The Skilled Labor Shortage Threatens Manufacturing's Full Recovery, Says Study
Before the pandemic, 38% of manufacturers had trouble finding candidates with the right skills and today that number is 54%, said The Workforce Institute at UKG.
Before the pandemic, 38% of manufacturers had trouble finding candidates with the right skills and today that number is 54%, said The Workforce Institute at UKG.

Workforce Institute at UKG
THE SKILLED WORKER IS A WHITE MALE
Adrienne Selko
JUL 14, 2021
While more than half, 54%, of manufacturers have achieved year-over-year growth, despite combatting the pandemic, workforce issues have escalated." The Resilience of Manufacturing: Strengthening people operations and bridging the talent gap amid crisis," a study from the Workforce Institute at UKG based on a survey of more than 300 hiring decision-makers representing a mix of U.S.-only manufacturers (65%) and multinational manufacturers with a strong U.S. presence (35%). found that finding talent with the right skills has been more difficult. Before the pandemic, 38% of manufacturers faced this issue and today that number has increased to 54%.
IndustryWeek talked to Kylene Zenk, director of the Manufacturing Practice at UKG to further explore the conclusions from the report.
IW: What are the reasons behind the problems finding skilled workers?
KZ: There are a number of reasons including:
Employees aren’t just calling out of scheduled shifts on short notice — many are actually “ghosting” their employer by skipping a scheduled shift with zero notice.
Between January and March 2021, more than two in three manufacturers (68%) let employees go due to poor attendance, and 13% said managers had to adjust labor schedules every day to account for unplanned absences.
Turnover is up 15% over the prior year: Nearly three in five manufacturers (59%) experienced “higher-than-average” turnover from March 2020 to March 2021, compared with 44% from March 2019 to March 2020. Among multinationals, 71% said turnover was up during the first year of the pandemic vs. 52% of U.S.-only manufacturers.
Although the study did not explicitly explore the reasons why employees are committing attendance infractions, the frequency at which last-minute call-outs occurred within the first 12 months of the pandemic is indeed troubling. Half of the respondents we surveyed said they had people call out of scheduled shifts with less than 24-hour’s notice at least several times a month and 1 in 10 said this happened daily, which puts pressure on managers as well as other team members to fill in the gaps and maintain production schedules.
Again, we can’t pinpoint exactly why these attendance issues happened, but it seems likely that pandemic-related obligations or concerns were a common cause given that frontline employees faced extraordinary personal challenges over the past year, such as enhanced childcare or remote schooling responsibilities, which would have likely impacted their ability to come to work on time or at all. Of course, some manufacturers with more people-centric cultures and policies offered their frontline team members more flexibility to address personal concerns, but this was not unilaterally the case.
We also have to keep in mind that attendance issues were commonplace in manufacturing even before the pandemic. When we surveyed manufacturers in March 2020, more than half said employee lateness (61%), short-staffed shifts (58%), and last-minute call-outs (55%) were all regular occurrences in the 12 months prior to COVID.
What this tells us is that attendance issues, which will presumably continue to impact manufacturing into the post-COVID era, demand a long-term solution — especially in light of the national labor shortage, wherein the decision to let a skilled employee go cannot be made lightly.
IW: What are the recruiting challenges?
KZ: The recruitment challenges noted in the survey seem to be consistent with data coming from other industry studies, and also what we are hearing anecdotally. Among the numerous recruitment challenges employers are facing, a third of our respondents said it’s difficult to compete with other manufacturers, and a quarter is having just as much trouble competing with employers outside the industry, which may have something to do with stagnant wages in manufacturing.
