If It Ain’t Broke – Monitor It
That’s the new mantra as advances in technology allow operators to peer behind the curtain.
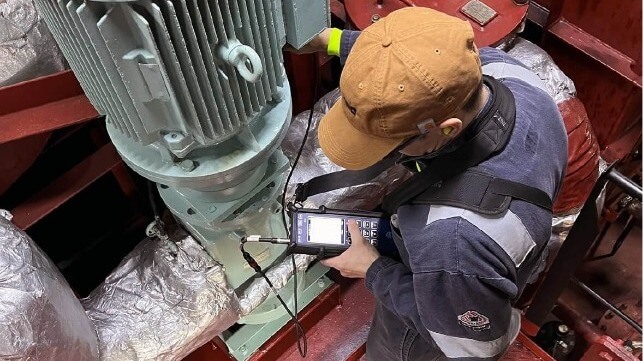
(Article originally published in Sept/Oct 2023 edition.)
In a business environment thick with environmental concerns, regulatory and compliance issues and economic pressures, the squeeze on vessel operations has never been tighter. Confronted by tight margins and ever-increasing obligations, vessel crews are forced to do much with little. And keeping the vessels moving is of prime importance.
Global supply chain issues mean parts might not be available when needed, which could lead to lengthy delays and catastrophic consequences for the operation of the business.
What the industry needs is a little bit of leverage.
Fortunately, the market has stepped up to answer the call.
Pulling the Maintenance Lever
Shipboard maintenance has been evolving since the days of the Industrial Revolution.
Maintenance is broadly defined as a set of activities or tasks used to restore an item to the state at which it can perform its primary function. Traditional maintenance was corrective in nature. That is, the machine or component would run to failure, then be repaired. This simple strategy leads to long downtime and costly repairs due to its last-minute nature. A better solution was needed.
Preventative maintenance was the next step. The idea was to perform maintenance prior to failure in order to reduce the failure rate and extend the operating life of the equipment. This is often based on manufacturers’ recommendations and is largely time-based – through tracking of either calendar hours or running hours.
A better solution for sure, but still not ideal. One hundred hours is one hundred hours, and the project timeframe likely doesn’t match the maintenance timeframe. The quest for a more flexible solution continued.
The 1950s saw a major advancement in the field of lube oil analysis, one of the earliest and most straightforward examples of condition monitoring. Careful examination of used engine oil began to tell the story of what was happening on the inside. Evaluating the oil’s properties, presence of contaminants or metal particles and water content suddenly gave great insight into the condition of the equipment.
Predictive maintenance started to become a thing. Engine life and mean time between failures increased. All of this led to cost savings and more predictable operating envelopes.
The age of condition monitoring had begun.
Lubes and Monitoring – A Perfect Combination
2-stroke marine engines are particularly prone to cylinder fouling compared to their 4-stroke counterparts. This is due to:
- Higher degree of incomplete combustion
- Higher operating temperature/pressure
- Sensitivity to fuel quality.
MAN ES makes marine engines that power international trade. Their longevity and reliability stem from the use of category II 40BN cylinder oils for their latest designs. One such engine was filled with GulfSea Cylcare XP 5040 by Gulf Marine.
8,077 hours later, the cylinders were inspected. Measurements of piston ring coatings, piston ring gap clearance and carbon thickness were all acceptable to OEM standards. Scavenge port inspection results also found excellent conditions for the piston crown, piston rings and cylinder liners.
Category II oils showed great improvement in dispersancy, wear protection and oxidization inhibition – the very properties needed as alternative fuels become more common.
From Fluids to Vibration
If lube oils are the lifeblood, reciprocating machinery is the muscle that makes the machine work.
Transforming rotation into movement and energy keeps things moving but comes at a cost. Excessive vibration, misalignment of parts and resonance are just a few of the issues equipment is subjected to, even equipment that’s in apparently good order.
Vibration monitoring is a good start and can provide a solid baseline, but detection and analysis have come much further and are able to discover so much more.
Video motion amplification is now a mature technology that’s growing by leaps and bounds. A high-speed, high-definition camera such as the IRIS-MX by RDI Technologies is used to take samples at upwards of 24,000 frames per second, which are then filtered through a supporting software that measures light intensity differentiation across individual pixels.
Each pixel becomes its own vibration measurement.
Vibration and alignment specialists Advanced Mechanical Engineering (AME) is the authorized service provider for this technology and has seen amazing results by taking a baseline reading for ships going into a shipyard for repairs and another when finished. This provides a blueprint for the vessel operator, identifies issues that may have not been on the repair list and ensures the repairs have been properly completed.
