Tesla Gigafactory in Gruenheide
Thu, September 14, 2023
By Norihiko Shirouzu
AUSTIN, Texas (Reuters) - Tesla has combined a series of innovations to make a technological breakthrough that could transform the way it makes electric vehicles and help Elon Musk achieve his aim of halving production costs, five people familiar with the move said.
The company pioneered the use of huge presses with 6,000 to 9,000 tons of clamping pressure to mold the front and rear structures of its Model Y in a "gigacasting" process that slashed production costs and left rivals scrambling to catch up.
In a bid to extend its lead, Tesla is closing in on an innovation that would allow it to die cast nearly all the complex underbody of an EV in one piece, rather than about 400 parts in a conventional car, the people said.
The know-how is core to Tesla's "unboxed" manufacturing strategy unveiled by Chief Executive Musk in March, a linchpin of his plan to churn out tens of millions of cheaper EVs in the coming decade, and still make a profit, the sources said.
While Tesla has said its unboxed model involves producing large sub-assemblies of a car at the same time and then snapping them together, the size and make-up of the modular blocks is still the subject of speculation.
Terry Woychowski, president of U.S. engineering company Caresoft Global, said if Tesla managed to gigacast most of the underbody of an EV, it would further disrupt the way cars are designed and manufactured.
"It is an enabler on steroids. It has a huge implication for the industry, but it's a very challenging task," said Woychowski, who worked for U.S. automaker GM for more than three decades. "Castings are very hard to do, especially the bigger and the more complicated."
Two of the sources said Tesla's previously unreported new design and manufacturing techniques meant the company could develop a car from the ground up in 18 to 24 months, while most rivals can currently take anywhere from three to four years.
The five people said a single large frame - combining the front and rear sections with the middle underbody where the battery is housed - could be used in Tesla's small EV which it aims to launch with a price tag of $25,000 by the middle of the decade.
Tesla was expected to make a decision on whether to die cast the platform in one piece as soon as this month, three of the sources said, though even if they do press ahead the end product could change during the design validation process.
Neither Tesla nor Musk responded to questions from Reuters for this story.
3D PRINTING AND SAND
The breakthrough Tesla has made centres on the how the giant molds for such a large part are designed and tested for mass production, and how casts can incorporate hollow subframes with internal ribs to cut weight and boost crashworthiness.
In both cases the innovations, developed by design and casting specialists in Britain, Germany, Japan and the United States, involve 3D printing and industrial sand, the five people said. All spoke to Reuters on condition of anonymity because they are not authorised to speak to the media.
So far, automakers have shied away from casting ever-bigger structures because of the "gigacast dilemma": creating molds to make parts of 1.5 metres squared or more boosts efficiency but is expensive and comes with myriad risks.
Once a large metal test mold has been made, machining tweaks during the design process could cost $100,000 a go, or redoing the mold altogether might come to $1.5 million, according to one casting specialist. Another said the whole design process for a large metal mold would typically cost about $4 million.
That has been deemed prohibitive by automakers - especially as a design might need half a dozen tweaks or more to achieve a perfect die from the perspective of noise and vibration, fit and finish, ergonomics and crashworthiness, the sources said.
But Musk's vision from the start was to find a way to cast the underbody in one piece, despite the risks, the sources said.
To overcome the obstacles, Tesla turned to firms that make test molds out of industrial sand with 3D printers. Using a digital design file, printers known as binder jets deposit a liquid binding agent onto a thin layer of sand and gradually build a mold, layer by layer, that can die cast molten alloys.
According to one source, the cost of the design validation process with sand casting, even with multiple versions, is minimal - just 3% of doing the same with a metal prototype.
That means Tesla can tweak prototypes as many times as needed, reprinting a new one in a matter of hours using machines from companies such as Desktop Metal and its unit ExOne.
The design validation cycle using sand casting only takes to two to three months, two of the sources said, compared with anywhere from six months to a year for metal mold prototypes.
TAILOR-MADE ALLOYS
The subframes in a car underbody are typically hollow to save weight and improve crashworthiness. At the moment, they are made by stamping and welding multiple parts together leaving a void in the middle.
To cast subframes with hollows as part of one gigacasting, Tesla plans to place solid sand cores printed by the binder jets within the overall mold. Once the part has been cast, the sand is removed to leave the voids.
But despite that greater flexibility achieved in both the design process and the complexity of the large frames, there was still one more major hurdle to clear.
The aluminium alloys used to produce the castings behaved differently in sand and metal molds and often failed to meet Tesla's criteria for crashworthiness and other attributes.
The casting specialists overcame that by formulating special alloys, fine-tuning the molten alloy cooling process, and also coming up with an after-production heat treatment, three of the sources said. And once Tesla is happy with the prototype mold, it can then invest in a final metal one for mass production.
The sources said Tesla's upcoming small car has given it a perfect opportunity to cast an EV platform in one piece, mainly because its underbody is simpler,
The kind of small cars Tesla is developing – one for personal use and the other a robotaxi – don't have a big "overhang" at the front and the back, as there is not much of a hood or rear trunk.
