$5 million to improve testing, durability and noise levels of wave energy devices, offshore wind
The research could make offshore renewable energy more reliable and a better neighbor to marine life, also enabling laboratory testing of larger prototypes
University of Michigan
Devices that create electricity from wave motion and offshore winds could become sturdier, quieter and easier to test at near-ocean-ready sizes, with four new grants to the University of Michigan.
The new funding from the U.S. Department of Energy totals around $5 million, which will be used to develop:
Shock absorbers that allow mooring lines to last longer and power sensors that monitor the device
Curtains of balloons and arrays of metal poles in the seabed that mitigate wildlife-disturbing noise produced by offshore wind turbines
Combinations of hardware and software—called hardware-in-loop platforms—that will enable laboratory testing of ocean-scale wave energy devices by mimicking the power produced by ocean waves
Standardized testing and a publicly accessible database of the performance of power takeoffs, the components of wave energy devices that convert motion to power
Researchers at Pacific Northwest National Laboratory, the National Renewable Energy Laboratory, Sandia National Labs, the American Bureau of Shipping and Virginia Tech will also contribute to these projects.
Ocean waves and offshore winds could be a vast energy source. The total available power in ocean waves in the United States is equivalent to nearly 60% of the electricity currently produced in the country. Global offshore wind energy can be 18 times the world's electricity needs.
Despite its potential, marine energy is still not as widely deployed as solar panels and land turbines. One reason the technology lags behind other renewables is because they don't survive rough waters. Waves can be strong enough to break mooring lines and leave wave energy devices lost at sea.
The shock absorbers designed in the first project could ensure that mooring lines don't break or weaken to the point that the attached devices can move in ways that prevent them from efficiently generating electricity. The motion of the shock absorbers will also be used to generate a small amount of electricity to power other electronics on the device, such as sensors that monitor the health of the device.
"It can cost around two million dollars to fix a mooring line that is only 30 to 80 meters deep," said Lei Zuo, the Herbet C. Sadler Collegiate Professor of Engineering and each project's principal investigator. "It's best to create as robust a system as possible."
Another limit to marine energy deployment are its environmental impacts. Some regulators and biologists fear that noisy offshore wind turbines could interfere with marine life by drowning out the sounds they use to communicate and navigate. These concerns will be addressed with the balloon curtains, which prevent sound waves produced by wind turbines from moving through the water column, and the metal poles, which stop them in the seabed.
The final two grants will enable easier and more rapid testing of prototype wave energy converters and their components. Today, engineers have to build smaller scale versions of their prototypes to test them in wave tanks, because testing at full-scales in real ocean environments can be expensive and risky—especially if a large wave breaks a mooring line. But the amount of power produced by wave energy converters scales exponentially with the device's size. As a result, components within the prototype device are exposed to uncharacteristically low amounts of power during smaller scale tests.
"Ideally, we would build and fully test a device that is half or one-third the size of an ocean-scale device before we'd deploy it in the ocean," said Zuo, who is also a professor of naval architecture and marine engineering and mechanical engineering. "For our tests in wave tanks, we are limited to prototypes that are 10 to 20 times smaller than ocean-scale devices, which reduces the power by a factor of 3,000 to 35,000."
That scaling problem can leave engineers less certain that their designs will function as expected and survive in expensive field trials. The hardware-in-loop platforms will enable engineers to comprehensively evaluate how well a variety of different power takeoff systems perform under more realistic levels of wave power before conducting any tests in the real ocean. The data that Zuo's team will create from their testing platforms will also be compiled into a standardized dataset for the research community to benchmark their prototypes against.
Other collaborators include Xiaofan Li, a former research scientist of naval architecture and marine engineering at U-M who is now at the University of Hong Kong, and David Dowling, the ABS Professor of Marine and Offshore Design Performance.
Evaluation of influence of offshore wind farm noise on fishes and dolphins
Offshore Wonders
A new generation of offshore wind service vessels is turin heads.
