Wood Mackenzie | June 13, 2022 |
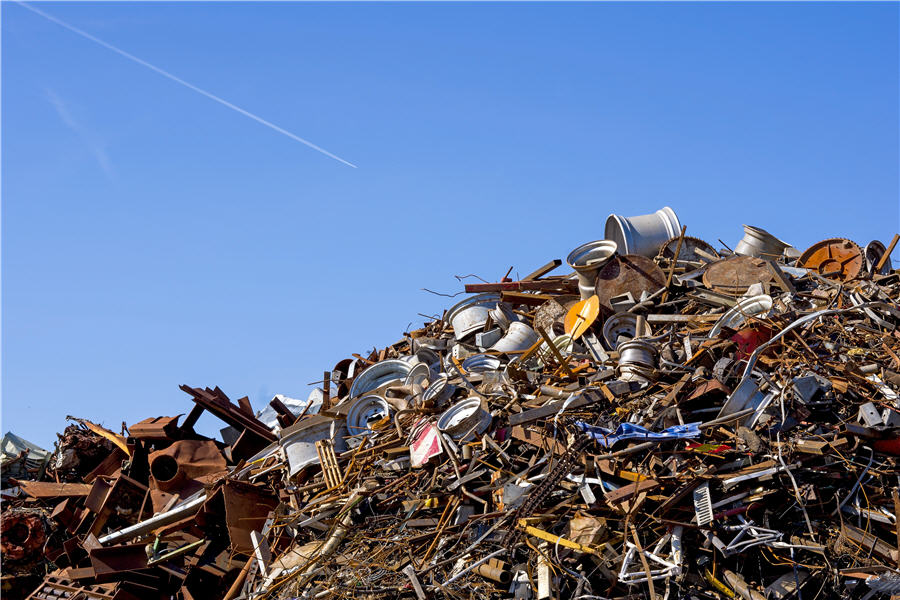
Scrap battery metal. (Stock image)
While recycling can relieve some pressure from the supply deficit of battery raw materials, it will not be able to meet demand, says Wood Mackenzie, a Verisk business (Nasdaq:VRSK).

The electrification of the transportation sector has caused a boom in demand for lithium-ion batteries. Global cumulative lithium-ion battery capacity could rise over five-fold to 5,500 gigawatt-hour (GWh) between 2021 and 2030.
Speaking at the Advanced Automotive Battery Conference in Mainz today, Wood Mackenzie research analyst Max Reid said: “With rapid expansion in the battery supply chain, we have created a situation of high waste. Recycling can reduce rapid expansion in carbon intensive mines as well as reduce waste. Together, recycling production scrap and end of life batteries could become a substantial source of raw material to meet surging demand. Recycling also presents an opportunity to source materials in regions which lack natural resources.”
Currently demand for key battery raw materials stands at 97 kilotonnes (kt) for lithium, 186 kt cobalt and 3,014 kt nickel. By 2030, these are expected to grow to 318 kt, 264 kt and 4,273 kt, respectively. Supply from recycled materials, though paling in comparison, are expected to reach 130 kt for lithium, 112 kt cobalt and 377 kt nickel, respectively, by the end of the decade.
At present, the challenges of recycled battery raw materials seem insurmountable. Most of the discussion has been around the collection and recycling of end-of-life electric vehicles (EVs), but the process is plagued with challenges.
Firstly, the cathode, which contains critical metals in the EV pack, is overpackaged with pack materials such as casings, interconnects, cooling channels and others. The result is a tedious recycling process with little value. Coupled with an industry push to use lower value materials, the move towards larger-sized EV packs is also a deterrence against recycling due to lower throughput while containing lower value materials.
Secondly, EV packs have long warranties and lifetimes. Recovering critical metals from them will be a long-term affair. In addition, the emergence of second-use applications, like residential or industrial energy storage, will also keep end-of-life EVs from entering the recycling system.
As such, recycling production scrap will be the main source of recycled material this decade. China, Europe and North America will see huge increases in battery and cathode manufacturing to meet demand for batteries. Globally, Wood Mackenzie expects battery manufacturing capacity to grow 3.5 times to over 4,621 gigawatt-hours by 2030, with China leading way ahead. This presents an increasing market for production scrap.
“At the end of the day, the amount of production scrap or EVs coming to end of life will never be able to meet demand while demand continues to increase,” Reid said. “There needs to be a push in expanding virgin sourcing while maximising the recycling sector to ease the deficit.”