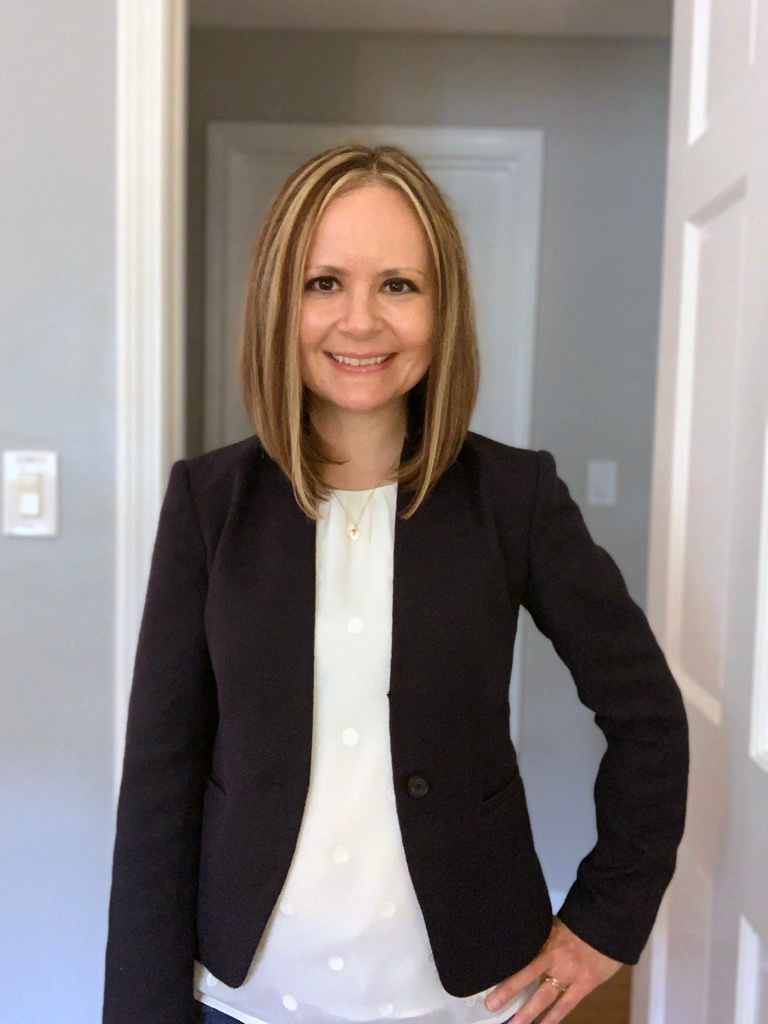
Adrienne Selko
JUL 14, 2021
While more than half, 54%, of manufacturers have achieved year-over-year growth, despite combatting the pandemic, workforce issues have escalated." The Resilience of Manufacturing: Strengthening people operations and bridging the talent gap amid crisis," a study from the Workforce Institute at UKG based on a survey of more than 300 hiring decision-makers representing a mix of U.S.-only manufacturers (65%) and multinational manufacturers with a strong U.S. presence (35%). found that finding talent with the right skills has been more difficult. Before the pandemic, 38% of manufacturers faced this issue and today that number has increased to 54%.
IndustryWeek talked to Kylene Zenk, director of the Manufacturing Practice at UKG to further explore the conclusions from the report.
IW: What are the reasons behind the problems finding skilled workers?
KZ: There are a number of reasons including:
Employees aren’t just calling out of scheduled shifts on short notice — many are actually “ghosting” their employer by skipping a scheduled shift with zero notice.
Between January and March 2021, more than two in three manufacturers (68%) let employees go due to poor attendance, and 13% said managers had to adjust labor schedules every day to account for unplanned absences.
Turnover is up 15% over the prior year: Nearly three in five manufacturers (59%) experienced “higher-than-average” turnover from March 2020 to March 2021, compared with 44% from March 2019 to March 2020. Among multinationals, 71% said turnover was up during the first year of the pandemic vs. 52% of U.S.-only manufacturers.
Although the study did not explicitly explore the reasons why employees are committing attendance infractions, the frequency at which last-minute call-outs occurred within the first 12 months of the pandemic is indeed troubling. Half of the respondents we surveyed said they had people call out of scheduled shifts with less than 24-hour’s notice at least several times a month and 1 in 10 said this happened daily, which puts pressure on managers as well as other team members to fill in the gaps and maintain production schedules.
Again, we can’t pinpoint exactly why these attendance issues happened, but it seems likely that pandemic-related obligations or concerns were a common cause given that frontline employees faced extraordinary personal challenges over the past year, such as enhanced childcare or remote schooling responsibilities, which would have likely impacted their ability to come to work on time or at all. Of course, some manufacturers with more people-centric cultures and policies offered their frontline team members more flexibility to address personal concerns, but this was not unilaterally the case.
We also have to keep in mind that attendance issues were commonplace in manufacturing even before the pandemic. When we surveyed manufacturers in March 2020, more than half said employee lateness (61%), short-staffed shifts (58%), and last-minute call-outs (55%) were all regular occurrences in the 12 months prior to COVID.
What this tells us is that attendance issues, which will presumably continue to impact manufacturing into the post-COVID era, demand a long-term solution — especially in light of the national labor shortage, wherein the decision to let a skilled employee go cannot be made lightly.
IW: What are the recruiting challenges?
KZ: The recruitment challenges noted in the survey seem to be consistent with data coming from other industry studies, and also what we are hearing anecdotally. Among the numerous recruitment challenges employers are facing, a third of our respondents said it’s difficult to compete with other manufacturers, and a quarter is having just as much trouble competing with employers outside the industry, which may have something to do with stagnant wages in manufacturing.
