3D Printing is Saving the U.S. Coast Guard Serious Money
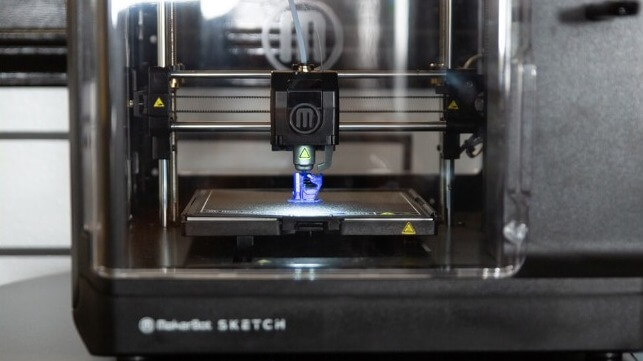
[By Jamie Rand, Consultant C5ISC]
Just as traffic lights and road signs inform drivers and warn them about upcoming hazards, aids to navigation, such as lighthouses, buoys, and radio beacons help mariners navigate waters and identify potential risks.
The Coast Guard is responsible for maintaining aids to navigation in waters under Federal jurisdiction, and that maintenance comes with an increasingly large price tag: according to a 2020 Government Accountability Office Report, “the overall costs to repair and replace aids to navigation increased from $12 million in Fiscal Year (FY) 2014 to about $20 million in 2018,” with “a collective replacement value of about $1.6 billion.”
The partnership between the USCG’s Shore Infrastructure Logistics Center’s Waterways Operations Product Line (SILC-WOPL) and the Command, Control, Communications, Computers, Cyber and Intelligence Service Center’s Electronics Repair Facility (C5ISC-ERF) has facilitated new techniques and helped lower the cost to repair and replace ATON – and in so doing, laid the groundwork for Additive Manufacturing (AM) to meet future needs of the USCG.
AM, also known as 3D-printing, enables the generation of tangible, three-dimensional objects directly from digital design files. Just as conventional desktop printers use ink and paper to create prints, 3D printers use an array of materials, including polymer composites, metals, and ceramics to create objects layer by layer. Using AM, C5ISC-ERF can create or recreate parts that are no longer commercially available, enabling personnel to salvage degraded or damaged equipment and return it to serviceable condition.
One successful example of this is the VRB-25 optical system, a standard 12-volt rotating light beacon with an incandescent bulb, used in lighthouses along the United States coastline. The Coast Guard began replacing the VRB-25s with light-emitting diode (LED) systems in the early 2010s, but despite the improved energy efficiency, the LED systems had higher repair costs and lacked the traditional appearance — the rotating beacon and glow — of the VRB-25, causing navigation complications for civilian mariners, the military, and the shipping industry.
Coast Guard technical authorities elected to reinstall the VRB-25 in lighthouses, which specifically require rotating beacons. SILC-WOPL, which serves as the focal point for implementing engineering and logistics solutions for the USCG’s ATON enterprise, found that the decommissioned VRB-25 systems had been sitting unused at Coast Guard units in various states of disrepair — or even discarded entirely — and could not always be used to replace the LED systems. SILC-WOPL then contacted C5ISC-ERF to see which broken systems could be brought back to serviceable condition.
Led by Mr. Guy Stewart (retired), C5ISC-ERF began the complicated and unique restoration process in late 2019, disassembling all hardware components and replacing wiring, motor bearings, and other parts, in addition to performing extensive corrosion mitigation procedures. For Original Equipment Manufacturer (OEM) components that were no longer available, such as the base foundation for the VRB-25 hanger plate, C5ISC-ERF used in-house 3D printing technology and recreated them to exact dimensions, with ET2 Kyle Perez developing the design and prototypes, and Mr. Stewart performing the verification and validation via engineering analysis and destructive testing to ensure that the 3D-printed parts could successfully replace the alloy parts. SILC-WOPL determined that the 3D printed part was good for the use case, and C5ISC-ERF was able to produce 18 VRB-25s for reinstallation.
Even at this early stage, AM is already enabling quick solutions and making a difference. Following a recent Command Cyber Readiness Inspection (CCRI) at C5ISC, some areas risked failing cyber-compliance due to missing simple emergency shut-off switch covers. Instead of procuring the covers through regular orders and waiting for them to arrive, C5ISC-ERF 3D printed the covers and shipped them overnight. And in just the last two fiscal years, AM has saved SILC-WOPL over $650,000 in acquisition costs and put 164 repaired pieces of equipment back into inventory.
To help better leverage this emerging technology, the AM Working Group will soon send personnel to a four-month industry training and a six-week training with the Navy. The Working Group is also beginning to coordinate with the USCG Force Readiness Command (FORCECOM) to find unique and expensive aids or prototypes that could be printed more economically, with some twenty to thirty parts under consideration, ranging from obsolete parts to safety covers. Low-risk parts such as switchboard or radio knobs and breaker blanks will help the USCG develop an organic understanding of AM capabilities before moving into production of higher-risk parts.
“The Coast Guard is not slow to follow suit with AM,” said LCDR Armstrong. “Mostly we’re just going about it logically and as engineering-sound as we can. There is some phenomenal work going on around the country, like flight-critical parts already approved by the Army and Air Force. We want to bring this solution space to everybody.”
This article appears courtesy of Coast Guard Compass and may be found in its original form here.
No comments:
Post a Comment