The majority of plastic waste is buried in landfills across the world
Image: REUTERS/Mohammad Ponir Hossain
25 Aug 2021
Emma Samson
Forum in focus
The one essential element needed to accelerate action on climate change
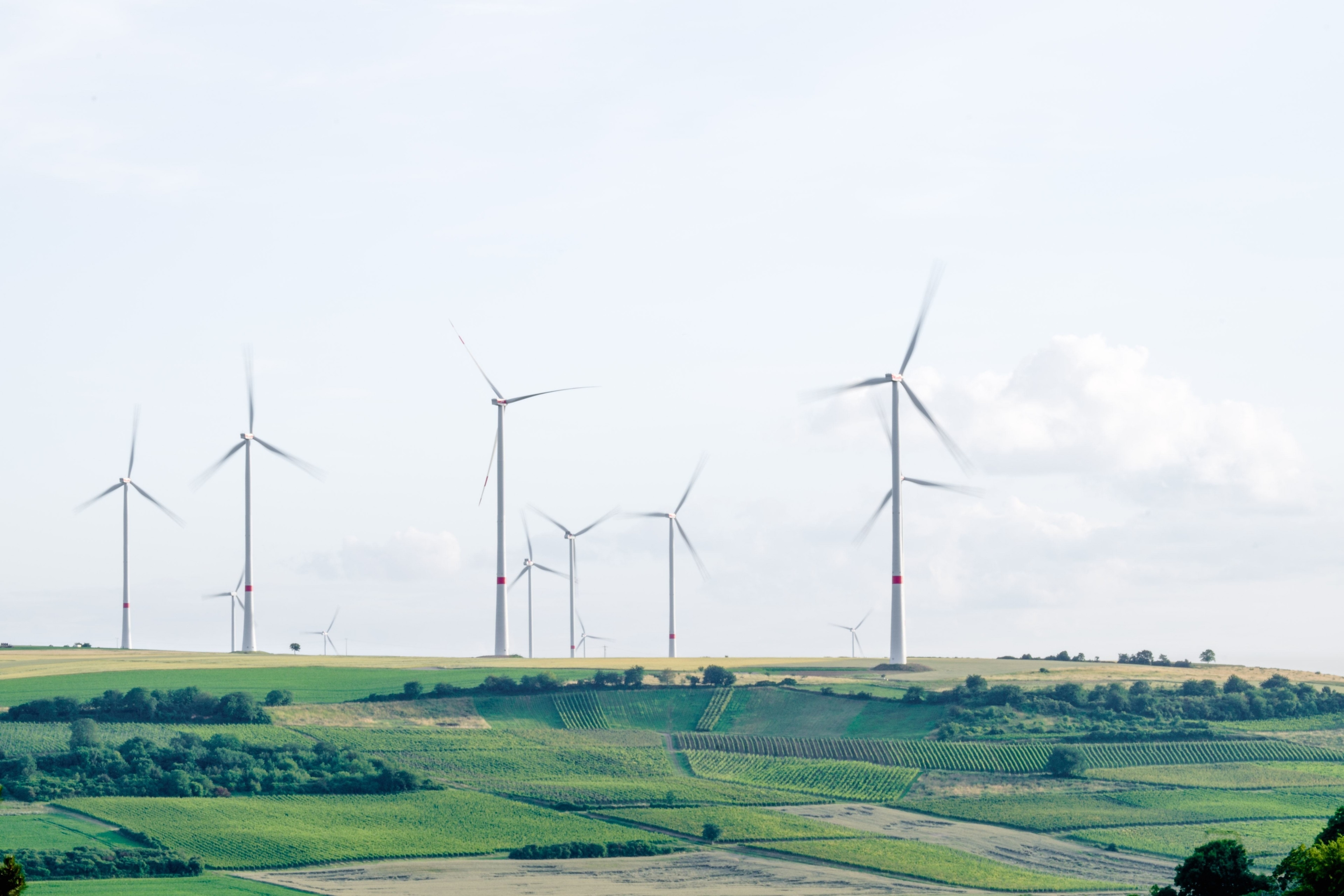
Read more about this project
Explore context
Plastics and the Environment
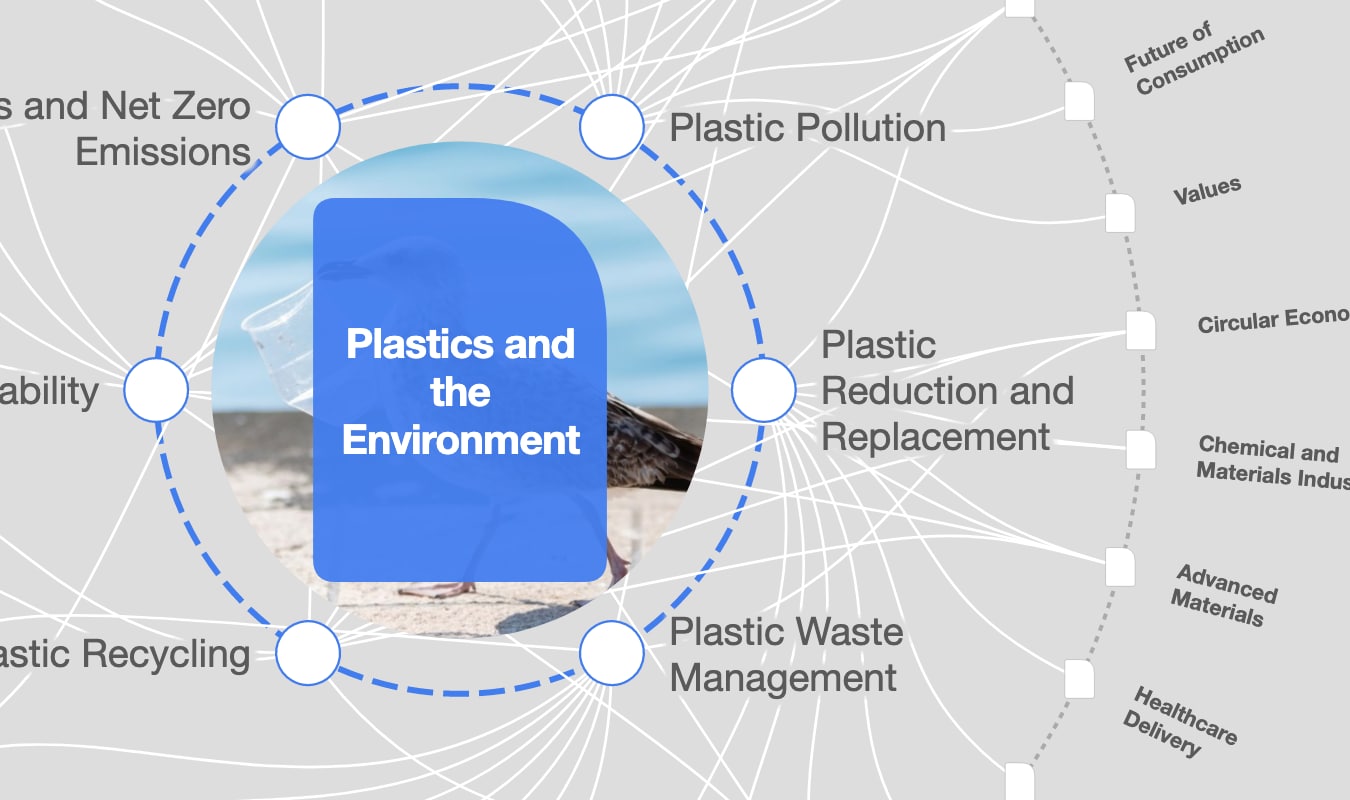
Explore the latest strategic trends, research and analysis
Just 9% of plastic waste created is recycled;
Recycling rates could be 100% with improved waste management, an optimized recycling system and clever product design;
To build a trash-to-treasure or waste-to-product mindset, the financial and sustainability benefits must be better understood by plastic producers.
Since the 1950s, the increase in mass production of plastics has led to 8.3 billion tonnes of plastic waste. Unfortunately, 12% of this waste has been incinerated and only 9% successfully recycled with the rest buried in landfills all over the world. As plastic takes hundreds of years to degrade, most of it still exists in some form.
Have you read?