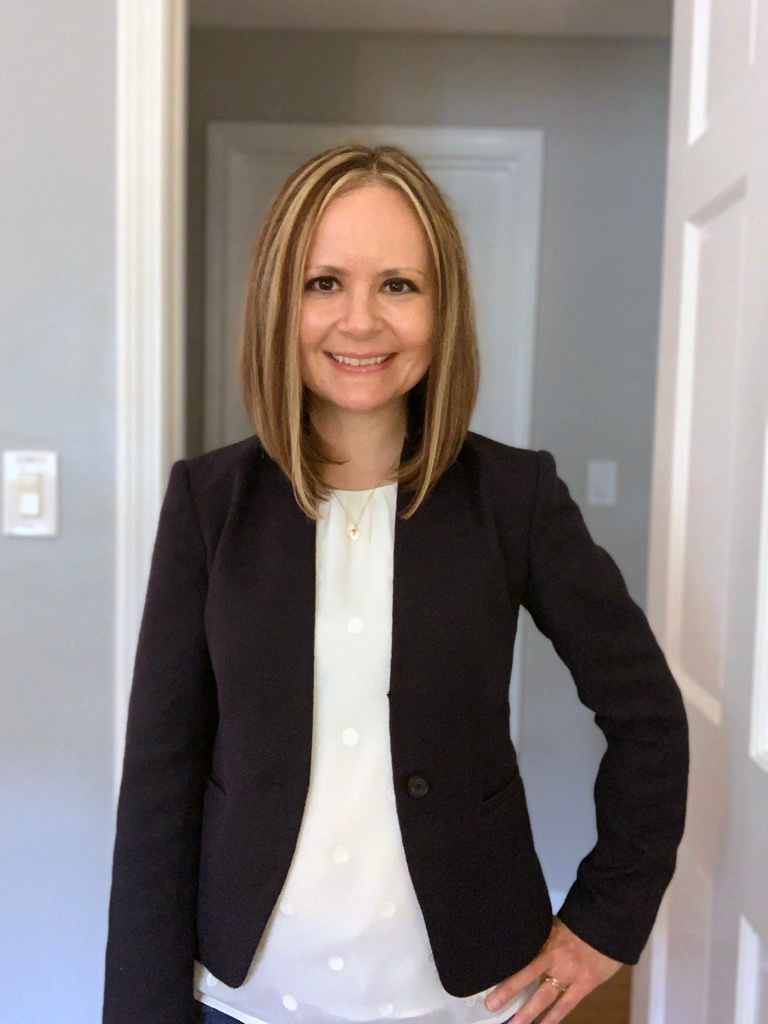
Kylene Zenk, director of the Manufacturing Practice at UKG
Across the board, competition for skilled talent is fierce right now. Following a staggering decline in frontline shift-work volume that began in March 2020, shift-work activity in the U.S. is hovering at 86.7% as of June 2021 — 13.3% below the 100% pre-pandemic baseline. And despite being a critical economic engine for growth in the U.S., manufacturing shift-work volume is still about 10% below pre-pandemic levels. This is according to the UKG Workforce Activity Report, which measures U.S. shift work for 3.3 million employees across 35,000 organizations.
Although the skills shortage in manufacturing has been a pervasive issue for the past several years, our research shows us that far more manufacturers today (54%) than a year ago (38%) are having a particularly hard timing finding candidates with the right skills to fill critical job openings. At the same time, 54% of manufacturers say that negative industry perceptions are impacting their ability to recruit Millennial and Gen Z talent, which is equally challenging.
To address the lack of skilled candidates, manufacturers must make a concerted effort to retain the people they have working for them today and cultivate desired skillsets internally, which many are doing by further developing their existing workforce. The survey found that 63% of manufacturers today are taking steps to reskill employees and another 60% are crossing training their people.
To address negative industry perceptions, manufacturers need to look closely at other industries that have been successful in attracting younger workers. This will likely involve adopting practices and policies that create a more employee-centric workplace where flexibility and empowerment are commonplace, which may be uncomfortable for those who hold the more traditional mindset of “command and control” often seen in manufacturing environments.
IW: Do you see the trend of using “alternative “ talent pools continuing?
KZ: The competition for talent will only continue to grow, so manufacturers absolutely need to do everything they can to widen their pool of potential candidates. This should include actively recruiting capable individuals from non-traditional or alternative sources, which is something the survey found many manufacturers are already doing today. For example, 62% have hired or considered hiring people with disabilities or special needs. Another 56% are targeting retirees, while 52% are considering previously incarcerated or “second-chance” workers as potential employees.
It’s important to understand that as employers expand their talent pools, additional training to adequately prepare new hires for their jobs may be needed, but with a severe shortage of labor, these investments will be worth it to streamline onboarding and optimize productivity.