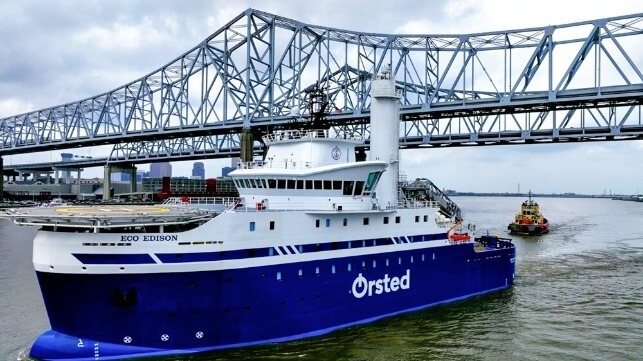
(Article originally published in Nov/Dec 2024 edition.)
What a year for boats!
As many Maritime Executive readers no doubt realize, I consider myself a boat nerd. Having run away to sea at 18, I discovered both a wide world and the best way to get around it.
I’ve sailed, shipped and even steamed on waters near and far, and despite many differences the one constant was a capable vessel under my feet.
Even after I “came ashore,” I’ve kept close to the water and have had the pleasure of surveying a huge variety of vessels. There are very few newbuild vessels in the U.S. Gulf of Mexico, for example, that I haven’t been on, and I write these words onboard a specialized heavy-lift cargo vessel in the Caribbean during a break in the project due to afternoon rains.
All that is to say I love boats, their design, capabilities and potential. The offshore renewables market is especially innovative, and it’s with great pleasure that I recap some of the noteworthy newbuilds and soon-to-launch vessels of the year.
ECO Edison
First up is the first Jones Act-compliant service operations vessel (SOV), ECO Edison.
Built at Edison Chouest Offshore’s (ECO) in-house shipyards in Louisiana, Mississippi and Florida with components sourced from 34 states, the ECO Edison was constructed by more than 600 workers completing nearly one million working hours. The state-of-the-art, 262-foot-long vessel immediately went to work for Ørsted, serving as a floating, year-round home base for 60 of the first American offshore wind turbine technicians, who are servicing and maintaining the massive offshore turbines off the U.S. East Coast.
It includes special features like an Ulmatec 47-inch-wide, walk-to-work, motion-compensated gangway, which includes an Alimak elevator with 4,400-pound lifting capacity that allows technicians to easily and safely cross up to 60 feet of water to access the wind turbines. A smaller daughter craft on board can be deployed to efficiently move crew within the field.
Providing power are four Caterpillar 3512E, 1,700kW generators that meet stringent EPA Tier IV emission standards. In a departure from the azimuth thrusters most often seen in the U.S. offshore, the ECO Edison instead uses twin Voith Schneider propellers. This cyclorotor design (think eggbeaters under the ship) can provide instantaneous thrust in any direction and is known for its extreme maneuverability.
Three Brunvoll tunnel thrusters at 1,250kW each complete the propulsion package forward.
“You can make the boat do whatever you want it to do,” Captain Taylor Apollonio says. “It takes the environmental conditions out of the equation because it has so much power.”
Purus Chinook
Across the ocean in Norway another groundbreaking vessel is nearing completion.
The Purus Chinook is a Vard-designed C/SOV (construction service operations vessel) that has already landed a multiyear contract with Vestas that will begin as soon as the vessel is launched early next year.
The cutting-edge design ensures it will meet the highest industry standards for offshore service, safety and hybrid battery technology to lower emissions and reduce engine hours. The Purus Chinook has the capacity to house up to 120 people at industry leading comfort-class and sea-keeping standards and also offers an all-electric gangway, 18-meter helideck, 5+ ton 3D motion-compensated crane and next-generation Chartwell 12 passenger daughter craft.
And just this past month Purus began cutting steel on the Purus Coriolis, which will be the second C/SOV in the expanding fleet. This one is scheduled for delivery in 2026 and should boast a similar set of amenities to the Chinook.
