by Fraunhofer-Gesellschaft
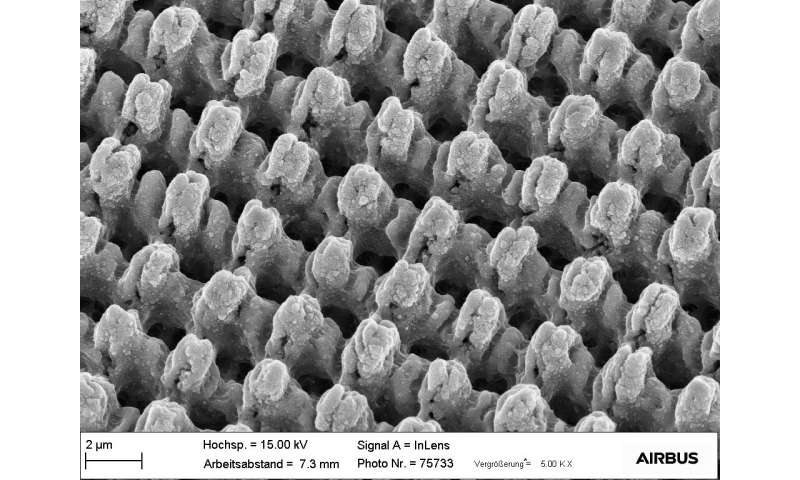
A close-up shot of the NACA airfoil’s surface taken from above. It was functionalized using DLIP. Credit: Airbus
Ice on an aircraft's surfaces can be a hazard. It increases drag and fuel consumption, disrupts aerodynamic flows, and decreases lift—which impairs the aircraft's ability to fly safely. Researchers at the Fraunhofer Institute for Material and Beam Technology IWS, Airbus and TU Dresden have developed a laser process that fills two needs with one deed. On one hand, accumulated ice falls off by itself and on the other it takes less heat to de-ice surfaces. Direct Laser Interference Patterning permits surfaces to be structured in ways that effectively repel ice.
Ice formation presents a safety risk for aircraft. A thin layer of frost settling on the wings or other neuralgic points such as the tail can adversely affect the aircraft's aerodynamics. Lift may decrease and drag increase. Ice accumulating on probes and sensors can compromise air speed measurements that are critical to in-flight safety. This is why snow and ice have to be cleared from aircraft before they take off. On the ground, this task falls to special vehicles that spray chemical agents onto all vulnerable surfaces. These antifreezes also go to prevent ice from forming. However, fluids of this type are harmful to the environment and expensive. Moreover, a substantial amount—400 to 600 liters—is needed to de-ice a plane. Airborne aircraft also have to be protected against this frosty peril. In most cases, ice protection systems such as heating elements are facilitated on board to do the job. The great drawback of these heaters is that they increase fuel consumption.
Ice on an aircraft's surfaces can be a hazard. It increases drag and fuel consumption, disrupts aerodynamic flows, and decreases lift—which impairs the aircraft's ability to fly safely. Researchers at the Fraunhofer Institute for Material and Beam Technology IWS, Airbus and TU Dresden have developed a laser process that fills two needs with one deed. On one hand, accumulated ice falls off by itself and on the other it takes less heat to de-ice surfaces. Direct Laser Interference Patterning permits surfaces to be structured in ways that effectively repel ice.
Ice formation presents a safety risk for aircraft. A thin layer of frost settling on the wings or other neuralgic points such as the tail can adversely affect the aircraft's aerodynamics. Lift may decrease and drag increase. Ice accumulating on probes and sensors can compromise air speed measurements that are critical to in-flight safety. This is why snow and ice have to be cleared from aircraft before they take off. On the ground, this task falls to special vehicles that spray chemical agents onto all vulnerable surfaces. These antifreezes also go to prevent ice from forming. However, fluids of this type are harmful to the environment and expensive. Moreover, a substantial amount—400 to 600 liters—is needed to de-ice a plane. Airborne aircraft also have to be protected against this frosty peril. In most cases, ice protection systems such as heating elements are facilitated on board to do the job. The great drawback of these heaters is that they increase fuel consumption.