IW: Are you hearing examples of companies who are unable to produce or increase output due to labor shortages?
KZ: Labor shortages are a pervasive problem. In fact, the survey uncovered that nearly two in three manufacturers (63%) are struggling to fill critical labor gaps, and almost a quarter (23%) are “really struggling.” Just recently, I heard about some organizations that have missed production deadlines due to frontline labor shortages, but most are doing everything they can to avoid that situation, like giving more hours to their current workforce. But taking on this extra workload — i.e. working longer shifts to help meet demand — is now starting to have negative impacts as employers run the risk of increased employee burnout, higher overtime expenses, and even more turnover. Already, three-quarters of respondents are concerned about employee burnout and two-in-five indicated that overtime costs are now affecting their bottom lines.
Unfortunately, with the massive competition for labor, it’s only a matter of time before frontline employees who feel overworked and underappreciated at their current job will look for opportunities elsewhere.
IW: Do you see any important trends manufacturers might be missing?
KZ: We are observing an interesting dynamic play out in the manufacturing industry. Some organizations have come to realize they essentially operate two distinct company cultures: one for office employees, and one for frontline, hourly team members. Corporate versus plant if you will. This has become especially apparent over the course of the past year, during the pandemic. One group was deemed “essential” and required to stay in the plants, while the other perhaps had the flexibility to work from their homes.
This dynamic highlights the fact that the quality of these two workplace cultures is not equal, and that there is significant work to be done to improve the workplace experience for frontline, hourly team members so that manufacturers can remain competitive employers now and into the future.
Although the skills shortage in manufacturing has been a pervasive issue for the past several years, our research shows us that far more manufacturers today (54%) than a year ago (38%) are having a particularly hard timing finding candidates with the right skills to fill critical job openings. At the same time, 54% of manufacturers say that negative industry perceptions are impacting their ability to recruit Millennial and Gen Z talent, which is equally challenging.
To address the lack of skilled candidates, manufacturers must make a concerted effort to retain the people they have working for them today and cultivate desired skillsets internally, which many are doing by further developing their existing workforce. The survey found that 63% of manufacturers today are taking steps to reskill employees and another 60% are crossing training their people.
To address negative industry perceptions, manufacturers need to look closely at other industries that have been successful in attracting younger workers. This will likely involve adopting practices and policies that create a more employee-centric workplace where flexibility and empowerment are commonplace, which may be uncomfortable for those who hold the more traditional mindset of “command and control” often seen in manufacturing environments.
IW: Do you see the trend of using “alternative “ talent pools continuing?
KZ: The competition for talent will only continue to grow, so manufacturers absolutely need to do everything they can to widen their pool of potential candidates. This should include actively recruiting capable individuals from non-traditional or alternative sources, which is something the survey found many manufacturers are already doing today. For example, 62% have hired or considered hiring people with disabilities or special needs. Another 56% are targeting retirees, while 52% are considering previously incarcerated or “second-chance” workers as potential employees.
It’s important to understand that as employers expand their talent pools, additional training to adequately prepare new hires for their jobs may be needed, but with a severe shortage of labor, these investments will be worth it to streamline onboarding and optimize productivity.
IW: Are you hearing examples of companies who are unable to produce or increase output due to labor shortages?
KZ: Labor shortages are a pervasive problem. In fact, the survey uncovered that nearly two in three manufacturers (63%) are struggling to fill critical labor gaps, and almost a quarter (23%) are “really struggling.” Just recently, I heard about some organizations that have missed production deadlines due to frontline labor shortages, but most are doing everything they can to avoid that situation, like giving more hours to their current workforce. But taking on this extra workload — i.e. working longer shifts to help meet demand — is now starting to have negative impacts as employers run the risk of increased employee burnout, higher overtime expenses, and even more turnover. Already, three-quarters of respondents are concerned about employee burnout and two-in-five indicated that overtime costs are now affecting their bottom lines.
Unfortunately, with the massive competition for labor, it’s only a matter of time before frontline employees who feel overworked and underappreciated at their current job will look for opportunities elsewhere.
IW: Do you see any important trends manufacturers might be missing?
KZ: We are observing an interesting dynamic play out in the manufacturing industry. Some organizations have come to realize they essentially operate two distinct company cultures: one for office employees, and one for frontline, hourly team members. Corporate versus plant if you will. This has become especially apparent over the course of the past year, during the pandemic. One group was deemed “essential” and required to stay in the plants, while the other perhaps had the flexibility to work from their homes.
This dynamic highlights the fact that the quality of these two workplace cultures is not equal, and that there is significant work to be done to improve the workplace experience for frontline, hourly team members so that manufacturers can remain competitive employers now and into the future.
No comments:
Post a Comment