.
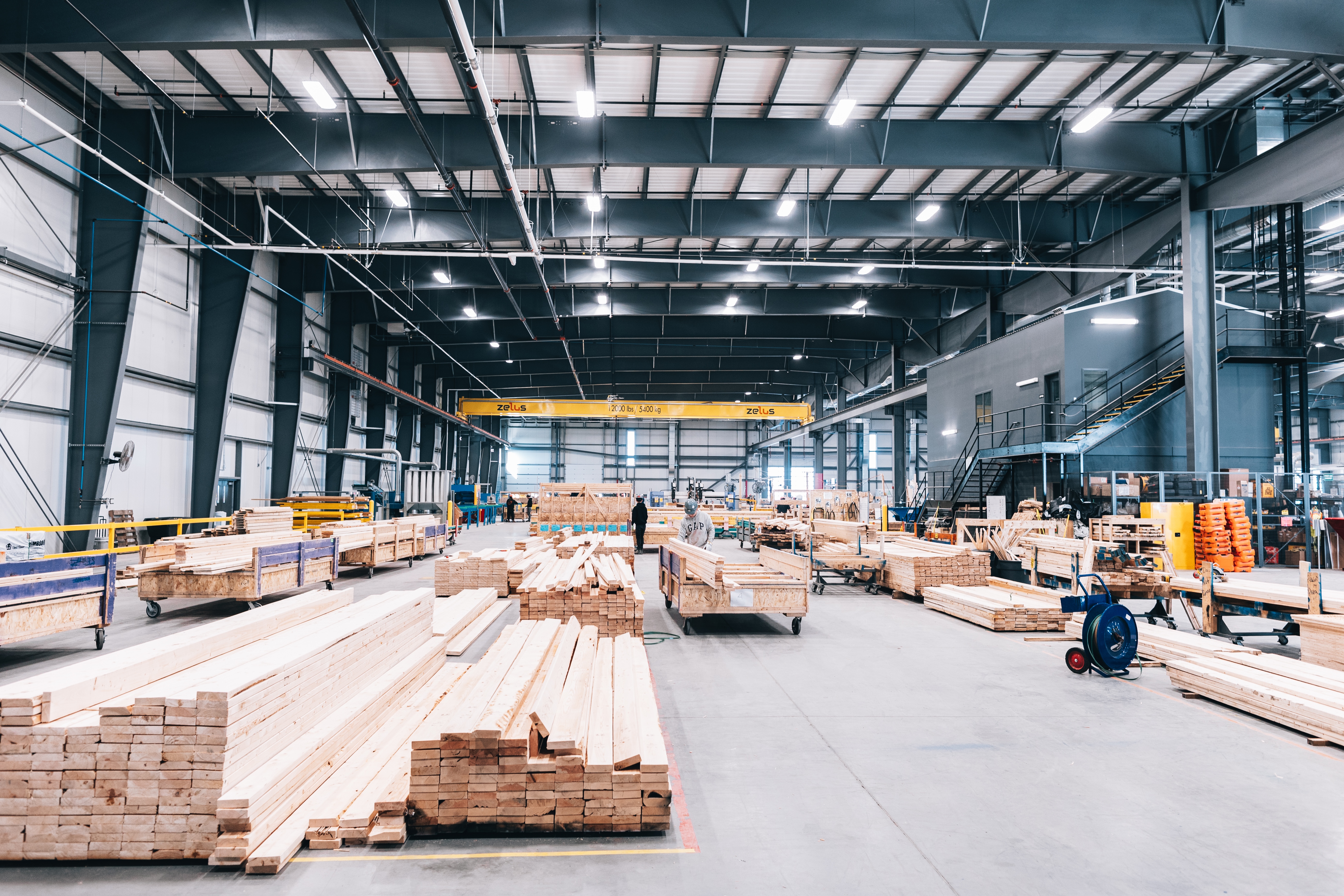
The standard building permit process applies to homes produced by Caivan, Cairo said. Going forward, he questions what the approval regime will look like for factory-manufactured homes compared to traditional builds.
Caivan currently operates mostly in Ottawa and the Greater Toronto Area. In Ontario, Cairo said his company faces challenges around uneven flow of land development approvals, which can disrupt productivity.
He said the company’s Ottawa factory runs best when it is operating at an “even pace,” requiring predictability in the approvals process.
How modular building works
Johal said modular building approaches can offer “substantial” reductions in construction times with “completion schedule rates about 25 to 50 per cent faster than traditional methods. That’s because under the modular method, “builders can undertake tasks concurrently rather than sequentially.”
Using this approach, about 80 per cent of construction occurs offsite, he explained.
Johal also noted that modular construction strategies can offer cost savings of up to 20 per cent when compared to traditional methods, and these types of construction projects can reduce waste by up to 46 per cent.
In addition to factory building techniques, Cairo said the technology used by Caivan “shaves about three and a half months off the build cycle of a new home.”
Automating much of the process reduces human error, he added.
“Our factory will fully manufacture between four and six individual homes a day, and then it will take one day to install those homes,” Cairo said.
This is partly possible due to “generative design algorithms” that automate large parts of the architectural process.
“Those architectural sets that get generated through the algorithm directly connect with our equipment line for manufacturing processes,” Cairo said.
At the moment, Caivan builds around 1,000 homes a year. The company has set an “ambitious target” to increase its annual manufacturing output, Cairo said, with a goal of building 4,000 homes per year within three years.
No comments:
Post a Comment