"It's like a boat in a way, a battery tray with small wings attached to both ends. That would make sense to do in one piece," one person said.
The sources said, however, that Tesla still had to make a call on what kind of gigapress to use if it decides to cast the underbody in one piece - and that choice would also dictate how complex the car frame would be.
To punch out such large body parts fast, the people said Tesla would need new bigger gigapresses with massive clamping power of 16,000 tons or more, which would come with a hefty price tag and might need larger factory buildings.
Three of the five sources said one problem with presses using high clamping power, however, was that they cannot house the 3D printed sand cores needed to make hollow subframes.
The people said Tesla could solve these obstacles by using a different type of press into which molten alloy can be injected slowly - a method that tends to produce higher quality castings and can accommodate the sand cores.
But the process takes longer.
"Tesla could still choose high-pressure for productivity, or they could choose slow alloy injection for quality and versatility," one of the people said. "It's still a coin toss at this point."
(Editing by David Clarke)
Tesla's Carmaking 'Breakthrough' Also Comes With Plenty Of Downsides
In theory, casting an entire underbody in one piece could be revolutionary.
By
Collin Woodard
PublishedYesterday
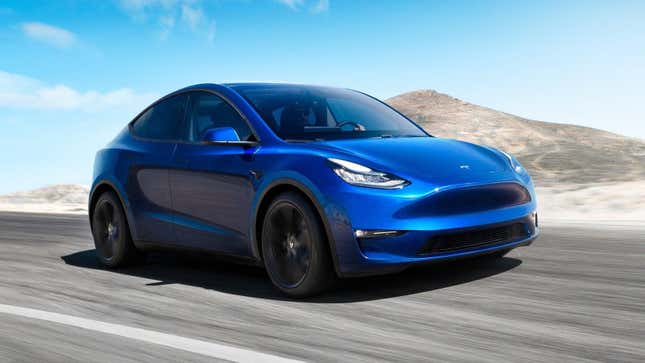
Photo: Tesla
After previously announcing that it would be able to cast the front and rear subsections of the Model Y in a move to cut costs and reduce complexity a couple of years ago, it sounds like Tesla is close to another engineering breakthrough. Five people recently spoke with Reuters, claiming Tesla will soon be able to cast essentially the entire underbody in one piece. Theoretically, that would allow Tesla to develop a new vehicle in two years or less and cut costs even further, allowing it to actually sell that elusive $25,000 electric car we’ve been promised.
Terry Woychowski, president of the engineering company Caresoft Global and former General Motors employee, told Reuters that if Tesla could actually pull it off, it would be a huge deal. But even he wasn’t exactly quick to predict a rapid Tesla victory over legacy automakers.
The Morning Shift: Tesla May Have Plans For Spain
GM Dealers Have Been Quietly Repairing Teslas For Over a Year
“It is an enabler on steroids. It has a huge implication for the industry, but it’s a very challenging task,” he told Reuters. “Castings are very hard to do, especially the bigger and the more complicated.”
To be fair to Tesla, it does sound like it’s made a number of breakthroughs. One downside to casting large pieces is that making changes to the test mold can be incredibly expensive. Smaller tweaks can reportedly easily cost $100,000, while redoing a mold could be more like $1.5 million. Considering it regularly takes several changes to get a design right, you’re spending a whole lot of money before you’ve even started production. But Tesla found a company that uses sand to 3D-print molds.
One source told Reuters that using these sand-based molds would likely cost about three percent of the total cost of creating a traditional mold even with multiple tweaks. It could also speed up the process, cutting the time it takes to get the molds right from six months or a year to just a couple of months.
As great as that sounds, though, there’s also a downside. To cast these underbodies quickly, Tesla would need to use more powerful presses that are too strong for the sand-based molds. Alternatively, they could take a slower approach with less powerful presses that create higher-quality castings but can’t be done as quickly.
Assuming it all works, though, there’s another downside that we’ve already covered. Casting the underbody in one piece also essentially makes the car impossible to repair if it gets into a wreck. So you may be able to buy a $25,000 Tesla, but if you crash, you’ll probably have to go out and buy another $25,000 Tesla to replace it. And we can’t imagine insurance companies are going to be happy about that, so prepare to pay higher monthly premiums.
There’s also the risk of cracks forming in the metal, which Tesla previously claimed to have solved by creating a super special aluminum alloy that wouldn’t have that problem. Except, as at least one Model Y owner has already found out, that isn’t necessarily the case.
Now, it’s entirely possible that the photos shown above are the only example of cracks forming during manufacturing, and that owner just got unlucky. And it’s also entirely possible that Tesla has been able to tweak the alloy it plans to use to cast the underbody as one piece to ensure that doesn’t happen. But that doesn’t mean there isn’t real reason to be concerned here.
If Tesla can pull the whole thing off and do it correctly, it’ll be seriously impressive. But at the same time, it’s far too early to say that Tesla has revolutionized auto manufacturing — and also a little too early to start questioning why legacy automakers aren’t following Tesla’s lead. With so many challenges, risks and upfront costs, it’s no wonder they’re not exactly rushing to beat Tesla to the punch.
No comments:
Post a Comment