Mining waste could be used as an ingredient for cheaper hydrogen fuel production
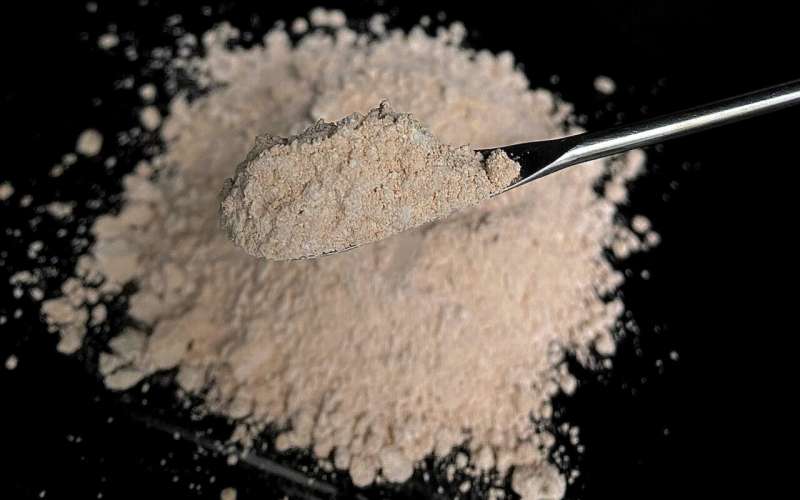
Researchers have discovered a way to use mining waste as part of a potential cheaper catalyst for hydrogen fuel production.
Water splitting reactions that produce hydrogen are triggered using rare platinum ($1450/ounce), iridium ($1370/ounce) and ruthenium ($367/ounce), or cheaper but less active metals—cobalt ($70,000/ton), nickel ($26,000/ton) and iron ($641/ton).
Professor Ziqi Sun from the QUT School of Chemistry and Physics and QUT Centre for Materials Science and Dr. Hong Peng from the School of Chemical Engineering at the University of Queensland led research to create a new catalyst using only a small amount of these reactive metals.
They combined them with feldspars, aluminosilicate rock minerals found in mining waste that Professor Sun said some companies pay about $30/ton to dispose of.
In the experiment, featured on the August cover of Advanced Energy & Sustainability Research, the researchers triggered a water splitting reaction using heated-activated feldspars nanocoated with only 1–2 percent of the cheaper reactive metals.
"Water splitting involves two chemical reactions—one with the hydrogen atom and one with the oxygen atom—to cause them to separate," Professor Sun said.
"This new nanocoated material triggered the oxygen evolution reaction, which controls the overall efficiency of the whole water splitting process," he said.
Professor Sun said cobalt-coated feldspar was most efficient and optimizing the new catalysts could see them outperform raw metals or even match the superior efficiency of platinum metals.
He said the new catalyst could also potentially lower the cost of lithium-ion (Li-Ion) batteries and other sustainable energy solutions that relied on electrochemical conversions.
"This research could potentially add to Australia's renewable energy value chain by repurposing mining waste and adding new technologies to traditional industries.
"Companies like Tesla could potentially use this technology for energy production, advanced energy storage solutions like new battery technologies, and renewable fuel," he said.
Researchers are now looking to test the catalysts at pilot scale.
"Australia's abundance of aluminosilicate and the simplicity of this modification process should make industrial scale production of this new catalyst easy to achieve," Professor Sun said.
Feldspars make up about 60 percent of the Earth's crust, according to Professor Sun, whose previous research activated feldspars for use as potential low-cost anodes in Li-Ion storage.
He said the aluminosilicates were chemically inert, but heat caused defects that were useful for chemical reactions and electron transport.
Joining Professor Sun and Dr. Peng were other researchers from the QUT Centre for Materials Science including Professor Godwin Ayoko, Dr. Jun Mei and Dr. Juan Bai from the QUT Faculty of Science, and Associate Professor Liao Ting from the QUT Faculty of Engineering.
Professor Sun and Dr. Peng are both focused on developing materials for emerging sustainable technologies.
Dr. Peng is an expert in utilizing clay minerals and mine tailings for functional materials through low-cost mineral processing technology.
He said the mining industry produced tons of waste material each year that Australia could be using for sustainable technologies.
"Aluminosilicate is commonly found in various mining tailings and is so cheap that mining companies would normally pay to dispose of it," Dr. Peng said.
No comments:
Post a Comment