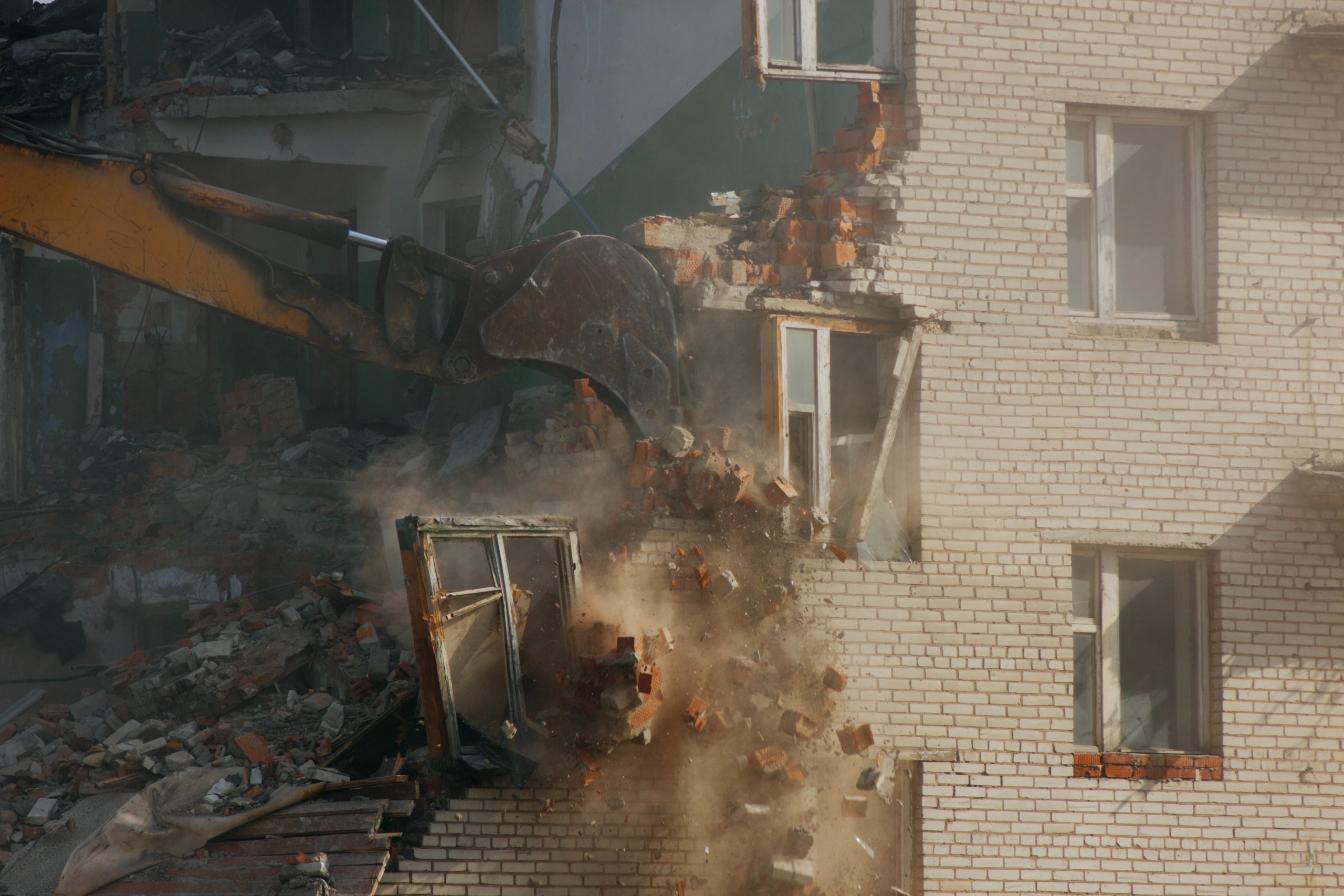
Q&A: ‘We need to reduce the ‘embodied energy’ of buildings
Retrofitting Europe’s buildings for energy efficiency is not enough to slash the carbon footprint of the construction sector and cut emissions in time to meet the Paris climate agreement goals, according to Dr Catherine De Wolf, assistant professor of design and construction management at TU Delft in the Netherlands.
She says that we need to design buildings to make them recyclable – but doing this will require a fundamental restructure of the construction industry.
How important is it to ‘green’ the construction industry?
The building sector is responsible for more than a third of our greenhouse gas emissions, and more than a third of our waste … and is one of the most resource-depleting industries.
That’s three good reasons for us to think about how to construct buildings in a more sustainable way.
And how urgent is it, given the rate at which emissions must be cut to meet the Paris climate agreement goal?
Europe has set a target of net zero emissions in the construction and buildings sector by 2050. It is a huge ambition. If we don’t change the sector in the next five years we won’t be able to achieve that target.
There has been a lot of innovation in reducing the energy we need to heat and cool buildings – the ‘operational energy’. But we also need to reduce the ‘embodied energy’ of buildings, which is related to production, construction, demolition and maintenance.
We need to shift from a linear model to a circular model where we use as little new material as possible, and (instead) we reuse, repair and recycle.
Can you give examples of what this might look like?
One of the things that makes demolition attractive is it is very quick … we just wreck everything and send it to landfill. But to go towards a circular construction industry, we want to be deconstructing buildings (and reusing the materials). This takes more time and often more expertise.