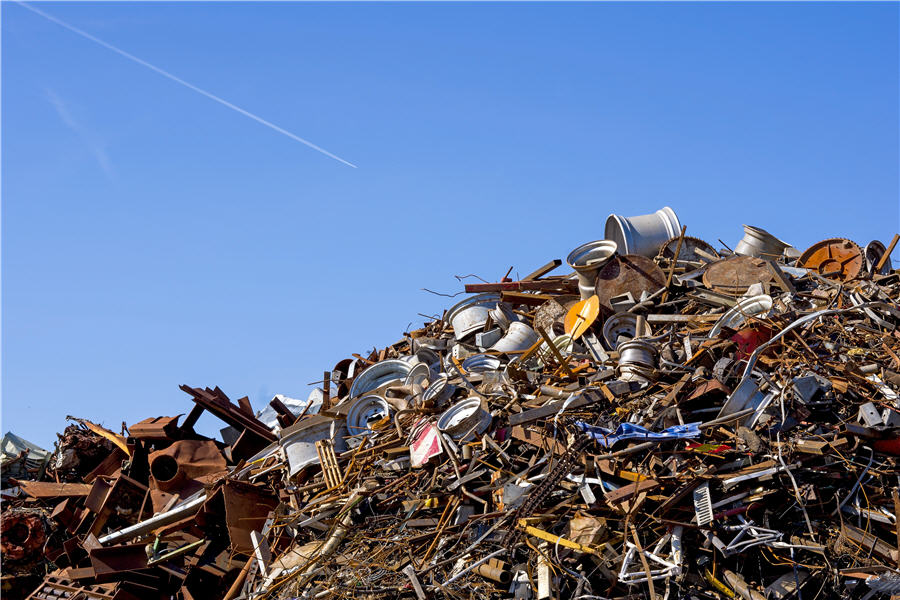
Scrap battery metal. (Stock image)
While recycling can relieve some pressure from the supply deficit of battery raw materials, it will not be able to meet demand, says Wood Mackenzie, a Verisk business (Nasdaq:VRSK).

The electrification of the transportation sector has caused a boom in demand for lithium-ion batteries. Global cumulative lithium-ion battery capacity could rise over five-fold to 5,500 gigawatt-hour (GWh) between 2021 and 2030.
Speaking at the Advanced Automotive Battery Conference in Mainz today, Wood Mackenzie research analyst Max Reid said: “With rapid expansion in the battery supply chain, we have created a situation of high waste. Recycling can reduce rapid expansion in carbon intensive mines as well as reduce waste. Together, recycling production scrap and end of life batteries could become a substantial source of raw material to meet surging demand. Recycling also presents an opportunity to source materials in regions which lack natural resources.”
Currently demand for key battery raw materials stands at 97 kilotonnes (kt) for lithium, 186 kt cobalt and 3,014 kt nickel. By 2030, these are expected to grow to 318 kt, 264 kt and 4,273 kt, respectively. Supply from recycled materials, though paling in comparison, are expected to reach 130 kt for lithium, 112 kt cobalt and 377 kt nickel, respectively, by the end of the decade.
At present, the challenges of recycled battery raw materials seem insurmountable. Most of the discussion has been around the collection and recycling of end-of-life electric vehicles (EVs), but the process is plagued with challenges.
Firstly, the cathode, which contains critical metals in the EV pack, is overpackaged with pack materials such as casings, interconnects, cooling channels and others. The result is a tedious recycling process with little value. Coupled with an industry push to use lower value materials, the move towards larger-sized EV packs is also a deterrence against recycling due to lower throughput while containing lower value materials.
Secondly, EV packs have long warranties and lifetimes. Recovering critical metals from them will be a long-term affair. In addition, the emergence of second-use applications, like residential or industrial energy storage, will also keep end-of-life EVs from entering the recycling system.
As such, recycling production scrap will be the main source of recycled material this decade. China, Europe and North America will see huge increases in battery and cathode manufacturing to meet demand for batteries. Globally, Wood Mackenzie expects battery manufacturing capacity to grow 3.5 times to over 4,621 gigawatt-hours by 2030, with China leading way ahead. This presents an increasing market for production scrap.
“At the end of the day, the amount of production scrap or EVs coming to end of life will never be able to meet demand while demand continues to increase,” Reid said. “There needs to be a push in expanding virgin sourcing while maximising the recycling sector to ease the deficit.”
No comments:
Post a Comment