Ecologically sustainable
Using a technology known as Direct Laser Interference Patterning (DLIP), a research team at Fraunhofer IWS collaborated closely with project partners Airbus and TU Dresden to develop a process allowing complex, meandering surface structures to be created on the micron and submicron scale to decrease ice accumulation and accelerate de-icing. (More on the DLIP technology in the box below). What sets this process apart is that the researchers combined DLIP with ultra-short pulse lasers to create multilevel, 3-D microstructures on wing profiles in a single step.
As a result, some of the ice simply loses its grip, depending on the conditions under which it froze, and spontaneously detaches after reaching a certain thickness. Also, technical de-icing requires 20 percent less heating energy. Other advantages of the new process are that it potentially reduces the required amount of environmentally harmful de-icing agents and the time passengers spend waiting for the plane to be de-iced. The same goes for in-flight power and fuel consumption. It can even reduce the aircraft's weight if smaller heating units are installed. This combination of these two effects has yet to be achieved with conventional technologies.
Wind tunnel tests with Airbus
This DLIP process was developed in a concerted effort between Fraunhofer IWS and TU Dresden in order to find the optimized DLIP surface structure. Finally, the IWS experts developed the patterning process to transfer the optimized structure onto final demonstrator: a complex three-dimensional NACA airfoil which served as a miniaturized but realistic wing pendant. The NACA airfoil was then tested by AIRBUS experts in the wind tunnel. The performance tests were carried out with a structured NACA airfoil and an unstructured NACA airfoil serving as a reference under realistic conditions at wind speeds ranging from 65 to 120 m/s, with air temperatures below minus ten degrees Celsius and at various humidity levels.
The partners from Airbus were able to demonstrate that ice growth on the functionalized surface is self-limiting. In fact, the ice falls off after a certain amount of time without requiring added surface heating. Additional experiments also showed that it took 70 seconds for the ice on an unstructured airfoil to melt at 60 watts of applied heat. The ice on the structured airfoil receded completely after just five seconds at the same amount of applied heat. The DLIP technology accelerated the process by more than 90 percent. It took 75 watts, or 25 percent more heating power compared to the DLIP surface, to remove the ice on the unstructured demonstrator. "In this wonderful collaboration with Airbus, we demonstrated for the first time and in a realistic way the great anti-icing potential that can be tapped with large-scale laser surface patterning. With our DLIP approach, we realized biomimetic surface structures on a complex component like the NACA airfoil, and demonstrated its distinct advantages over other laser processes", says Dr. Tim Kunze, Team Leader Surface Functionalization at Fraunhofer IWS. His colleague Sabri Alamri adds, "The application of micro- and nanostructures on metal prevents water droplets from adhering. Inspired from nature, this is widely known as the lotus effect. With our new DLIP process, we can create a fragmented surface to significantly reduce the number of adhesion points for ice. We will soon publish a paper on the results." Project partner Elmar Bonaccurso, Research Engineer for Surface Technology / Advanced Materials at Airbus, adds, "Ice formation is particularly dangerous during landing. Water on the surface freezes within milliseconds when the aircraft flies through the clouds at sub-zero temperatures. This can disrupt the functions of control elements such as landing flaps and slats, which impairs the aerodynamics. Today, we use hot air sourced from the engines to heat wing surfaces. The water-repellent structure, which we developed with our partner Fraunhofer IWS in the EU project Laser4Fun, is an attempt to replace conventional technologies with ecofriendly, more cost-effective alternatives." The partners' next step will be to optimize the method and adapt it to various air zones. They will take into account the results obtained in real-world flight tests currently underway with an A350 aircraft whose surfaces have been treated with DLIP.