Habitability, comfort and reduced noise levels have led to an increase in resiliency-mounted equipment – sitting on rubber or springs. Previously, it was difficult to tell whether the mounts were properly balanced with an imbalance leading to increased vibrations. Now, with video motion amplification, it can be visibly determined in just minutes.
Nobody wants mechanical drama onboard. Downtime is expensive, creates chaos for the crew and can be avoided. A smart survey program is cheap insurance.
Vibration Analysis
Vibration analysis is used to improve profitability, efficiency and safety in most major industries in the world.
Marine vibration specialists Condition Analyzing Corporation (CAC) has applied vibration analysis for over 50 years. CAC keeps an eye on emerging technologies and blends them with time-proven processes, providing knowledge of the condition of all rotating machinery on a vessel and focusing attention on those machines that require maintenance on a priority basis and those that are healthy as is.
CAC recently invested in new ATEX-rated vibration analyzers for use on tankers, barges and the ever-increasing number of LNG dual-fueled ships. These intrinsically safe analyzers are a must for safe and efficient condition-monitoring surveys on ships and ATBs.
Over the past year, CAC has increased the use of an innovative analysis tool called an operational deflection shape (ODS) video of a machine. These videos help exaggerate the movement of the machines to facilitate diagnosis of foundational issues and parts of the machines other than traditional bearing locations.
CAC has a customer interface via its proprietary CAC Decision Point® website, which provides clients access to survey reports and trend data. Further, Decision Point® enables clients to report repair actions made onboard to CAC for informed future analysis of the machine. The survey reports help in prioritizing what machines need maintenance and what the best solution should be, starting with the lowest cost solution and progressing to more expensive options.
Decision Point® is a management tool for the chief engineer and ship manager to prioritize maintenance funds and man-hours advantageously.
While remote monitoring is part of its capability, the company knows that nothing beats the value of talking to the crew, hearing the sounds, placing a hand on the machine and getting repeatable vibration readings. When CAC technicians find excessive vibrations, it’s immediately reported to the crew to ensure that the machine is flagged for corrective action.
If a repair is made before the technician debarks the ship, then a new set of readings can be taken to determine if the repair worked. While onboard, the CAC technician can also improve safety by performing a thermographic (infrared) inspection of electrical components.
The strategic use of condition monitoring paired with real-world experience leads to greater efficiencies, higher productivity and better outcomes.
Machines Learning About Machines
Fairbanks Morse Defense is top of class when it comes to innovation.
While best known for its work designing and providing high-reliability power systems, it’s constantly innovating – because you don’t build world-class reliability without world-class monitoring technology.
FMD’s onboard suite of tools – FM OnBoard – takes condition-based monitoring two steps further by enabling users across the oceans to learn and access live support through 3D simulation training that utilizes augmented reality and real-time data mapped from physical engines to digital twins.
With a hands-free interface and intuitive tools, you can access work instructions and multiple media formats in 3D space, increase operational availability, improve first-time fix rates and reduce the time for repairs.
The technology stack includes remote collaboration, asset monitoring/digital twin, anomaly detection, and mixed reality work instructions and authoring tools. The authoring in particular is interesting with FMD writing, training personnel and deploying work instructions to guide standard maintenance and repair processes for technical staff with a no-code solution. And it’s as easy to set up as writing an email.
The differentiator is the use of AI and machine learning algorithms in place of more traditional physics-based models that use set parameters and expected outcomes.
Instead, AI first learns what “normal” looks like (supported by data from all ships in the class), then looks for deviations from that norm. All of the data is saved in a data historian that visualizes and reports on asset health. When an anomaly is detected, FMD can then offer real-time support remotely using a hands-free, heads-up display, phone or tablet, all over an end-to-end encrypted data link.
While the company’s focus is in the marine defense market, the system is technology-agnostic and can be used from commercial vessels to ship davits (the number one fail-to-sail item) to nuclear powerplants. It’s simple to integrate as it taps into existing sensors and uses OEM data.
With each iteration the machine learns to do better. And that expertise gets fed back in to start the process again.
An Ounce Of Prevention
Poorly functioning equipment leads to downtime, loss of revenue and loss of reputation.
Advances in technology allow operators to peer behind the curtain, see inside the machine and slow down time to learn what is really going on. This knowledge is priceless when compared against the cost of a major malfunction or unplanned maintenance event.
As the saying goes, an ounce of prevention is worth a pound of cure.
Sean Hogue is Senior Vice President of Operations at Baker Marine Solutions.
No comments:
Post a Comment