Reusing 10% will stop almost half of plastic waste from entering the ocean. Here's how
The Loop Alliance plans to eliminate plastic waste
How rivals can work together to stop plastic waste
What if we could recapture those legacy resources and use them to create new products, saving us from extracting raw fossil fuels in the future? While large scale urban mining may be a way off, we can capture the plastic waste we produce now and turn it back into treasure.
Losing our virginity
Some scientists have called for a global treaty to end production of “virgin” plastic by 2040. Such an agreement would turbocharge the development of full circularity in the plastic chain, where everything is reused and nothing wasted and plastic material stays in a perpetual loop. Improved waste management, an optimized recycling system and clever product design can make recycling rates of 100% possible if all the moving parts work in unison.
To adopt a fully integrated waste-to-product mindset, we need to communicate the value proposition to plastic manufacturers. There are clear financial benefits to this strategy as well as sustainability advantages. Using recycled content is not only about preventing waste; it also reduces CO2 emissions and energy use, allowing companies to meet ambitious corporate social responsibility (CSR) objectives and pre-empt government legislation on extended producer responsibility (EPR) and recycled content mandates. In addition, it lessens dependence on importing raw materials, shortening supply chains and reducing costs. Losing our virginity is a goal we must race towards.
In a circular utopia, all plastics would be recycled back into the same products in a never-ending loop. Nothing would leak into the environment, nothing would downgrade and nothing would be made from fossil fuels ever again. However, even state-of-the-art facilities have systemic and technological limitations preventing them from attaining higher recycling rates. Technically, all plastics could be converted back into fuel through advanced chemical recycling methods, such as pyrolysis, but these are incredibly investment and energy-intensive and not feasible for small communities.
Mechanical recycling may have its constraints when dealing with post-consumer waste, but what we can't convert back into the same product, we can still make into something else. Waste-to-product may be a line rather than a circle, but thankfully, it's a much longer line in terms of the life span and use of the material.
Bottles to bricks?
Lego made headlines in June 2021 with its bricks made from recycled PET bottles. Exciting news, although it caused quite a storm on social media, where people criticized their use of rPET (recycled polyethylene terephthalate), an already high-demand recycled material owing to its broad application in critical industries such as FMCG (fast-moving consumer goods) and textiles. On the one hand, the bricks turn discarded, single-use packaging into multi-use products that will last for generations; on the other hand, valuable plastic bottles that could be part of the circular economy have just been lost to the toybox.