Using a technology known as Direct Laser Interference Patterning (DLIP), a research team at Fraunhofer IWS collaborated closely with project partners Airbus and TU Dresden to develop a process allowing complex, meandering surface structures to be created on the micron and submicron scale to decrease ice accumulation and accelerate de-icing. (More on the DLIP technology in the box below). What sets this process apart is that the researchers combined DLIP with ultra-short pulse lasers to create multilevel, 3-D microstructures on wing profiles in a single step.
As a result, some of the ice simply loses its grip, depending on the conditions under which it froze, and spontaneously detaches after reaching a certain thickness. Also, technical de-icing requires 20 percent less heating energy. Other advantages of the new process are that it potentially reduces the required amount of environmentally harmful de-icing agents and the time passengers spend waiting for the plane to be de-iced. The same goes for in-flight power and fuel consumption. It can even reduce the aircraft's weight if smaller heating units are installed. This combination of these two effects has yet to be achieved with conventional technologies.
Wind tunnel tests with Airbus
This DLIP process was developed in a concerted effort between Fraunhofer IWS and TU Dresden in order to find the optimized DLIP surface structure. Finally, the IWS experts developed the patterning process to transfer the optimized structure onto final demonstrator: a complex three-dimensional NACA airfoil which served as a miniaturized but realistic wing pendant. The NACA airfoil was then tested by AIRBUS experts in the wind tunnel. The performance tests were carried out with a structured NACA airfoil and an unstructured NACA airfoil serving as a reference under realistic conditions at wind speeds ranging from 65 to 120 m/s, with air temperatures below minus ten degrees Celsius and at various humidity levels.
The partners from Airbus were able to demonstrate that ice growth on the functionalized surface is self-limiting. In fact, the ice falls off after a certain amount of time without requiring added surface heating. Additional experiments also showed that it took 70 seconds for the ice on an unstructured airfoil to melt at 60 watts of applied heat. The ice on the structured airfoil receded completely after just five seconds at the same amount of applied heat. The DLIP technology accelerated the process by more than 90 percent. It took 75 watts, or 25 percent more heating power compared to the DLIP surface, to remove the ice on the unstructured demonstrator. "In this wonderful collaboration with Airbus, we demonstrated for the first time and in a realistic way the great anti-icing potential that can be tapped with large-scale laser surface patterning. With our DLIP approach, we realized biomimetic surface structures on a complex component like the NACA airfoil, and demonstrated its distinct advantages over other laser processes", says Dr. Tim Kunze, Team Leader Surface Functionalization at Fraunhofer IWS. His colleague Sabri Alamri adds, "The application of micro- and nanostructures on metal prevents water droplets from adhering. Inspired from nature, this is widely known as the lotus effect. With our new DLIP process, we can create a fragmented surface to significantly reduce the number of adhesion points for ice. We will soon publish a paper on the results." Project partner Elmar Bonaccurso, Research Engineer for Surface Technology / Advanced Materials at Airbus, adds, "Ice formation is particularly dangerous during landing. Water on the surface freezes within milliseconds when the aircraft flies through the clouds at sub-zero temperatures. This can disrupt the functions of control elements such as landing flaps and slats, which impairs the aerodynamics. Today, we use hot air sourced from the engines to heat wing surfaces. The water-repellent structure, which we developed with our partner Fraunhofer IWS in the EU project Laser4Fun, is an attempt to replace conventional technologies with ecofriendly, more cost-effective alternatives." The partners' next step will be to optimize the method and adapt it to various air zones. They will take into account the results obtained in real-world flight tests currently underway with an A350 aircraft whose surfaces have been treated with DLIP.