We’re exploring robots in our research. If we can find ways to program robots to carefully disassemble building elements, potentially it could be done quicker than humans because they could work 24/7 in an automated way.
We still need the human expertise, and we still need to design for deconstruction so building materials are not glued together and cast together in a way that makes it hard to take them apart.
There’s a lot of innovation (still) to do in designing buildings that can be quickly disassembled.
And there are already a lot of startups in the reuse sector – they train people who are specialised in recognising which materials are valuable on the market, and how to remove materials without breaking them.
But (robots) can be one of the solutions.
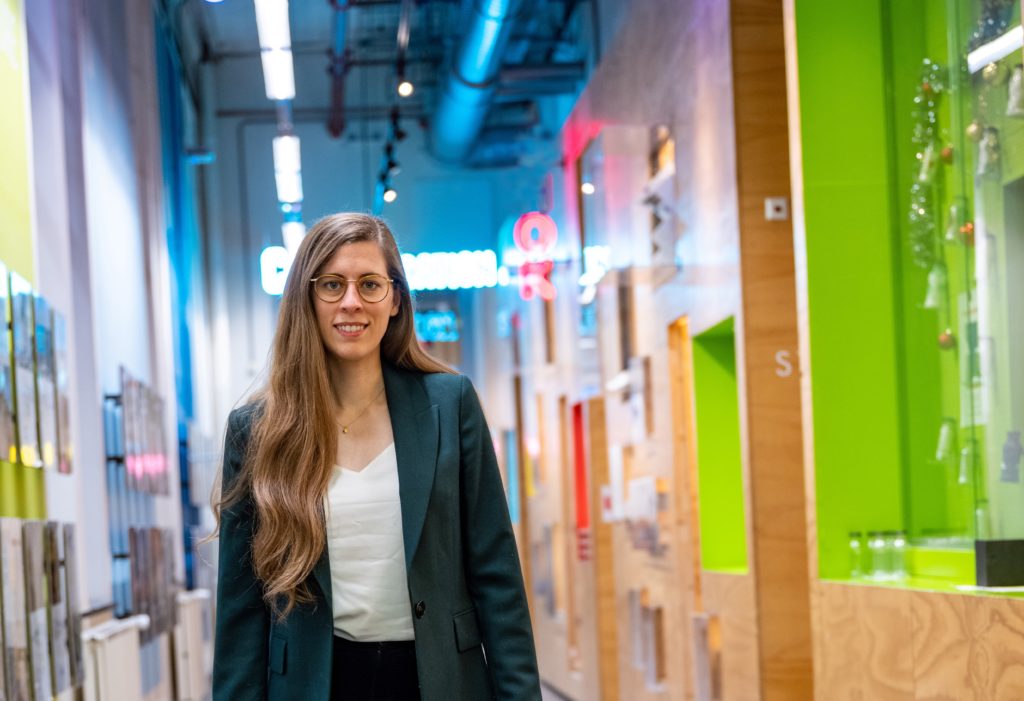
How much material is currently reused from old buildings?
(Construction companies) take away only about 1% of building materials from a demolition site for reuse, because the market isn’t in place yet.
If there was more demand and more actors involved, we could (reuse) more materials from buildings.
(In the meantime) you can reuse buildings as a whole by keeping the structure in place and putting a more flexible infill into them. For example, introducing movable wall partitions allows an office to be reconfigured quickly and cheaply in the future.
What needs to happen for us to achieve circular construction?
We will need to completely review the whole supply chain in the building sector.
Building users and owners, architects, engineers, contractors, materials suppliers … (and) governments need to work together towards this transition.
At TU Delft we are looking at how digitalisation can help put stakeholders in contact with each other so they can exchange materials and reuse them, rather than throwing them away.
(We) are exploring AI technology to make digital platforms for exchanging materials more efficient.
‘We still need to design for deconstruction so building materials are not glued together and cast together in a way that makes it hard to take them apart.’
-Dr Catherine De Wolf, TU Delft, the Netherlands
What’s holding back the shift to a circular economy?
There’s a strong concrete and steel lobby in the construction industry that is definitely playing a role.
But it’s also about how fragmented the construction industry is. There are so many contractors and subcontractors, so communication between stakeholders is quite difficult.
The construction sector in general is quite slow in the uptake of innovation – especially digital innovation – compared to other sectors, and I think this is because of how fragmented the value chain is.
Can the construction industry really become circular within 5 years?
Yes I think so. It’s already shifting towards circular construction. And there’s a lot we can do to accelerate the transition.
For example, currently some building materials are quite cheap. We don’t pay for their environmental impact, or the impact of waste on the environment and on society. Carbon and waste taxes could help address that.
The public sector can play a big role through changing building regulations and through public procurement.
Also, we need to start assessing the price of a building based on its long-term lifecycle cost, and the cost of waste and emissions.
Is the shift to a circular economy the most important change?
We should go beyond circular construction and talk about regenerative construction.
That means designing buildings that improve the environment rather than harming it. For example, as well as reusing materials, use materials with carbon sequestration, use (biological-based technology to) treat wastewater from the building, grow vegetables on the roof.
A building is a complex entity so it should be looked at holistically.
Dr De Wolf has received EU funding under the EPFL Fellows project.
No comments:
Post a Comment