Both vessels are optioned with dual-fuel, methanol-ready propulsion systems, targeted for potential implementation starting in 2027.
WindServe CTVs from Senesco Marine
Another type of boat of key importance to the offshore wind industry is the crew transfer vessel (CTV).
These are fast and sleek. Typically constructed from aluminum using a catamaran hull design, they require extensive investment in tooling and technology and specialized experience to build. In the U.S. market, Senesco Marine brings this experience to the forefront.
Operating from a World War II Naval Air Station, the New England-based shipyard features a 1,200'x 80' pier with a depth of 28', originally designed to berth aircraft carriers, plus the only two drydocks in Rhode Island.
The yard recently completed the last CTV of a six-vessel package for WindServe Marine, which will provide crew transfer support to East Coast wind projects.
The first four builds all measured in at 88.6' x 29.5' x 5.6' and can carry up to 24 offshore technicians. They’re fitted with Volvo Penta D13 main engines, each rated 690 hp at 2,300 rpm, and a Volvo Penta IPS 900 propulsion system. This allows for a service speed of 24 knots and a top speed of 27 knots.
The final two CTVs received an additional six feet to accommodate “hybrid-ready” battery capabilities.
Senesco President Ted Williams (recently interviewed in the May/June issue of The Maritime Executive) is committed to further investment in the yard’s technological capabilities, such as those recently made to support advanced aluminum fabrication techniques, which will further allow them to support “…more complex builds (including Department of Defense work) as well as future technologies such as composite materials and alternative energy propulsions systems.”
The yard also recently delivered the first-ever hybrid ferries in New England, further cementing its commitment to sustainable shipping and environmental stewardship.
“Senesco has become a national leader in green and blue energy builds as well as in developing a robust deck barge fleet in the near future,” says Williams. “We look forward to 2025 and beyond for the increased opportunities coming to the region.”
GLDD and the SRI Acadia
While SOVs and CTVs house and transport crew to the wind turbines, what goes on under the water is equally as important.
Scour protection is a vital part of offshore construction. It consists of strategic rock placement which protects against “scour” – water-powered erosion around the base of subsea structures such as offshore turbines. This stabilizes the seafloor and ensures the full service life of the asset.
Great Lakes Dredge & Dock (GLDD), the leading provider of dredging services in the U.S., is currently building the first U.S.-flagged, Jones Act-compliant, subsea rock installation vessel (SRI) at Philly Shipyards in Philadelphia.
The Ulstein-designed SRI Acadia will carry a SUSTAIN-2 ABS notation, which recognizes adherence to U.S. Sustainable Development goals related to vessel design, outfitting and layout. It will further be fitted with state-of-the-art technology including a Battery Energy Storage System to reduce emissions, biofuel ready engines and a shore power connection allowing the vessel to be plugged in while in port to achieve full zero emissions.
Other design features include Work-Class ROV capabilities, a loading capacity of 20,000mT (2 x 10,000mT bins), DP-2 control system, advanced multi-beam sonar and a heave-compensated fall pipe for rock placement operations.
The vessel represents part of a critical advance in building the future of U.S. offshore wind that includes establishing a U.S.-based rock supply network spanning eastern seaboard states with active offshore wind leases, which is expected to spur additional job growth and regional economic opportunities.
It should also be noted that GLDD recently received the prestigious 2024 Significant Boat of the Year Award at the International WorkBoat Show for its newly launched Multi Cat dredge support vessels, Cape Hatteras and Cape Canaveral. The award underscores the company’s commitment to safety, innovation and operational excellence in the dredging and maritime sectors as well as its commitment to building world-class vessels.
With the construction of the Acadia, GLDD is literally helping to build the foundation for U.S. offshore wind.
Damn Fine Boats
The offshore wind sector can only be as successful as the vessels and crews that build and service it.
The examples here showcase the innovation and aspirations of both new and established market entrants utilizing the latest technology to achieve operational success while aggressively d
No comments:
Post a Comment