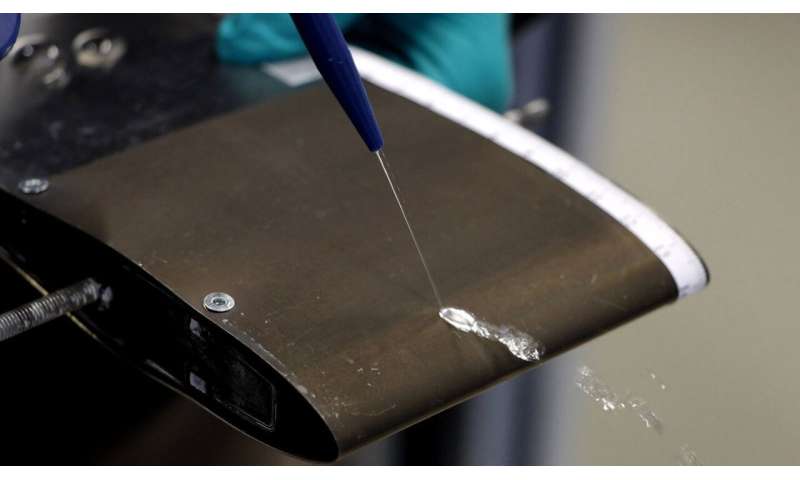
The NACA airfoil with the water-repellent structured surface. Credit: Airbus
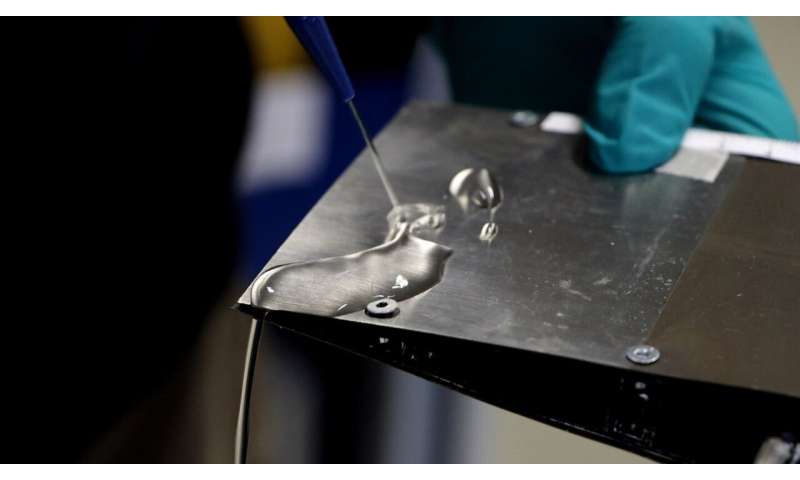
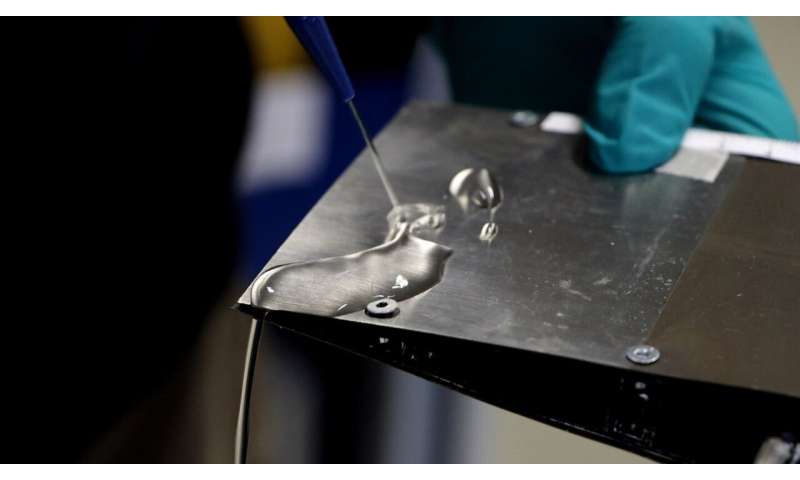
A comparison showed that water adheres to the unstructured NACA airfoil and freezes within seconds at sub-zero temperatures. Credit: Airbus
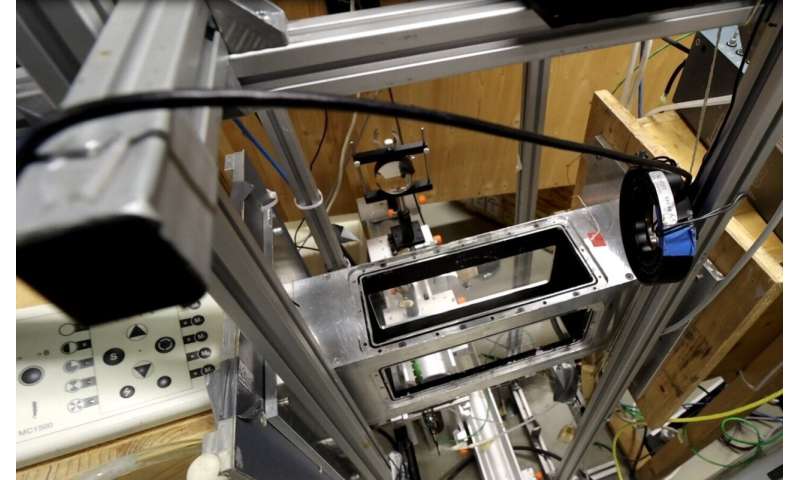
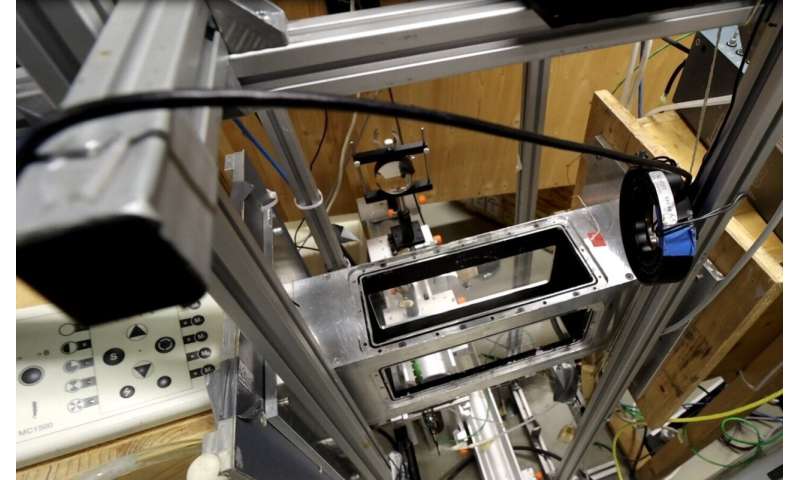
Tests in the wind tunnel at AIRBUS showed that the ice falls off the structured surface by itself after a defined time. Credit: Airbus
A key technology
The research team has established a key technology by using short and ultrashort pulse lasers for Direct Laser Interference Patterning. It can serve many applications, for example, to structure functional surfaces on wind turbines or other components that can ice over in cold regions. This technology can be also applied to very different fields such as product protection, biocompatible implants and improved contacts for electrical connectors. "We can apply functional microstructures over large areas and at high process speeds, thereby achieving benefits for a number of applications that, until now, had been inconceivable," says Tim Kunze.
Laser system prevents contamination on aircraft surfaces
Provided by Fraunhofer-Gesellschaft
A key technology
The research team has established a key technology by using short and ultrashort pulse lasers for Direct Laser Interference Patterning. It can serve many applications, for example, to structure functional surfaces on wind turbines or other components that can ice over in cold regions. This technology can be also applied to very different fields such as product protection, biocompatible implants and improved contacts for electrical connectors. "We can apply functional microstructures over large areas and at high process speeds, thereby achieving benefits for a number of applications that, until now, had been inconceivable," says Tim Kunze.
Laser system prevents contamination on aircraft surfaces
Provided by Fraunhofer-Gesellschaft
No comments:
Post a Comment