PET is the most commonly recycled plastic globally and it is the only commercially available recycled material approved for food contact – exactly why Lego chose it over other types of polymers because children have a tendency to put things in their mouths. Regulations for food-grade plastic are prohibitively strict, but for non-food-grade items in critical sectors such as construction and automotive, there are few reasons not to use waste-to-product design.
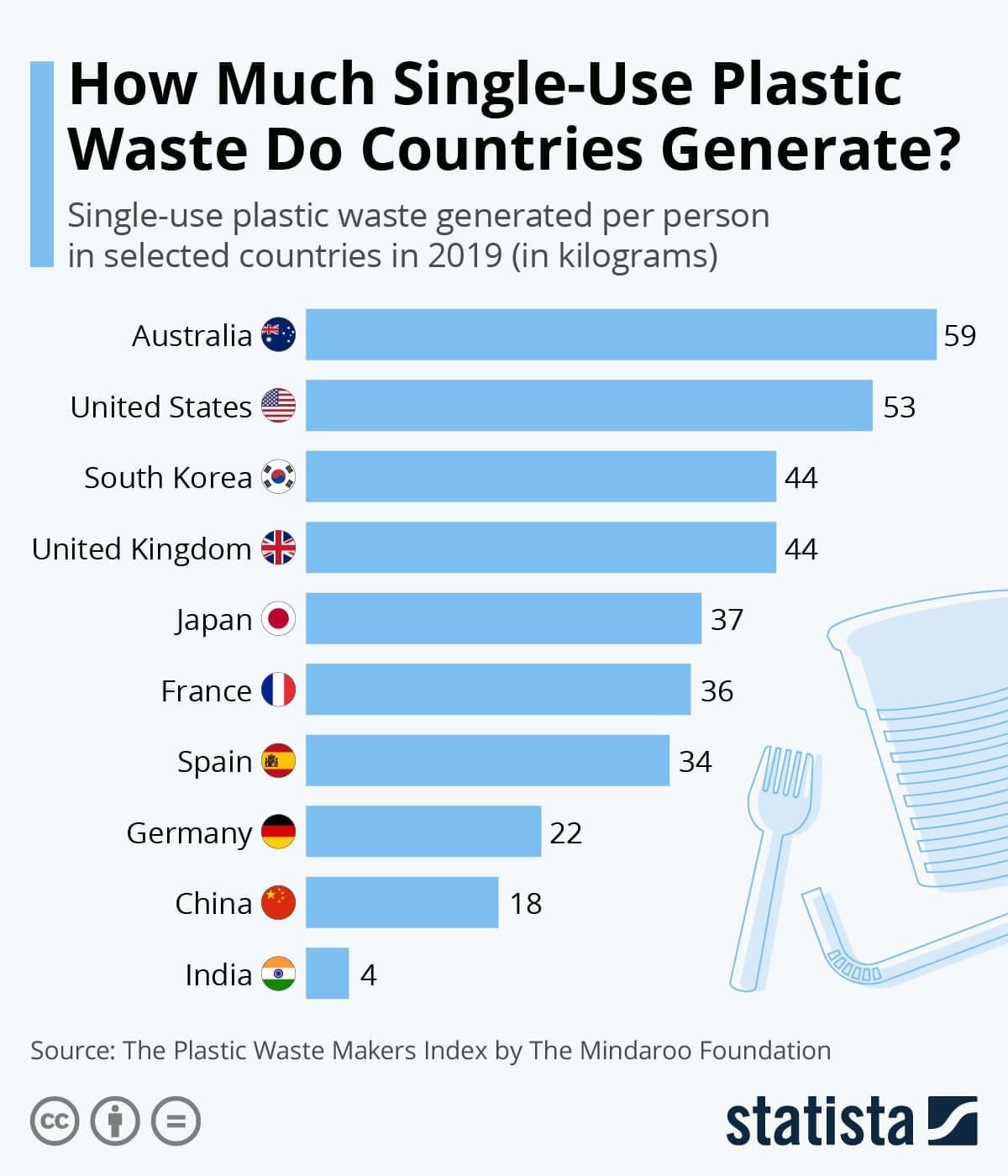
How much single-use plastic waste do countries generate?
Image: Statista
Waste-to-product solutions
Much of the 381 million tonnes of plastic waste generated each year come from developing countries, where waste management and recycling is rudimentary at best. However, basic mechanical recycling can transform mixed, low-quality waste into long-lasting functional products such as furniture, dustbins and latrines – keeping waste out of the ocean and boosting the local economy. For example, a lounge chair made from recycled HDPE (high-density polyethylene) has been shortlisted in the Plastics Recycling Awards Europe 2021 for its waste-to-product design.
"The chair shows not only that it's possible to incorporate recycled material without sacrificing aesthetics, but also that it's possible using low-key technology in remote settings," says Jaap Patijn of Searious Business.
Another remarkable opportunity for waste-to-product lies in the fishing industry, which contributes 10% of ocean plastics in the form of discarded gear and nets. For example, the Greek initiative Enaleia has collected more than 20,000kg of used nets and upcycled them into 260,000 pairs of socks, preventing ocean pollution and providing extra income to 1,000 fishers in the region.
No such thing as disposable
The pandemic forced us to temporarily prioritize health concerns over the future of our planet. Millions of people turned to disposable PPE (personal protective equipment) to protect themselves and others from COVID-19 infection. Masks are used for a short time and then discarded, often littering our high streets and parks. UK retailers, Wilko and recycling specialists ReWorked came up with a possible response to the problem. Masks can be washed and shredded down into raw materials and then refashioned into products ranging from other safety materials for businesses to building materials and furniture.
A fully circular plastic economy may be a dream, but it is not a total fantasy and innovative waste-to-product designs like these demonstrate the possibilities. While recycling technology is developing faster and faster, pushing us closer to a cradle-to-cradle model, we must let go of our take-make-waste mentality. There is no such thing as waste, only opportunities.
No comments:
Post a Comment